Русский размер дизеля / Вооружения / Независимая газета
Недавно «Адмиралтейскими верфями» была спущена на воду дизельная подводная лодка 4-го поколения «Санкт-Петербург». Было много споров по поводу целесообразности производства лодок такого класса в интересах российского ВМФ, особенно много дискуссий вызвала энергетическая установка на основе дизельных двигателей производства ОАО «Коломенский завод». Перед ЦКБ МТ «Рубин» возникла дилемма — ставить свой, российский, или закупать иностранный. Дело в том, что в Германии на 212-м проекте используется энергетическая установка с так называемыми топливными ячейками. «Топливными элементами» немцы занимаются на протяжении последних 30 лет. В России про них знали давно, но аналогичных разработок не велось. О том, что такое пропульсивные энергоустановки нового поколения, а также о национальных особенностях дизелестроения рассказывает доктор технических наук, профессор, научный консультант-руководитель экспертной группы по перспективным разработкам Управления главного конструктора по машиностроению ОАО «Коломенский завод» Евгений Никитин, который с 1952 года и по сей день является конструктором уникальных дизелей для подводного флота.
— Евгений Александрович, расскажите, что такое двигательная установка с «топливными ячейками», которая установлена на немецких лодках «Тип 212»?
— Новый проект подводной лодки делается в северогерманском Киле на верфи судостроительного концерна «Howaldtswerke-Deutsche Werft GmbH» (HDW). Построенная здесь за 400 миллионов евро лодка проекта 212 и спущенная на воду в 2002 году получила название U-31. Объявленная немцами «уникальность» состоит в том, что лодка оснащена серийной энергетической установкой нового поколения, наличие которой удорожает лодку как минимум в два раза.
«Топливная ячейка» — как называют ее немцы, — позволяющая лодке находиться в подводном положении в течение нескольких недель, это довольно-таки громоздкая и маломощная конструкция. Она идет в дополнение к обычному дизельному двигателю фирмы МТУ. Принцип топливного элемента состоит в том, что получается электрический ток при пропускании водорода вместе с кислородом через специальные пористые мембраны. Это позволяет лодке в подводном положении подзаряжать аккумуляторы и тихо двигаться со скоростью не более трех узлов в час. В надводном положении или на глубине 5-6 метров, когда можно использовать шноркель, работает обычный дизель MTU 12V 396 SE 84.
— Почему в России никто не занимается топливными элементами?
— Использование кислорода, водорода, вообще газов связано с огромными технологическими и эксплуатационными проблемами. Преобразование химической реакции водорода и кислорода в электроэнергию дает малую мощность при больших габаритах. Вырабатывается 200 киловатт — это крохи за большие деньги. Нужна специальная система охлаждения, повышенные меры пожаробезопасности┘ В Советском Союзе в свое время были попытки конструирования лодок, на которых использовали химические реакции получения кислорода. Подводники называли эти лодки «зажигалками» из-за частых пожаров, возникающих при работе с кислородом. Тем не менее, думаю, работы над топливными элементами имеют перспективы для ПЛ.
— Как рассчитывается необходимая мощность дизельного двигателя для обеспечения нормальной, надежной работы энергоустановки лодки?
— Оценить можно просто. Вот, например, лодка «Санкт-Петербург». Водоизмещение порядка тысячи тонн. На ней стоят два дизеля мощностью по 1200 киловатт, то есть 2400 киловатт на 1000 тонн. Получается — 2,4 киловатта на тонну. У немцев, при больших габаритах установки — длина более шести метров, ширина и высота — по три метра, естественно, и весит она много, — дается всего 180-200 киловатт. В 12 раз мощность топливного элемента должна быть увеличена — для обеспечения нормального функционирования лодки, если использовать без обычного дизеля, что сегодня невозможно.
— Сколько времени на максимальном режиме может работать ваш двигатель?
— Сколько надо, столько и будет работать. Дело в том, что максимальным режимом считается 75-80% мощности, которую может развить силовая установка. Моряки берегут ресурс, берегут двигатель. Поэтому, когда мы говорим о мощности 2000 киловатт, это значит, что используется максимум 1600. Конечно, в каких-то экстремальных ситуациях моряки выходят на максимальные мощности, но это бывает чрезвычайно редко (не более 500 часов в год). Несмотря на то что в последнее время несколько оживилось дело с боевой работой на флоте, выходом кораблей и лодок в море, но все равно мало они ходят. В советское время моторесурс нарабатывался намного больше.
— А когда на лодке работает дизель?
— Дизели работают для подзарядки батарей, в основном скрытным образом, ночью, на перископной глубине и когда лодка движется в надводном положении.
— На какой максимальной глубине возможно использовать дизель?
— 6 метров. Это так называемый режим РДП. Дизелю требуется для работы воздух. Максимальное противодавление, которое создается при глубине 6 метров, — 0,6 атмосферы. На выхлоп у дизеля давит водяной столб. Стоят специальные заслонки, которые не пускают воду в дизель. Есть относительно небольшая емкость, в нее попадают отработанные газы. И как только давление в этой емкости превысит давление этих шести метров, заслонки открываются и давлением газов, которое скопилось в емкости, выбрасывается столб воды. Вода, таким образом, в дизель не попадает. Устройство, благодаря которому работает дизель под водой, называется шноркель. Впервые оно было применено немцами еще во время Второй мировой войны на лодках ХХI серии, а нами — на 613-м проекте. Кстати, самому массовому в СССР. За всю историю советского подводного флота лодки 613-го проекта были самыми многочисленными. Благодаря использованию шноркеля лодка из «ныряющей» превратилась в по-настоящему подводную лодку. Нам — конструкторам дизелей для подлодок — это добавило массу новых задач.
— Технических?
— И технических, и технологических — всяких. Принципиально для работы под водой появляются два основных требования. Первое — необходимо обеспечить работу дизеля при противодавлении на выхлопе. То есть мы не можем пустить воду в дизель и постоянно должны ее выталкивать. В результате приходится в прямом смысле слова уродовать рабочий процесс работы дизеля как такового, а температуры рабочих процессов на лодочном двигателе на 25-30% выше на сухопутном. Расход топлива другой, и КПД под водой падает.
— В 70-е годы вами велись работы по снижению следности лодки из-за выхлопных газов…
— Да. Эти работы получили название «Проект «Защита 109». Выхлопные газы шли прямо в забортную воду. Лодка двигалась на глубине 25-30 метров. Газы растворялись в воде до достижения поверхности. То есть не было видно характерных пузырьков. Конечно, возникали определенные сложности с работой дизеля. Расход топлива резко увеличивался. Но это все было технологически решаемым.
Проблема была в другом. Совершенствовались средства обнаружения лодок. Дизель во время работы вырабатывает тепловое поле, которое никак не спрячешь, и способ избавления от пузырьков погружением на большую глубину оказался недостаточным для избавления от следности работающей дизельной установки лодки как таковой.
Пузырьки растворялись в воде. Но волнение на поверхности воды от движения подводного тела оставалось. С самолета или вертолета по характерному следу вычислялось положение лодки. Никуда не спрячешь тепловой след. Были и другие факторы, которых не удалось избежать для обеспечения скрытности лодки при движении ее на относительно небольших глубинах с работающим дизелем. Поэтому работы по «Защите 109» были прекращены.
— Немецкий проект «212» решил эти вопросы следности?
— С абсолютной уверенностью я этого сказать не могу. Но незаметно подкрасться со скоростью 3 узла в час она способна.— Когда вам давали ТТЗ на двигатель к проекту «Лада» — «Амур», какие сравнительные характеристики иностранных фирм были указаны? И рассматривался ли вопрос закупки дизелей иностранных фирм?
— Когда «Рубин» выбирал, какой двигатель ставить на «Санкт-Петербург», рассматривался вариант закупки импортного двигателя и велись переговоры с различными фирмами. Коломенский завод, находясь в крайне тяжелом экономическом положении, смог предложить двигательную установку, пропульсивного типа.
— Почему такая разница в цене двигателей для подводного флота у европейских стран-производителей?
— У них двигатели все высокооборотные и для каждой лодки — индивидуальные. Штучный товар, как принято говорить. У нас двигатель дешевый ввиду особенности конструкции — он сделан из модулей. Нам все равно, сколько цилиндров в двигателе делать, и это благодаря примененной модульной конструкции — в отличие от немцев или французов. Хотя сейчас немцы выкупили и английских, и французских производителей дизелей, а потом еще и объединились с американцами. Поэтому можно смело их всех немцами называть. Так вот, у них каждый двигатель делают индивидуально. Только нами, единственными в мире, применена модульная схема.
Уникальность ее состоит в том, что вся конструкция двигателя как бы разбита на блоки, на модули, которые делаются, испытываются, отдельно доводятся, а на сборке — как в детском конструкторе — складывается из готовых и проверенных узлов. У них подгонка и доводка осуществляется при общей сборке двигателя, что существенно удорожает производство.
Количество цилиндров 12 или 16 определяет конструктивный замысел по использованию дизеля. Мощность у MTU при разном количестве цилиндров — одинакова. Но при 16 цилиндрах машина менее форсирована, менее нагружена по эксплуатации. Тем самым закладывается больший моторесурс. У нас же каждый литр цилиндра нагружен меньше, поэтому и ресурс нашего двигателя больше.
— А как они отреагировали на возрождение конкурента?
— Нормально. «Исключительно гармоничная конструкция двигателя, к которой нечего добавить» — так отозвались специалисты фирмы MTU.
— На корвете проекта 20380 устанавливаются ваши двигательные установки?
— Да, разработанный нами тип Д49 обеспечивает диапазон мощностей от 500 до 6000 л.с., нужный для такого класса кораблей. Он имеет перспективы дальнейшего увеличения мощности за счет разного количества цилиндров и разной степени форсирования, то есть изменения давления в цилиндре. Главная задача, которую мы выполнили, с точки зрения производства — максимальная унификация. Все технологичнее и проще. Поэтому и цена ниже в пять раз по сравнению с другими. Разность в степени форсировки дает возможность варьировать моторесурс. Например, моторесурс на маневровый тепловоз — 100 000 часов до первого ремонта, на подлодке 20 000 часов, а на корабле — совсем другой. Унификация для завода очень удобна с точки зрения организации производства.
Все детали — что для дизеля тепловоза, что для подлодки, — все они на 87% одинаковы. Разница в настройке рабочего процесса, турбокомпрессора, топливной аппаратуры.
— Количеством дизельного топлива обеспечивается запас хода, а что используется в качестве топлива и чем его при необходимости можно заменить?
— Топливо — обычное дизельное топливо, как на автомобилях. Все военно-морские плавательные средства используют такое топливо, за исключением атомного флота.
— В последних ваших разработках возможно использовать в качестве топлива и сырую нефть, и природный газ. Значит ли это, что лодку можно «дозаправить», остановив в море любой танкер?
— Есть ряд конструктивных решений, позволяющих использовать и сжиженный природный газ, и сырую нефть в качестве топлива. Мы такие двигатели устанавливаем на ПБУ, которые ведут разведку и добычу нефти, на электростанции. В подлодках тоже можно использовать сырую нефть, но мощность будет немного ниже. Сырую нефть ввиду большой вязкости перед использованием надо слегка подогревать. Она тяжелее, хоть и имеет ряд легких фракций. Но самая большая проблема — наличие парафина. Парафин начинает «забивать» каналы топливной аппаратуры. Поэтому, если гипотетически предположить такую ситуацию, какое-то время можно пройти на таком топливе, но потом надо двигатель разбирать и ремонтировать.
— Почему вы отказались от размерности 30/38?
— Мы не отказались от нее. Это классика дизелестроения для подводного флота. Еще в 20-х годах прошлого века Коломенский завод начал выпускать двигатели размерности 30/38 — аналог немецкого 38К-8 по лицензии и технологии фирмы MAN. Она специально разработана для подлодок, используется и по сей день японцами — это фирма «Мицубиси» — и другими странами как одна из лучших размерностей в дизелестроении. Рядом стран ведутся разработки в очень близком диапазоне.
Мы изначально выбрали размерность 26/26 из соображений компактности для размещения внутри ограниченных объемов подводных лодок последнего поколения. А для лодок водоизмещением более полутора тысяч тонн, где места больше, например проект 877 «Кило», мы ставим двигатель типа 30/38. На китайский заказ — строящиеся для ВМФ Китая лодки — тоже будет установлен двигатель ЧН 30/38, как и на индийских лодках этого проекта. «Санкт-Петербург» — это первая лодка с двигательной установкой размерности 26/26. Предварительно можно сказать, что очень удачная и тихая получилась конструкция, но┘ поживем — увидим.
— Понижение шумности обусловлено конструктивными особенностями?
— Да. Так сделали конструкцию. Защитные стенки блока изолированы. Поставлены добавочные экраны и так далее. Мы ограничиваем проникновение шума наружу и применяем специальные меры по его снижению. Не случайно наш двигатель считается одним из самым «тихих» в мире.
— Редуктор для корвета — это коломенская разработка?
— Нет. Дизельные агрегаты производим мы — ОАО «Коломенский завод», редуктор и звукоизолирующую муфту поставляет ОАО «Звезда» (Санкт-Петербург), трансмиссионные валы, упругодеформируемые муфты — из Николаева («Машпроект»), главный гребной вал делает Балтийский завод, системы автоматического управления — HПП «Аврора» (Санкт-Петербург), подшипники главного гребного вала — «Севмаш» (Северодвинск). Вот какие предприятия участвуют в производстве пропульсивной двигательной установки. Но впервые в мировой практике мы этот комплекс собираем и тестируем в стенах завода, производящего двигатель, а не при сборке корабля. Мы производим теперь не отдельный узел энергоустановки, а конечный продукт. Тем самым исключаются проблемы при сборке и доводке двигательной установки на объекте. Это значимое событие не только для нас, но и для всего ВМФ. Ведь теперь создается не ниокровский задел, а выработано целое принципиальное решение. Это новая схема и принцип организации работ, значительно удешевляющий конечную стоимость корабля в целом.
P.S.
В нынешней ситуации вопросы антитеррора, охраны приграничной зоны, локальные конфликты приоритетны и возникают чаще, чем потребность решать глобальные стратегические проблемы обороны в целом. Дорогой атомный флот отходит на вторые позиции. Многие специалисты предприятия считают, что не иметь быстрого пограничного флота, оснащенного высокоманевренными и мобильными кораблями класса «Корвет» — это очень недальновидно и просто преступно в интересах обороноспособности России. По цене корвет с дизельной энергоустановкой несопоставим со стоимостью атомохода. А вопросы, решаемые таким классом кораблей, к сожалению, возникают в последнее время слишком часто.
Не менее важны вопросы переоборудования старых или оснащения недостроенных кораблей современными двигательными установками. Причем для российского дизелестроения не принципиально, под каким флагом вступает в строй новый агрегат. Например, российский бюджет существенно проиграл, уступив финнам индийский рынок. Почему переоборудование энергоустановки на «Адмирале Горшкове» будут производить в Финляндии? Авианосец был не востребован в России и куплен для ВМС Индии. Коломенские двигатели туда органично вписывались, поскольку проект был рассчитан под них. Россия проиграла свой рынок из-за того, что фирма «Вяртсиля» — финский производитель дизельных двигателей — в Индии создала свою ремонтную базу. Финны продали лицензии, открыли сервисные центры и потихоньку «прибрали» индийский рынок. Они дают индусам возможность производить часть запасных частей. Именно поэтому Индия, не исходя из параметров цена-качество, а из-за того, что с «Вяртсиля» хорошая завязка в смысле сервиса, отдала предпочтение скандинавам, а не России. Поэтому индусы теперь ориентированы на финские машины. Вот почему было принято решение на авианосце «Адмирал Горшков» ставить при переоборудовании дизели «Вяртсиля», а не «Коломенского завода». На сегодняшний день с Индией у российских двигателестроителей никаких контрактов, договоров на приобретение новых дизелей нет.
Опасные тенденции намечаются и на других территориальных рынках. Объединение немцев с американцами, создание MTU Friedrichshafen GmbH — Detroit Diesel Corporation, фирма MAN, поглотившая французскую Pielstick и другие мировые фирмы — это не просто настораживает и вызывает серьезные опасения. Германия наращивает производство своих лодок 212-го проекта. Поэтому нужно максимально чутко реагировать на тенденции мирового рынка. Может, имеет смысл рассмотреть возможности научной, исследовательской и конструкторской работ по «топливным элементам». Пусть они сейчас громоздки и маломощны. ЭВМ ведь тоже были двухэтажными.
На сегодняшний день у подмосковных дизелистов реально существуют две ключевые сложности.
Первая — это необходимость заключения долгосрочных контрактов от ВМФ и РЖД, которые бы гарантировали наличие заказа. Это послужило бы основой для принятия решения о дополнительных инвестициях. В отсутствие контрактов на 5-7 лет предприятие, прогнозируя рост сбыта, инвестиции проводит самостоятельно, но не столько, сколько было бы разумно.
Второй, более значимый вопрос — это кадры. На сегодняшний день возраст наиболее квалифицированных конструкторов предельный. Молодежь с трудом идет на завод, в машиностроение. Предприятие не может молодым инженерам платить высокие зарплаты. А конструктора, технолога нужно воспитывать не один год. Предприятие сколько может — столько инвестирует в кадры, но это капля в море. К сожалению, уровень заработной платы производственных, рабочих и инженерных кадров в машиностроении России далеко не такой, как на Западе. Государственной программы поддержки молодого инженера нет.
Если обеспечить решение хотя бы эти двух вопросов, то в стране не будет импорта дорогих дизельных двигателей. Ведь импорт — это не просто потеря валюты. Уходят деньги, меняется внешнеторговый баланс. В каждом двигателе заложены определенные отчисления на науку, на КБ, социальную составляющую. Каждый купленный двигатель или собранный по лицензии — это поддержка конструкторской школы другой страны и потеря своего потенциала. Вот о чем стоит серьезно задуматься.
Из досье «НВО»
Евгений Александрович Никитин родился в 1927 г. Окончил Всесоюзный заочный политехнический институт. С 1946 г. работает на Коломенском заводе, где прошел путь от инженера-конструктора до главного конструктора по машиностроению и проработал в этой должности 32 года. Доктор технических наук, крупнейший ведущий специалист в области дизелестроения. Автор и редактор многих книг, монографий, справочников и статей по различным научно-техническим вопросам дизелестроения. Лауреат Государственной премии СССР в области науки и техники. Имеет звания: заслуженный деятель науки и техники РСФСР, почетный работник Министерства тяжелого, энергетического и транспортного машиностроения СССР.
Используемые двигатели для подводного флота европейскими странами-производителями.
Марка двигателя | MTU 12V 396 SE 84 | MTU 16V 396 SE 84 | 12 PA 4.200 | A210.16 SM GMT | 8 ЧН 26/26(28 ДГ) |
Страна/фирма производитель |
Германия MTU |
Франция Pielstick | Италия Grandi Motori Trieste | Россия ОАО «Коломенский завод» | |
Количество цилиндров | 12 | 16 | 12 | 16 | 8 |
Рабочий цикл |
Четырехтактный | ||||
Номинальная мощность | 1800 | 1800 | 1300 | 1500 | 1250 |
Рабочий объем цилиндра (литры) | 3.96 | 3.96 | ═ | ═ | 14 |
Диаметр поршня, | 165 | 165 | ═ | 210 | 260 |
ход поршня | 185 | 185 | ═ | 230 | 260 |
Абсолютное противодавление на выхлопе компрессора двигателя | 1600 | 1600 | 1680 | 1560 | 1422 При продувании главного балласта |
Стоимость по состоянию на декабрь 1997 г. | 1 560 000 | 1 700 000 | Одна/ две поставки 3 062 700 2 792 000 | 2 453 00 | 450 000 |
nvo.ng.ru
Дизельный двигатель
В последнее десятилетие дизельные технологии развиваются впечатляющими темпами. Модификации легковых авто с дизельными моторами составляют половину новых автомобилей, продаваемых в Европе. Густой черный дым из выхлопной трубы, громкое тарахтение и неприятный запах остались далеко в прошлом. Дизельные моторы сегодня – это не только экономичность, но также высокая мощность и достойные динамические характеристики.
Современный дизель стал тихим и экологически чистым. Как же удалось этому типу ДВС соответствовать постоянно ужесточающимся нормам токсичности и при этом не только не проигрывать в тяговитости и экономичности, но и улучшать эти показатели? Рассмотрим все по порядку…
Содержание статьи
Принцип работы
На первый взгляд дизельный двигатель почти не отличается от обычного бензинового – те же цилиндры, поршни, шатуны. Главные и принципиальные отличия заключаются в способе образования и воспламенения. В карбюраторных и обычных инжекторных двигателях приготовление смеси происходит не в цилиндре, а во впускном тракте.
В бензиновых двигателях с непосредственным впрыском смесь образуется так же как и в дизелях- непосредственно в цилиндре. В бензиновом моторе топливо-воздушная смесь в цилиндре воспламеняется в нужный момент от искрового разряда. В дизеле же топливо воспламеняется не от искры, а вследствие высокой температуры воздуха в цилиндре.
Рабочий процесс в дизеле происходит следущим образом: вначале в цилиндр попадает чистый воздух, который за счет большой степени сжатия (16-24:1) разогревается до 700-900°С. Дизтопливо впрыскивается под высоким давлением в камеру сгорания при подходе поршня к верхней мертвой точке. А так как воздух уже сильно разогрет, после смешивания с ним происходит воспламенение топлива. Самовоспламенение сопровождается резким нарастанием давления в цилиндре – отсюда повышенная шумность и жесткость работы дизеля.
Такая организация рабочего процесса позволяет использовать более дешевое топливо и работать на очень бедных смесях, что определяет более высокую экономичность. Дизель имеет больший КПД (у дизеля – 35–45%, у бензинового – 25–35%) и крутящий момент. К недостаткам дизельных двигателей обычно относят повышенную шумность и вибрацию, меньшую литровую мощность и трудности холодного пуска. Но описанные недостатки относятся в основном к старым конструкциям, а в современных эти проблемы уже не являются столь очевидными.
Конструкция
Особенности
Как уже отмечалось, конструкция дизельного двигателя подобна конструкции бензинового двигателя. Однако аналогичные детали у дизеля существенно усилены, чтобы воспринимать более высокие нагрузки – ведь степень сжатия у него намного выше (16-24 единиц против 9-11 у бензинового). Характерная деталь в конструкции дизелей — это поршень.
Форма днища поршней у дизелей определяется типом камеры сгорания, поэтому по форме легко определить, какому двигателю принадлежит данный поршень. Во многих случаях днище поршня содержит в себе камеру сгорания. Днища поршней находятся выше верхней плоскости блока цилиндров, когда поршень находится в верхней точке своего хода.
Так как воспламенение рабочей смеси осуществляется от сжатия, в дизелях отсутствует система зажигания, хотя свечи могут применяться и на дизеле. Но это не свечи зажигания, а свечи накаливания, которые предназначены для подогрева воздуха в камере сгорания при холодном пуске двигателя.
Поршни и свечи дизеляТехнические и экологические показатели автомобильного дизельного двигателя в первую очередь зависят от типа камеры сгорания и системы впрыскивания топлива.
Типы камер сгорания
Форма камеры сгорания значительно влияет на качество процесса смесеобразования, а значит и на мощность и шумность работы двигателя. Камеры сгорания дизельных двигателей разделяются на два основных типа: неразделенные и разделенные.
Несколько лет назад на рынке легкового машиностроения доминировали дизели с разделенными камерами сгорания. Впрыск топлива в этом случае осуществляется не в надпоршневое пространство, а в специальную камеру сгорания, выполненную в головке блока цилиндров. При этом различают два процесса смесеобразования: предкамерный (его еще называют форкамерным) и вихрекамерный.
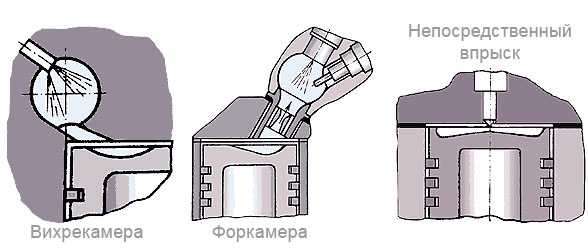
При форкамерном процессе топливо впрыскивается в специальную предварительную камеру, связанную с цилиндром несколькими небольшими каналами или отверстиями, ударяется об ее стенки и перемешивается с воздухом. Воспламенившись, смесь поступает в основную камеру сгорания, где и сгорает полностью. Сечение каналов подбирается так, чтобы при ходе поршня вверх (сжатие) и вниз (расширение) между цилиндром и форкамерой возникал большой перепад давления, вызывающий течение газов через отверстия с большой скоростью.
Во время вихрекамерного процесса сгорание также начинается в специальной отдельной камере, только выполненной в виде полого шара. В период такта сжатия воздух по соединительному каналу поступает в предкамеру и интенсивно закручивается (образует вихрь) в ней. Впрыснутое в определенный момент топливо хорошо перемешивается с воздухом.
Таким образом, при разделенной камере сгорания происходит как бы двухступенчатое сгорание топлива. Это снижает нагрузку на поршневую группу, а также делает звук работы двигателя более мягким. Недостатком дизельных двигателей с разделенной камерой сгорания являются: увеличение расхода топлива вследствие потерь из-за увеличенной поверхности камеры сгорания, больших потерь на перетекание воздушного заряда в дополнительную камеру и горящей смеси обратно в цилиндр. Кроме того, ухудшаются пусковые качества.
Дизельные двигатели с неразделенной камерой называют также дизелями с непосредственным впрыском. Топливо впрыскивается непосредственно в
цилиндр, камера сгорания выполнена в днище поршня. До недавнего времени непосредственный впрыск использовался на низкооборотистых дизелях большого объема (проще говоря, на грузовиках). Хотя такие двигатели экономичнее моторов с разделенными камерами сгорания, их применение на небольших дизелях сдерживалось трудностями организации процесса сгорания, а также повышенными шумом и вибрацией, особенно в режиме разгона.
Сейчас благодаря повсеместному внедрению электронного управления процессом дозирования топлива удалось оптимизировать процесс сгорания топливной смеси в дизеле с неразделенной камерой сгорания и существенно снизить шумность. Новые дизельные двигатели разрабатываются только с непосредственным впрыском.
Системы питания
Важнейшим звеном дизельного двигателя является система топливоподачи, обеспечивающая поступление необходимого количества топлива в нужный момент времени и с заданным давлением в камеру сгорания.
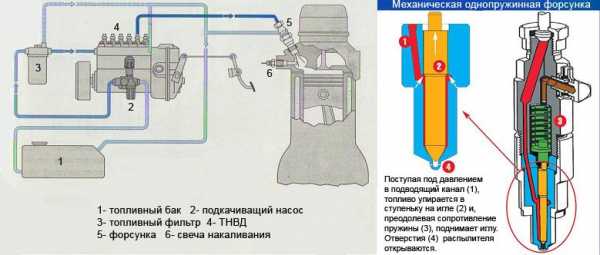
Топливный насос высокого давления (ТНВД), принимая горючее из бака от подкачивающего насоса (низкого давления), в требуемой последовательности поочередно нагнетает нужные порции солярки в индивидуальную магистраль гидромеханической форсунки каждого цилиндра. Такие форсунки открываются исключительно под воздействием высокого давления в топливной магистрали и закрываются при его снижении.
Существует два типа ТНВД: рядные многоплунжерные и распределительного типа. Рядный ТНВД состоит из отдельных секций по числу цилиндров дизеля, каждая из которых имеет гильзу и входящий в нее плунжер, который приводится в движение кулачковым валом, получающим вращение от двигателя. Секции таких механизмов расположены, как правило, в ряд, отсюда и название – рядные ТНВД. Рядные насосы в настоящее время практически не применяются ввиду того, что они не могут обеспечить выполнение современных требований по экологии и шумности. Кроме того, давление впрыска таких насосов зависит от оборотов коленвала.
Распределительные ТНВД создают значительно более высокое давление впрыска топлива, нежели насосы рядные, и обеспечивают выполнение действующих нормативов, регламентирующих токсичность выхлопа. Этот механизм поддерживает нужное давление в системе в зависимости от режима работы двигателя. В распределительных ТНВД система нагнетания имеет один плунжер-распределитель, совершающий поступательное движение для нагнетания топлива и вращательное для распределения топлива по форсункам.
Эти насосы компактны, отличаются высокой равномерностью подачи топлива по цилиндрам и отличной работой на высоких оборотах. В то же время они предъявляют очень высокие требования к чистоте и качеству дизтоплива: ведь все их детали смазываются топливом, а зазоры в прецизионных элементах очень малы.
Ужесточение в начале 90-х законодательных экологических требований, предъявляемых к дизелям, заставило моторостроителей интенсивно совершенствовать топливоподачу. Сразу же стало ясно, что с устаревшей механической системой питания эту задачу не решить. Традиционные механические системы впрыска топлива имеют существенный недостаток: давление впрыска зависит от частоты вращения двигателя и нагрузочного режима.
Это значит, что при низкой нагрузке давление впрыска падает, в результате топливо при впрыске плохо распыляется, попадая в камеру сгорания слишком крупными каплями, которые оседают на ее внутренних поверхностях. Из-за этого уменьшается КПД сгорания топлива и повышается уровень токсичности отработанных газов.
Кардинально изменить ситуацию могла только оптимизация процесса горения топливо – воздушной смеси. Для чего надо заставить весь её объём воспламениться в максимально короткое время. А здесь необходима высокая точность дозы и точность момента впрыскивания. Сделать это можно, только подняв давление впрыска топлива и применив электронное управление процессом топливоподачи. Дело в том, что чем выше давление впрыска, тем лучше качество его распыления, а соответственно – и смешивания с воздухом.
В конечном итоге это способствует более полному сгоранию топливо-воздушной смеси, а значит и уменьшению вредных веществ в выхлопе. Хорошо, спросите вы, а почему бы не сделать такое же повышенное давление в обычном ТНВД и всей этой системе? Увы, не получится. Потому что есть такое понятие, как “волновое гидравлическое давление”. При любом изменении расхода топлива в трубопроводах от ТНВД к форсункам возникают волны давления, “бегающие” по топливопроводу. И чем сильнее давление, тем сильнее эти волны. И если далее повышать давление, то в какой-то момент может произойти обыкновенное разрушение трубопроводов. Ну, а о точности дозирования механической системы впрыска даже и говорить не приходится.

В результате были разработаны два новых типа систем питания – в первом форсунку и плунжерный насос объединили в один узел (насос-форсунка), а в другом ТНВД начал работать на общую топливную магистраль (Common Rail), из которой топливо поступает на электромагнитные (или пьезоэлектрические) форсунки и впрыскивается по команде электронного блока управления. Но с принятием Евро 3 и 4 и этого оказалось мало, и в выхлопные системы дизелей внедрили сажевые фильтры и катализаторы.
Насос-форсунка устанавливается в головку блока двигателя для каждого цилиндра. Она приводится в действие от кулачка распределительного вала с помощью толкателя. Магистрали подачи и слива топлива выполнены в виде каналов в головке блока. За счет этого насос-форсунка может развить давление до 2200 бар. Дозированием топлива, сжатого до такой степени и управлением угла опережения впрыска занимается электронный блок управления, выдавая сигналы на запорные электромагнитные или пьезоэлектрические клапаны насос-форсунок.
Насос-форсунки могут работать в многоимпульсном режиме (2-4 впрыска за цикл). Это позволяет произвести предварительный впрыск перед основным, подавая в цилиндр сначала небольшую порцию топлива, что смягчает работу мотора и снижает токсичность выхлопа. Недостаток насос-форсунок – зависимость давления впрыска от оборотов двигателя и высокая стоимость данной технологии.
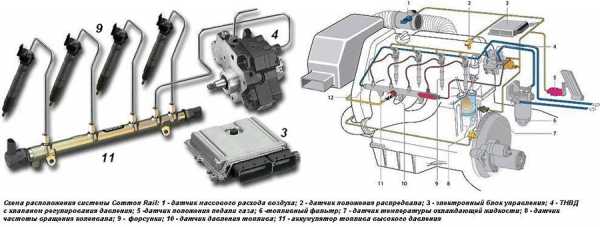
Система питания Common Rail используется в дизелях серийных моделей с 1997 года. Common Rail – это метод впрыска топлива в камеру сгорания под высоким давлением, не зависящим от частоты вращения двигателя или нагрузки. Главное отличие системы Common Rail от классической дизельной системы заключается в том, что ТНВД предназначен только для создания высокого давления в топливной магистрали. Он не выполняет функций дозировки цикловой подачи топлива и регулировки момента впрыска.
Система Common Rail состоит из резервуара – аккумулятора высокого давления (иногда его называют рампой), топливного насоса, электронного блока управления (ЭБУ) и комплекта форсунок, соединенных с рампой. В рампе блок управления поддерживает, меняя производительность насоса, постоянное давление на уровне 1600-2000 бар при различных режимах работы двигателя и при любой последовательности впрыска по цилиндрам.
Открытием-закрытием форсунок управляет ЭБУ, который рассчитывает оптимальный момент и длительность впрыска, на основании данных целого ряда датчиков – положения педали акселератора, давления в топливной рампе, температурного режима двигателя, его нагрузки и т. п. Форсунки могуть быть электромагнитными, либо более современными- пьезоэлектрическими. Главные преимущества пьезоэлектрических форсунок – высокая скорость срабатывания и точность дозирования. Форсунки в дизелях c Common rail могут работать в многоимпульсном режиме: в ходе одного цикла топливо впрыскивается несколько раз – от двух до семи. Сначала поступает крохотная, всего около милиграмма, доза, которая при сгорании повышает температуру в камере, а следом идет главный «заряд».
Для дизеля — двигателя с воспламенением топлива от сжатия — это очень важно, так как при этом давление в камере сгорания нарастает более плавно, без «рывка». Вследствие этого мотор работает мягче и менее шумно, снижается количество вредных компонентов в выхлопе. Многократная подача топлива за один такт попутно обеспечивает снижение температуры в камере сгорания, что приводит к уменьшению образования окиси азота- одной из наиболее токсичных составляющих выхлопных газов дизеля.
Характеристики двигателя с Common Rail во многом зависят от давления впрыска. В системах третьего поколения оно составляет 2000 бар. В ближайшее время в серию будет запущено четвертое поколение Common Rail с давлением впрыска 2500 бар.
Турбодизель
Эффективным средством повышения мощности и гибкости работы является турбонаддув двигателя. Он позволяет подать в цилиндры дополнительное количество воздуха и соответственно увеличить подачу топлива на рабочем цикле, в результате чего увеличивается мощность двигателя.
Давление выхлопных газов дизеля в 1,5-2 раза выше, чем у бензинового мотора, что позволяет турбокомпрессору обеспечить эффективный наддув с самых низких оборотов, избежав свойственного бензиновым турбомоторам провала – “турбоямы”. Отсутствие дроссельной заслонки в дизеле позволяет обеспечить эффективное наполнение цилиндров на всех оборотах без применения сложной схемы управления турбокомпрессором.
На многих автомобилях устанавливается промежуточный охладитель наддуваемого воздуха – интеркулер, позволяющий поднять массовое наполнение цилиндров и на 15-20 % увеличить мощность. Наддув позволяет добиться одинаковой мощности с атмосферным мотором при меньшем рабочем объеме, а значит, снизить массу двигателя. Турбонаддув, помимо всего прочего, служит для автомобиля средством повышения “высотности” двигателя – в высокогорных районах, где атмосферному дизелю не хватает воздуха, наддув оптимизирует сгорание и позволяет уменьшить жесткость работы и потерю мощности.
В то же время турбодизель имеет и некоторые недостатки, связанные в основном с надежностью работы турбокомпрессора. Так, ресурс турбокомпрессора существенно меньше ресурса двигателя. Турбокомпрессор предъявляет жесткие требования к качеству моторного масла. Неисправный агрегат может полностью вывести из строя сам двигатель. Кроме того, собственный ресурс турбодизеля несколько ниже такого же атмосферного дизеля из-за большой степени форсирования. Такие двигатели имеют повышенную температуру газов в камере сгорания, и чтобы добиться надежной работы поршня, его приходится охлаждать маслом, подаваемым снизу через специальные форсунки.
Прогресс дизельных двигателей сегодня преследует две основные цели: увеличение мощности и уменьшение токсичности. Поэтому все современные легковые дизели имеют турбонаддув (самый эффективный способ увеличения мощности) и Соmmоn Rail.
avtonov.info
Дизельный двигатель — это… Что такое Дизельный двигатель?
Ди́зельный дви́гатель — поршневой двигатель внутреннего сгорания, работающий по принципу самовоспламенения распылённого топлива от воздействия разогретого при сжатии воздуха.[1]
Спектр топлива для дизелей весьма широк, сюда включаются все фракции нефтеперегонки от керосина до мазута и ряд продуктов природного происхождения — рапсовое масло, фритюрный жир, пальмовое масло и многие другие. Дизель может с определённым успехом работать и на сырой нефти.
Компрессионные карбюраторные двигатели не относят к дизельным двигателям, так как в «дизелях» происходит сжатие чистого воздуха, а не топливо-воздушной смеси. Топливо впрыскивается в конце такта сжатия.[2][3].
История
В 1824 году Сади Карно формулирует идею цикла Карно, утверждая, что в максимально экономичной тепловой машине нагревать рабочее тело до температуры горения топлива необходимо «изменением объема», то есть быстрым сжатием. В 1890 году Рудольф Дизель предложил свой способ практической реализации этого принципа. Он получил патент на свой двигатель 23 февраля 1892 года (в США в 1895 году[2]), в 1893 году выпустил брошюру. Ещё несколько вариантов конструкции были им запатентованы позднее.[3] После нескольких неудач первый практически применимый образец, названый Дизель-мотором, был построен Дизелем к началу 1897 года, и 28 января того же года он был успешно испытан. Дизель активно занялся продажей лицензий на новый двигатель. Несмотря на высокий КПД и удобство эксплуатации по сравнению с паровой машиной практическое применение такого двигателя было ограниченным: он уступал паровым машинам того времени по размерам и весу.
Первые двигатели Дизеля работали на растительных маслах или лёгких нефтепродуктах. Интересно, что первоначально в качестве идеального топлива он предлагал каменноугольную пыль. Эксперименты же показали невозможность использования угольной пыли в качестве топлива — прежде всего из-за высоких абразивных свойств как самой пыли, так и золы, получающейся при сгорании; также возникали большие проблемы с подачей пыли в цилиндры.
Инженер Экройд Стюарт (англ.)русск. ранее высказывал похожие идеи и в 1886 году построил действующий двигатель (см. полудизель). Он предложил двигатель, в котором воздух втягивался в цилиндр, сжимался, а затем нагнетался (в конце такта сжатия) в ёмкость, в которую впрыскивалось топливо. Для запуска двигателя ёмкость нагревалась лампой снаружи, и после запуска самостоятельная работа поддерживалась без подвода тепла снаружи. Экройд Стюарт не рассматривал преимущества работы от высокой степени сжатия, он просто экспериментировал с возможностями исключения из двигателя свечей зажигания, то есть он не обратил внимания на самое большое преимущество — топливную эффективность.
Независимо от Дизеля в 1898 году на Путиловском заводе в Петербурге инженером Густавом Тринклером был построен первый в мире «бескомпрессорный нефтяной двигатель высокого давления», то есть дизельный двигатель в его современном виде с форкамерой, который назвали «Тринклер-мотором». При сопоставлении Дизель-мотора и Тринклер-мотора русская конструкция, появившаяся на полтора года позднее немецкой и испытанная на год позднее, оказалась гораздо более удачной в плане практического использования. Именно Тринклер-мотор был первым двигателем с воспламенением от сжатия, работавшим на сырой нефти. Использование гидравлической системы для нагнетания и впрыска топлива позволило отказаться от отдельного воздушного компрессора и сделало возможным увеличение скорости вращения. Российская конструкция оказалась проще, надёжнее и перспективнее немецкой.[4] Однако под давлением Нобелей и других обладателей лицензий Дизеля работы над двигателем в 1902 году были прекращены.
В 1898 г. Эммануэль Нобель приобрёл лицензию на двигатель внутреннего сгорания Рудольфа Дизеля. С 1899 г. Механический завод «Людвиг Нобель» в Петербурге развернул массовое производство дизелей. В Петербурге Тринклер приспособил двигатель для работы на сырой нефти вместо керосина. В 1900 г на Всемирной выставке в Париже двигатель Дизеля получил Гран-при, чему способствовало известие, что завод Нобеля в Петербурге наладил выпуск двигателей, работавших на сырой нефти. Этот двигатель получил в Европе название «русский дизель».[5] Выдающийся русский инженер Аршаулов впервые построил и внедрил топливный насос высокого давления оригинальной конструкции — с приводом от сжимаемого в цилиндре воздуха, работавший с бескомпрессорной форсункой (В. Т. Цветков, «Двигатели внутреннего сгорания», МАШГИЗ, 1954 г.).
В настоящее время для обозначения ДВС с воспламенением от сжатия используется термин «двигатель Дизеля», «дизельный двигатель» или просто «дизель», так как теория Рудольфа Дизеля стала основой для создания современных двигателей этого типа. В дальнейшем около 20—30 лет такие двигатели широко применялись в стационарных механизмах и силовых установках морских судов, однако существовавшие тогда системы впрыска топлива с воздушными компрессорами не позволяли применять дизели в высокооборотных агрегатах. Небольшая скорость вращения, значительный вес воздушного компрессора, необходимого для работы системы впрыска топлива сделали невозможным применение первых дизелей на автотранспорте.
В 20-е годы XX века немецкий инженер Роберт Бош усовершенствовал встроенный топливный насос высокого давления, устройство, которое широко применяется и в наше время. Он же создал удачную модификацию бескомпрессорной форсунки. Востребованный в таком виде высокооборотный дизель стал пользоваться всё большей популярностью как силовой агрегат для вспомогательного и общественного транспорта, однако доводы в пользу карбюраторных двигателей (традиционный принцип работы, лёгкость и небольшая цена производства) позволяли им пользоваться большим спросом для установки на пассажирских и небольших грузовых автомобилях: с 50-х — 60-х годов XX века дизель устанавливается в больших количествах на грузовые автомобили и автофургоны, а в 70-е годы после резкого роста цен на топливо на него обращают серьёзное внимание мировые производители недорогих маленьких пассажирских автомобилей.
В дальнейшие годы происходит рост популярности дизельных двигателей для легковых и грузовых автомобилей, не только из-за экономичности и долговечности дизеля, но также из-за меньшей токсичности выбросов в атмосферу. Все ведущие европейские производители автомобилей в настоящее время имеют модели с дизельным двигателем.
Дизельные двигатели применяются также на железной дороге. Локомотивы, использующие дизельный двигатель — тепловозы — являются основным видом локомотивов на неэлектрифицированных участках, дополняя электровозы за счёт автономности. Тепловозы перевозят до 40 % грузов и пассажиров в России, они выполняют 98 % маневровой работы[источник не указан 995 дней]. Существуют также одиночные автомотрисы, дрезины и мотовозы, которые повсеместно используются на электрифицированных и неэлектрифицированных участках для обслуживания и ремонта пути и объектов инфраструктуры. Иногда автомотрисы и небольшие дизель-поезда называют рельсовыми автобусами.
Принцип работы
Четырёхтактный цикл
Работа четырёхтактного дизельного двигателя.- 1-й такт. Впуск. Соответствует 0° — 180° поворота коленвала. Через открытый ~от 345—355° впускной клапан воздух поступает в цилиндр, на 190—210° клапан закрывается. По крайней мере до 10-15° поворота коленвала одновременно открыт выхлопной клапан, время совместного открытия клапанов называется перекрытием клапанов.
- 2-й такт. Сжатие. Соответствует 180° — 360° поворота коленвала. Поршень, двигаясь к ВМТ (верхней мёртвой точке), сжимает воздух в 16(в тихоходных)-25(в быстроходных) раз.
- 3-й такт. Рабочий ход, расширение. Соответствует 360° — 540° поворота коленвала. При распылении топлива в горячий воздух происходит инициация сгорания топлива, то есть частичное его испарение, образование свободных радикалов в поверхностных слоях капель и в парáх, наконец, оно вспыхивает и сгорает по мере поступления из форсунки, продукты горения, расширяясь, двигают поршень вниз. Впрыск и, соответственно, воспламенение топлива происходит чуть раньше момента достижения поршнем мёртвой точки вследствие некоторой инертности процесса горения. Отличие от опережения зажигания в бензиновых двигателях в том, что задержка необходима только из-за наличия времени инициации, которое в каждом конкретном дизеле — величина постоянная и изменению в процессе работы не подлежит. Сгорание топлива в дизеле происходит, таким образом, длительно, столько времени, сколько длится подача порции топлива из форсунки. Вследствие этого рабочий процесс протекает при относительно постоянном давлении газов, из-за чего двигатель развивает большой крутящий момент. Из этого следуют два важнейшие вывода.
- 1. Процесс горения в дизеле длится ровно столько времени, сколько требуется для впрыска данной порции топлива, но не дольше времени рабочего хода.
- 2. Соотношение топливо/воздух в цилиндре дизеля может существенно отличаться от стехиометрического, причем очень важно обеспечить избыток воздуха, так как пламя факела занимает небольшую часть объема камеры сгорания и атмосфера в камере должна до последнего обеспечить нужное содержание кислорода. Если этого не происходит, возникает массивный выброс несгоревших углеводородов с сажей — «тепловоз „даёт“ медведя».).
- 4-й такт. Выпуск. Соответствует 540° — 720° поворота коленвала. Поршень идёт вверх, через открытый на 520—530° выхлопной клапан поршень выталкивает отработавшие газы из цилиндра.
Далее цикл повторяется.
В зависимости от конструкции камеры сгорания, существует несколько типов дизельных двигателей:
- Дизель с неразделённой камерой: камера сгорания выполнена в поршне, а топливо впрыскивается в надпоршневое пространство. Главное достоинство — минимальный расход топлива. Недостаток — повышенный шум («жесткая работа»), особенно на холостом ходу. В настоящее время ведутся интенсивные работы по устранению указанного недостатка. Например, в системе Common Rail для снижения жёсткости работы используется (зачастую многостадийный) предвпрыск.
- Дизель с разделённой камерой: топливо подаётся в дополнительную камеру. В большинстве дизелей такая камера (она называется вихревой либо предкамерой) связана с цилиндром специальным каналом так, чтобы при сжатии воздух, попадая в оную камеру, интенсивно завихрялся. Это способствует хорошему перемешиванию впрыскиваемого топлива с воздухом и более полному сгоранию топлива. Такая схема долго считалась оптимальной для легких дизелей и широко использовалась на легковых автомобилях. Однако, вследствие худшей экономичности, последние два десятилетия идёт активное вытеснение таких дизелей двигателями с нераздельной камерой и с системами подачи топлива Common Rail.
Двухтактный цикл
Принцип работы двухтактного дизельного двигателя Продувка двухтактного дизельного двигателя: внизу — продувочные окна, выпускной клапан верху открытКроме вышеописанного четырёхтактного цикла, в дизеле возможно использование двухтактного цикла.
При рабочем ходе поршень идёт вниз, открывая выпускные окна в стенке цилиндра, через них выходят выхлопные газы, одновременно или несколько позднее открываются и впускные окна, цилиндр продувается свежим воздухом из воздуходувки — осуществляется продувка, совмещающая такты впуска и выпуска. Когда поршень поднимается, все окна закрываются. С момента закрытия впускных окон начинается сжатие. Чуть не достигая ВМТ, из форсунки распыляется и загорается топливо. Происходит расширение — поршень идёт вниз и снова открывает все окна и т. д.
Продувка является врожденным слабым звеном двухтактного цикла. Время продувки, в сравнением с другими тактами, невелико и увеличить его невозможно, иначе будет падать эффективность рабочего хода за счет его укорочения. В четырёхтактном цикле на те же процессы отводится половина цикла. Полностью разделить выхлоп и свежий воздушный заряд тоже невозможно, поэтому часть воздуха теряется, выходя прямо в выхлопную трубу. Если же смену тактов обеспечивает один и тот же поршень, возникает проблема, связанная с симметрией открывания и закрывания окон. Для лучшего газообмена выгоднее иметь опережение открытия и закрытия выхлопных окон. Тогда выхлоп, начинаясь ранее, обеспечит снижение давления остаточных газов в цилиндре к началу продувки. При закрытых ранее выхлопных окнах и открытых — еще — впускных осуществляется дозарядка цилиндра воздухом, и, если воздуходувка обеспечивает избыточное давление, становится возможным осуществление наддува.
Окна могут использоваться и для выпуска отработавших газов, и для впуска свежего воздуха; такая продувка называется щелевой или оконной. Если отработавшие газы выпускаются через клапан в головке цилиндра, а окна используются только для впуска свежего воздуха, продувка называется клапанно-щелевой. Существуют двигатели, где в каждом цилиндре находятся два встречно двигающихся поршня; каждый поршень управляет своими окнами — один впускными, другой выпускными (система Фербенкс-Морзе — Юнкерса — Корейво: дизели этой системы семейства Д100 использовались на тепловозах ТЭ3, ТЭ10, танковых двигателях 4ТПД, 5ТД(Ф) (Т-64), 6ТД (Т-80УД), 6ТД-2 (Т-84), в авиации — на бомбардировщиках Junkers (Jumo 204, Jumo 205).
В двухтактном двигателе рабочие ходы происходят вдвое чаще, чем в четырёхтактном, но из-за наличия продувки двухтактный дизель мощнее такого же по объёму четырёхтактного максимум в 1,6—1,7 раз.
В настоящее время тихоходные двухтактные дизели весьма широко применяются на больших морских судах с непосредственным (безредукторным) приводом гребного винта. Ввиду удвоения количества рабочих ходов на одних и тех же оборотах двухтактный цикл оказывается выгодным при невозможности повысить частоту вращения, кроме того, двухтактный дизель технически проще реверсировать; такие тихоходные дизели имеют мощность до 100 000 л.с.
В связи с тем, что организовать продувку вихревой камеры (или предкамеры) при двухтактном цикле сложно, двухтактные дизели строят только с неразделёнными камерами сгорания.
Варианты конструкции
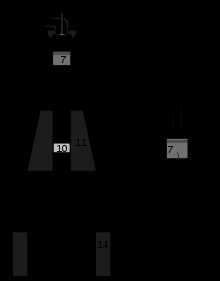
Для средних и тяжелых двухтактных дизельных двигателей характерно применение составных поршней, в которых используется стальная головка и дюралевая юбка. Основной целью данного усложнения конструкции является снижение общей массы поршня при сохранении максимально возможной жаростойкости донышка. Очень часто используются конструкции с масляным жидкостным охлаждением.
В отдельную группу выделяются четырехтактные двигатели, содержащие в конструкции крейцкопф. В крейцкопфных двигателях шатун присоединяется к крейцкопфу — ползуну, соединенному с поршнем штоком (скалкой). Крейцкопф работает по своей направляющей — крейцу, без воздействия повышенных температур, полностью ликвидируя воздействие боковых сил на поршень. Данная конструкция характерна для крупных длинноходных судовых двигателей, часто — двойного действия, ход поршня в них может достигать 3 метров; тронковые поршни таких размеров были бы перетяжеленными, тронки с такой площадью трения существенно снизили бы механический КПД дизеля.
Реверсивные двигатели
Большинство ДВС рассчитаны на вращение только в одну сторону; если требуется получить на выходе вращение в разные стороны, то используют передачу заднего хода в коробке перемены передач или отдельный реверс-редуктор. Электрическая передача также позволяет менять направление вращения на выходе.
Однако на судах с жёстким соединением двигателя с гребным винтом фиксированного шага приходится применять реверсивные двигатели, чтобы иметь возможность двигаться задним ходом. Для этого нужно изменять фазы открытия клапанов и впрыска топлива. Обычно распределительные валы снабжаются двойным количеством кулачков; при остановленном двигателе специальное устройство приподнимает толкатели клапанов, что даёт возможность передвинуть распредвалы в новое положение. Встречаются также конструкции с реверсивным приводом распределительного вала — здесь при изменении направления вращения коленчатого вала сохраняется направление вращения распределительного вала. Двухтактные двигатели с контурной продувкой, когда газораспределение осуществляется поршнем, не нуждаются в специальных реверсивных устройствах (однако в них всё же требуется корректировка момента впрыска топлива).
Реверсивные двигатели также применялись на ранних тепловозах с жёстким соединением вала двигателя с колёсами.
Преимущества и недостатки
Проверить информацию. Необходимо проверить точность фактов и достоверность сведений, изложенных в этой статье. |
Возможно, эта статья содержит оригинальное исследование. Добавьте ссылки на источники, в противном случае она может быть выставлена на удаление. |
Современные дизельные двигатели обычно имеют коэффициент полезного действия до 40-45 %, некоторые малооборотные крупные дизели — свыше 50 % (например, MAN S80ME-C7 тратит только 155 гр на кВт*ч, достигая эффективности 54,4 %).[6] Дизельный двигатель из-за особенностей рабочего процесса не предъявляет жестких требований к испаряемости топлива, что позволяет использовать в нём низкосортные тяжелые масла.
Дизельный двигатель не может развивать высокие обороты — топливо не успевает догореть в цилиндрах, для возгорания требуется время инициации. Высокая механическая напряженость дизеля вынуждает использовать более массивные и более дорогие детали, что утяжеляет двигатель. Это снижает удельную мощность двигателя, что послужило причиной малого распространения дизелей в авиации (только некоторые бомбардировщики Junkers, а также советский тяжёлый бомбардировщик Пе-8 и Ер-2, оснащавшиеся авиационными дизелями АЧ-30 и АЧ-40 конструкции А. Д. Чаромского и Т. М. Мелькумова). На максимальных эксплуатационных режимах топливо в дизеле не догорает, приводя к выбросу облаков сажи.
Сгорание впрыскиваемого в цилиндр дизеля топлива происходит по мере впрыска. Потому дизель выдаёт высокий вращающий момент при низких оборотах, что делает автомобиль с дизельным двигателем более «отзывчивым» в движении, чем такой же автомобиль с бензиновым двигателем. По этой причине и ввиду более высокой экономичности в настоящее время большинство грузовых автомобилей оборудуются дизельными двигателями[источник не указан 196 дней]. Например, в России в 2007 году почти все грузовики и автобусы были оснащены дизельными двигателями (окончательный переход этого сегмента автотранспорта с бензиновых двигателей на дизели планировалось завершить к 2009 году)[7]. Это является преимуществом также и в двигателях морских судов, так как высокий крутящий момент при низких оборотах делает более лёгким эффективное использование мощности двигателя, а более высокий теоретический КПД (см. Цикл Карно) даёт более высокую топливную эффективность.
По сравнению с бензиновыми двигателями, в выхлопных газах дизельного двигателя, как правило, меньше окиси углерода (СО), но теперь, в связи с применением каталитических конвертеров на бензиновых двигателях, это преимущество не так заметно. Основные токсичные газы, которые присутствуют в выхлопе в заметных количествах — это углеводороды (НС или СН) , оксиды (окислы) азота (NOх) и сажа (или её производные) в форме чёрного дыма. Больше всего загрязняют атмосферу в России дизели грузовиков и автобусов, которые часто являются старыми и неотрегулированными.
Другим важным аспектом, касающимся безопасности, является то, что дизельное топливо нелетучее (то есть легко не испаряется) и, таким образом, вероятность возгорания у дизельных двигателей намного меньше, тем более, что в них не используется система зажигания. Вместе с высокой топливной экономичностью это стало причиной широкого применения дизелей на танках, поскольку в повседневной небоевой эксплуатации уменьшался риск возникновения пожара в моторном отделении из-за утечек топлива. Меньшая пожароопасность дизельного двигателя в боевых условиях является мифом, поскольку при пробитии брони снаряд или его осколки имеют температуру, сильно превышающую температуру вспышки паров дизельного топлива и так же способны достаточно легко поджечь вытекшее горючее. Детонация смеси паров дизельного топлива с воздухом в пробитом топливном баке по своим последствиям сравнима со взрывом боекомплекта[источник не указан 400 дней], в частности, у танков Т-34 она приводила к разрыву сварных швов и выбиванию верхней лобовой детали бронекорпуса[источник не указан 400 дней]. С другой стороны, дизельный двигатель в танкостроении уступает карбюраторному в плане удельной мощности, а потому в ряде случаев (высокая мощность при малом объёме моторного отделения) более выигрышным может быть использование именно карбюраторного силового агрегата (хотя это характерно для слишком уж лёгких боевых единиц).
Конечно, существуют и недостатки, среди которых — характерный стук дизельного двигателя при его работе. Однако, они замечаются в основном владельцами автомобилей с дизельными двигателями, а для стороннего человека практически незаметны.
Явными недостатками дизельных двигателей являются необходимость использования стартёра большой мощности, помутнение и застывание (запарафинивание) летнего дизельного топлива при низких температурах, сложность и более высокая цена в ремонте топливной аппаратуры, так как насосы высокого давления являются прецизиоными устройствами. Также дизель-моторы крайне чувствительны к загрязнению топлива механическими частицами и водой. Ремонт дизель-моторов, как правило, значительно дороже ремонта бензиновых моторов аналогичного класса. Литровая мощность дизельных моторов также, как правило, уступает аналогичным показателям бензиновых моторов, хотя дизель-моторы обладают более ровным и высоким крутящим моментом в своём рабочем объёме. Экологические показатели дизельных двигателей значительно уступали до последнего времени двигателям бензиновым. На классических дизелях с механически управляемым впрыском возможна установка только окислительных нейтрализаторов отработавших газов, работающих при температуре отработавших газов свыше 300 °C, которые окисляют только CO и CH до безвредных для человека углекислого газа (CO2) и воды. Также раньше данные нейтрализаторы выходили из строя вследствие отравления их соединениями серы (количество соединений серы в отработавших газах напрямую зависит от количества серы в дизельном топливе) и отложением на поверхности катализатора частиц сажи. Ситуация начала меняться лишь в последние годы в связи с внедрением дизелей так называемой системы Common rail. В данном типе дизелей впрыск топлива осуществляется электронно-управляемыми форсунками. Подачу управляющего электрического импульса осуществляет электронный блок управления, получающий сигналы от набора датчиков. Датчики же отслеживают различные параметры двигателя, влияющие на длительность и момент подачи топливного импульса. Так что, по сложности современный — и экологически такой же чистый, как и бензиновый — дизель-мотор ничем не уступает своему бензиновому собрату, а по ряду параметров (сложности) и значительно его превосходит. Так, например, если давление топлива в форсунках обычного дизеля с механическим впрыском составляет от 100 до 400 бар (приблизительно эквивалентно «атмосфер»), то в новейших системах «Common-rail» оно находится в диапазоне от 1000 до 2500 бар, что влечёт за собой немалые проблемы. Также каталитическая система современных транспортных дизелей значительно сложнее бензиновых моторов, так как катализатор должен «уметь» работать в условиях нестабильного состава выхлопных газов, а в части случаев требуется введение так называемого «сажевого фильтра» (DPF — фильтр твёрдых частиц). «Сажевый фильтр» представляет собой подобную обычному каталитическому нейтрализатору структуру, устанавливаемую между выхлопным коллектором дизеля и катализатором в потоке выхлопных газов. В сажевом фильтре развивается высокая температура, при которой частички сажи способны окислиться остаточным кислородом, содержащимся в выхлопных газах. Однако часть сажи не всегда окисляется, и остается в «сажевом фильтре», поэтому программа блока управления периодически переводит двигатель в режим «очистки сажевого фильтра» путём так называемой «постинжекции», то есть впрыска дополнительного количества топлива в цилиндры в конце фазы сгорания с целью поднять температуру газов, и, соответственно, очистить фильтр путём сжигания накопившейся сажи. Стандартом де-факто в конструкциях транспортных дизель-моторов стало наличие турбонагнетателя, а в последние годы — и «интеркулера» — устройства, охлаждающего воздух после сжатия турбонагнетателем — чтобы после охлаждения получить большую массу воздуха (кислорода) в камере сгорания при прежней пропускной способности коллекторов, а Нагнетатель позволил поднять удельные мощностные характеристики массовых дизель-моторов, так как позволяет пропустить за рабочий цикл большее количество воздуха через цилиндры.
В своей основе конструкция дизельного двигателя подобна конструкции бензинового двигателя. Однако, аналогичные детали у дизеля тяжелее и более устойчивы к высоким давлениям сжатия, имеющим место у дизеля, в частности, хон на поверхности зеркала цилиндра более грубый, но твёрдость стенок блока цилиндров выше. Головки поршней, однако, специально разработаны под особенности сгорания в дизельных двигателях и почти всегда рассчитаны на повышенную степень сжатия. Кроме того, головки поршней в дизельном двигателе находятся выше (для автомобильного дизеля) верхней плоскости блока цилиндров. В некоторых случаях — в устаревших дизелях — головки поршней содержат в себе камеру сгорания («прямой впрыск»).
Сферы применения
Дизельные двигатели применяются для привода стационарных силовых установок, на рельсовых (тепловозы, дизелевозы, дизель-поезда, автодрезины) и безрельсовых (автомобили, автобусы, грузовики) транспортных средствах, самоходных машинах и механизмах (тракторы, асфальтовые катки, скреперы и т. д.), а также в судостроении в качестве главных и вспомогательных двигателей.
Мифы о дизельных двигателях
Цех судовых дизелей завода «Даймлер-Бенц» в Штутгарте Дизельный двигатель с турбонаддувом- Дизельный двигатель слишком медленный.
Современные дизельные двигатели с системой турбонаддува гораздо эффективнее своих предшественников, а иногда и превосходят своих бензиновых атмосферных (без турбонаддува) собратьев с таким же объёмом. Об этом говорит дизельный прототип Audi R10, выигравший 24-х часовую гонку в Ле-Мане, и новые двигатели BMW, которые не уступают по мощности атмосферным (без турбонаддува) бензиновым и при этом обладают огромным крутящим моментом.
- Дизельный двигатель слишком громко работает.
Громкая работа двигателя свидетельствует о неправильной эксплуатации и возможных неисправностях. На самом деле некоторые старые дизели с непосредственным впрыском действительно отличаются весьма жёсткой работой. С появлением аккумуляторных топливных систем высокого давления («Common-rail») у дизельных двигателей удалось значительно снизить шум, прежде всего за счёт разделения одного импульса впрыска на несколько (типично — от 2-х до 5-ти импульсов).
- Дизельный двигатель гораздо экономичнее.
Основная экономичность обусловлена более высоким КПД дизельного двигателя. В среднем современный дизель расходует топлива до 30 % меньше[8]. Срок службы дизельного двигателя больше бензинового и может достигать 400—600 тысяч километров. Запчасти для дизельных двигателей несколько дороже, стоимость ремонта так же выше, особенно топливной аппаратуры. По вышеперечисленным причинам, затраты на эксплуатацию дизельного двигателя несколько меньше, чем у бензинового. Экономия по сравнению с бензиновыми моторами возрастает пропорционально мощности, чем определяется популярность использования дизельных двигателей в коммерческом транспорте и большегрузной технике.
- Дизельный двигатель нельзя переоборудовать под использование в качестве топлива более дешёвого газа.
С первых моментов построения дизелей строилось и строится огромное количество их, рассчитанных для работы на газе разного состава. Способов перевода дизелей на газ, в основном, два. Первый способ заключается в том, что в цилиндры подаётся обеднённая газо-воздушная смесь, сжимается и поджигается небольшой запальной струёй дизельного топлива. Двигатель, работающий таким способом, называется газодизельным. Второй способ заключается в конвертации дизеля со снижением степени сжатия, установкой системы зажигания и, фактически, с построением вместо дизеля газового двигателя на его основе.
Рекордсмены
Самый большой/мощный дизельный двигатель
Судовой, 14 цилиндровый — Wärtsilä-Sulzer RTA96-C, созданный финской компанией Wärtsilä в 2002 году, для установки на крупные морские контейнеровозы и танкеры, является самым большим дизелем в мире[9].
Конфигурация — 14 цилиндров в ряд
Рабочий объём — 25 480 литров
Диаметр цилиндра — 960 мм
Ход поршня — 2500 мм
Среднее эффективное давление — 1,96 МПа (19,2 кгс/см²)
Мощность — 108 920 л.с. при 102 об/мин. (отдача с литра 4,3 л.с.)
Крутящий момент — 7 571 221 Н·м
Расход топлива — 13 724 литров в час
Сухая масса — 2300 тонн
Габариты — длина 27 метров, высота 13 метров
Самый большой дизельный двигатель для грузового автомобиля[источник не указан 1275 дней]
MTU 20V400 предназначен, для установки на карьерный самосвал БелАЗ-7561.
Мощность — 3807 л.с. при 1800 об/мин. (Удельный расход топлива при номинальной мощности 198 г/кВт*ч)
Крутящий момент — 15728 Н·м
Самый большой/мощный серийный дизельный двигатель для серийного легкового автомобиля[источник не указан 1275 дней]
Audi 6.0 V12 TDI с 2008 года устанавливается на автомобиль Audi Q7.
Конфигурация — 12 цилиндров V-образно, угол развала 60 градусов.
Рабочий объём — 5934 см³
Диаметр цилиндра — 83 мм
Ход поршня — 91,4 мм
Степень сжатия — 16
Мощность — 500 л.с. при 3750 об/мин. (отдача с литра — 84,3 л.с.)
Крутящий момент — 1000 Нм в диапазоне 1750-3250 об/мин.
См. также
Примечания
Ссылки
dic.academic.ru
Дизельный двигатель
Дизельный двигатель — двигатель внутреннего сгорания, в котором:
— сжатию подвергается воздух, температура которого повышается до 600-700°С.
— топливо воспламеняется при соприкосновении с раскаленным воздухом.
Дизели ставят только на грузовики. Многие современные легковые автомобили имеют дизельные двигатели, причем, например, в Европе люди даже предпочитают дизели бензиновым двигателям.
Дизельный двигатель менее мощный, чем бензиновый. При современном уровне технологий чаще оказывается наоборот. Современный дизельный двигатель может превосходить бензиновый по мощности, не говоря уже о крутящем моменте, который обеспечивает эластичность и удобство управления разгоном.
Дизельные двигатели эффективны только при большом объеме. Для дизельного двигателя, точно так же, как и для бензинового, не существует ограничений по объему. Сейчас выпускаются автомобили с объемом дизельного двигателя 1,1; 1,3 литра, и даже мотоциклы с дизельным двигателем объемом 0,6 литра.
Даже если дизель мощнее, за счет своего веса он проигрывает по характеристикам бензиновому. Сейчас для дизельных двигателей применяются те же материалы, что и для бензиновых, поэтому они ненамного тяжелее.
Дизельный двигатель хуже заводится зимой. Если не экономить деньги на свечах накаливания и зимнем дизтопливе, то он будет запускаться в любой мороз с такой же легкостью.
Дизельный двигатель с турбиной расходует больше топлива. Как это ни парадоксально, но турбина в дизельном двигателе, в отличие от бензинового, снижает расход топлива. Это объясняется резко возрастающим крутящим моментом, который позволяет управлять машиной более спокойно.
Дизельный двигатель необходимо долго прогревать. Если прогревать дизельный двигатель регулярно, то на клапанах остаются остатки нагара и смол, которые при накоплении могут привести к неплотному прилеганию клапана к седлу и даже его стопорению. Но, тем не менее, турбодизели нуждаются в недолгом прогреве на холостом ходу для избежания поломок турбины.
Дизельный двигатель намного сложнее в обслуживании и ремонте. Дизельный двигатель по своей конструкции намного проще бензинового, так как в нем воспламенение происходит не от искры, производимой свечой зажигания, а от сжатия смеси в цилиндре. А так как простые конструкции всегда надежнее, то поломки этого типа двигателя происходят намного реже. В обслуживании и ремонте дизельные двигатели также намного проще по понятной причине.
Дизельный двигатель чрезвычайно шумный. Дизельный двигатель, оснащенный хорошим глушителем и современной системой впуска работает немного громче бензинового, но в большинстве случаев звук работы современных бензиновых и дизельных двигателей практически невозможно различить.
Любой дизель требует хорошего топлива. Во-первых, многие дизельные двигатели, особенно атмосферные, абсолютно не требовательны к топливу. А во-вторых даже на самый прихотливый дизель можно поставить фильтр-водоотделитель и фильтр твердых частиц, которые позволят заправлять автомобиль топливом любого качества.
Бензиновые двигатели все же надежнее – они лучше проверены. Это не так. Дизельные двигатели в среднем имеют ресурс на 40-50% больший, чем у бензинового двигателя.
В дизеле бесполезно применять сложную электронику. Дизельный двигатель допускает применение в нем любых сложных систем. Так, в современном дизельном двигателе применяются такие системы, как электронноуправляемые форсунки, общая аккумуляторно-возвратная топливная рампа Common Rail и другие.
Форсировать дизельный двигатель невозможно. Да, дизели хуже поддаются тюнингу, чем бензиновые двигатели, но поднять мощность в 1,5 раза без особого прироста расхода топлива все же возможно.
Автоматическая коробка передач и дизель несовместимы. Дизельный двигатель стыкуется с автоматической коробкой передач даже лучше бензинового за счет более высокого крутящего момента, который лучше приводит в действие гидротрансформатор.
Выхлоп дизельного двигателя сильнее загрязняет окружающую среду. При применении каталитических нейтрализаторов, рециркуляции выхлопных газов и сажевого фильтра выхлоп дизельного двигателя может соответствовать самым жестким экологическим нормам.
Дизельная машина дешевле бензиновой. При равном уровне оснащения машина с дизельным двигателем будет стоить дороже бензиновой за счет применения более дорогих электронных и очистных систем, но ее эксплуатация обойдется дешевле.
Вибронагруженность дизеля слишком высока. При четном количестве цилиндров в одном ряду вибронагруженность дизельного двигателя вполне приемлема, но если наоборот – то это утверждение становится правдивым.
В дизельный двигатель заливается такое же масло, как и в бензиновый. Для дизелей лучше использовать специальное масло, причем стоит внимательно изучить, для каких именно типов дизелей оно предназначено.
Популярные мифы
Популярные факты
Популярные советы
Популярные сленг
www.molomo.ru
Дизельные двигатели
Французский ученый С. Карно в 1824 году создал основы термодинамики. В этой работе он, в числе многого другого, утверждал, что заставить тепловую машину работать наиболее экономично можно, доводя рабочее тело до температуры вспышки топлива сжатием. Фактически он сформулировал принцип, на котором работают дизельные двигатели. Оставалось только взять и сделать такой двигатель. Но этого пришлось ждать еще несколько десятков лет.
В 1892 году немецкий инженер Рудольф Дизель получает патент на первый двигатель (показан на рисунке), работающий на сжатии воздуха до температуры вспышки. В 1987 году первый «дизель-мотор» (так немцы называют двигатель с воспламенением от сжатия) заработал и доказал свою эффективность.
По сравнению с «отто-мотором» (бензиновый двигатель со свечами зажигания) новый двигатель был более тяжелым и поначалу не внушал большого энтузиазма. Но только поначалу. Устройство дизельного двигателя первых образцов включало воздушный компрессор для впрыскивания топлива.
Сам Дизель вначале предполагал применить совсем уж экзотический вариант: угольная пыль. Смесь угольной пыли и воздуха, конечно, способна работать в двигателе, но за сколько часов абразивные частицы съедят кольца, поршни, седла и тарелки клапанов, об этом как-то не подумали. Да и саму угольную пыль получить не так просто.
Из-за тяжелого компрессора двигатель оказывалось невозможно применить на наземном транспорте. Но в работе он расходовал так мало горючего и работа его была настолько устойчивой, что отказаться от него было уже невозможно. Расчеты показывали, что от двигателя можно ожидать значительно большую мощность, если решить проблему с подачей топлива.
У инженеров возникла идея заменить компрессор плунжерным насосом. Качать топливо в жидком виде было чрезвычайно выгодно, на это уходит гораздо меньше энергии, а насос можно сделать совсем небольшим. Однако, изготовить плунжерную пару было не так просто. Дело в особой точности изготовления — расстояние между деталями составляет 2-3 микрона.
Все же дизелям нашлась работа. Впервые они были установлены на немецких подводных лодках еще при кайзере Вильгельме. (Возможно, с этим как раз связано темная история исчезновения самого изобретателя, утонувшего в Ла-Манше по дороге в Англию.)
В 1920 году Роберт Бош наконец, получает качественный плунжерный насос. В цилиндры двигателя научились подавать больше топлива. Теперь обороты дизельного двигателя и его удельная мощность, становятся достаточными для установки на автотранспорте. Вместе с насосом Бош разрабатывает и очень удачную форсунку для топлива.
Сгорание топлива в дизельном двигателе
Проще всего понять, как работает дизельный двигатель, если посмотреть на сгорание топлива в нем. В дизелях используется тяжелое топливо. Это означает, что двигатель внутреннего сгорания такого типа может работать на керосине (известном как солярка), мазуте, сырой нефти, и даже на некоторых растительных маслах.
Все эти виды топлива более калорийны, чем бензин. Так что, рабочая температура дизельного двигателя заметно выше, чем у бензинового. Но тяжелые виды топлива горят хуже, чем бензин, медленнее и трудно поджигаются. Для их воспламенения требуется большая степень сжатия, воздушно-топливная смесь должна нагреваться до 700-800°С.
Вязкость любого из дизельных видов топлива, даже в подогретом состоянии, выше бензиновой, а распылять его необходимо до мельчайшего состояния, особенно в быстроходных дизелях. Еще экспериментальный двигатель Дизеля работал при впрыске топлива под давлением не менее 50 бар (атм), а практический двигатель требует 100-200 бар.
Однако, у тяжелых калорийных топлив есть свое преимущество перед бензином. Давление в цилиндре дизеля практически постоянно на всем такте расширения, поэтому крутящий момент у них весьма значителен и стабилен. Благодаря постоянному давлению, угол опережения зажигания также остается постоянным и регулировки не требует. Ресурс дизельного двигателя больше, чем у бензинового. Есть области, где дизель практически незаменим, например в сельскохозяйственном тракторе.
Разновидности дизельных двигателей
Принцип действия дизельного двигателя для всех из них одинаков: сначала производится сжатие свежего заряда рабочего тела (воздуха), затем впрыскивается топливо. От высокой температуры смесь воспламеняется и сгорает, поднимая давление. Под его действием поршень двигается обратно и в нижней точке выпускной клапан цилиндра открывается, выпуская отработанный газ. В основном, это углекислый газ, дизельные двигатели экологически чище бензиновых.
Камеры сгорания дизелей могут выполняться непосредственно в днище поршня — там делается выемка особой формы — или в ряде случаев используют предкамеры (или форкамеры, как это говорят на родине двигателя). Первый вариант — самый экономичный, второй считался оптимальным в прежние годы. Сейчас, когда экономичность, во многих случаях, считается решающей, от предкамерных вариантов снова отказываются.
Рабочий процесс в дизеле может протекать, как и в бензиновом двигателе, в два или четыре такта. Подавляющее большинство дизелей — четырехтактные. Двухтактные проще реверсировать, поэтому они распространены на морских судах, где применяется жесткая связь с гребным валом. Камеры сгорания в двухтактных дизелях не разделяются из-за очевидных проблем с продувкой форкамеры.
Конструкция дизельного двигателя зависит от его мощности и назначения. Наиболее мощные двигатели, применяемые на судах и некоторых электростанциях, имеют крейцкопф — устройство для снижения боковых сил на поршень. Все мощные дизели имеют сложно устроенное дно, потому, что подвергаются высокой температуре.
Часть, обращенная в цилиндр, делается стальной, а остальная часть поршня (юбка) — алюминиевой. Кроме того, в поршне сделаны канавки для системы масляного охлаждения.
Типы дизельных двигателей различаются и по расположению цилиндров. Бывает рядовое, V-образное и даже такое, при котором цилиндры располагаются с разворотом на 180 градусов. Это зависит от тех условий, которые имеются на месте установки двигателя. Например, на современном грузовике или автобусе, скорее всего, будет применен двухрядный дизель, установленный под полом кабины водителя. Как устроен дизельный двигатель, будет зависеть и от наличия наддува.
Турбонаддув дизелей
Мощность дизельного двигателя, без увеличения расхода топлива, можно повысить при помощи турбокомпрессора. Тогда можно использовать еще неплохой кусочек диаграммы цикла Карно. Эксплуатация дизельного двигателя с турбокомпрессором имеет то преимущество, что используя энергию выхлопных газов можно раскрутить турбину, и на том же валу установить другую турбину — компрессор.
Этот компрессор будет нагнетать воздух, поступающий через впускной коллектор, увеличится заряд воздуха в цилиндрах, и, таким образом, мощность двигателя заметно возрастет. (Работу таких двигателей легко узнать по характерному свисту в момент раскручивания турбины.)
Плюсы и минусы дизелей
Преимущества дизельного двигателя — это высокий и постоянный крутящий момент в сочетании с высокой экологичностью выхлопных газов (это относится, правда, только к современным двигателям). Также вне конкуренции их высокий КПД, самый высокий среди ДВС. Известны дизели (MAN) дающие свыше 50%, (что считалось «теоретическим» максимумом). Там использован максимум всех современных достижений. Экономичность достигает до 40%, если провести сравнение с бензиновыми.
Проблемы дизельных двигателей, а без них техники не бывает, заключаются в тяжелом пуске, из-за высокой степени сжатия (до 25 в современных двигателях), на автомобилях приходится ставить мощный стартер и аккумулятор. Большая точность изготовления деталей насосов высокого давления и форсунок затрудняет обслуживание.
Дизели крайне чувствительны к механическим загрязнениям топлива, для очистки которого приходится применять даже центрифугу в составе топливной аппаратуры. При равном объеме в литрах, дизельный двигатель уступает бензиновому по мощности, при равной мощности дизель тяжелее. Дизельный двигатель требует более качественных сплавов для своего изготовления и заметно дороже бензинового.
И все же, сравнивая преимущества и недостатки дизельного двигателя, можно сделать выбор в пользу дизеля. Особенно этому способствует технический прогресс в области электроники и блоков управления двигателями. Система «общая магистраль» (common rail) и электромагнитные форсунки позволяет сильно упростить ТВНД, а блок управления доводит экономию топлива до максимума, поскольку работает на любых переходных режимах и успевает все отследить.
avtodvigateli.com
Дизельный двигатель
16.05.2010
Описание конструкции
Дизельный двигатель — это двигатель с возвратно-поступательным движением поршней, имеющий такую же базовую конструкцию и рабочий цикл, что и бензиновый двигатель. Главное отличие между дизельным двигателем и бензиновым двигателем заключается в используемом топливе и способе воспламенения топлива для обеспечения его сгорания.
Работа
В дизельных двигателях для зажигания воздушно-топливной смеси в камере сгорания используется теплота сжатия. Такое зажигание выполняется с использованием высокого давления сжатия и дизельного топлива, впрыскиваемого в камеру сгорания под очень высоким давлением. Комбинация дизельного топлива и высокого давления сжатия обеспечивает самовоспламенение, позволяющее начать цикл сгорания.
Блок цилиндров
Блоки цилиндров дизельного и бензинового двигателя аналогичны друг другу, но в их конструкции имеются некоторые различия. В большинстве дизельных двигателей используются гильзы цилиндров, а не цилиндры, выполненные как часть блока. При использовании гильз цилиндров может быть выполнен ремонт, позволяющий эксплуатировать двигатель в течение длительного времени. На тех дизельных двигателях, в которых не используют гильзы цилиндров, стенки цилиндра толще, чем стенки на бензиновом двигателе с аналогичным рабочим объемом. Для увеличения опорной поверхности коленчатого вала дизельные двигатели имеют более тяжелые и более толстые коренные перемычки.
Мокрые гильзы цилиндров
Мокрые гильзы цилиндров, используемые в дизельных двигателях, аналогичны используемым в бензиновых двигателях. Физические размеры гильз могут отличаться, чтобы соответствовать рабочим условиям дизельного двигателя.
Коленчатый вал
Коленчатый вал, используемый в дизельных двигателях имеет конструкцию, аналогичную конструкции коленчатого вала на бензиновых двигателях, но с двумя отличиями:
• Коленчатые валы дизельных двигателей обычно кованые, а не литые. Ковка делает коленчатый вал более прочным.
• Шейки коленчатого вала дизельного двигателя обычно больше по размеру, чем шейки коленчатого вала бензинового двигателя.
Увеличение шеек позволяют коленчатому валу выдерживать большие нагрузки.
Шатуны
Шатуны, используемые в дизельных двигателях, обычно изготавливаются из кованной стали. Шатуны дизельных двигателей отличаются от шатунов бензиновых двигателей тем, что крышки смещены и имеют мелкие зубья на поверхности сопряжения с шатуном. Конструкция со смещением и мелкими зубьями помогает удерживать крышку на месте и уменьшает нагрузку на болты шатуна.
Поршни и поршневые кольца
Поршни, используемые в дизельных двигателях, предназначенных для работы в легких условиях, выглядят аналогично поршням, используемым в бензиновых двигателях. Дизельные поршни тяжелее чем поршни бензиновыхдвигателей, потому что дизельные поршни обычно изготавливаются из кованной стали, а не из алюминия, и больше внутренняя толщина материала.
Компрессионные кольца, используемые в дизельных двигателях, обычно изготавливаются из чугуна и часто покрываются хромом и молибденом, что позволяет уменьшить трение.
Головка цилиндров
Внешне головка цилиндров дизельного двигателя во многом выглядит подобно головке цилиндров бензинового двигателя. Но имеется много внутренних конструктивных различий, которые делают дизельные двигатели иными, оригинальными.
На дизельном двигателе сама головка цилиндров должна быть намного более прочной и более тяжелой, чтобы выдержать большие тепловые нагрузки и воздействие давления. Конструкция камеры сгорания и воздушные каналы на дизельных двигателях могут быть более сложными, чем на бензиновом двигателе.
В дизельных двигателях используются несколько конструкций камер сгорания, но две конструкции наиболее распространены: неразделенная камера сгорания и вихревая камера.
Конструкция с неразделенной камерой сгорания
Наиболее распространенный тип камеры сгорания для дизельного двигателя — это неразделенная камера, также известная как камера сгорания с прямым впрыскиванием. В неразделенной конструкции обеспечение турбулентности (завихрения) впускаемого воздуха происходит за счет формы канала впуска воздуха. Топливо впрыскивается прямо в камеру сгорания.
Конструкция с вихревой камерой
В конструкции с вихревой камерой используются по две камеры сгорания для каждого цилиндра. Главная камера соединяется узким каналом с меньшей по размеру вихревой камерой. В вихревой камере находится топливная форсунка. Вихревая камера предназначается для обеспечения начала процесса сгорания. Впускаемый воздух вводится в вихревую камеру через узкий канал. Затем в вихревую камеру впрыскивается топливо, и образуемая смесь загорается. После этого горящая смесь входит в главную камеру сгорания, где и заканчивает свое горение, заставляя поршень перемещаться вниз.
Клапаны и седла клапанов
Клапаны дизельного двигателя изготавливаются из специальных сплавов, которые способны хорошо работать при высоком теплообразовании и давлении, характерным для дизельного двигателя. Некоторые клапаны частично заполняются натрием, который помогает отводить тепло. Большой процент от тепла передается от головки клапана седлу клапана. Для обеспечения соответствующей теплопередачи особое внимание должно быть уделено ширине седла клапана.
Широкое седло клапана имеет преимущество, заключающееся в способности передавать большее количество тепла. Однако, широкое седло клапана имеет и большую возможность накопления отложений нагара, которые могут стать причиной протечек в клапане. Узкое седло клапана обеспечивает лучшее уплотнение, чем широкое седло клапана, но не передает такое же количество тепла. В дизельном двигателе необходим компромисс между широкими и узкими седлами клапанов.
В дизельных двигателях часто используются вставные седла клапанов. Вставки имеют преимущество, заключающееся в возможности их замены. Вставные седла клапанов изготавливаются из специальных металлических сплавов, которые выдерживают воздействие тепла и давления дизельного двигателя.
Система подачи топлива
Обычная конструкция
В обычной системе подачи дизельного топлива топливо вытягивается из топливного бака, отфильтровывается и подается к насосу высокого давления. Топливо под высоким давлением доводится до требуемого давления и подается к топливному коллектору, который питает топливные форсунки. Система управления впрыскиванием в соответствующие моменты времени активизирует форсунки, которые на ходе сжатия поршня впрыскивают топливо для его последующего сгорания.
Конструкция с общим топливным коллектором («Common rail»)
В дизельных двигателях с общим топливным коллектором используются независимые системы создания давления топлива и впрыскивания топлива. Топливный насос высокого давления вытягивает топливо от бака и подает его через регулятор давления к общему топливному коллектору. Насос высокого давления состоит из перекачивающего насоса низкого давления и камеры высокого давления. Впрыскивание топлива управляется модулем управления силовым агрегатом (РСМ) и модулем управления форсунками (IDM), который регулирует продолжительность открытого состояния форсунок в зависимости от рабочих условий двигателя.
В конструкции с общим топливным коллектором уровень токсичности отработавших газов значительно уменьшен и минимизирован шум при работе. Все это следствие большего управления процессом сгорания. Регулировка давления топлива и фазы работы форсунок управляются ЮМ и РСМ. Также изменена конструкция форсунки, которая теперь позволяет выполнять предварительное(пред-впрыскивание)и заключительное (пост-впрыскивание) впрыскивание топлива на различных стадиях хода сжатия и рабочего хода.
Улучшенное управление подачей топлива позволяет обеспечивать более чистое, более устойчивое сгорание и создавать требуемое давление в цилиндрах. Это оказывает влияние на уменьшение токсичности выхлопа и шума при работе.
Система смазки
Система смазки, используемая в дизельных двигателях, по принципу действия аналогична системам бензиновых двигателей. Большинство дизельных двигателей имеют маслоохладитель того или иного типа, помогающий отводить тепло от масла. Масло течет под давлением по каналам двигателя и возвращается к картеру двигателя.
Смазочное масло, используемое в дизельных двигателях, отличается от масла, используемого в бензиновых двигателях. Специальное масло необходимо по той причине, что при работе дизельного двигателя происходит большее загрязнение масла, чем в бензиновом двигателе. Высокое содержание углерода в дизельном топливе заставляет масло, используемое в дизельных двигателях, изменять свой цвет вскоре после начала его использования. Должно использоваться только такое моторное масло, которое предназначено специально для дизельных двигателей.
Система охлаждения
Система охлаждения дизельного двигателя обычно имеет больший заправочный объем, чем система охлаждения бензинового двигателя. Температура внутри дизельного двигателя должна тщательно контролироваться, потому что для самовоспламенения топлива используется тепло.
Если температура двигателя слишком низкая, возникают следующие проблемы:
• Повышенный износ
• Плохая экономия топлива
• Скапливание воды и отстоя в картере двигателя
• Потеря мощности
Если температура двигателя слишком высокая, возникают следующие проблемы:
• Повышенный износ
• Задиры
• Детонация
• Прогорание поршней и клапанов
• Проблемы со смазкой
• Заклинивание движущихся частей
• Потеря мощности
Система впрыскивания топлива
Дизельный двигатель работает по принципу самовоспламенения. Впускаемый воздух и топливо сжимаются в камере сгорания так сильно, что молекулы нагреваются и загораются без помощи внешней искры зажигания. Степень сжатия дизельного двигателя намного выше, чем степень сжатия бензинового двигателя. Значение степени сжатия в дизельных двигателях с прямым забором воздуха равняется приблизительно 22:1. Турбодизельные двигатели имеют степень сжатия в диапазоне 16.5-18.5:1. Создается давление сжатия, и температура воздуха возрастает приблизительно с 500 °С до 800 °С (от 932 °F до 1 472 °F).
Дизельные двигатели могут работать только с системой впрыскивания топлива. Смесеобразование происходит только в фазе впрыскивания и сгорания топлива.
В конце хода сжатия топливо впрыскивается в камеру сгорания, где оно смешивается с горячим воздухом и загорается. Качество этого процесса сгорания зависит от качества смесеобразования. Т.к. топливо впрыскивается столь поздно, оно не имеет много времени для смешивания с воздухом. В дизельном двигателе соотношение «воздух -топливо» постоянно поддерживается на уровне больше чем 17:1, таким образом обеспечивается сгорание всего топлива. За более подробной информацией обратитесь к публикации «Работа двигателя и его систем».
автозапчасти в москве
www.mskjapan.ru
История создания дизельного двигателя. Часть вторая. Первые дизельные двигатели
Категория: Полезная информация.
В первой части нашего повествования мы познакомились с Рудольфом Дизелем – немецким инженером, который придумал использовать смесь горючего и сильно сжатого воздуха для воспламенения топливной смеси в двигателе. И вот, вооружившись расчетами, патентом на разработку и контрактами владельцев заводов-пароходов, Дизель приступает к созданию «нового, эффективного теплового двигателя».
Эксперименты Дизеля
Три неудачных попытки предшествуют рождению прообраза современного мотора. Первая попытка – двигатель, работающий на угольной пыли – перегорает почти мгновенно. Дизель меняет пыль на керосин, придумывает систему охлаждения стенок мотора водой и наконец добивается сколь-нибудь устойчивых результатов. И четвертая попытка оказывается удачной – созданный в 1896 году двигатель развивает до 20 «лошадей» и выдает рекордных, по сравнению с паровыми агрегатами, 34% КПД.
Через год появляется созданный на заводе в Аугсбурге первый пригодный к использованию мотор системы Дизеля. Три метра в высоту и 20 «лошадей» — свои лавры Дизель получит чуть позже, когда агрегат прогремит на весь мир на выставке паровых машин в Мюнхене в 1898 году.
Другие имена
Параллельно с Дизелем разработку нового мотора вел русский инженер Густав Тринклер. Он представил свой двигатель с аналогичной системой высокого давления, «Тринклер-мотор», опоздав на год по сравнению с Дизелем и, несмотря на превосходство конкурента по части эффективности и технологического совершенства, успеха не получил. Дело в том, что крупнейшие корпорации и заводы к тому моменту за огромные деньги выкупили патенты на производство двигателей системы Дизеля – в их интересах было скрыть разработку Путиловского завода.
Что же касается технологической доработки мотора Дизеля, ею занялся в 1909 году инженер завода Benz&Cie Проспер Леранж. Он не только изобрел предкамеру двигателя, но и спроектировал форсунки с игольчатым клапаном и первые насос-форсунки.
Первый дизельный транспорт
Из-за огромных масс и размеров первых двигателей системы Дизеля, они могли использоваться только на морских судах и в тяжелой промышленности. Со временем дизельные двигатели стали устанавливать на подводные лодки. Лишь к началу 20-х годов ХХ века инженерам-конструкторам удалось уменьшить габариты дизельных двигателей до тех параметров, которые позволили использовать их на наземном транспорте.
Так, в 1923 году на выставке в Берлине был представлен первый грузовой автомобиль с мотором системы Дизеля. Им оказался выпущенный на заводе в Мангейме пятитонный грузовик Mercedes Benz 5K3. Двигатель, установленный в грузовике, имел предкамеру объемом почти 9 литров и развивал от 45 до 50 л.с. при 1000 об./мин.
Почти в то же самое время инженеры компании Daimler-Motoren-Gesellschaft сконструировали аналогичный по мощности атмосферный мотор, а компания MAN представила дизельный двигатель с системой непосредственного впрыска.
Что касается легковых автомобилей, то первой ласточкой по части дизельного двигателя стала модель 260D Mercedes Benz, представленная в 1936 году. Это первый в мире серийный легковой автомобиль с дизельным мотором.

Золотой век дизеля в США
Нужно сказать, что автовладельцы США ХХ века по достоинству оценили изобретение Дизеля лишь к концу 70-х годов, и связано это было с экономическими причинами. Нефтяной кризис и резкое подорожание топлива в этот период вынудило американцев массово скупать Peugeot, Mercedes Benz, Isuzu, Volkswagen, Audi, Volvo и Datsun – и все с дизельными моторами. Существенно выросли и продажи производителя собственных дизельных автомобилей в Америке, концерна General Motors.
Однако к середине 80-х с урегулированием цен на бензин, приоритеты американцев снова повернулись в сторону бензиновых автомобилей. Вскоре Дженерал Моторс прекратил выпуск собственных дизельных автомобилей.
Если вы в поиске качественных запчастей для своего дизельного двигателя, проверьте наш каталог.
Перейти в каталог
www.dieselkraft.by