описание работы, материалы и способы
Всем, у кого есть автомобиль, знакома проблема, когда появляется потребность выпрессовать или же запрессовать сайлентблоки. Не всегда хочется обращаться к специалистам, да и сделать это своими руками намного приятнее.
Благодаря этой статье вы узнаете, что такое сайлентблоки, зачем они нужны, и главное — как их запрессовать и выпрессовать в домашних условиях разными методами.
Что такое сайлентблок
Это слово имеет зарубежное происхождение. В переводе с английского языка silent — это тишина, а block — деталь. Сайлентблок, либо просто «сайлент», представляет собой резинометаллическую составную часть, обычными словами — это две втулки, которые соединены между собой слоем прочной резины. Это изобретение, кроме того, что гарантирует комфортное и беззвучное передвижение на автомобиле, имеет еще ряд плюсов, которые будут перечислены дальше.
Предназначение и функции
Сайлентблоки выполняют следующие функции:
- Оберегают составные части от выработки и разрушения посредством гашения колебаний.
- Они глушат колебания, которые поступают от ходовой части колес, таким образом, обеспечивают комфортную и мягкую езду.
- Предотвращают вибрации и биения, которые появляются в процессе движения машины между разными элементами ходовой части и моторного отсека.
И это только главные плюсы, на самом деле их гораздо больше.
Как понять, что пора проводить замену
Перед тем как вы вознамеритесь запрессовать данные детали, в первую очередь следует отлично их осмотреть, чтобы удостовериться в том, что они и вправду требуют замены. Проверьте, нет ли дыр и каких-либо деформаций, не вспучились ли резины на шарнирах и не возникли ли трещины. Проведите манипуляции с составными частями, определяя присутствие люфтов. Если же допустимая норма превышена, значит, замена деталей неминуема. Откладывать процедуру запрессовки не рекомендуется. С течением времени эта проблема только усугубится, она может привести к выходу из строя рычага подвески.
Главные показатели, которые указывают на поломку одной детали либо же нескольких:
- Управлять машиной стало намного труднее.
- Во время преодоления неровностей подвеска начинает громко стучать. Покрышки изнашиваются неравномерно, чего раньше не наблюдалось.
- Стало значительно сложнее регулировать развал-схождение.
Необходимые материалы
- Монтировка;
- Домкрат;
- Набор гаечных ключей;
- Новые шарниры.
В качестве смазки рекомендуется применять машинное масло либо же другие виды смазки.
Помимо прочего, вам будут необходимы специальные оправки, предназначенные для запрессовки сайлентблоков, в качестве альтернативы можно воспользоваться куском трубы с необходимым диаметром. Также нужно обзавестись прессом для запрессовки нового резинометаллического шарнира. Когда речь идет о домашних условиях, прессом могут послужить обыкновенные тиски. Вдобавок можно запастись набором кувалд, однако при таком подходе необходимо соблюдать высокую точность выполнения работы.
Выпрессовка в домашних условиях
Заменить данные детали не так трудно, как могло бы показаться на первый взгляд. К примеру, многие владельцы автомобилей в этом удостоверились, когда производили замену деталей, руководствуясь специальной техникой для самостоятельной замены. Именно по данной причине встречается много людей, которые приняли решение собственноручно и в домашних условиях сделать замену сайлентблоков.
Первый метод
В первую очередь, узнаем о том, как это должно быть в идеале.
Рычаг, в котором нужно сделать замену резинометаллического шарнира, устанавливают на специальную проставку под пресс. На эту проставку и будет выдавливаться старый сайлент. Затем сверху устанавливают еще одну проставку — она выдавливает старую втулку. Такой метод употребляют работники СТО, так как у них имеется нужный набор проставок и мощнейший пресс в 10−20 тонн.
Второй метод
Практически у всех владельцев машин мощного пресса, естественно, нет, но у множества в гараже есть домкрат либо хорошие тиски. Если воспользоваться мощными тисками, можно удачно выдавить старые втулки по знакомому нам уже принципу: проставка для исходной втулки и проставка для надавливания на втулку.
На первый взгляд, становится непонятно, как можно домкратом выдавить сайлент? Все очень просто: нужно сварить рамку в форме прямоугольника из швеллера либо уголка, чтобы по высоте она была чуть выше рычага и домкрата. Принцип работы следующий: поставьте домкрат в рамку, затем сверху штока установите проушину рычага, а также две проставки, про которые было сказано выше. Создаем нужное давление, после чего втулка выдавливается из своего посадочного места. Необходимо подчеркнуть, что чаще всего домкрат мощностью в 3−5 тонн не в силах совладать с такой работой, поэтому рекомендуется применять 10-тонные домкраты.
Третий метод
В случае если у вас нет ни пресса, ни домкрата, но при этом присутствует сильное желание заменить сайлентблоки без помощи других, можно воспользоваться третьим методом — использование простого пресс-съемника (болт с гайкой либо же шпилька).
Принцип работы состоит в том, чтобы образовать давление с помощью постепенного закручивания гайки на шпильке, этот метод можно назвать аналогом тисков. Данная шпилька с шайбой подходящего диаметра просовывается в проушину через сайлентблок, затем с другой стороны следует надеть проставку с шайбой и закручивать гайку. Вертясь по резьбе, гайка создает нужное давление и принуждает сайлент выдавливаться в специальную проставку.
Этот «способ» требует использования прочной, каленой шпильки и с такой же крепкой гайкой. Если же взять мягкую шпильку либо гайку, у вас, скорее всего, ничего не выйдет. К примеру, бывают случаи, когда из-за сильного давления шпилька кривится, вследствие чего срывается резьба на гайке. Однако существует и тысячи тех, кому удалось поменять сайлентблоки, используя именно этот метод. Ведь все зависит от качественности и прочности используемого материала.
Плюсом этого метода считается его бюджетность, а также удобство, если посмотреть со стороны «мобильности». Другими словами, вам не надо, к примеру, полностью снимать рычаг или же всю ступицу, достаточно будет просто иметь такой вот простой пресс-съемник.
Четвертый метод
Этот метод можно отнести к кардинальным решениям либо к крайним мерам. Его принцип заключается в том, чтобы всеми популярными методами и приспособлениями добыть сайлент из посадочного места. Для этого вам нужно выбить старую деталь при помощи мощной отвертки либо толстого клинообразного куска арматуры. Вам необходимо постараться забить отвертку либо что-то между сайлентблоком и втулкой, таким образом, деформируя внутри стенку втулки. Теперь, когда втулка сминается и подается внутрь, выбить ее совсем нетрудно. Прежде чем начать выбивать сайлентблок, нужно выдавить либо выжечь внутреннюю втулку детали и по возможности все остатки резины.
Пятый метод
Следующий способ извлечения сайлентблока невозможно назвать выпрессовкой, так как он, как и предыдущий, не предусматривает присутствия пресса: все, что нужно — это полотно по металлу, молоток и отвертка. Принцип простой, однако небезопасный. Устраняем внутреннюю втулку, потом берем полотно и принимаемся резать наружную втулку. Старайтесь максимально прорезать старый сайлент, при всем этом не испортив сам рычаг либо проушину. Лучше всего сделать два надреза, а затем при помощи плоской отвертки сайлентблок будет легко деформироваться и выбиваться.
В случае если ни один из перечисленных выше методов не помог, а вам по-прежнему нужно это сделать, остается только один выход — доверить данную работу специалистам. Чтобы достичь желаемого результата, берите деталь и отправляйтесь на СТО, где специалисты, используя выпрессовыватель сайлентблоков и другие специальные инструменты, качественно сделают всю необходимую работу «в мгновение ока».
Запрессовка сайлентблоков
Про то, как достать «сайленты», мы уже подробно рассказали, теперь появляется иная проблема — как запрессовать данную деталь? Эта процедура трудна тем, что требует определенных умений и способностей. Неправильно или же криво установленный сайлент или не будет ходить, или сломается раньше времени.
Первый метод
Как и в выпрессовывании, запрессовка в идеальном варианте должна выполняться с помощью тисков. Принцип несколько похож, но только с точностью наоборот. Прежде чем запрессовать деталь, нужно наждачной бумагой тщательно очистить посадочное гнездо от остатков и ржавчины предыдущего сайлента. Потом проушина щедро смазывается смазкой наподобие «Литол» либо же мыльным раствором. Устанавливается рычаг, сверху ставится деталь, после этого через особую оправку осуществляется давление пресса на проставку. Она и будет вдавливать деталь в посадочное место.
Второй метод
Когда у вас нет пресса, запрессовать деталь можно, используя при этом вышеупомянутый домкрат либо тиски. Принцип работы ничем не отличается от пресса. Устанавливается рычаг, втулка, а также проставка. После чего под действием силы тисков либо домкрата производится запрессовка детали в посадочное гнездо.
Третий метод
Пресс-съемник. В случае если сайлентблок маленький, «поставить его на свое место» можно с помощью такого же пресс-съемника, который употреблялся для выпрессовки детали из гнезда. Снова принцип одинаковый, лишь в качестве пресса употребляется толстая шайба и шпилька.
Четвертый метод
С использованием кувалды и грубой силы. Этот метод не самый лучший из всех существующих, так как он больше рассматривается чисто с теоретической стороны. Другими словами, он действительно позволяет запрессовать деталь, вот только очень сложно сказать, какими будут результаты и качество работы. Принцип достаточно простой: берем рычаг, на него ставим сайлент, после этого быстро и сильно бьем по нему.
После такого сильного воздействия он должен зайти в ухо рычага. Только главный недостаток метода в том, что спрогнозировать правильность движения данной детали не так просто, он может криво зайти в место посадки. Помимо прочего, может произойти «закусывание» резиновых составных частей и повреждение самого рычага либо же сайлентблока. Проще говоря, удар очень трудно держать под контролем, и часто после подобного рода «экспериментов» приходится обращаться к специалистам и заново все переделывать. Поэтому хорошенько подумайте о возможных последствиях до применения данного способа.
Пятый метод
Последний известный метод запрессовки сайлента — это использование веса авто. Принцип состоит в том, чтобы использовать вес своей машины в корыстных целях. Происходит все это так: под машину устанавливаете гидравлический либо винтообразный домкрат, снимаете колесо. Потом устанавливаете рычаг с сайлентом, который нужно запрессовать, под ступицу.
Дальше хорошенько все ровняем и начинаем медленно опускать домкрат. В таком случае рекомендуется, чтобы вам кто-нибудь помогал. Веса машины будет вполне достаточно, чтобы прочно вдавить деталь в место посадки. Недостаток этого метода в том, что он неудобен и в некоторой мере небезопасен, кроме того, не так просто держать под контролем правильность посадки детали в посадочное гнездо. Но, когда у вас нет иного варианта, метод вполне достоин внимания.
Каждый метод по-своему эффективен и интересен. Обдумайте для себя все плюсы и минусы каждого способа, чтобы наверняка определиться.
tokar.guru
Как заменить направляющие втулки клапанов
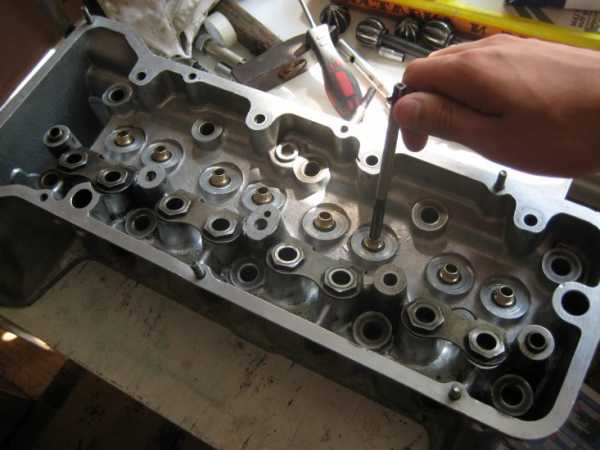
Ремонт головки блока цилиндров (ГБЦ) зачастую предполагает необходимость замены направляющих втулок клапанов ГРМ. Для замены необходимо выпрессовывать старые втулки клапанов, после чего на их место устанавливаются новые элементы. Существует несколько способов для выпрессовки старых втулок. Наиболее простым и самым неправильным является выбивание втулок молотком и зубилом. Данный ударный способ широко применяется в практике «гаражных» мастеров. Отметим, что извлечение втулок в подобных случаях часто заканчивается повреждением посадочного гнезда в головке блока цилиндров.
Немного более правильным вариантом является использование специальной ступенчатой оправки из латуни или бронзы вместо зубила. Такая оправка устанавливается со стороны седла на направляющую втулку, далее по ней ударяют молотком. Указанный способ выпрессовки втулок снижает риск повреждений ГБЦ, но не исключает полностью. Оптимальным же способом выпрессовки втулок является использование специального съемника. Указанный съёмник для снятия направляющих втулок клапанов также используется для последующей установки новых втулок в ГБЦ. Далее мы рассмотрим способы замены направляющих втулок клапанов при помощи оправки и съемника.
Читайте в этой статье
Как самому менять направляющие втулки клапанов
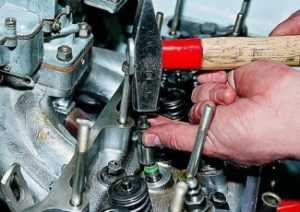
Сначала рассмотрим способ выпрессовки направляющих втулок клапанов при помощи оправки, так как указанный способ является распространенным. Перед заменой втулок снимаются пружины и сами клапана. Как уже было сказано выше, оправка для выпрессовывания втулок клапанов используется ступенчатая. Ступенька необходима для того, чтобы снизить риск повреждений посадочного гнезда в головке блока. Меньший диаметр оправки позволяет ей войти во втулку на 3-4 см, причем с зазором. Больший диаметр позволяет свободно пройти через гнездо в ГБЦ.
Отметим, что зачастую бронзовые втулки достаточно легко выпрессовываются из головки, так как установлены с относительно слабым натягом. Если же необходимо выпрессовать направляющую втулку клапана из более жесткого материала, тогда ГБЦ следует предварительно нагреть до температуры 140-160 градусов Цельсия в электропечи или до 80-90 градусов в емкости с горячей водой. Нагрев головки блока цилиндров позволит уменьшить натяг.
В крайних случаях плотно запрессованную втулку нужно высверливать. Обратите внимание, делать это разрешается только на станке, так как попытки высверлить втулку клапана дрелью приведут к перекосу и повреждениям посадочного гнезда. Втулку также желательно высверливать не до конца, то есть оставлять стенки толщиной около 1-го миллиметра. Так снижается риск повреждений гнезда, а сам остаток втулки легко удаляется оправкой.
Следующим шагом становится обязательный замер натяга новой втулки перед установкой в головку, так как строго запрещается производить запрессовку новых втулок до измерения натяга. Для замеров натяга понадобится определить диаметр гнезда и направляющей втулки. Допускается показатель на отметке от 0.03 до 0.05 мм. Этот показатель следует понимать как то, что диаметр новой втулки превышает диаметр посадочного гнезда на указанную величину.
Слабый натяг по причине гнезда потребует увеличения диаметра гнезда, куда потом устанавливается ремонтная втулка увеличенного размера. Рассверливать гнездо в ГБЦ также нужно исключительно на станке, что позволит избежать возможного перекоса при выполнении нового отверстия. Что касается степени натяга ремонтной втулки, данный показатель следует максимально увеличить, так как в новом отверстии материал более твердый и имеет большую шероховатость на поверхности стенок.
Чтобы запрессовать новые втулки клапанов головку блока следует повторно нагреть в печи аналогично способу снижения натяга при снятии. Параллельно с этим новые втулки охлаждают. Запрессовка новых втулок без нагрева ГБЦ является неправильной. Это касается алюминиевого сплава ГБЦ, в котором происходит деформация при наличии сильного натяга. После такой установки итоговый натяг будет меньше необходимого. В результате после сборки мотора и его нагрева при работе направляющая втулка клапана не будет иметь плотной посадки, а сам клапан в указанной втулке начнет страдать от перегревов. Перегрев клапана будет происходить в результате того, что эффективность отвода избыточного нагрева от стержня клапана к ГБЦ существенно снизится. Неисправность будет быстро прогрессировать, втулка начнет болтаться в посадочном гнезде, что потребует повторной разборки двигателя для проведения ремонта.
Теперь перейдем к тому, как установить направляющие втулки клапанов в головку блока цилиндров. Саму запрессовку реализуют при помощи описанной выше оправки, по которой следует нанести молотком пару резких ударов. Учтите, наличие на новой втулке специального тонкого пояса для размещения маслосъемного колпачка обязывает к тому, чтобы оправка ни с одной стороны не опиралась на данный пояс. Игнорирование данной рекомендации может привести к тому, что втулка деформируется или окажется сломанной.
Завершением процесса установки направляющих втулок клапанов ударным способом является финальная калибровка отверстий. Данную процедуру выполняют при помощи разверток. Рекомендуется использовать алмазные развертки, так как данный инструмент более долговечен и обеспечивает стабильный предсказуемый результат сравнительно с обычными стальными развертками. После обработки отверстий необходимо выполнить проверку зазоров клапанов во втулках с учетом рекомендуемых параметров. Зазоры впускных клапанов должны быть на 0.01 мм меньше по сравнению с выпускными, которые сильнее нагреваются при работе ДВС (например, 0.02 — 0.04 против 0.03 — 0.04 мм). Отметим, что добиваться минимально допустимых зазоров не обязательно. Следует добавить, что данное утверждение особенно актуально для выпускных клапанов, так как малые зазоры в направляющих втулках могут привести к их заклиниванию.
Выпрессовка и установка направляющих втулок клапанов съемником
Далее рассмотрим наиболее оптимальный способ выпрессовки направляющих втулок клапанов специальным съемником-выпрессовщиком втулок. Начнем с того, что съемники бывают разными и являются универсальными инструментами. При помощи данного решения можно снимать втулки клапанов на разных ГБЦ без риска повредить посадочную плоскость в головке блока. Другими словами, наличие съемника сводит к минимуму возможные задиры или другие дефекты отверстия по сравнению с использованием молотка и оправки.
Работа со съемником предполагает:
- под инструмент подкладывается втулка подходящего размера. Подбор такой втулки осуществляется с учетом того, чтобы при установке съёмника резьбовая часть вышла из направляющей клапана на 20-30 мм;
- далее съемник устанавливается и фиксируется парой гаек, которые специально обточены. Также допускается использование одной гайки, если таковая предусмотрена конструкцией съемника;
- следующим шагом становится необходимость придержать верхним ключом съёмник в его центральной части;
- одновременно с этим нижним ключом выпрессовывается направляющая втулка клапана;
После того, как к съемнику прикладывается определенное усилие, можно услышать явный щелчок. Такой звук укажет на то, что втулка клапана сорвана с посадочного места и движется наружу из отверстия в ГБЦ. Далее нужно крутить винт съемника до того момента, пока втулка не будет извлечена. Затем необходимо приготовить новые втулки для запрессовывания. Далее следует повторить все подготовительные процедуры, описанные выше при установке втулок оправкой. Дополнительно можно смазать втулку клапана моторным маслом для облегчения посадки в гнездо.
Чтобы запрессовать втулки съемником понадобятся 2 проставки, которые имеют коническую фаску и упираются в седло клапана. Одна деталь должна иметь больший диаметр, а другая меньший (в соответствии с тем, что посадочное место впускного клапана больше, а выпускного клапана меньше). Также снова понадобиться осуществить подбор распорных втулок съёмника, учитывая при этом необходимость выхода резьбовой части съемника на 20-30 мм при установке новой втулки клапана.Параллельно с этим нужно избежать повреждения пояса (буртика) на направляющей втулке, так как данный пояс служит местом крепления резинового колпачка. Если пояс повредить при установке, герметичность колпачка-сальника будет нарушена. Чтобы не повредить пояс, используется отдельная гайка, которая упирается в направляющую без риска повреждения пояса. Получается, данная гайка поджимает направляющую втулку клапана. Обратите внимание, установка дополнительной гайки уменьшает количество резьбы на шпильке съемника. По этой причине для уменьшения нагрузки на резьбу следует накрутить еще одну втулку съемника.
Рекомендуем также прочитать статью о том, какой зазор должен быть у поршневого кольца. Из этой статьи вы узнаете о правильном подборе теплового зазора поршневых колец во время их замены или в процессе капитального ремонта двигателя.Теперь можно запрессовать втулку съемником. Окончанием запрессовки является момент, когда прокручивать съемник станет тяжелее. Это будет говорить о том, что втулка опустилась на посадочное место и уперлась стопорным кольцом, которое выполнено на направляющей для регулировки правильной посадки. После появления усилия крутить съемник дальше не нужно, так как можно повредить направляющую. Съёмник пора разбирать и снимать, так как новая втулка уже запрессована в головку блока.
Далее втулки понадобится подгонять по посадочным размерам. Это необходимо в том случае, если направляющую слегка сдавило при запрессовке. Выполняется данная процедура аналогично описанной выше, то есть при помощи развертки. Развертка вставляется в отверстие и без давления прокручивается, благодаря чему происходит аккуратное развёртывание. По окончании следует выдуть остатки стружки при помощи сжатого воздуха.
Завершающим этапом становятся обязательные замеры диаметра полученного отверстия в направляющей втулке. Для проверки используется специальный индикаторный нутромер. Также следует измерить толщину стержня клапана при помощи микрометра. Если все выполнено правильно, тогда зазор будет находиться в допустимых пределах.Затем можно вставить клапан и проверить качество его прилегания к седлу. В том случае, если клапан не полностью прилегает к седлу, тогда очевидна потеря соосности между центром втулки и центром седла клапана. Такое явление иногда возникает после замены направляющих втулок клапанов. Для решения данной проблемы потребуется осуществить притирку клапанов. Чтобы притереть клапана, нужно обработать специальной шарошкой седло клапана. После притирки клапанов можно считать процесс замены направляющих втулок полностью завершенным.
Читайте также
krutimotor.ru
Как запрессовать втулку стартера
В данной статье, мы поговорим о стартерах, конкретно речь пойдёт о такой работе как замена втулок стартера ВАЗ 2107-2110. Данная проблема (износ втулок стартера), сильно распространённая среди автомобилей, которые эксплуатировались длительное время и нуждаются в частичном сервисном обслуживании по причине постепенного износа деталей.
Якорь стартера вращается на специальных втулках, изготовленных из бронзы с графитовыми добавками для уменьшения износа при трении. Ресурс втулок как правело большой и выход их со строя возможен только при длительной эксплуатации.
На автомобилях ВАЗ, устанавливается несколько видов стартеров, которые существенно отличаются друг от друга, но принцип замены втулок практически одинаков, так что будем рассматривать всё по порядку.
Не будим, как говорят «лить воду» и сразу перейдём к делу.
Для начала нам нужно полностью разобрать стартер. Как его правильно разобрать, рекомендую прочитать соответствующую статью «Разборка стартера ВАЗ 2106-2114»
Начнём с автомобилей ВАЗ 2101-2107.
В стартерах данной модели, нам нужно заменить две бронзовые втулки, которые находятся спереди (в носке) и в задней крышке. Вот бронзовая втулка, запрессованная в носок стартера.
Запрессованная бронзовая втулка.
Её нужно выбить с посадочного места. Делается это с помощью молотка и специально изготовленной наставкой. Наставкой может быть кусок подходящей трубы или металлический кругляк определённого диаметра.
Выбиваем втулку наставкой из носка стартера.
При выпрессовке, будьте внимательны, что бы наставка ни пошла на перекос, потому как можно повредить посадочное место втулки в носке стартера.
После извлечения старой втулки принимаемся за установку новой. При покупке новых втулок будьте внимательны, что бы они были нужного вам размера и формы, для этого можно воспользоваться штангенциркулем и замерить размеры старой втулки. Вот так она выглядит, изношенная и новая.
Бронзовые втулки.
Смазав новые втулки маслом, запрессовываем их обратно в носок стартера. Втулка должна заходить без применения больших усилий, но если она идёт туго, нужно немного обработать её снаружи мелкой наждачной бумагой, иначе есть опасность что может лопнуть корпус носка стартера в месте запрессовки.
Место где может лопнуть носок стартера.
После запрессовки, втулка вжимается и внутренний её размер уменьшается. Если в снятом положении она находила на вал якоря стартера свободно, то после запрессовки якорь стартера не входит во втулку или если входит то очень туго. Для свободного проворачивания якоря, нам нужно втулку обработать специальной развёрткой диаметром 12 миллиметров. Лучше взять развёртку вот такого типа, это будет самый лучший вариант.
Развёртки 12мм.
Такие развёртки отлично выполняют свою работу и Вы без особого труда, подгоните внутренний диаметр втулки под нужный диаметр. Идеальным вариантом подгона втулки будет то, когда вал якоря свободно проворачивается во втулке и не болтается.
Задняя втулка меняется таким же способом, как и передняя.
Задняя втулка стартера.
Далее, замена втулок стартера ВАЗ 2109.
Задняя втулка меняется точно так же как и на всех стартерах, а вот с передней есть некоторые проблемы, вот об этом и буду дальше расказывать.
Дело в том, что на этом автомобиле (ВАЗ 2109) используется вот такой тип стартера.
Стартер ВАЗ 2109.
Здесь стартер имеет только одну опору сзади, а вторая опора расположена в корпусе коробки передач. Вот в этом и есть вся задача, что бы заменить втулку, которая установлена в картере коробки.
Опорная втулка стартера расположеная в корпусе КПП.
Здесь, просто взять и выбить повреждённую втулку не получится, потому что нет сквозного отверстия, куда бы она выходила, поэтому нужен специальный съемник, с помощью которого мы сможем вытащить её из корпуса коробки передач.
Бывает и такая ситуация, когда втулка снимается вместе со стартером и на оборот она не фиксируется в своём посадочном месте, как это исправить я расскажу чуть дальше.
А теперь представьте, Вы сняли стартер и обнаружили вот такую картинку.
Изношенная втулка стартера.
Видно как расплющило втулку. В таком состоянии якорь смещается со своего места и начинает доставать по магнитам (башмачит), как результат стартер плохо крутит и быстро садится батарея.
Что бы вытащить втулку, нужно сделать вот такой съемник.
Съёмник для втулок.
В его основе используется метчик м14 и приваренная к нему рукоятка. Затем на эту конструкцию одевается массивная металлическая обойма. Инструмент готов к использованию. Закручиваем метчик во втулку и выбиваем её. Эта конструкция похожа на маленький обратный молоток.
Извлечение втулки специальным съемником.
Таким способом мы легко удалили старую втулку.
Посадочное место втулки.
Перед установкой новой бронзовой втулки, нужно убедиться, что она нормального размера, потому что если мы запрессуем её в корпус, то пройти её развёрткой не будет возможности, а значит, нам нужно сделать во втулке немного больше внутренний диаметр. Можно просто купить новую втулку с уже большим внутренним диаметром.
Если втулка спокойно выпадает из своего места, то можно изготовить новую с увеличенными размерами или стандартную усадить на фиксатор резьбы, обезжирив при этом место посадки растворителем.
Далее запрессовываем новую бронзовую втулку.
Запрессованная новая втулка.
Данные варианты замены относятся ко всем стартерам автомобилей ВАЗ, и правильное проведение работ обеспечит нормальную работу стартера.
Если плотно подогнать втулки, стартер будет заклинивать после двух секунд работы или вообще медленно и тяжело крутится. Некоторые мастера говорят, что плотная посадка втулка вал это хорошо, мол, притрётся, поверьте мне, пока они притрутся, Вы десять раз захотите снять стартер и переделать всё заново. Так что лучше сразу сделать всё нормально.
Износ втулок стартера — это довольно распространённая проблема у автомобилей, которые эксплуатируются длительное время и нуждаются в техническом обслуживании. Несмотря на то, что на этапе производства в эти детали закладывается значительный ресурс, со временем они всё же подвергаются критическому износу и становятся неспособными выполнять свою функцию. То есть металлокерамические и бронзовые втулки, по сути, представляют собой расходный материал, срок службы которого зависит от качества изготовления и интенсивности эксплуатации. Поэтому владельцу машины рано или поздно приходится обращаться в автосервис для замены либо решать вопрос самостоятельно. Но для этого необходимо знать, как поменять втулки на стартере, не повредив при этом сами заменяемые детали и их посадочные места.
Как определить, что проблема при нарушении работы механизма запуска двигателя кроется именно в непригодных к дальнейшему использованию втулках? Прежде всего, если они изношены или полностью разрушены, появляется чрезмерное осевое биение ротора. Это, в свою очередь, является причиной утраты контакта и отсутствия массы на роторной обмотке. В результате стартер попросту может перестать работать, а если через раз двигатель и удаётся запустить, то в процессе отчётливо слышны посторонние шумы.
Втулки изнашиваются, потому для нормальной работы стартера потребуется их замена
Как проводится замена втулок стартера ВАЗ-2109
Перед тем как поменять втулки на стартере, его придётся демонтировать, но сначала снимите с аккумулятора клемму. Потом от втягивающего реле необходимо отсоединить два провода. Если для отключения тонкого (питает обмотку реле) нужно за него просто потянуть, то снятие толстого проводника требует использования гаечного ключа на «13», чтобы открутить фиксирующую гайку. Далее, при помощи того же ключа на «13» открутите три гайки, которыми стартер прикручен к блоку сцепления.
Отсоедините провода в задней части реле
После снятия устройство необходимо разобрать, что позволит определить, действительно ли причина неисправности кроется в изношенных втулках. Для этого сначала отсоедините втягивающее реле, открутив два болта при помощи отвёртки. Теперь нужно снять ротор с пластин бендикса. Воспользовавшись ключом на «10», демонтируйте заднюю крышку стартера, после чего откроется доступ к оси ротора. Имеющееся на ней стопорное кольцо необходимо снять при помощи плоской отвёртки. На последнем этапе разборки остаётся открутить гайки на двух шпильках, чтобы все три части, из которых состоит корпус стартера, рассоединились. На этом процесс разборки завершается. О том, как заменить втулки стартера, не прибегая к помощи мастера, вы узнаете далее.
Замена задней втулки стартера
Если в результате внешнего осмотра было выявлено, что одна или обе втулки изношены, их необходимо извлечь из посадочных мест и установить работоспособные аналоги. Даже в тех случаях, когда к дальнейшей эксплуатации оказывается непригодной только одна деталь, обычно меняют и переднюю, и заднюю. Сначала рассмотрим, как правильно должна выполняться замена втулки, расположенной в задней крышке стартера ВАЗ-2109.
Технология демонтажа мало чем отличается от того, как выполняется замена задней втулки стартера на всех классических моделях производства ВАЗ. Другими словами, нужно просто снять заднюю крышку и выбить старую деталь и её остатки. После этого производится запрессовка новой втулки, на чём работа и завершается. Правда, очень часто устанавливаемый образец входит в посадочное гнездо слишком туго. В этом случае его внешний диаметр следует немного уменьшить — заталкивать с большим усилием нельзя, поскольку крышка может лопнуть. Поэтому просто обработайте деталь наждачной бумагой. В процессе установки не рекомендуется использовать смазочные материалы, в противном случае втулка может проворачиваться и разбивать посадочное место.
Замена передней втулки стартера
На переднюю втулку стартера приходится более значительная часть нагрузки при пуске двигателя, в связи с чем она изнашивается гораздо быстрее. Если стартер на вашем автомобиле отказал по той же причине и вы интересуетесь, как заменить втулку стартера ВАЗ-2109, расположенную в его передней части, просто возьмите на вооружение приведённую ниже информацию.
Вначале хочется обратить внимание на то, что в отличие от классики ВАЗ у «девятки» передняя втулка находится не в корпусе стартера — она запрессована в специальное посадочное гнездо в картере сцепления. Поэтому для её снятия стартер разбирать не нужно, но демонтировать устройство всё-таки придётся, чтобы получить доступ к посадочному гнезду. Извлечь деталь голыми руками не получится — для этого понадобится метчик диаметром 14 мм с приваренной ручкой. А также желательно надеть на инструмент тяжёлую металлическую обойму, которая облегчит процесс извлечения.
Вкрутив инструмент до упора, попробуйте вытянуть его вместе с втулкой
Метчик необходимо вставить в отверстие втулки и закручивать его до тех пор, пока он не упрётся в картер. Далее, попробуйте подёргать за ручку. Если усилием рук изделие не удаётся вынуть, в таком случае ударами молотка по обойме вы точно сможете её выбить из гнезда. Перед тем как заменить переднюю втулку на стартере, тщательно очистите посадочное место от загрязнений.
Не спешите устанавливать деталь на своё место, не убедившись, что она подходит по размеру. Довольно часто после запрессовки бронзовая втулка ужимается, уменьшается её внутренний диаметр и вал стартера не заходит в отверстие. После установки никаким образом увеличить диаметр не удастся, поэтому подгонку следует выполнить заранее при помощи специального инструмента — развёртки.
Ни в одном прилагающемся к автомобилю руководстве по эксплуатации и ремонту не указывается, как правильно развернуть втулки стартера, из-за чего многие автолюбители часто оказываются в затруднительной ситуации. В действительности это очень простая операция, которая выполняется легко при наличии тисков и подходящей развёртки. Сначала нужно надеть деталь на вал стартера и, если окажется, что деталь заходит туго, её нужно зажать в тиски и увеличить внутренний диаметр при помощи указанного выше инструмента. Разворачивать изделие нужно постепенно, чтобы не перестараться. Регулярно проверяйте диаметр, надевая её на вал стартера. Если в итоге втулка заходит свободно и без лишнего биения, она может быть установлена в посадочное место в картере сцепления. Установка стартера на автомобиль производится в порядке, обратном снятию.
Удобнее будет, если зажать втулку в тисках
Замена втулки стартера на автомобиле Ока
Несмотря на то что конструкция стартера на Оке реализована по принципу, сходному с ВАЗ-2109 (передняя втулка также расположена в картере сцепления), исполнение механизма пуска двигателя оказалось крайне неудачным, впрочем, как и большинство других узлов этой машины. Основная причина тому — стремление конструкторов максимально удешевить производственный процесс. Именно по этой причине втулки изготавливаются по технологии, взятой из порошковой металлургии, а в качестве исходного материала используется сочетание графитной крошки и бронзы. Из-за этого эти детали имеют очень незначительный запас прочности, что негативно сказывается на их ресурсе.
Для тех автолюбителей, которые интересуются, как заменить втулку стартера на Оке, необходимо знать ещё об одном недостатке двигателя этого автомобиля. Речь идёт о посадочном гнезде в самом картере сцепления, которое в процессе длительной эксплуатации разбивается, причём неравномерно. Поэтому если для замены вы купите изделие стандартного размера (внешний диаметр 13,03 мм), то, скорее всего, оно будет заходить на место слишком свободно и даже начнёт болтаться. Этого допускать не стоит, так как деталь очень скоро придёт в негодность. Зная эту особенность, специалисты рекомендуют использовать втулку ремонтного размера (внешний диаметр 14 мм), но зачастую оказывается, что её диаметр не соответствует размеру и даже форме посадочного места.
В случае когда выработка гнезда относительно одинаковая по всей окружности, проблема решается обычной подгонкой внешнего диаметра втулки при помощи наждачной бумаги. Если же при замене вы обнаружили, что посадочное место разбито неравномерно (к примеру, в виде эллипса), в этом случае его придётся выравнивать. При этом специалисты не рекомендуют пытаться развернуть гнездо передней втулки самостоятельно при помощи ручного инструмента, так как в этом случае не удастся сохранить соосность с валом стартера, что чревато проблемами в его работе. Если вы оказались в такой ситуации, лучше обратитесь к специалистам, которые с использованием специального оснащения развернут отверстие в нужном направлении. Кстати, многие автосервисы занимаются изготовлением втулок стартера ремонтного размера из бронзы.
Изготовить деталь нужного диаметра можно на специализированных СТО
После прочтения этого руководства вы сами смогли убедиться, что замена втулок стартера на «девятке», как и на любом другом автомобиле, — это не самая простая задача. Трудности могут начаться уже на этапе снятия стартера из-за неудобства работы и закончиться запрессовкой втулок. Поэтому в процессе выполнения этого вида ремонта проявите терпение, не спешите и строго следуйте инструкциям.
Устройство стартера
Как же выполняется замена втулок стартера? Прежде чем приступать к сути вопроса необходимо хотя бы в общих чертах познакомиться с устройством агрегата. Автомобильный стартер по своей сути является миниатюрным четырехполосным электродвигателем, обеспечивающим начало вращения коленчатого вала. Он обеспечивает такую начальную частоту вращения, которая необходима для того, чтобы завелся двигатель внутреннего сгорания. Стартер является электрическим двигателем постоянного тока, берущим энергию от аккумуляторной батареи. Получая электрическое напряжение от аккумулятора, он увеличивает мощность посредством четырех щеток, являющихся его неотъемлемой частью. Стартеры бывают:
И первые и вторые имеют как свои преимущества, так и недостатки.
Стартеры с редуктором хороши тем, что могут обеспечивать вращение коленчатого вала, необходимое для запуска двигателя, даже при сильно разряженной аккумуляторной батарее.
Кроме того, сильной стороной редукторных вариантов является присутствие постоянных магнитов, за счет которых проблемы с обмоткой статора сводятся к минимуму. Хотя при длительной эксплуатации такого стартера возможен выход из строя вращающей шестерни. Справедливости ради стоит отметить, что к этому чаще всего приводит низкое качество производства или брак.
Безредукторные стартеры оказывают непосредственное воздействие на вращение шестерни.
Эти устройства имеют более простую конструкцию. Их проще ремонтировать самостоятельно, не прибегая к помощи специалистов из автосервиса. Они достаточно надежны, а вероятность выхода их из строя из-за электрического воздействия стремится к нулю. Однако при низких температурах безредукторные стартеры все же могут работать нестабильно.
В каких случаях требуется замена втулок?
В жизни любого автомобилиста могут быть ситуации когда по различным причинам не удается запустить двигатель. Одной из причин могут быть изношенные втулки. Представим такую ситуацию. Во время заводки стартер с заметным трудом пытается проворачивать коленчатый вал то и дело заедая и останавливаясь. Непосвященный автомобилист при этом недоумевает из-за чего это может происходить, ведь аккумуляторная батарея исправна и полностью заряжена. Причиной в этом случае является задевание якоря за статор. Зазор между первым и вторым всего десятые доли миллиметра, за счет этого даже самый небольшой перекос вала якоря относительно статора обязательно приведет вышеуказанным проблемам. Этот перекос появляется за счет выхода из строя подшипников скольжения в которых и вращается якорь. Как правило, более изношенным является передний подшипник, так как основная нагрузка ложится именно на него. Подшипниками в данном случае являются втулки из латуни. Передний встраивается в специальное отверстие, которое расположено в картере сцепления. Задний же подшипник расположен на крышке стартера.
Технология замены
Прежде всего необходимо отсоединить хотя бы один из проводов от аккумуляторной батареи, а также все провода от стартера. Затем нужно вывернуть нижний болт, который крепит стартер, и ввернуть его с обратной стороны для фиксации двигателя к своей передней опоре. В противном случае мотор может податься вперед. После этого требуется вывернуть остальные два болта, которые крепят стартер, и снять его с автомобиля. Как говорилось ранее, втулка встроена в картер сцепления. Для ее извлечения необходим метчик М12, а также патрон от дрели. Метчик придется вставить в патрон, затем зажать, после чего необходимо с осторожностью ввернуть его во втулку, одновременно нарезая тем самым резьбу. Большая аккуратность требуется вследствие того, что сталь метчика весьма хрупкая и даже небольшой перекос с приложенным усилием может привести к его поломке. При этом хвостовик останется в руках, а режущая часть внутри втулки. Казалось бы, ситуация безвыходная. Однако это не так. Длина втулки равна примерно 14 миллиметрам, а это означает, что на руках имеется примерно 10 или 20 мм режущей части метчика. Нужно взять обычную гайку с точно такой же резьбой М12 и навернуть ее на сломанный метчик. В ситуации когда метчик обломан так, что навернуть на него гайку не получается, можно взять соответствующей резьбы болт длиной около 10 сантиметров и выточить на нем канавки, аналогичные канавкам метчика. А можно поступить более радикально, но в то же время проще. Отправиться в магазин за новеньким метчиком. Метчик снабжен тремя канавками в которые необходимо вставить гвозди подходящего размера. Это нужно сделать таким образом, чтобы их концы выпирали за торец метчика примерно на 10 мм. Получившуюся конструкцию необходимо постараться вставить во втулку с поломанным концом метчика. Получиться может не сразу, однако при должном упорстве операция легко выполнима. После этого можно пробовать выкручивать обломок и снова пытаться вывернуть втулку. Как правило, после нескольких оборотов втулка начнет проворачиваться, и ее можно будет аккуратно выкрутить. Если же втулка сильно прикипела, то придется нарезать в ней резьбу приблизительно на 6 или 8 оборотов. После этого вынуть метчик, а на его место ввернуть подходящего размера болт и уже с его помощью вынимать втулку. Когда на ее место вставляется новая, то слегка запрессовывается.
Если замена происходит уже не в первый раз, то втулку можно довольно легко вставить рукой. Но в процессе длительной эксплуатации это может привести к тому, что она провернется в посадочном отверстии. С течением времени посадочное отверстие будет разбиваться, образуя так называемый эксцентриситет, и может произойти перекос вала стартера. Это означает, что стартер будет заедать, и двигатель завести не получится. Однако это довольно легко устраняется. Для этого необходимо определить размер так называемого эксцентриситета. Затем надо выточить либо заказать у специалиста втулку большего наружного диаметра как раз на размер эксцентриситета. Сбоку этой втулки следует напаять немного припоя. После этого втулка будет входить с маленьким натягом.
Резюме
Стоить отметить, что у стартера без редуктора зазор между якорем и статором больше нежели у редукторного аналога По этой причине допустимый перекос вала у него также больше.
И еще один совет. Если стартер все равно разобран, то неплохо было бы заменить и щетки. Детали ведь копеечные, поэтому ждать их отказа, чтобы потом заниматься с ними отдельно не стоит. Конечно, для всех операций, о которых рассказывалось выше необходим хотя бы небольшой опыт. А он, как известно, дело наживное. В конце концов, чтобы его получить надо пробовать. Дерзайте!
skoda-rapid.ru
Как запрессовать сайлентблок – меняем втулки своими руками + Видео
1 Как определить необходимость замены сайлентблока?
Ресурс резинометаллического шарнира в среднем составляет 120 тысяч километров. На практике все зависит от конкретной модели автомобиля, качества сайлентблоков и частоты движения по неровной дороге. На необходимость замены указывают такие изменения в поведении автомобиля как:
- стуки подвески во время наезда на препятствие,
- потеря управляемости при входе в повороты,
- раскачка автомобиля во время движения,
- неравномерный износ резины и др.
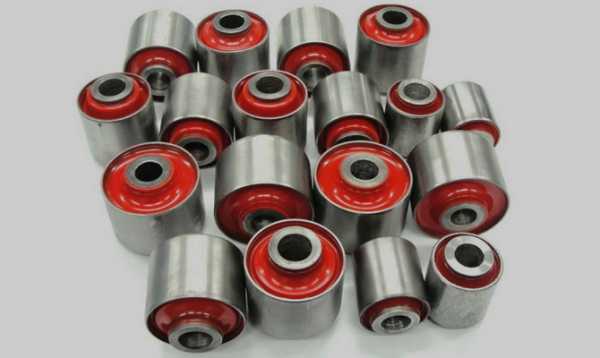
Резинометаллические шарниры автомобиля
Если вы обнаружили одну из представленных выше причин на вашем авто, необходимо провести замену сайлентблоков.
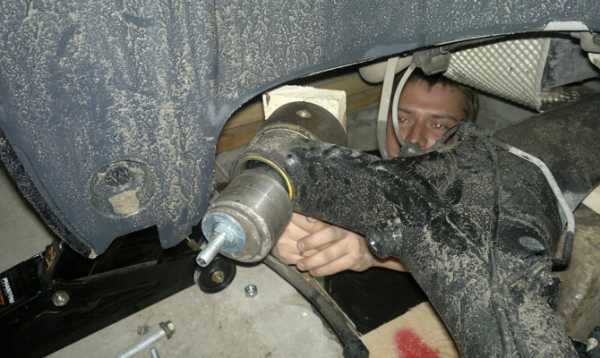
Замена сайлентблока
Так как эта деталь входит в рычаг или другую конструкцию с усилием, для ее установки необходим специальный механический пресс, который имеется в автосервисах по ремонту ходовой. Однако существуют способы как запрессовать сайлентблок с помощью различных инструментов и определенной техники.
2 Правильно запрессовываем сайлентблок своими руками
Замену сайлентблоков необходимо проводить на смотровой яме или подъемнике. Деталь, на которой необходимо заменить сайлентблок, рекомендуется снять. Процедура снятия рычагов и других элементов подвески с резинометаллическими шарнирами может отличаться на разных моделях. При этом выпрессовать старый и запрессовать новый сайлентблок в рычаг без снятия последнего практически невозможно. Для замены сайлентблоков вам потребуются новые детали, которые подходят по диаметру (внешнему и внутреннему, на это стоит обращать внимание в первую очередь при выборе новых сайлентблоков). Чтобы запрессовать новый сайлентблок, вам потребуются следующие детали и инструменты:
- набор ключей и отверток,
- молоток,
- кувалда,
- тиски,
- нож,
- наждачная бумага,
- смазка типа WD40,
- мыльный раствор.
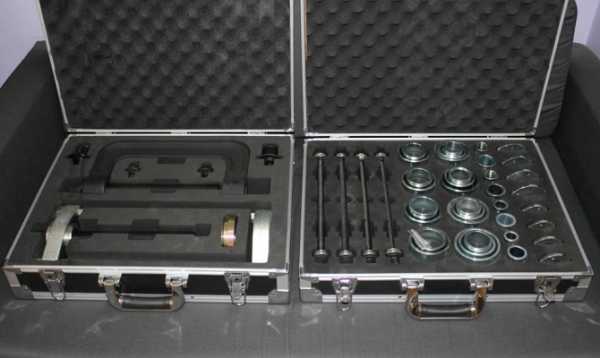
Набор для замены сайлентблоков
Снятую деталь необходимо зажать в тиски. Выпрессовывать сайлетблок можно несколькими способами, приведем наиболее популярные и эффективные.
Выбить сайлентблок с помощью кувалды. Для этого необходимо использовать специальную конструкцию на основе прочного металлического стержня (например, болт М120), шайбу и металлическую трубку с диаметром, который подходит под диаметр сайлентблока. По этой конструкции нужно наносить удары кувалдой до тех пор, пока втулка не выйдет из отверстия. Для стандартного рычага подвески на легковом автомобиле достаточно 5-10 точных ударов.
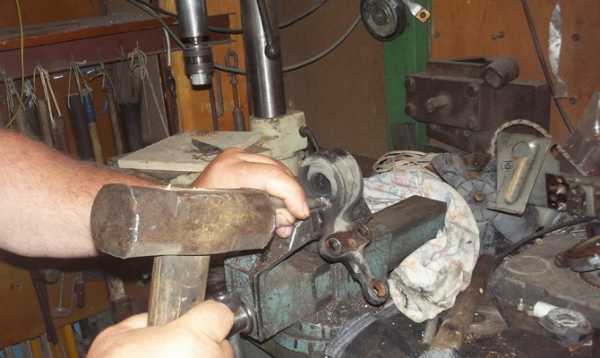
Выбивание детали с помощью кувалды
Распил внутренней втулки. Для этого потребуется качественная ножовка по металлу, с помощью которой необходимо осуществить распил металлического кольца с двух сторон. После надреза резину можно будет вынуть с помощью простой отвертки и молотка. На этапе распила очень важно соблюдать осторожность, так как есть риск задеть ножовкой часть рычага.
Более простой способ как запрессовать сайлентблок заключается в использовании паяльной лампы или газовой горелки. В таком случае старая деталь попросту выжигается. После того как резина прогорит 10-20 минут, сайлентблок можно вытащить с помощью зубила и простого молотка. Как в первом, так и во втором случае после снятия старой детали необходимо тщательно зачистить отверстие при помощи наждачной бумаги и смазать его мыльным раствором (чем больше, тем лучше).
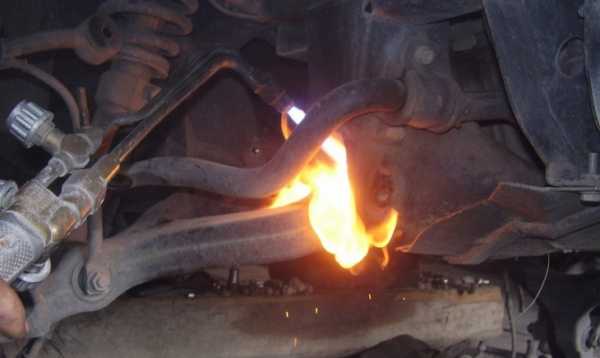
Выжигание старого шарнира горелкой
Теперь необходимо приступать к запрессовке новых сайлентблоков. Для этого рычаг или иную деталь снова необходимо правильно установить на тиски и постепенно сжимать их, контролируя равномерность вхождения детали. Как правило, в тисках до конца сайлентблок не войдет, поэтому необходимо вытащить рычаг и установить его на ровную поверхность, а далее досадить молотком или кувалдой (с максимальной осторожностью, так как можно повредить резину при неточных ударах). Если на этом этапе возникает проблема, следует использовать приспособление, конструкция которого описана в первом способе выпрессовки шарниров.
tuningkod.ru
Как запрессовать втулку в амортизатор
Посторонние стуки или резиновые скрипы во время движения автомобиля по неровностям дороги могут возникать помимо сайлентблоков рычагов из-за сильного износа резиновых втулок и сайлентблоков амортизаторов передней и задней подвески. В этой статье я дам практические советы о том, как без особых усилий осуществить замену изношенных деталей. Начнём с передней подвески.
Виновниками посторонних шумов могут быть сайлентблоки амортизаторов, а в очень редких случаях нижняя подушка на штоке амортизатора. Сперва провлдим визуальный осмотр на наличие потресканной или раздутой резины в сайлентблоке и нижней подушке. В этом случае не помешает помощник, который будет шатать автомобиль, а другой в это время будет руками прощупывать источник скрипов или стуков. При износе подушки или сайлентблока, на месте их заменить не получится, поэтому в любом случае придётся снимать с автомобиля амортизатор, а делается это довольно просто. Автомобиль не нужно поднимать на домкрате, поэтому достаточно того, что он будет стоять над смотровой канавой. Со стороны капота откручивается гайка крепления штока амортизатора к кузову автомобиля. Неудобство в том, что при откручивании проворачивается шток, который нужно держать вторым ключом. Можно придерживать шток и обычным, но удобнее всего будет использовать специальный ключ.
Открутив шток, снимаем с него шайбу с верхней подушкой, опускаемся в смотровую канаву и откручиваем две гайки нижней опоры амортизатора. Главное откручивать их осторожно, потому что они очень часто прикипают к резьбе. Теперь амортизатор вытаскивается вместе с пятой (нижней опорой). В этот момент со штока можно снять нижнюю подушку и при необходимости её заменить. Именно в проушине амортизатора и сидит сайлентблок, который соединён с пятой при помощи болта (пальца), который нужно вытащить, раскрутив гайку. Сайлентблок выпрессовывается наставкой в виде головки подходящего диаметра или обрезка трубы, по которой делают несколько ударов молотком. Чтобы сайлентблок беспрепятственно вышел из проушины, под саму проушину следует подложить большую головку или обрезок трубы.
Внутреннюю часть проушины и внешнюю обойму нового сайлентблока советую смазать Нигролом или моторным маслом, чтобы облегчить запрессовку. Запрессовывается с помощью наставки и молотка. Теперь устанавливается пята, продевается болт, затягивается и амортизатор можно ставить обратно на автомобиль. Резиновые подушки в идеале конечно тоже заменить, но если они целые и на них нет существенных трещин или деформаций, то можно смело их устанавливать.
Амортизаторы задней подвески имеют две проушины, в которые с обеих сторон устанавливаются по две резиновые втулки. Когда они сильно потрескались или порвались, то их уже пора заменить.
Сначала от заднего моста откручивается гайка болта нижней опоры амортизатора, вынимается болт вместе с шайбами по бокам и старыми втулками и металлической втулкой. После этого, откручивается гайка шпильки верхней опоры амортизатора, снимается шайба и амортизатор получится снять с автомобиля. Здесь нужно быть предельно осторожным, потому что шпилька приварена к кузову и её можно испортить. В большинстве случаев, металлическая втулка прикипает к шпильке и чтобы её снять нужно только нагревать паяльной лампой шпильку. Но ничего этого делать не стоит, поэтому пусть она там и остаётся.
Установка амортизатора начинается с верхней опоры. Перед этим, обе проушины амортизатора советую обработать лёгкой наждачной бумагой для того, чтобы убрать шероховатую внутреннюю поверхность в проушине, которая быстро сотрёт новую втулку. На шпильку с прикипевшей металлической втулкой надевается резиновая втулка, затем проушина амортизатора, вторая втулка и шайба, которая затягивается гайкой. Во время затягивания гайки, главное не пережать втулки, так как они работают как сайлентблок, и небольшой зазор будет обеспечивать скручивание втулок при ходе подвески. Правильная установка резиновых втулок также играет важную роль — втулки должны друг на против друга сужаться, а не наоборот. Также обращайте внимание на состояние металлических втулок. Если же они деформированы, то их нужно заменить новыми.
Через проушину заднего моста, продевается болт, на который надевается шайба, первая резиновая втулка, амортизатор, вторая втулка, шайба и затягивается гайка. Затягиваем также аккуратно, чтобы обеспечить свободный ход втулок при работе подвески. Крайне не рекомендую устанавливать полиуретановые втулки. То что задняя часть автомобиля будет жёсткой это понятно, однако жесткие полиуретановые втулки не дают проушине проворачиваться, то есть не создаётся эффекта сайлентблока, в результате чего в большинстве случаев проушина отрывается от корпуса амортизатора.
Как известно всем владельцам классических Жигулей, на задней подвеске автомобиля четыре реактивные тяги — две маленькие, две большие, и одна большая тяга поперечной устойчивости или как её ещё бывает называют — тяга Панара. Внутри них находятся резиновые втулки (подушки), которые также изнашиваются и служат причиной возникновения шумов или скрипов. Для замены подушек тяг, их нужно снимать целиком с автомобиля. Одна сторона тяги при помощи болта (пальца) и гайки соединена с кузовом автомобиля, а другая с задним мостом. Для их снятия нужно только открутить и вытащить оба болта и тяга снимается. Немного сложнее с большими тягами. Чтобы открутить ту часть, которая соединена с задним мостом, нужно сперва открутить нижнюю опору амортизатора и вытащить его болт. Тягу Панара часто очень сложно открутить, потому что болты сильно прикипают и с этим приходится повозиться.
После того как сняты тяги, на которых требуется замены подушек, нужно извлечь старые. Сначала наставкой выбивается старая металлическая втулка, затем резиновые подушки можно выковыривать монтировкой, напильником, выбивать наставкой и молотком или выпрессовывать при помощи наставок и тесков. При установке новых резиновых втулок, нужно знать какой их размер под какую тягу предназначается. Сами подушки бывают двух размеров: большие запрессовываются в большие реактивные тяги и тягу Панара, а маленькие соответственно в маленькие реактивные тяги.
Перед запрессовкой, проушины тяг обрабатываются наждачной бумагой, чтобы также новые подушки не вышли из строя раньше времени. Запрессовываются подушки аналогично молотком или тесками. Для начала хорошо промазываем внутреннюю поверхность проушины тяги и наружную часть подушки жидким мылом или обычным мылом, разведённым с водой, но лучше всего подойдёт жидкое. Установив тягу параллельно земле и наставив сверху на проушину подушку, уверенным ударом молотка загоняете её в тягу. Затем стоит постучать молотком несколько раз с одной, а затем с другой стороны, чтобы резина хорошо расправилась внутри проушины и села на своё место. Затем старая или новая втулка вместе с центральным отверстием подушки смазывается мылом, и втулка также загоняется в подушку молотком.
Всегда трудно забить втулку в небольшое отверстие подушки, поэтому я край втулки, который заходит в отверстие немного затачиваю на верстаке. Если хорошо вдавить втулку заострённым концом в подушку, она немного туда войдёт от руки, и без лишних усилий забивается до конца молотком или тесками.
После замены подушек, тяги устанавливаются в порядке обратном снятию. Советую все болты смазать Нигролом, чтобы исключить прикипание при следующем ремонте.
Сайлентблок или резиномеханический шарнир – две втулки (наружная и внутренняя) между которыми располагается резиновая или полиуретановая вставка. Используются эти шарниры для соединения деталей в подвеске, а также в системе креплений двигателя, КПП и амортизаторов.
За счет упругой силы резины или полиуретана происходит «гашение» пиковых нагрузок, которые возникают при наезде на препятствие, в яму и т.п. При нормальном режиме эксплуатации рабочий ресурс салйнтблоков составляет 100 тыс.км. Но учитывая состояние наших дорог многие из них на доживают и до половины срока. На скорость разрушения и износа полиуратана/резины влияет также манера езды: частый наезд на препятствие или преодоление их при нажатом тормозе способствуют их быстрому разрушению.
Как определить, что сайлентблоки разрушились и нужна замена? Обратите внимание на поведение машины во время движения и торможения. Если она не очень хорошо стала держать дорогу, если ее ведет в одну сторону или она «рыскает», а раньше таких проблем не наблюдалось, скорее всего, вам пора менять сайлентблоки. Если машина при раскачивании издает неприятный скрип – также предстоит замена. И еще один симптом – преждевременный износ шин. Часто разрушение резины/полиуретана видно невооруженным глазом: видны трещины, вспучивания и другие деформации.
Как запрессовать сайлентблок
Сайлентблок входит в рычаг с усилием. Потому просто вставить его на место не получится. Необходим или специальный пресс, который используют на СТО, или некоторые нехитрые инструменты, которые используют умельцы для запрессовки сайлентблоков (см. видео).
«Народных» методов есть несколько. Но смысл их один: сначала нужно удалить старый сайлентблок, зачистить посадочное место на рычаге, и запрессовать новый. С удалением резины обычно проблем не бывает, а удалить наружную обойму (оболочку) бывает сложно.
Перед тем как запрессовать сайлентблок, нужно удалить старый
Как вариант – сделать аккуратный пропил лобзиком (не заденьте сам рычаг), а затем при помощи молотка и какого-то металлического предметы выбить распиленную обойму. Выбрасывать ее не спешите – она может понадобиться при запрессовке.
Затем посадочное место нужно тщательно очистить, удалить все заусенцы и острые кромки. Поверхность должна быть ровная и гладкая. Затем, если сайлентблок не имеет наружно металлической обоймы, его и посадочное место для облегчения процесса смазать. Тут есть два варианта: использовать мыло (мыльный раствор), силиконовую смазку (подойдет для сайлентблоков из полиуретана) или смазку на литиевой основе (с железной обоймой).
Как запрессовать сайлентблок
Далее идет сам процесс. Кто-то использует тиски и кувалду, кто-то только тиски. Самый простой вариант: отцентровать втулку относительно посадочного места и кувалдой вогнать ее на место. Но такой способ требует определенной сноровки. При отсутствии опыта легко повредить не только сайлентблок, но и деталь, в которую он должен быть вставлен.
Чуть более сложный вариант: закрепить рычаг в тиски, отцентровать новую втулку, наставить сверху на нее старую металлическую обойму, сверху какое-нибудь приспособление по которому можно будет бить кувалдой или молотком. Все это отцентровываем и начинаем кувалдой вгонять втулку на место.
Вместо ударов кувалды можно использовать усилие тисков. Тогда вся конструкцию располагаете в горизонтальной плоскости, поджимаете тисками. Крепко прирерживая рычаг или другую деталь, куда запрессовываете сайлентблок, зажимаете тиски до тех пор, пока втулка не станет на место.
Как запрессовать сайлентблок в рычаг
Вот несколько способов того, как можно запрессовать сайлентблок. Какой из них вам больше нравится, тот и используйте.
Отдельно нужно сказать о том, как запрессовать сайлентблок в амортизатор.
Перед тем как, запрессовать сайлентблок в амортизатор, нужно удалить (выбить или выдавить) старый сайлентблок
Снимать старый придется скорее всего по частям – сначала высверлить резину или выдавить (если есть чем). Затем аккуратно ножовочным полотном подпилив наружную обойму, выбить ее молотком (аккуратно, не повредите края посадочного места).
Как запрессовать сайлентблок в амортизатор
Затем вставив подходящий блок и найдя подходящую головку, молотком загоните втулку на место.
Как запрессовать сайлентблок в амортизатор
При всей кажущейся простоте замена сайлентблока требует сноровки и опыта. Если экспериментировать с рычагами еще можно, то запрессовывать сайлентблок крепления двигателя или коробки передач лучше на СТО.
Всем, у кого есть автомобиль, знакома проблема, когда появляется потребность выпрессовать или же запрессовать сайлентблоки. Не всегда хочется обращаться к специалистам, да и сделать это своими руками намного приятнее.
Благодаря этой статье вы узнаете, что такое сайлентблоки, зачем они нужны, и главное — как их запрессовать и выпрессовать в домашних условиях разными методами.
Что такое сайлентблок
Это слово имеет зарубежное происхождение. В переводе с английского языка silent — это тишина, а block — деталь. Сайлентблок, либо просто «сайлент», представляет собой резинометаллическую составную часть, обычными словами — это две втулки, которые соединены между собой слоем прочной резины. Это изобретение, кроме того, что гарантирует комфортное и беззвучное передвижение на автомобиле, имеет еще ряд плюсов, которые будут перечислены дальше.
Предназначение и функции
Сайлентблоки выполняют следующие функции:
- Оберегают составные части от выработки и разрушения посредством гашения колебаний.
- Они глушат колебания, которые поступают от ходовой части колес, таким образом, обеспечивают комфортную и мягкую езду.
- Предотвращают вибрации и биения, которые появляются в процессе движения машины между разными элементами ходовой части и моторного отсека.
И это только главные плюсы, на самом деле их гораздо больше.
Как понять, что пора проводить замену
Перед тем как вы вознамеритесь запрессовать данные детали, в первую очередь следует отлично их осмотреть, чтобы удостовериться в том, что они и вправду требуют замены. Проверьте, нет ли дыр и каких-либо деформаций, не вспучились ли резины на шарнирах и не возникли ли трещины. Проведите манипуляции с составными частями, определяя присутствие люфтов. Если же допустимая норма превышена, значит, замена деталей неминуема. Откладывать процедуру запрессовки не рекомендуется. С течением времени эта проблема только усугубится, она может привести к выходу из строя рычага подвески.
Главные показатели, которые указывают на поломку одной детали либо же нескольких:
- Управлять машиной стало намного труднее.
- Во время преодоления неровностей подвеска начинает громко стучать. Покрышки изнашиваются неравномерно, чего раньше не наблюдалось.
- Стало значительно сложнее регулировать развал-схождение.
Необходимые материалы
Чтобы запрессовать данную деталь в домашних условиях, вам пригодятся такие инструменты:
- Монтировка;
- Домкрат;
- Набор гаечных ключей;
- Новые шарниры.
В качестве смазки рекомендуется применять машинное масло либо же другие виды смазки.
Помимо прочего, вам будут необходимы специальные оправки, предназначенные для запрессовки сайлентблоков, в качестве альтернативы можно воспользоваться куском трубы с необходимым диаметром. Также нужно обзавестись прессом для запрессовки нового резинометаллического шарнира. Когда речь идет о домашних условиях, прессом могут послужить обыкновенные тиски. Вдобавок можно запастись набором кувалд, однако при таком подходе необходимо соблюдать высокую точность выполнения работы.
Выпрессовка в домашних условиях
Заменить данные детали не так трудно, как могло бы показаться на первый взгляд. К примеру, многие владельцы автомобилей в этом удостоверились, когда производили замену деталей, руководствуясь специальной техникой для самостоятельной замены. Именно по данной причине встречается много людей, которые приняли решение собственноручно и в домашних условиях сделать замену сайлентблоков.
Первый метод
В первую очередь, узнаем о том, как это должно быть в идеале.
Рычаг, в котором нужно сделать замену резинометаллического шарнира, устанавливают на специальную проставку под пресс. На эту проставку и будет выдавливаться старый сайлент. Затем сверху устанавливают еще одну проставку — она выдавливает старую втулку. Такой метод употребляют работники СТО, так как у них имеется нужный набор проставок и мощнейший пресс в 10−20 тонн.
Второй метод
Практически у всех владельцев машин мощного пресса, естественно, нет, но у множества в гараже есть домкрат либо хорошие тиски. Если воспользоваться мощными тисками, можно удачно выдавить старые втулки по знакомому нам уже принципу: проставка для исходной втулки и проставка для надавливания на втулку.
На первый взгляд, становится непонятно, как можно домкратом выдавить сайлент? Все очень просто: нужно сварить рамку в форме прямоугольника из швеллера либо уголка, чтобы по высоте она была чуть выше рычага и домкрата. Принцип работы следующий: поставьте домкрат в рамку, затем сверху штока установите проушину рычага, а также две проставки, про которые было сказано выше. Создаем нужное давление, после чего втулка выдавливается из своего посадочного места. Необходимо подчеркнуть, что чаще всего домкрат мощностью в 3−5 тонн не в силах совладать с такой работой, поэтому рекомендуется применять 10-тонные домкраты.
Третий метод
В случае если у вас нет ни пресса, ни домкрата, но при этом присутствует сильное желание заменить сайлентблоки без помощи других, можно воспользоваться третьим методом — использование простого пресс-съемника (болт с гайкой либо же шпилька).
Принцип работы состоит в том, чтобы образовать давление с помощью постепенного закручивания гайки на шпильке, этот метод можно назвать аналогом тисков. Данная шпилька с шайбой подходящего диаметра просовывается в проушину через сайлентблок, затем с другой стороны следует надеть проставку с шайбой и закручивать гайку. Вертясь по резьбе, гайка создает нужное давление и принуждает сайлент выдавливаться в специальную проставку.
Этот «способ» требует использования прочной, каленой шпильки и с такой же крепкой гайкой. Если же взять мягкую шпильку либо гайку, у вас, скорее всего, ничего не выйдет. К примеру, бывают случаи, когда из-за сильного давления шпилька кривится, вследствие чего срывается резьба на гайке. Однако существует и тысячи тех, кому удалось поменять сайлентблоки, используя именно этот метод. Ведь все зависит от качественности и прочности используемого материала.
Плюсом этого метода считается его бюджетность, а также удобство, если посмотреть со стороны «мобильности». Другими словами, вам не надо, к примеру, полностью снимать рычаг или же всю ступицу, достаточно будет просто иметь такой вот простой пресс-съемник.
Четвертый метод
Этот метод можно отнести к кардинальным решениям либо к крайним мерам. Его принцип заключается в том, чтобы всеми популярными методами и приспособлениями добыть сайлент из посадочного места. Для этого вам нужно выбить старую деталь при помощи мощной отвертки либо толстого клинообразного куска арматуры. Вам необходимо постараться забить отвертку либо что-то между сайлентблоком и втулкой, таким образом, деформируя внутри стенку втулки. Теперь, когда втулка сминается и подается внутрь, выбить ее совсем нетрудно. Прежде чем начать выбивать сайлентблок, нужно выдавить либо выжечь внутреннюю втулку детали и по возможности все остатки резины.
Пятый метод
Следующий способ извлечения сайлентблока невозможно назвать выпрессовкой, так как он, как и предыдущий, не предусматривает присутствия пресса: все, что нужно — это полотно по металлу, молоток и отвертка. Принцип простой, однако небезопасный. Устраняем внутреннюю втулку, потом берем полотно и принимаемся резать наружную втулку. Старайтесь максимально прорезать старый сайлент, при всем этом не испортив сам рычаг либо проушину. Лучше всего сделать два надреза, а затем при помощи плоской отвертки сайлентблок будет легко деформироваться и выбиваться.
В случае если ни один из перечисленных выше методов не помог, а вам по-прежнему нужно это сделать, остается только один выход — доверить данную работу специалистам. Чтобы достичь желаемого результата, берите деталь и отправляйтесь на СТО, где специалисты, используя выпрессовыватель сайлентблоков и другие специальные инструменты, качественно сделают всю необходимую работу «в мгновение ока».
Запрессовка сайлентблоков
Про то, как достать «сайленты», мы уже подробно рассказали, теперь появляется иная проблема — как запрессовать данную деталь? Эта процедура трудна тем, что требует определенных умений и способностей. Неправильно или же криво установленный сайлент или не будет ходить, или сломается раньше времени.
Первый метод
Как и в выпрессовывании, запрессовка в идеальном варианте должна выполняться с помощью тисков. Принцип несколько похож, но только с точностью наоборот. Прежде чем запрессовать деталь, нужно наждачной бумагой тщательно очистить посадочное гнездо от остатков и ржавчины предыдущего сайлента. Потом проушина щедро смазывается смазкой наподобие «Литол» либо же мыльным раствором. Устанавливается рычаг, сверху ставится деталь, после этого через особую оправку осуществляется давление пресса на проставку. Она и будет вдавливать деталь в посадочное место.
Второй метод
Когда у вас нет пресса, запрессовать деталь можно, используя при этом вышеупомянутый домкрат либо тиски. Принцип работы ничем не отличается от пресса. Устанавливается рычаг, втулка, а также проставка. После чего под действием силы тисков либо домкрата производится запрессовка детали в посадочное гнездо.
Третий метод
Пресс-съемник. В случае если сайлентблок маленький, «поставить его на свое место» можно с помощью такого же пресс-съемника, который употреблялся для выпрессовки детали из гнезда. Снова принцип одинаковый, лишь в качестве пресса употребляется толстая шайба и шпилька.
Четвертый метод
С использованием кувалды и грубой силы. Этот метод не самый лучший из всех существующих, так как он больше рассматривается чисто с теоретической стороны. Другими словами, он действительно позволяет запрессовать деталь, вот только очень сложно сказать, какими будут результаты и качество работы. Принцип достаточно простой: берем рычаг, на него ставим сайлент, после этого быстро и сильно бьем по нему.
После такого сильного воздействия он должен зайти в ухо рычага. Только главный недостаток метода в том, что спрогнозировать правильность движения данной детали не так просто, он может криво зайти в место посадки. Помимо прочего, может произойти «закусывание» резиновых составных частей и повреждение самого рычага либо же сайлентблока. Проще говоря, удар очень трудно держать под контролем, и часто после подобного рода «экспериментов» приходится обращаться к специалистам и заново все переделывать. Поэтому хорошенько подумайте о возможных последствиях до применения данного способа.
Пятый метод
Последний известный метод запрессовки сайлента — это использование веса авто. Принцип состоит в том, чтобы использовать вес своей машины в корыстных целях. Происходит все это так: под машину устанавливаете гидравлический либо винтообразный домкрат, снимаете колесо. Потом устанавливаете рычаг с сайлентом, который нужно запрессовать, под ступицу.
Дальше хорошенько все ровняем и начинаем медленно опускать домкрат. В таком случае рекомендуется, чтобы вам кто-нибудь помогал. Веса машины будет вполне достаточно, чтобы прочно вдавить деталь в место посадки. Недостаток этого метода в том, что он неудобен и в некоторой мере небезопасен, кроме того, не так просто держать под контролем правильность посадки детали в посадочное гнездо. Но, когда у вас нет иного варианта, метод вполне достоин внимания.
Каждый метод по-своему эффективен и интересен. Обдумайте для себя все плюсы и минусы каждого способа, чтобы наверняка определиться.
Понравилась статья? добавь ее в закладки, чтобы не потерять — ЖМИ «Ctrl + D»
на Ваш сайт.
prodemio.ru
Ремонт ходовой части: как выпрессовать и запрессовать сайлентблоки в домашних условиях? Проверенные способы, которые облегчат вашу жизнь!
Что такое сайлентблок?
Слово «сайлентблок» имеет иностранное происхождение, в переводе с английского «silent» — тишина и «block» — деталь. Сайлентблок или «сайлент» представляет собой резинометаллическую деталь, проще говоря — это две втулки, соединенные между собой толстым слоем прочной резины. Это изобретение кроме того, что обеспечивает комфортное и беззвучное передвижение на авто, имеет ряд плюсов, которые не могу перечислить.
Для чего нужны сайлентблоки?
- Сайлентблоки предотвращают биения и вибрации, которые возникают во время движения автомобиля между различными деталями ходовой части и моторного отсека.
- Защищают детали от выработки и разрушения посредством гашения колебаний.
- Гасят колебания, поступающие от колес и ходовой части, обеспечивая тем самым мягкую и комфортную езду.
И это лишь основные плюсы сайлентблоков, на самом деле их намного больше. Однако мы сегодня поговорим немного о другом, а именно о том, как выполняя ремонт авто своими руками, выпрессовать и запрессовать сайлентблоки, не повредив при этом деталь и свой автомобиль.
Когда и зачем менять сайлентблоки?
Замена сайлентблоков производится чаще всего после того, как водитель начинает замечать ухудшение ходовых характеристик своего авто или после появления посторонних звуков (стуков, скрипов, скрежета), свидетельствующих о необходимости замены «сайлентов». Также нередко поврежденные сайлентблоки обнаруживаются во время диагностики ходовой части на вибростенде.
Если замена сайлентблоков не будет произведена вовремя, владелец рискует получить еще больше поломок, которые так или иначе возникнут при неисправных «сайлентах». Например, из-за одного поврежденного сайлентблока, нагрузка начинает распределяться неравномерно, в итоге происходит выработка в других соединениях и узлах. В результате, вместо одной втулки придется раскошелиться на замену всех сайлентблоков задней или передней подвески.
Более того, следует учитывать тот факт, что неисправная подвеска влияет на: ухудшение уровня комфорта, увеличение расхода топлива, повышенный износ резины, а также увеличивает тормозной путь, в результате риск возникновения ДТП серьезно возрастает.
Как выпрессовать сайлентблок в домашних условиях?
Замена сайлентблоков не представляет собой ничего сложного, например, я, лично в этом убедился, когда производил замену сайлентблоков и амортизаторов на задней подвеске своими руками. Именно по этой причине довольно часто можно встретить тех, кто решил самостоятельно выполнить замену сайлентблоков в домашних ус
vaz-remont.ru
Как запрессовать направляющие втулки клапанов
Как происходит выпрессовка старых втулок
Технология выпрессовки старых втулок бывает разной, но чаще применяют ударный способ. Со стороны седла на втулку устанавливают латунную или бронзовую оправку, по которой наносят удары молотком. Чтобы не повредить посадочное гнездо в головке, оправка должна быть ступенчатой: по меньшему диаметру она с небольшим зазором входит во втулку на глубину 30—40 мм, а по большему — свободно проходит через гнездо в головке цилиндров.
Втулки из бронзы не создают больших проблем при выпрессовке, обычно они устанавливаются в головку с небольшим натягом. При выпрессовке «твердых» втулок головку желательно нагреть до 150 градусов, чтобы несколько уменьшить натяг. Нагревать головку лучше в электропечи, но в условиях гаража подойдет бытовая электроплитка.
Если ни один из способов не позволяет выпрессовать втулку из-за слишком плотной посадки в гнезде, ее приходится высверливать. Обычный сверлильный станок вполне подойдет, а вот при пользовании ручной электродрели неизбежны перекосы и повреждение посадочного гнезда. Кстати, деталь лучше высверливать не полностью. При толщине стенки около 1 мм оставшуюся часть удается выбить без особого труда.
Измеряем натяг втулки перед заменой
Общее правило замены втулок на любых двигателях гласит: ни в коем случае нельзя запрессовывать новые детали без измерений фактического натяга. Поэтому надо точно измерить диаметр гнезда и новой втулки, чтобы определить натяг. Он должен быть в пределах 0,03—0,05 мм (то есть диаметр втулки больше диаметра гнезда на эту величину).
Если натяг недостаточен из-за “слабого” гнезда, придется увеличивать его диаметр, чтобы установить втулку ремонтного размера. Эту работу также следует выполнять только на станке во избежание перекоса отверстия. Натяг для ремонтной втулки желательно сделать большим, поскольку в старом гнезде материал на поверхности уже деформирован, а в новом нет, да и шероховатость поверхности здесь больше.
Как запрессовать втулки клапанов
Перед запрессовкой надо обеспечить разность температуры деталей: головку нагреть до 150 градусов, а втулки охладить. Запрессовку выполняют быстро, двумя-тремя ударами молотка по оправке. Если втулка имеет тонкий поясок для посадки маслосъемного колпачка, то оправка не должна опираться на этот поясок ни с одной стороны, иначе втулка сломается.
Некоторые мотористы запрессовывают втулки “вхолодную”, без нагрева и охлаждения деталей. Это плохо. Алюминиевый сплав при большом натяге деформируется, и реальный натяг уменьшается. Когда при работе двигателя посадка естественным образом ослабляется, клапан в такой втулке начинает перегреваться. Это связано с нарушением отвода тепла от стержня клапана к головке. В дальнейшем втулка начнет “ездить” в гнезде. Иными словами — потребуется повторный ремонт, причем сложнее предыдущего.
После запрессовки втулок и остывания головки их отверстия калибруют развертками. Здесь тоже есть свои хитрости. Желательно применять специальные алмазные развертки — они дают стабильный размер отверстия при довольно долгой работе. Простые ручные развертки из инструментальной стали быстро изнашиваются, обычно их хватает на одну-две головки.
Обработав отверстия, надо обязательно проверить зазоры клапанов во втулках. Для впускных клапанов они должны быть в пределах 0,02—0,04 мм, для выпускных — 0,03—0,04 мм. Стремиться к минимальным зазорам не следует, особенно у выпускных клапанов, поскольку это чревато их заклиниванием при работе.
Ремонт седел клапанов
Для обработки седел применяют различный инструмент. В гараже чаще всего используют ручные угловые фрезы с жестким креплением на направляющем стержне (пилоте). Фрезы обычно имеют углы при вершине 30, 45 и 60 град. Такие фрезы могут быть изготовлены из инструментальной стали или с твердосплавными пластинами.
Основной недостаток данного инструмента — люфт пилота в направляющей втулке, особенно когда у нее есть какой-либо износ. Из-за люфта очень трудно обеспечить соосность седла и втулки.
При обработке формируют определенный профиль седла: уплотнительную фаску и две фаски, примыкающие к ней. Здесь надо руководствоваться данными производителей автомобиля, но есть и некоторые общие рекомендации. У подавляющего большинства моторов уплотнительная фаска имеет угол 45 град. и ширину примерно 1,5 мм. Примыкающие фаски чаще сделаны под углами 30 и 60 град., хотя изредка встречаются седла с более сложным профилем.
Если для ремонта используют ручные фрезы и резцовые головки, то предварительную обработку уплотнительной фаски ведут, пока не получится ровная поверхность без дефектов.
Окончательный этап: притирка клапанов
Окончательная обработка стыка клапана и седла — притирка клапанов. При профессиональном ремонте такая операция практически не применяется. Если седло и фаска клапана обработаны точно, то притирка не нужна, но даже вредна. Другое дело при ручной обработке деталей фрезами и резцовыми головками. Поверхности после ремонта могут иметь не идеальную форму и шероховатость.
Огромным преимуществом российского автопрома является возможность не только замены, но и полноценного ремонта всех узлов и агрегатов автомобилей. Довольно часто автовладельцы проводят полный разбор двигателей ВАЗ 2106 и ВАЗ 2109 и меняют все его составляющие, в том числе и направляющие втулки клапанов.
Конструкция ГБЦ и клапанов
Функционирование клапанного механизма на машинах ВАЗ 2106 и ВАЗ 2109 зависит от работы цепного привода (современные модели авто оснащаются ремёнными приводами).
Устройство головки блока цилиндров довольно примитивное: это сёдла, пружины, направляющие втулки. Захлопывание клапанов в системе осуществляется автоматически при помощи встроенных пружин. Чтобы в камеру сгорания не просачивалось моторное масло, на втулку крепится маслосъёмный сальник.
Клапанный механизм работает в сложных условиях с высокими температурами и масляным голоданием. Основной его задачей является обеспечение герметичности всей системы. Проблемы в его работе могут стать причиной снижения мощности, повышения расхода топлива и быстрого износа ГРМ.
Общее устройство втулок головки блока цилиндров
На современных машинах головки клапанов выполнены из специальных сплавов.
Направляющие втулки клапанов ВАЗ 2106
На ВАЗ 2109, к примеру, направляющие изготовлены из износостойкого материала и запрессованы в головку при высокой температуре, поэтому сменить их достаточно сложно. Но проводить процедуру замены всё же нужно, поскольку втулка, несмотря на её прочность, со временем изнашивается, теряя герметичность. Проблема особенно актуальна для двигателей с большим количеством клапанов.
Назначение гильз
Основная задача клапанов — подача в камеру сгорания топливно-воздушной смеси и вывод из неё выработанных газов. У каждого из цилиндров мотора имеется два клапана — впускной и выпускной. В направляющей втулке движется шток, который и впускает/выпускает отработанные газы и топливную смесь. Герметизация камеры сгорания происходит за счёт точной «посадки» головки на седло.
Качество работы клапанов двигателя зависит от направляющих втулок и сёдел. Во время эксплуатации они изнашиваются и не могут поддерживать высокую производительность двигателя. В такой ситуации их придётся менять.
Почему гильзы могут выйти из строя
Основной причиной выхода из строя направляющих втулок является их износ. В результате увеличивается расход смазочной жидкости, так как люфт деталей приводит к быстрому выходу из строя маслосъёмного колпачка и масло просачивается в камеру сгорания. В результате наблюдается образование нагара, нарушение температурного режима работы мотора, увеличение токсичности отработанных газов и поломка катализатора (если он в машине есть).
Своевременная замена моторного масла и правильная эксплуатация ДВС автомобиля позволяет продлить срок службы втулок и менять их каждые 180–200 тысяч километров пробега. Однако из-за зазоров клапанов и несоответствия моторного масла рекомендуемым нормам может произойти боковой износ втулок и снижение подвижности клапанов по оси штока из-за увеличения радиальной нагрузки на него. По этой причине после смены маслосъёмных колпачков обязательно проводят корректировку зазора в направляющих втулках. При слишком большом зазоре и выявлении люфта втулки в обязательном порядке меняют.
Признаки неисправности направляющих гильз
Износ направляющих втулок клапанов легко и быстро определяется владельцем транспортного средства. Основной симптом этой неисправности — увеличение расхода моторного масла.
Первое, что стоит проверить при увеличении расхода моторного масла, это клапаны двигателя автомобиля. Ещё одним признаком неисправности может стать характерный шум мотора в области головок. Самый лёгкий способ проверить это — открыть капот автомобиля, запустить двигатель и внимательно прислушаться. Если на фоне работы мотора будет заметен странный и необычный шум, то стоит провести диагностику клапанов и направляющих втулок.
Инструменты и материалы
Замена направляющих втулок проводится с использованием следующего инструментария:
- молоток;
- развёртки на 8.022 и 8.028;
- оправка для выпрессовки и запрессовки втулок.
Втулки меняют с помощью ступенчатой оправки — латунного либо бронзового инструмента. Упирается он в направляющую втулку, после чего она выбивается ударом молотка. Такой способ выпрессовки не так вредит ГБЦ, как использование обычного молотка и зубила. Специальный съёмник используется не только для снятия втулок, но и для их замены.
Лучшим инструментом для замены направляющих втулок является съёмник-выпрессовщик. Такие приспособления позволяют снимать втулки клапанов без повреждения посадочной плоскости на ГБЦ. Наличие этого инструмента позволяет избежать задиров и других дефектов ГБЦ, которые могут появиться при использовании оправки и молотка.
Как заменить клапанные втулки на ВАЗ 2106
- Открыть доступ к втулкам клапанов за счёт проворачивания двух крайних шпилек, которые мешают установить оправку. Отворачиваются они методом навинчивания на них четырёх гаек попарно. Можно прибегнуть к специальному шпильковёрту.
Замена клапанных гильз на ВАЗ 2106 — видео
Установка направляющих втулок на ВАЗ 2109
- Смена направляющих втулок на ВАЗ 2109 начинается с фиксации на детали съёмника посредством обточенных гаек. Центральная часть инструмента придерживается верхним ключом, а при помощи нижнего выпрессовывается направляющая втулка. Её выход из гнезда сопровождается характерным щелчком, после этого деталь вынимается.
Итак, поменять направляющие втулки можно как самостоятельно, так и в автосервисе. Это довольно простая в исполнении процедура, которая может значительно продлить срок эксплуатации двигателя автомобиля.
Как меняются направляющие клапанов. Оправка для запрессовки направляющих втулок клапанов
В ходе ремонта ГБЦ мне потребовалось заменить направляющие втулки клапанов. Ударные методы ремонта я не приемлю, поэтому решено было сделать винтовой выпрессовыватель «как у Травникова» , упростив конструкцию и адаптировав ее под свои задачи.
Тут есть нюанс — заводская технология замены направляек на моем моторе предусматривает извлечение и запрессовывание втулок в одну сторону, сверху вниз (в сторону камеры сгорания). Это несколько упрощает конструкцию приспособления, поскольку позволяет менять только сменные упоры, передающие усилие на втулку, а весь бутерброд в КС оставлять как есть. В то же время на самих направляющих втулках отсутствуют буртики либо стопоры, ограничивающие глубину запрессовывания, т.о. этот момент должен быть обеспечен инструментально в процессе работы.
Приняв во внимание эти особенности я изготовил такой вот нехитрый суповой набор:
Основа всего прибора — болт М14 с гайкой. Класс прочности подножный 8.8, на поверку его более чем достаточно для нормальной работы устройства. Метиз потребуется слегка доработать, выполнив в его торце глухое резьбовое отверстие М6 глубиной 10мм.
Шайба и гайка опять же подножные из ближайшего магазина крепежа, упорный подшипник с внутренним диаметром 15мм какой первый попался в Автоштампе, все остальные детали, кроме направляющей втулки из 12Х18Н10Т. Направляющая втулка с конусами нужна для центровки приспособления по седлу клапана, посему сделана из алюминия для исключения повреждения седла. Кроме того изготовление ее из мягкого металла позволяет закрыть глаза на неточность угла 45 градусов, этот момент перестает играть какую либо роль в работе устройства.
Неочевидные, но очень важные моменты: сменные ввертыши необходимы для правильного распределения усилия на втулку клапана при работе — маленькая используется при выпрессовывании, большая используется при запрессовывании и одновременно является кондуктором, обеспечивающим необходимую глубину установки втулок.
Порядок сборки устройства:
Усилия при выпрессовывании весьма небольшие, максимум усилия достигается при страгивании втулки с места, далее же все проходит без видимого напряжения. Я снял на видео работу девайса, но никак не выковырну его из старенького Айфона, так что придется подождать:) любуемся:
Ну и фотодоказательства работоспособности приспособления:
Процесс запрессовывания ничем не отличается от процесса выпрессовывания, кроме использования другого ввертыша. Запрессовывать нужно до упора торца ввертыша в посадочное место нижней тарелки пружины на ГБЦ.
Засим доклад окончен, любите свои моторы друзья!
Пока!
Зачастую ремонтом автомобилей занимаются сами владельцы, приспосабливая для этого частные гаражные помещения. Особенно это касается отечественных марок машин, конструкция которых предусматривает ремонт основных узлов и механизмов. Не являются исключением ремонтные работы ответственных узлов двигателя.
Ремонт головки блока цилиндров часто подразумевает замену направляющих втулок клапанов газораспределительного механизма, который отвечает за своевременную подачу воздуха и топливовоздушной смеси в цилиндры двигателя внутреннего сгорания.
ГБЦ – узел — крышка, функция которого — сочленение с блоком двигателя, закрытие блока от разнообразных неблагоприятных факторов. Это деталь сложной конструкции, созданная из дералюминиевого сплава или легированного чугуна. Внутренняя поверхность головки блока цилиндров имеет ровную, гладкую структуру, что показывает значимость данного узла. Нижнюю часть головки БЦ производят чуть шире для более надежного соединения с блоком цилиндров.
Признаки, указывающие на осмотр и необходимость замены направляющих втулок:
- прослушивается посторонний стук в двигателе;
- повышается расход масла;
- наблюдается поперечный люфт клапана во втулке.
Часто понятия «выпрессовка » и «запрессовка » деталей ассоциируют с термином «демонтаж » и «монтаж ». Это не совсем правильно, так как демонтажные или монтажные работы больше относятся к свободно посаженным деталям, а вот выпрессовка или запрессовка — к деталям, установленным с натягом. Это более трудоемкий процесс.
Для процесса запрессовки и выпрессовки применяют разные по своей конструкции виды прессов: гидравлические, верстачные реечные, верстачные винтовые. У каждого пресса имеются свои функциональные возможности. Верстачные реечные и верстачные винтовые уместно применять для выпрессовки небольших деталей: втулок, пальцев, шпилек и т.д. Гидравлические прессы уместны при выполнении работ с большими деталями. Замена втулки клапанов. Для установления новых деталей требуется подготовить каждое гнездо — выпрессовать старые элементы.
Способы выпрессовки и запрессовки втулок клапанов ГБЦ
Способ 1 . Самый распространенный, простой и неправильный метод — выбивание втулок с помощью молотка, зубила. Извлечение подобным способом втулок приводит к порче посадочного места в ГБЦ. Такой подход к ремонту чаще наблюдается у мастеров — самоучек.
Способ 2 . Использование специализированной латунной оправки вместо зубила почти полностью исключает риск повреждений газораспределительного механизма, но не даёт полной гарантии качества. Оправка должна быть расположена со стороны седла на направляющую втулку, которую в дальнейшем выбивают молотком.
Способ 3 . Применение специального съемника — это процесс, наиболее оптимальный при изъятии втулок. Правильный демонтаж и монтаж втулок. Основной проблемой при демонтажных работах втулок является снятие слоя металлической поверхности посадочного места. Для наилучшей выпрессовки необходимо нагреть головку блока до девяноста градусов. Перед монтажными работами новых направляющих будет правильнее выдержать их в масле в течение 5-8 минут для пропитки. Головка блока нагревается, а сами втулки охлаждаются с помощью жидкого азота или низких температур морозильной камеры.
Как самому заменить направляющие втулки с помощью оправки
Шаг 1. Выпрессовка втулок клапанов
Непосредственно перед разборкой втулок производится подготовка газораспределительного узла. Оправка для процесса выпрессовки имеет форму ступеней. Ступень крайне необходима, чтобы исключить процесс повреждения посадочного гнезда в ГБЦ. За счет небольшого диаметра оправка входит во втулку на 3-3,5 см. Расширение диаметра позволяет спокойно пройти сквозь гнездо в головку блока цилиндра.
Небольшой диаметр оправки позволяет ей войти во втулку на 3-3,5 см с зазором. Наибольший размер диаметра позволяет намного легче продвинуться через гнездо в ГБЦ. Стоит напомнить, что втулки из бронзы с легкостью демонтируются из головки по причине относительно слабого натяга при установочном процессе.
Сложнее обстоит дело с выпрессовкой втулки из чугуна и металлокерамики. В этом случае нужно заранее нагреть ГБЦ в термопечи до 130-135 градусов Цельсия. Нагрев можно производить и в емкости с горячей вводов, нагретой приблизительно до 100 градусов. Это процедура позволяет ослабить натяг. В некоторых случаях запрессованную втулку высверливают, но велик риск порчи стенок посадочного гнезда.
- Работа производится только на стационарном сверлильном станке.
- Диаметр сверла должен быть меньше посадочного гнезда примерно на один миллиметр.
- Втулка высверливается аккуратно, не до самого конца.
Шаг 2. Замер посадочного места
Перед установкой втулки в головку блока цилиндров необходимо произвести замеры натяга. Только после этого можно производить запрессовку новой детали.
Замер натяга подразумевает:
- Замер диаметра самого гнезда нутрометром.
- Замер направляющей втулки микрометром. Допустимый показатель натяга при запрессовки — 0.032 — 0.051 мм. При ослабленном натяге из-за гнезда следует увеличить диаметр посадочного гнезда, в которое затем следует запрессовать ремонтную втулку большего размера. Данный вид работ производится только на стационарных станках: фрезерных или сверлильных. Размер натяга заменяемой втулки необходимо увеличить по причине более жесткого и шероховатого материала поверхности обработанных стенок. Для запрессовки головку блока нагревают, а саму втулку подвергают охлаждению. Без нагревания ГБЦ процесс считается неправильным. Особенно это относится к ГБЦ, изготовленной из алюминиевого сплава. Сам материал легко деформируется при сильном натяге. Результат — нет плотной посадки направляющей втулки клапана при сборке и нагревании двигателя, сам клапан начинает портиться от перегревания. Такой вид неисправности со временем прогрессирует. Может потребоваться ещё один разбор двигателя для осуществления ремонтных работ.
Шаг 3. Установка направляющих втулок клапанов
Запрессовку втулок производят с помощью оправки, описанной выше, нанесением точных ударов молотком. Необходимо помнить, что имеющийся на вновь поставленной втулке опорный поясок не должен страдать при запрессовке оправкой. В противном случае может произойти поломка или деформация втулки.
Шаг 4. Калибровка отверстий
Для финальной калибровки отверстий понадобятся развертки определенного размера. Профессионалы чаще всего применяют алмазные развертки, а не стальные. Инструмент из этого материала считается более долговечным и значительно точнее производит калибровку отверстий.
- Стержни впускных клапанов должны иметь размер меньше выпускных (0,022-0,055 мм).
- Выпускные клапана подвергаются более сильному нагреванию при работе двигателя внутреннего сгорания (0,029 – 0,062 мм). Не стоит также стремиться к минимально допустимому размеру зазоров, так как это может привести к заклиниванию клапанов.
Добрый день. Начиная эту статью, я немного объясню, о чем пойдёт речь. Речь пойдёт не только о специальных инструментах, с помощью которых можно произвести ремонт головки блока цилиндров, но и о том, как правильно работать этим инструментом. Оказывается, что ни все умеют правильно пользоваться специальным инструментом и это приводит порой к не поправимым последствиям. Я постараюсь подробно описать весь процесс работ, что бы вы смогли самостоятельно проделать всю работу по ремонту ГБЦ.
И так начнём. В принципе весь процесс практически одинаков, что на классике, что на Самарах и им последующих моделях. Первое с чем нам приходится столкнуться, это снятие пружин и клапанов (разсухаривание клапана). Для этого используется специальный съёмник.
Конечно же, есть много всяких приспособлений, но это самое распространительное. Именно его мы и рассмотрим. Съёмник крепится передней частью к шпильке, а специальный захват устанавливаем на тарелку пружины.
Теперь нам понадобится специальная подложка в камеру сгорания под клапана. Зачем она нужна? При нажатии на рычаг приспособления, клапан уйдёт в низ, и он пройдёт соответствующий путь пока своей тарелкой не упрется, например, в стол на котором забираете головку. В это время пружина сожмётся и не даст вытащить сухари. Этой подложкой может послужить кусок резины нужной толщины или деревянный брусок.
Придавив на рычаг, клапан упрётся в подложку, а вы с лёгкостью можете извлечь сухари.
Все сухари аккуратно складывайте в коробочку, потому что потом искать потерявшийся сухарь очень тяжело.
Есть, конечно, и варварский способ извлечения сухарей. Прибегать к нему стоит только в особых случаях, когда нет специального съёмника. Этот процесс осуществляется с помощью молотка и отрезка металлической трубы (здесь хорошо подойдёт свечной ключ).
После нанесения удара не убирайте сразу молоток, иначе сухари разлетятся в стороны. Можно в верхнюю часть трубки запихнуть кусочек ветоши, это задержит вылетающие сухари.
Следующий инструмент, который нам понадобится – это съёмник для снятия направляющих втулок клапанов. Сам процесс замены направляющих клапана я написал в статье ( Замена направляющих втулок клапанов ). Есть разные съёмники. Первый (ударный).
Почему ударный? А потому что запрессовка происходит ударом молотка по оправке. Такой метод ни всегда проходит гладко. Бывали случаи, когда оправка заходила на перекос и снимала немного металла с посадочной плоскости втулки, тем самым уменьшается плотность её посадки, что не хорошо в нашем случае.
Распространённым приспособлением стал винтовой плавной запрессовки съёмник.
Этот съёмник позволяет плавно и безопасно заменить втулку. Продаются они в авто магазинах, но можно изготовить и самому как нарисую чертёж обязательно выложу.
Так же нам понадобится инструмент для снятия и установки сальника клапана. Работу по снятию и установке сальников нужно проводить осторожно. Почему осторожно? Потому что бортик, на который устанавливается сальник очень хрупкий и его можно повредить.
Для демонтажа применяются специальные зажимы, кстати, этот зажим можно изготовить самому. Я видел, как один мастер сделал зажим из распиленной на пополам гайки, приваренной к круглогубцам.
Метод извлечения прост. Охватываете снимаемый сальник и строго вертикально прокручиваете захват по оси в одну и другую сторону, при этом делаете натяжку вверх. Строго запрещается расшатывать сальник в стороны, потому как есть опасность повредить бортик направляющей втулки и нужно будет менять направляющую.
Установка сальников (колпачков) делается в специальной оправке.
Прежде чем устанавливать сальники, проверьте их на плотность установки. Попробуйте руками его надеть на ободок втулки. Если он не находит, то это наш сальник и его можно устанавливать. Если сальник находит свободно или болтается, то он будет пропускать масло и не справится со своей задачей.
Я рекомендую пользоваться именно такими развёртками, потому что у них есть направляющая для точного захода в отверстие. Нам нужна развёртка с диаметром 8.00 мм. Развёртывание происходит следующим образом. Устанавливаете развертку в только что запрессованную направляющую втулку и лёгким нажатием прокручиваем её до тех пор, пока она не выйдет с другой стороны.
Следующим этапом будет притирка клапанов. Перед тем как притереть клапана их нужно обработать шарошками.
Использовать лучше вот такие шарошки. Нам понадобится три шарошки с разным углом обработки. Первая 45 градусов, вторая 60 и третья 30. Они обрабатывают седло клапана с лёгкостью и без особого усилия.
Пожалуй, из специального инструмента это всё, дальше всё можно сделать с помощью ключей и отвёрток.
В данный момент это всё и если появится ещё что-то, обязательно допишу.
automotocity.com