Установка момента впрыска (зажигания) на КАМАЗ.
Необходимость регулировки возникает очень часто у водителей КамАЗа. Например, в поле оборвало пластины привода ТНВД, и что делать? Побежал за пластинами, поменял и тут надо обычными ключами без стробоскопов и прочей спецтехники, не то что бы уехать, но и продолжить работать дальше. Как же это сделать в полевых условиях? Все будет описано простым и понятным языком, но придется немного вникнуть в теорию…
Многие счастливые обладатели дизельной техники привыкли «момент впрыска» называть «зажиганием», как на бензиновом двигателе, но это не важно, главное понять смысл процесса.
Момент впрыска — это начало подачи дизельного топлива, когда поршень подошел к верхней мертвой точке при закрытых впускных и выпускных клапанах. Получается, поршень сжал воздух максимально, именно в этот момент надо подавать топливо.
Вообще, а зачем его настраивать? Почему с завода не поставят раз и навсегда, что бы мы не мучились?
Все просто! Для каждого двигателя момент впрыска свой, нет абсолютно одинаковых агрегатов и узлов, да и топливо тоже может отличаться банально — зимняя и летняя солярка.
Для этого нам и дана возможность его регулировки, хотя абсолютно на каждом двигателе есть МЕТКИ или ГРАДУСЫ… Если зажигание поставить точно по меткам машина будет конечно работать идеально, но если это эталонный двигатель, эталонный ТНВД, и ГОСТовское топливо. Метка — это своего рода ориентир, от которого надо исходить, иначе не было бы у нас возможности крутить-вертеть в поисках наилучшего.
На КамАЗе сам привод ТНВД ставится на шпонку со стороны коробки, а вот муфту ТНВД можно повернуть в двух вариантах с разницей в 180 градусов. Так вот обычно, когда зажимной винт привода находится сверху, тогда метка на ТНВД и на муфте должны быть друг напротив друга
. Итак, поставили все по меткам, затянули и можно заводить. Машина должна завестись, если нет запуска и с выхлопной идет белый дым, значит перепутали на 180 градусов. Открутили, повернули на 180 , затянули и теперь точно заводим. Если меток нет, или их там непонятное количество набитых ранее, то ставить надо примерно посередине регулировочных прорезей.
После того как завели машину надо понимать, а как же должен то работать двигатель, какой же он, тот самый «момент»? Чтобы это понять, надо знать признаки ПОЗДНЕГО и РАННЕГО момента.
Поздний момент впрыска — это когда поршень уже пошел вниз от ВМТ, и только тогда начинает поступать топливо, взрыв идет вдогонку. В работе двигателя это можно определить по некоторым признакам:
Белый дым из выхлопа, особенно на холодном двигателе, и чем позднее , тем больше дыма.
Тупо набирает обороты.
Мягко работает.
При плавном нажатии на педаль газа двигатель трясет на средних оборотах, потом его как бы прорывает и тряска исчезает на повышенных.
Машина тупая и плохо тянет.
Большой расход.
Греется.
Ранний момент впрыска — это когда поршень еще не подошел к верхней мертвой точке, а топливо уже начало поступать, взрыв идет навстречу поршню. В работе двигателя это определяется по следующим признакам:
Двигатель работает жестко.
При резкой перегазовке или в нагрузку слышен звон, как будто клапанов, и чем выше температура двигателя, тем звон сильнее.
При сильно раннем моменте впрыска возможен белый дым.
Плохая тяга.
Большой расход.
Как правило, момент выставленный по заводским меткам чуть поздноват.
Далее, допустим, поняли, что зажигание позднее и надо его поставить раньше, что делать, куда крутить?
Момент выставляется при рабочей температуре двигателя, но если явно видны признаки неправильной работы и на холодном, то можно уже начинать регулировку.
Выставляем привод таким образом, что бы метка была сверху, (можно и свою сделать) и отпускаем два болта на 17. Теперь надо понять что двигатель остается на месте, а крутится муфта ТНВД.
Раньше — двигать привод ТНВД по ходу движения, то есть по часовой стрелке.
Позже — двигать привод ТНВД в обратную сторону движения — против часовой стрелки.
И самое важное!!! Двигать привод надо по чуть-чуть, примерно на толщину спички от метки!!! И обязательно затягивать болты!!!
После чего запускаем двигатель и проверяем его работу, если изменений нет или работа машины все еще не устраивает, можно повторить, и двинуть еще немного. Это необходимо повторять до тех пор, пока при резкой газовке или в нагрузку не появится небольшой звон, тогда можно двинуть чуть обратно, и звон исчезнет, вот это и будет тем самым моментом.
Главное двигать на что-то ориентируясь и немного сразу, чтобы не запутаться.
Правильно выставленный момент впрыска, это наилучшая тяга, с наименьшим расходом топлива, а это очень важные показатели в работе любой машины.
Фирсов Роман
Установка опережения впрыска на дизеле
Своевременное опережение впрыска так же важно для дизельных двигателей, как правильно отрегулированный момент зажигания для бензиновых.
Зачастую говорят не об опережении впрыска, а об опережении нагнетания как о главном контрольном параметре топливного насоса высокого давления. Речь идет о том, какой угол пройдет коленчатый вал за время от момента начала выталкивания топлива из нагнетательной секции насоса в топливопровод высокого давления до момента, в который поршень достигнет ВМТ. Установка опережения впрыска — это установка момента нагнетания топлива топливным насосом относительно определенного положения коленчатого вала. Обычно она производится по положению первого цилиндра, и положение насоса высокого давления для первого цилиндра будет правильным и для всех остальных цилиндров.
Проверка и установка опережения впрыска производится в случае падения мощности двигателя, при «жесткой» работе его, дымности выхлопа, а также периодически — через каждые 50 000—60 ООО км во время плановой проверки на СТО.
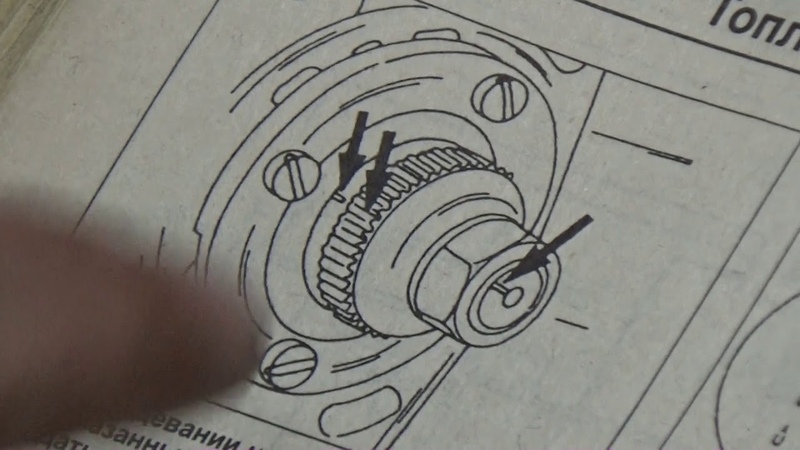
Статический метод
Статический метод проверки и установки опережения впрыска наиболее прост и доступен.
Потребуется моментоскоп — приспособление для определения момента впрыска методом слива (прозрачная пластмассовая трубка с наконечником, позволяющим надеть ее на выпускной штуцер, на место снятого трубопровода, ведущего к форсунке).
Потребуется также ключ для снятия наконечника провода высокого напряжения и ключ для выполнения регулировки в случае необходимости.
На плунжерных насосах проверка производится следующим образом.
Снимите трубопровод высокого давления, ведущий к первому цилиндру, и наденьте на штуцер трубку-моментоскоп
Установите управляющий рычаг регулятора в положение максимальной подачи топлива. Если нужно, удалите воздух из топливной системы топливоподкачивающим насосом или при помощи стартера.
Проворачивайте коленчатый вал до момента, пока стеклянную трубку моментоскопа не заполнит топливо, затем верните коленвал назад примерно на четверть оборота.
Снова медленно проворачивайте коленвал, наблюдая при этом за трубкой моментоскопа: начало движения топлива в трубке означает момент начала нагнетания, поэтому запомните положение установочных знаков на маховике или насосе.
Если установочный знак на фланце насоса не совпадет со знаком на распредвале, требуется регулировка опережения зажигания.
Регулируется оно или вращением переставной части муфты в пределах, которые позволяет регулировочный винт, или (в тех конструкциях, в которых насос крепится фланцево) вращением насоса относительно своей оси.
Остается добавить, что плунжерные насосы встречаются довольно редко, около 90 % дизельных автомобилей оснащены насосами распределительного типа.
К топливным насосам высокого давления распределительного типа относятся насосы фирмы «Bosch», японских фирм, большинство насосов фирмы «Lucas». В таких насосах есть заглушки, закрывающие отверстие для установки датчика часового типа или установочного штифта (производимых, кстати, теми же фирмами).
Проверка опережения впрыска на насосах распределительного типа сложнее.
Для нее потребуются уже упомянутые датчик, а также установочные штифты в зависимости от типа двигателя. Эту операцию, как и проверку опережения впрыска динамическим методом с использованием специального дизельного стробоскопа («Bosch», «Sun», AVL, «Time Track Stanodyne», «Technotest» и др.), выгоднее производить у профессионалов на СТО.
Опережение впрыска на насосах распределительного типа статическим методом регулируется так.
Вращая коленвал, установите — поршень первого цилиндра в ВМТ. Ориентируйтесь по установочным знакам, либо действуйте с помощью установочного штифта:
Снимите заглушку с топливного насоса, вставьте на ее место датчик в специальной оправке и действуйте в соответствии с инструкцией. Датчик должен показать заданную величину опережения нагнетания впрыска. В случае необходимости регулировки ослабьте крепление насоса и поверните его соответствующим образом, а затем повторно проверьте опережение.
При регулировочных работах не трогайте креплений, указанных стрелками:
Проверка и установка угла опережения впрыска топлива двигателя Камаз-740
Категория:
Автомобили Урал-375д, Урал-4320
Публикация:
Проверка и установка угла опережения впрыска топлива двигателя Камаз-740
Читать далее:
Проверка и установка угла опережения впрыска топлива двигателя Камаз-740
Исполнители: механик-регулировщик и водитель.
Инструмент и принадлежности: ключи гаечные 13, 14, 17 и 19 мм, ломик для поворота коленчатого вала, отвертка.
Продолжительность работ: 35 мин.
Рекламные предложения на основе ваших интересов:
Содержание работ и технические условия Проверка угла опережения впрыска топлива
1. Снять с двигателя воздушный фильтр и соединительный патрубок впускных трубопроводов.
2. Оттянуть рукоятку фиксатора, смонтированного на картере маховика, повернуть на 90° и отпустить.
3. Снять крышку люка в нижней части картера сцепления.
4. Провернуть ломиком коленчатый вал в такое положение, при котором фиксатор войдет в паз маховика, а метки на фланце ведомой полумуфты будут находиться вверху.
5. Проверить, совпадают ли метки А на корпусе топливного насоса высокого давления и Б на муфте опережения впрыска. Если метки совместились, то угол опережения впрыска топлива установлен правильно. Если метки не совместились, необходимо провести установку угла опережения впрыска топлива.
6. Оттянуть рукоятку фиксатора, повернуть на 90° и отпустить в мелкий паз.
Установка угла опережения впрыска топлива
1. Ослабить верхний болт, провернуть коленчатый вал на один оборот и ослабить второй болт ведомой полумуфты привода.
2. Развернуть автоматическую муфту опережения впрыска в направлении, обратном ее вращению, до упора болтов в стенки пазов (вращение муфты правое, если смотреть со стороны привода).
3. Оттянуть рукоятку фиксатора, повернуть на 90° и отпустить в глубокий паз.
4. Провернуть ломиком коленчатый вал по ходу часовой стрелки (если смотреть со стороны вентилятора), пока метка В на заднем фланце 5 ведущей полумуфты привода топливного насоса не окажется в верхнем положении. При этом фиксатор должен войти в отверстие на маховике.
5. Провернуть автоматическую муфту опережения впрыска за фланец ведомой полумуфты привода в направлении вращения привода топливного насоса до совмещения меток на корпусе топливного насоса и муфте опережений впрыска,
6. Затянуть верхний стяжной болт ведомой полумуфты привода.
7. Оттянуть рукоятку фиксатора, повернуть на 90° и ввести в мелкий паз.
8. Провернуть ломиком коленчатый вал по ходу вращения и затянуть второй болт 4 ведомой полумуфты привода.
9. Проверить правильность установки угла опережения впрыска топлива согласно пп. 1—6 настоящей карты.
10. Пустить двигатель, проверить и при необходимости отрегулировать минимальную частоту вращения коленчатого вала на холостом ходу (см. технологическую карту № 15).
11. Установить на двигатель соединительный патрубок впускных трубопроводов и воздушный фильтр.
12. Закрыть крышкой люк картера сцепления.
Рекламные предложения:
Читать далее: Проверка и регулировка минимальной частоты вращения коленчатого вала двигателя Камаз-740
Категория: — Автомобили Урал-375д, Урал-4320
Главная → Справочник → Статьи → Форум
Установка ГБО 4 поколения (метан) для непосредственного впрыска бензина
Важно знать
Все больше производителей автомобилей в погоне за увеличением мощности своих моторов при уменьшении объема двигателя переходят на на системы непосредственного впрыска бензина. Основными отличиями данных систем от традиционного распределенного впрыска являются наличие топливного насоса высокого давления (ТНВД) и бензиновых форсунок, расположенных не во впускном коллекторе, а непосредственно в камере сгорания блока цилиндров. По сути это аналог дизельного впрыска, только воспламенение происходит не от сжатия, а от электрической искры. КПД таких моторов увеличивается за счет более эффективного распыления жидкого топлива и, как следствие, лучшего смешивания его с воздухом. Таким образом в камеру сгорания такого двигателя возможно подавать большее количество топлива, в результате мощность мотора повышается. К основным недостаткам таких моторов можно отнести большой расход топлива и низкий моторесурс.
Из всего выше сказанного можно сделать вывод о высокой актуальности установки газобаллонного оборудования на данные моторы по следующим соображениям:
- мощность двигателя не снизится при работе на газе, так как газовое топливо эффективно смешивается с воздухом независимо от того подается оно во впускной коллектор или непосредственно в камеру сгорания;
- экономия на топливе будет весьма существенной, так как расход 4-х цилиндрового мотора с непосредственным впрыском сравним с расходом 6-8-ми цилиндрового мотора с традиционным распределенным впрыском топлива.
Особенности ГБО 4 поколения для непосредственного впрыска бензина
Внешне и по составу комплектующих ГБО для непосредственного впрыска идентично традиционным системам 4-го поколения, но имеются существенные отличия в следующем:
- во всех режимах работы на газовом топливе в камеру сгорания подается небольшая порция бензина для охлаждения бензиновых форсунок, расположенных непосредственно в камере сгорания;
- программное обеспечение строго индивидуальное для конкретно взятого мотора и привязано к заводскому коду мотора, так как для каждого мотора на специальном стенде подбирается минимальная порция бензина, необходимая для охлаждения бензиновых форсунок во всех режимах работы двигателя;
- корректировка угла опережения зажигания не производится ни для метана ни для пропана, так как система всегда работает на двойном топливе;
- подбор компонентов их размещение строго по монтажной схеме производителя системы ГБО;
- для точной доводки системы на всех режимах работы двигателя требуется высокая квалификация специалиста.
Метан |
Пропан |
---|---|
хранится в баллоне в сжатом газообразном состоянии | хранится в баллоне в сжиженном состоянии |
октановое число 110-125 |
октановое число 100-105 |
расход 1:1 к бензину | расход в среднем на 15 % выше расхода бензина |
измеряется в кубических метрах | измеряется в литрах |
занимает примерно 25 % объема баллона (в баллон 50 л. ![]() |
занимает минимум 80 % объема баллона (в баллон 50 л. входит минимум 40 л. газа) |
Распределенный впрыск газа — 4 поколение |
|
---|---|
Метан | Пропан |
баллоны только цилиндрической формы | баллоны цилиндрические и тороидальные |
баллоны металлические, металокомпозитные, композитные, композитные — облегченные |
баллоны только металлические |
давление в баллонах 200-250 атм. | давление в баллонах 16-20 атм |
рекомендуется коррекция угла опережения зажигания | коррекция угла опережения зажигания необязательна |
газовая магистраль стальная | газовая магистраль медная, пластиковая, алюминиевая |
газовый редуктор с дополнительной ступенью понижения давления | редуктор без дополнительной ступени |
В остальном системы идентичны.![]() |
Безопасность
Важнейшим аспектом внесения изменений в конструкцию автомобиля является безопасность. Особенно это касается установки ГБО.
На что необходимо обязательно обращать внимание при установке ГБО-метан на свой автомобиль для безопасности эксплуатации:
* запорная арматура каждого баллона (вентиль) оснащена электромагнитным клапаном, пожарным клапаном и скоростным клапаном;
* газовый баллон при размещении внутри автомобиля должен быть оборудован газонепроницаемым кожухом (венткамерой) для исключения проникновения газа во внутреннее пространство автомобиля при возникновении утечки в запорной арматуре или повреждении газовой магистрали;
* газовый баллон должен иметь минимум 2 ленты крепления. Если баллон подвешивается на ленты, то их должно быть минимум 3 при объеме баллона до 100 литров и 4 ленты при объеме более 100 литров;
* газовые форсунки должны быть жестко прикреплены на двигателе или к кузову автомобиля (ни каких пластиковых хомутов!). Газовый клапан и газовый редуктор жестко крепятся на кузове автомобиля;
* выносное заправочное устройство (ВЗУ) должно находиться либо снаружи автомобиля (лючок бензобака, бампер и т.п.) либо под капотом и его крепление должно исключать возможность вращения;
* газовая магистраль должна быть заключена в защитную оболочку;
* газовый шланг должен быть маркирован надписью (CNG) и надписью о допустимом давлении, минимум 6 bar;
* вся проводка ГБО должна быть в защитной оболочке и максимально проходить по штатной проводке автомобиля.
Все эти требования закреплены в Техническом Регламенте Таможенного Союза (ТР ТС 018/2011), действуют с 1 января 2015 года и обязательны для всех установщиков ГБО.
Проверка и установка угла опережения впрыска топлива автомобиля Урал
Чтобы проверить или установить правильно угол опережения впрыска топлива, необходимо знать:
— у двигателя положение коленчатого вала при такте сжатия в первом цилиндре;
— у топливного насоса высокого давления положение кулачкового вала в начале подачи топлива восьмой секцией.
Чтобы быстро и безошибочно определить и установить в указанные положения коленчатый вал двигателя и кулачковый вал топливного насоса высокого давления, на корпусе топливного насоса, автоматической муфте опережения впрыска топлива и заднем фланце ведущей полумуфты, нанесены метки.
На рис. 2 эти метки соответственно обозначены «А», «В» и «С».
Угол опережения впрыска топлива установлен правильно, если метки «А» и «В» на корпусе топливного насоса и муфте опережения впрыска топлива совмещены, а метка «С» на заднем фланце ведущей полумуфты находится в верхнем положении, для установки заднего фланца 8 в положение, при котором метка «С» займет верхнее положение по фиксатору, необходимо отвернуть болты, и снять крышку нижнего люка картера сцепления.
Вставляя ломик в отверстия маховика, повернуть коленчатый вал в положение, при котором метка «С» будет двигаться снизу вверх.
В этот момент повернуть на 90˚ штифт фиксатора маховика и опустить его в глубокий паз.
Продолжить вращение коленчатого вала ломиком за маховик до момента, когда фиксатор войдет в отверстие маховика.
Это будет верхнее фиксированное положение метки «С» на фланце 8; при этом в первом цилиндре будет заканчиваться такт сжатия.
Совместить метки «А» и «В» на корпусе насоса и муфте опережения впрыска топлива, установить насос и закрепить болтами к блоку двигателя.
Болты крепления насоса к блоку затягивать равномерно, в несколько приемов, в последовательности, показанной на рис. 3.
Не нарушая взаимного совмещения положения меток «А» и «В» на корпусе насоса и муфте опережения впрыска топлива, соединить болтами 6 (см. рис. 2) верхний конец ведомой полумуфты 2 с передней пластиной 4.
Установить штифт фиксатора в мелкий паз, повернуть коленчатый вал на один оборот, установить и затянуть второй болт 6.
Когда на двигателе установлен компрессор и насос гидроусилителя, фланец 8 (особенно метку на фланце) увидеть затруднительно.
В этом случае более удобно верхнее положение метки «С» на заднем фланце 8 ведущей полумуфты определить по клапанам.
Для этого снять крышку головки первого цилиндра (рис. 4), и проворачивать коленчатый вал ломиком за маховик до начала закрытия всасывающего клапана (передний клапан от вентилятора).
Перевести штифт фиксатора в глубокий паз и продолжить вращение коленчатого вала пока фиксатор не войдет в отверстие маховика.
Это и будет фиксированное положение коленчатого вала, при котором метка «С» фланца 8 (см. рис. 2) будет находиться в верхнем положении.
После установки насоса на двигатель, подсоединения к нему привода управления, трубок подвода (отвода) масла, топливопроводов и трубок высокого давления дополнительно проверить и уточнить установку угла опережения впрыска топлива.
Для этого рычаг 2 (см. рисунок) управления регулятором перевести в среднее рабочее положение и опустить до упора в болт 3.
Прокачать систему питания двигателя ручным подкачивающим насосом в течение 2—3 мин.
Повернуть коленчатый вал на пол-оборота против часовой стрелки, если смотреть со стороны вентилятора, и перевести штифт фиксатора в глубокий паз.
Медленно вращать коленчатый вал по ходу вращения до тех пор, пока фиксатор не войдет в отверстие маховика.
Если метки на корпусе насоса и муфте опережения впрыска совместились, то угол опережения впрыска установлен правильно.
Если метки не совместились, то ослабить верхний болт 6 (см. рис. 2) ведомой полумуфты, установить штифт фиксатора в мелкий паз, повернуть коленчатый вал по ходу вращения на один оборот и ослабить крепление второго болта 6.
Повернуть муфту опережения впрыска против хода (против часовой стрелки, если смотреть со стороны маховика) до упора болтов в паз передней пластины 4.
Опустить фиксатор маховика в глубокий паз и повернуть коленчатый вал по ходу вращения до совмещения фиксатора с отверстием в маховике.
Повернуть муфту опережения впрыска за фланец ведомой полумуфты 2 по ходу вращения до совмещения меток на корпусе насоса и муфте опережения.
Затянуть верхний болт 6, перевести штифт фиксатора маховика в мелкий паз, повернуть коленчатый вал на один оборот и затянуть второй болт 6.
Проверить точность совпадения меток на корпусе насоса и муфте опережения впрыска еще один раз тем же способом.
После установки и проверки угла опережения впрыска топлива запустить двигатель, прогреть до температуры охлаждающей жидкости 80˚ С и болтом 3 (см. рисунок) отрегулировать минимальную частоту вращения коленчатого вала, которая не должна превышать 600 об/мин.
Установка впрыска водо-метанола | Тюнинг ателье VC-TUNING
Установка занимает примерно 4 часа (kit Devilsown). В багажник был установлен бак для водо-метанольной смеси, на него был прикреплен насос (штатное место), по салону были проложены проводка и армированный магистральный шланг 4AN, под капотом были установлены контроллер, реле/предохранители и форсунка.
Как работает впрыск водо-метанола?
Основные плюсы которые даёт впрыск метанола, это существенное охлаждение впускного воздуха, значительное увеличение эффективного октанового числа топливной смеси, увеличение угла зажигания. Все это позволяет избежать детонации — серьёзной угрозы для любого мотора. При использовании системы впрыска водо-метанола на двигателе работающем на 98м бензине, эффективное октановое число топливной смеси попадающей в цилиндры, будет сопоставимо с использованием бензина с октановым числом 116, т.к. октановый эквивалент метанола 123.
Какой прирост мощности можно ожидать от установки системы водо-метанола?
Прирост зависит от конфигурации мотора. К примеру, на стоковом Evolution 8-9, со стоковой турбиной можно ожидать прироста в 30-40л.с. В то время как, на том же автомобиле но с большей турбиной, такой как FPRed или Garrett GT30, можно уже ожидать прибавку в 60-70л.с.
Говоря проще, система впрыска водо-метанола даёт прирост аналогичный переходу на спортивное топливо с октановым числом 116, имея в баке всего лишь 98й.
Насколько сложно использовать системы впрыска водо-метанола?
Хорошая качественная система впрыска водо-метанола работает полностью автоматически и не создаёт трудностей, при грамотной установке и настройке. Она должна знать когда ей включаться и выключаться, уметь правильно дозировать водо-метанол, так же обеспечивать возможность отслеживания параметров системы и самое главное, обеспечивать безопасность мотора в случае механической поломки частей системы или падения уровня жидкости. От пользователя требуется лишь заправлять систему.
Может ли водо-метанол повредить мотор?
Нет — если система работает правильно, то ожидать от неё можно только плюсов. Свечи, клапана, камеры сгорания будут оставаться чистыми, так как метанол будет растворять отложения и нагар, температура выхлопа снизится. Повреждения мотора обычно происходят от детонации, и чрезмерного перегрева камер сгорания и поршней – то с чем призвана бороться система впрыска водо-метанола.
Какие жидкости можно использовать в системе впрыска?
Возможно использование химически чистого метанола, дистиллированной воды и водо-метанольной смеси в любых пропорциях, так же этанола изопропанола и их смесей с водой. Можно также использовать дешевые зимние жидкости для омывания стекол -30. Следует остановиться на одном варианте смеси, тщательно настроить под неё двигатель и не менять её.
В общем и целом можно подвести итог — хорошая проверенная система, грамотно установленная и настроенная, не создаёт неудобств её пользователю и позволяет получить значительный прирост мощности.
Как выглядит kit водо-метанола смотрите далее.
Установка зажигания ЯМЗ 238: настройка угла впрыска и оценка точности
Установка зажигания ЯМЗ 238 проблематична. С ней часто приходится сталкиваться водителям грузовиков, работающих на дизельном двигателе. Чтобы исправить это, необходимо знать, как правильно откалибровать угол опережения впрыска топлива и как правильно отрегулировать зажигание.
Угол впрыска
Чтобы точно определить, какой угол опережения должен быть выставлен, на футляре имеет два просвета для контроля, а на диске – ориентиры, расположенные в двух местах. Обозначения имеют маркировки в виде букв и цифр. Нижнее значение указывается цифрами 20, 15, 10, 5, а боковое – буквами А, Б, В, Г.
Чтобы установить ЯМЗ 238, необходимо открыть на футляре вращающегося диска проемы. Затем нужно провернуть коленчатый вал до соединения штрихов, расположенных на теле распределительных шестерней и на шкиве. Сразу смотрят, совпали или нет метки на маховике.
Калибровка угла проводится до тех пор, пока отметка А не совпадет с отметкой Б. Первая располагается на торце, а вторая – на указателе.
Во время калибровки, полученные показатели должны совпадать с теми, которые указаны. Все регулировки выполняются строго при закрытых поршнях в первом цилиндре.
Настройка угла
Чтобы правильно провести калибровку, необходимо выполнить следующие действия:
- Осмотреть муфту опережения зажигания на плотность посадки. Если она села хорошо, затягивается шуруп клеммового вала.
- Шурупы зажимной системы отворачиваются.
Отметки А и Б соединяются.
- Шурупы на приводе закрепляются.
- Оценивается место фиксации пластин. Допускается незначительное расхождение этого показателя в пределах 1 мм.
- Оценивается правильность выставления УОВТ. Для этого нужно прокрутить коленвал. Допустимое отклонение от нормы – 10 или одно деление.
- Обязательно проверяется уровень масла в ОВТ.
- Оценивается как выставлен угол впрыска горючего.
Чтобы проверить точность выставленного угла, зажимное устройство смещают проемом в верхнюю позицию и убирают крышку. При правильности выставления, во время вращения вала под углом 70 градусов, из проема покажется смазка. После закрывается крышка.
Способы задать угол ЯМЗ 238
Настройка угла оказывает влияние работа каждой муфты, а также подбор на переднем торце тела агрегата чисел опережения.
Чтобы калибровка была выполнена правильно, необходимо:
- Убрать рукав высокого давления от патрубка первой ячейки насоса.
- Измеритель зажимается на том же патрубке.
- Спускается воздух. Для этого убирается крышка ТНВД. Это действие помогает в дальнейшем прокачать горючим систему ДВС.
- Прокачку проводят до тех пор, пока горючее не перестанет пениться. После этого можно закрыть крышку.
- Проверяется регулярность подачи горючего скобой контролера. Если все сделано правильно, то оно должно поступать без перебоя.
- Проворачивается вал ДВС. Это выполняется слева направо. Повороты делаются до тех пор, пока не появится горючее в стеклянном шланге измерителя.
- Вал продолжают вращать, контролируя горючее в отсеке из стекла.
Выполнение анализа движения топлива
При самостоятельном выставлении зажигания, необходимо уметь оценивать движение топлива. В норме, при движении вала в отсеке топливо движется, а все штрихи стоят по отметкам.
При начале движения горючего, штрихи не совпадают, необходимо сделать следующее:
- Извлекают фиксирующие шурупы.
- Убирается полумуфта валика на кромке.
- Все крепежи фиксируются.
- Еще раз оценивается угол вращения.
Если во время движения топлива, штрихи перескакивают через нужную отметку, то следует выполнить следующее:
- Полумуфту ДВС прокручивают по резьбе кромки.
- Муфту смещают на один показатель относительно кромки. Это приравнивается 4-м штрихам, расположенным на диске.
Оценка точности впрыска
Разброс показателей должен быть не больше 10. Чтобы оценить показатель точности впрыска, необходимо:
- Из вытачки на маховике устанавливается фиксирующая деталь. Фиксировать верхние позиции не нужно.
- Вал проворачивается на полтора оборота.
- Вал вращают аккуратно, оценивая состояние горючего в отсеке.
Когда горючее начнет двигаться, нужно следить, чтобы на футляре маховика совпадали с числом показателя, который указан на муфте ОВТ. Если выявятся расхождения, то отворачиваются фиксаторы, а после вращается муфта на кромке в обратном направлении. Затем фиксаторы возвращаются в исходное положение, оценивается угол впрыска.
В идеале, выставление угла впрыска должно выполняться с использованием специального оборудования профессиональными мастерами. Самостоятельно провести эту процедуру не просто. В случае неправильной оценки работы зажигания, могут возникнуть нежелательные последствия, которые будет проблематично исправить.
— обзор
2.30.2.1 Блок впрыска
Блок впрыска, как показано на Рисунке 2, состоит из нагретого цилиндра, содержащего поршневой винт. Как следует из названия, шнек можно перемещать горизонтально (возвратно-поступательно), чтобы выполнить действие впрыска, или вращать, чтобы действовать как насос расплава при перемещении расплава вперед. Винт установлен в упорных подшипниках на одном конце цилиндра и обычно приводится во вращение гидравлическим двигателем и поступательное движение с помощью гидроцилиндра. В последние годы популярность машин с полностью электрическим приводом также возросла благодаря их повышенной эффективности и чистой работе. Для более распространенных машин с гидравлическим приводом мощность обеспечивается одним электродвигателем, перекачивающим гидравлическую и масляную системы под давлением, последняя — для охлаждения. Машины с более высокими характеристиками могут также иметь гидроаккумулятор для повышения давления впрыска и сглаживания нагрузки. Переключение различных действий машины обеспечивается сервогидравлическими клапанами, управляемыми в современных машинах микропроцессорами.Сложные компьютерные системы управления позволяют тщательно контролировать все аспекты функций машины и цикла формования, включая синхронизацию, температуру, давление и механизмы безопасности.
Цилиндр станка, обычно изготовленный из закаленной (азотированной) легированной стали, рассчитан на высокое давление впрыска в диапазоне 100–200 МПа. Цилиндр нагревается несколькими ленточными нагревателями, которые позволяют регулировать температуру по всей длине цилиндра от конца подачи до сопла. Сырье, обычно в виде гранул полимера, под действием силы тяжести подается в цилиндр из бункера на стороне подачи.
Ключевым компонентом узла литья под давлением является винт со спирально намотанными лопастями, которые определяют канал потока, как показано на рисунке 2 (а). Винт плотно входит в ствол, зазор между лопастью и внутренней стенкой ствола составляет менее 0,1 мм. При вращении шнека относительное движение между основанием канала шнека и неподвижной стенкой цилиндра заставляет полимер, в твердой или расплавленной форме, двигаться вперед в условиях увлекаемого потока к концу сопла машины.Конструкция шнека сложна и может быть адаптирована для конкретных материалов, однако винты общего назначения, которые часто используются для композитов с короткими волокнами, содержат три отдельные зоны. Во-первых, зона подачи на приводном конце шнека имеет глубокий равномерный канал. Его основная функция — предварительный нагрев и начало плавления полимерных гранул. Во-вторых, это зона сжатия, которая имеет постепенно уменьшающуюся глубину канала и служит для сжатия, консолидации и плавления гранул. Плавление происходит за счет трения и сдвига материала в канале сжатия, а также за счет кондуктивного нагрева от нагретой стенки цилиндра.Наконец, зона дозирования, которая также имеет постоянную глубину канала, действует как основная секция смешивания и подает гомогенный полимерный расплав в сопло. Длина шнека делится между зонами подачи / сжатия / дозирования, как правило, в соотношении 2: 1: 1, хотя длина зоны сжатия может варьироваться, в частности, если она адаптирована для соответствия конкретным материалам, например, полукристаллическим материалам, таким как нейлон, с резким плавлением. точечное преимущество от короткой зоны сжатия. При литье под давлением типичное соотношение длина / диаметр ( L / D ) для шнека составляет 20: 1 или 22: 1, а степень сжатия (глубина зоны подачи: глубина зоны дозирования) обычно находится в диапазоне 2– 4, опять же в зависимости от материала.
Лепестки шнека обычно режутся с квадратным шагом (шаг = наружный диаметр винта), что дает угол вылета 17,7 ° (см. Рисунок 2 (а)). Для повышения скорости пластификации обычно используются барьерные винты, хотя и с дополнительным капиталом Стоимость. Они представляют собой двойную лопастную конструкцию в зоне сжатия, которая определяет два соседних канала, как показано на Рисунке 2 (b). Расположение лопастей таково, что ширина одного из каналов постепенно уменьшается вдоль зоны сжатия, а ширина другого канала увеличивается.Расплав полимера может переходить из одного канала в другой по соединительной ленте. Восстановительный канал несет в основном твердый полимер и увеличивающийся канал полимерного расплава. Принцип действия предотвращает перенос твердой пробки в ванне расплава, что может произойти в едином канале с равномерной шириной, тем самым улучшая теплопередачу и скорость плавления. Хотя барьерные шнеки улучшают плавление, смешивание с короткими шнеками все еще может быть проблемой. Этого можно избежать, если включить смесительную головку в зону дозирования.Смесительная головка представляет собой короткую секцию шнека, которая разделяет расплав на ряд каналов, соединенных лопастями с прорезями.
Движение расплава между этими каналами улучшает характеристики смешивания, что особенно важно для цветных маточных смесей и материалов, содержащих добавки.
Наконечник винта включает обратный клапан обратного потока (см. Рисунок 2 (c)), который обычно представляет собой скользящее кольцо. По мере вращения шнека поступательное движение расплава переводит кольцо в открытое левое положение.Во время впрыска части цикла (т.е. возвратно-поступательное действие винта), обратное давление из пула расплава вперед винта приводит к тому, кольцу клапана, чтобы двигаться вправо и уплотнение против упорного кольца. Это предотвращает любое перемещение расплава обратно по шнеку во время впрыска.
Материал вводится в форму через нагретое сопло (см. Рисунок 2 (d)). Несмотря на то, что доступны форсунки с запорными клапанами, обычно используется открытая форсунка, которая обеспечивает свободное течение расплава полимера во время впрыска и минимизирует мертвые зоны, в которых может скапливаться материал. Во время возвратной части цикла, т.е. когда шнек вращается, низкое давление и высокая вязкость расплава обычно обеспечивают минимальное слюноотделение расплава из открытого сопла. Открытые сопла также сводят к минимуму повреждение волокон в композитах с короткими волокнами. Однако для материалов с очень низкой вязкостью может потребоваться запорная форсунка. Сопло нагревается одной лентой нагревателя, а температура точно регулируется с помощью обратной связи от термопары, установленной в сопле. Весь узел впрыска установлен на линейном подшипнике и может быть втянут во время закручивания, чтобы уменьшить потери тепла из-за контакта между горячим соплом и более холодной формой.
№ 100 единиц, относящихся к литьевой машине | Техническое руководство
Устройство впрыскаУзлы впрыска машины для литья пластмасс под давлением — это узел, в котором поршень для впрыска или винт перемещается вперед внутри цилиндра для впрыскивания расплавленного пластика в форму.
Производительность впрыскивающего устройства выражается скоростью впрыска (объем расплавленного пластика, который впрыскивается за одну секунду, см3 / с) или скоростью впрыска (скорость поступательного движения плунжера, мм / с).

В случае супертехнических пластмасс, есть некоторые материалы, которые вызывают потерю качества формованных изделий, если не используется впрыскивающее устройство с высокой скоростью впрыска, или, с другой стороны, есть также пластики, для которых подходят впрыскивающие устройства. который может стабильно впрыскивать на низкой скорости.
Можно сказать, что тип используемого узла впрыска тесно связан с используемым формовочным материалом.
Наконечник узла впрыска снабжен соплом, и обычно наконечник сопла имеет сферическую форму, чтобы он мог плотно контактировать со сферическим гнездом литниковой втулки пресс-формы, и были учтены соображения чтобы не было подтекания пластика при впрыске.Существует много типов форсунок, таких как открытая форсунка, закрывающаяся форсунка или форсунка с игольчатым клапаном и т. Д.
Блок зажима формыБлок зажима формы — это блок, отвечающий за установку формы в машину для литья под давлением , а также открытия и закрытия формы.
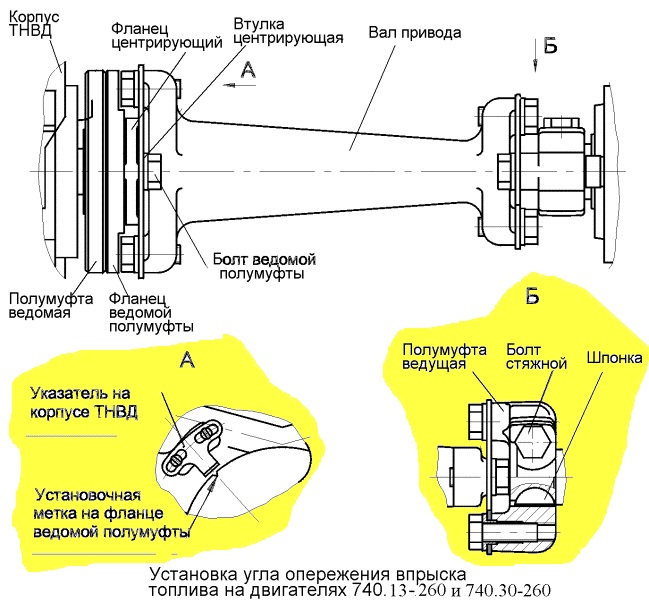
Способы зажима формы можно разделить на следующие два типа.
1) Тип прямого давления
2) Тип переключателя
Тип прямого давления — это тот, при котором плита на подвижной половине приводится в действие посредством гидравлического цилиндра для зажима формы. В этом методе, поскольку можно зажать форму с постоянным давлением, прилагаемым к большой площади, этот метод подходит для форм формованных изделий, имеющих большую площадь выступа.Кроме того, регулировка усилия зажима проста, и есть преимущество в том, что работа по установке формы не является обременительной, даже если толщина формы изменяется.
Переключаемый тип — это тот, который использует зажимное усилие, когда рычажный механизм выдвигается или сжимается. Этот тип имеет высокую скорость открытия и закрытия, и, хотя он сокращает время цикла, требуется время для настройки, поскольку работа по регулировке усилия зажима должна выполняться для каждой формы.
Устройство защиты формы предусмотрено в последних узлах зажима формы. Существуют также устройства, в которых зажим формы выполняется при низком давлении до определенного процесса зажима формы, и предусмотрено защитное устройство с датчиком, который останавливает зажим формы под высоким давлением, если случайно попадает какой-либо посторонний предмет или бегунок, и т. д., попал между формами.
Обычно узел зажима пресс-формы также снабжен устройством для выталкивания формованного изделия, которое имеет конструкцию, в которой выталкивающий стержень движется вперед от движущейся половины и заставляет выталкивающую пластину пресс-формы двигаться вперед, тем самым выталкивая формованное изделие. .
Термопластавтомат — Beaumont Technologies, Inc.
Ниже приведены различные термины, относящиеся к обработке и литьевой машине.
Стяжки для стяжек — Поддерживайте и выровняйте плиты, которые затем поддерживают форму. Пространство между стяжками ограничивает размер формы, которую можно разместить в литьевой машине.
Форма — Обеспечивает формирование и выталкивание формованной детали
Контроллер — Управляет термопластавтоматом
Форсунка — переходник между узлом впрыска и формой, который предназначен для подачи расплава из узла впрыска в форму
Ствол — В нем находится винт, и в нем плавится пластик
Нагревательные ленты — Нагрейте бочку и поддерживайте соответствующую равномерную температуру для приготовления расплава.
Винт — он находится внутри цилиндра и предназначен для дозирования материала от подачи до сопла и для пластификации полимерных материалов.
Винтовой двигатель -Вращает винт для пластификации и подготовки расплава для впрыска в форму.
Индикатор положения винта — показывает размер выстрела в зависимости от положения винта
Бункер — Пластиковые гранулы хранятся в бункере, откуда они загружаются в бочку
Подвижная плита — Поддерживает половину В (обычно половину выброса) формы и открывает и закрывает форму в каждом цикле формования.
Стационарная плита — Поддерживает половину формы
Thermolator — Регулирует подачу и температуру охлаждающей жидкости в форму.
Время впрыска — Время, за которое винт перемещается из начального положения впрыска в положение переноса (размер впрыска).
Положение переноса — это расстояние на контроллере термопластавтомата, на которое проходит винт, чтобы достичь желаемого положения переноса детали.Это момент, когда мы переключаемся с управления скоростью на управление давлением. Обычно это происходит в точке, где деталь заполнена на 95-99%. Это должно быть предусмотрено для подушки.
Уплотнение затвора — Время, при котором материал на затворе замерзает и больше материала не может скапливаться в полостях. Неправильное уплотнение ворот может привести к плохой отделке поверхности, раковинам, пустотам, чрезмерной усадке и деформации.
Замороженный слой — Во время заполнения формы, когда расплавленный пластик входит в контакт с периметром любого охлаждаемого канала (литника, желоба, затвора и полости для формования детали), образуется замороженный слой.Первоначально замороженная корка образуется почти мгновенно, и ее толщина будет динамически изменяться на всех этапах заполнения и упаковки формы в цикле формования. Во время заполнения формы на толщину в значительной степени влияет скорость сдвига и давление заполнения.
Сверхкомпактные вспомогательные устройства впрыска и взлома
Vector Injection — все еще новое имя для большинства формовщиков в США, хотя фирма была основана пять лет назад в Актоне, Онтарио. , ветераном другой фирмы в Онтарио, Mold Hotrunner Solutions (MHS), которая производит горячеканальные системы и системы микроформования. «Доставка расплава — это ядро нашей деятельности, — говорит президент Vector Injection Эван Гудвин. «Мы используем комбинацию инъекций, экструзии, автоматизации и интеграции роботов для разработки решений для производства индивидуальных деталей».
Он описывает бизнес своей компании как состоящий из трех основных видов деятельности. Самая большая с точки зрения выручки — создание индивидуальных термопластавтоматов, полностью с нуля и воплощение довольно необычных конструкций.Одна система, например, была построена для формования компонентов экстерьера автомобилей. Он устанавливает автоматику на пресс и манипулятор для формования с несколькими инжекционными блоками на одной пресс-форме, прилагая 10 тонн силы на каждое место впрыска.
Второе направление бизнеса работает с производителями пресс-форм над внедрением сервоприводов для слайдов, стержней и других компонентов. «Мы заполняем пробел между производителями форм и специалистами в области автоматизации», — объясняет Гудвин.
Направление деятельности, представляющее интерес для самой широкой аудитории формовщиков, — это линейка устройств вторичного впрыска Vector Injection, которые добавляют возможности многокомпонентности любому обычному прессу.Гудвин говорит, что они на 30% короче и на 50% легче и занимают на 30% меньше места, чем его ближайший конкурент, что позволяет этим монтируемым на пресс-форме элементам вписываться в ограждение формовочной машины. Никакой дополнительной поддержки или подставки не требуется. Например, небольшой блок имеет ширину менее 6 дюймов, а блок среднего размера — всего 6,5 дюйма. «Таким образом, его можно установить очень близко к плите без увеличения высоты прижимной пластины», — отмечает Гудвин. При установке на литейную форму параллельно линии разъема требуется всего 3 дюйма высоты формы для достижения входного отверстия тракта плавления.Устройство сконструировано таким образом, что винт может полностью втягиваться в корпус инжектора, что упрощает установку устройства на форму, которая уже подвешена в прессе. Утверждается, что полностью втянутый винт позволяет легко механически очистить винт, что позволяет очень эффективно менять цвет.
Устройства X-Caliber имеют электрический сервопривод и могут быть установлены вертикально или горизонтально на пресс-форме, параллельно или перпендикулярно линии разъема. Они бывают трех размеров, каждый с возможностью выбора семи размеров поршневого винта, для выстрелов от 1 г до 300 г (0.65 фунтов). Максимальная скорость впрыска составляет от 20 до 280 куб. См / сек. Возможное давление до 40 000 фунтов на квадратный дюйм. Стандартные функции включают в себя механическое запорное сопло, 8-в. отвод сопла и контроллер с 15-дюйм. сенсорный экран и восьмизонное управление задвижкой. Гудвин отмечает, что запорная форсунка устраняет непостоянство контрольных колец и позволяет перекрывать процесс пластификации и открытия формы для более быстрых циклов.
Vector Injection ( vectorinjection.com ) имеет запатентованную конструкцию «раздельного ствола», в которой передние две трети ствола (обычно 25: 1 L / D) постоянно прикреплены к горячеканальной системе. коллектор рядом с центральной линией формы.Такое уменьшение длины потока снижает падение давления, сдвиг и время пребывания материала в горячеканальной системе, объясняет Гудвин.
ОДНО- ИЛИ ДВУХСТУПЕНЧАТЫЙ ВПРЫСК
Установки X-Caliber выпускаются как в поршневом одновинтовом, так и в двухступенчатом исполнении. Двухступенчатые устройства имеют стационарный экструдер для пластификации расплава и второй возвратно-поступательный шнек для впрыска. Во время пластификации контур ПИД регулирует положение винта впрыска для поддержания постоянного противодавления.Механический запорный клапан блокирует поток между экструзионным и нагнетательным цилиндрами. Гудвин отмечает, что он использует инъекционный винт вместо простого поршня, чтобы противодействовать неизбежной небольшой утечке через переднюю часть инжектора. Кроме того, такая конструкция сохраняет преимущество поршневого винта «первым пришел — первым вышел», которое теряется при использовании обычного плунжера.
Vector Injection также предлагает блок микроинжекции X-07, двухступенчатую модель, в которой используется пластифицирующий шнек диаметром 12 или 14 мм, который может вместить гранулы стандартного размера, и шнек для впрыска 0.От 04 до 0,08 мм диам. Размеры выстрелов могут быть от 0,05 до 0,5 г. Максимальный размер впрыска составляет 6 куб. См, а максимальная скорость впрыска — 25 куб. См / сек. Допустимое давление до 35 000 фунтов на квадратный дюйм.
ВПУСКНАЯ ФОРМОВКА
Для особых случаев, когда требуется большая мощность дробления, чем может обеспечить стандартная машина, Vector Injection также предлагает дополнительные устройства защиты от проникновения — установленные в пресс-форме экструдеры с сервоприводом. Один из них, называемый Intruder, представляет собой очень легкий 22-миллиметровый блок 20: 1 с регулятором давления, который может преобразовать любую литьевую машину для совместного впрыска или сэндвич-формования с толстым сердечником между двумя оболочками.
Устройство гораздо большего размера называется BFE. Все еще находящийся в стадии разработки, этот блок имеет большой винт 10: 1 L / D; он может произвести выстрел весом 35 унций, но его длина составляет менее 10 футов. Типичный узел впрыска аналогичной мощности будет более чем в два раза длиннее. BFE был разработан для увеличения производительности инжекционной машины среднего и большого размера и для облегчения совместной инъекции оболочки в ядро больших деталей, возможно, с переработанной смолой в ядре. Как и меньший блок, он устанавливается сбоку от формы.
Литье под давлением: новый узел впрыска с продольным винтом / плунжером
Давние ограничения обычных термопластавтоматов с поршневым шнеком устраняются с помощью новой системы Inject-EX от Md Plastics, Колумбия, Огайо. Этот узел впрыска, который впервые появится на выставке NPE2018 в следующем месяце, может быть оснащен гидравлическим, гибридным или полностью электрическим приводом. Полностью электрическая версия состоит из винта с сервоприводом, соединенного на одной линии с плунжером.Таким образом, винт и плунжер перемещаются вместе, когда весь узел впрыска совершает возвратно-поступательное движение, приводимый в движение двумя серводвигателями и шариковинтовой передачей, установленными с обеих сторон узла.
Как объяснил Майкл Дурина, президент Md Plastics, одна хорошо известная проблема обычных машин для литья под давлением — непостоянный объем впрыска из-за непостоянства закрытия обратного клапана на конце винта в начале впрыска. Другая проблема заключается в том, что по мере того, как шнек втягивается во время восстановления, гранулы испытывают непрерывное изменение L / D, поэтому их воздействие на сдвиг непостоянно, что приводит к изменению вязкости расплава.Этот эффект усугубляется тем фактом, что, когда шнек перемещается вперед во время впрыска, гранулы падают из бункера в пустые лопасти, которые предназначены для заполнения дроби. Эти гранулы не уплотняются эффективно, что создает проблему во время восстановления следующего выстрела из-за добавления сдвига из-за проскальзывания шнека и паузы во времени восстановления.
Система Inject-EX решает вторую проблему, потому что шнек (конструкция компании Posi-Melt) неподвижен по отношению к загрузочной воронке, которая перемещается вперед и назад вместе с остальной частью узла впрыска.Поэтому пластификация каждой гранулы одинакова, как при непрерывной экструзии, говорит Дурина, даже если этот шнек работает прерывисто.
Что касается первой проблемы, то есть обратный клапан в передней части винта, где он переходит к плунжеру, но на самом деле клапан имеет ту же конструкцию, что и в запорных форсунках Mini-Shut от Md Plastics, а не его обратные клапаны. Это тарельчатый клапан, подпружиненный шайбами Бельвилля. Поэтому он немедленно закрывается, когда винт перестает вращаться, а не когда он движется вперед для впрыска.
Расплав, проходящий через клапан, проходит через центр плунжера, пока не достигнет переднего конца, где он накапливает дробь перед плунжером. Для заполнения формы весь узел впрыска движется вперед, опорожняя камеру расплава перед плунжером. Дурина говорит, что это устройство проще и дешевле, чем другие двухступенчатые системы.
Durina построила 20-тонную машину с новым инжектором Чен Хсонг из Гонконга. Это будет лабораторная машина Дурины для дальнейшего тестирования и демонстрации концепции Inject-EX.
Более того, машина Inject-EX будет использовать эксклюзивный датчик температуры расплава и давления Temp-Tek компании Md Plastics (см. Крупный план октября 2015 г.). Один датчик будет встроен в камеру плавления на конце плунжера; другой будет помещен в загрузочный бункер. Первый датчик поможет обеспечить нагнетание постоянной массы пластика, которая является функцией постоянного объема и плотности. Другой предоставит потенциально ценную информацию о температуре гранул, попадающих в шнек, говорит Дурина.
Hi-Tech Mold & Tool, Inc
Это первый из двух видеороликов, посвященных изучению литьевых машин. Первое видео посвящено блоку впрыска.
В нашем списке оборудования указаны как унции полистирола, которые может выдержать каждый узел впрыска или цилиндр литьевой машины, так и пиковое давление впрыска. Унции полистирола очень полезны, так как, если у вас есть объем интересующей вас детали, вы можете определить, достаточно ли велик ствол или узел впрыска, чтобы сделать вашу деталь.Поставщики материалов рекомендуют, чтобы объем детали был не ниже 20% емкости баррелей и не выше 80% емкости баррелей. Если объем детали слишком мал по сравнению с вместимостью бочки, то время пребывания может означать, что материал ухудшается. Если объем детали слишком велик, расплав может плохо перемешаться, и может присутствовать вероятность образования нерасплавленных гранул.
Основными элементами узла впрыска являются цилиндр, шнек, бункер для материала и способ создания давления, гидравлический или электрический.Внутри нагретого ствола находится возвратно-поступательный винт. Винт используется для подачи материала к передней части шнека мимо стопорного кольца. Существуют разные винты для разных смол, но чаще всего подходит винт общего назначения.
Пока винт пластифицирует или принимает следующий выстрел, он вращается и медленно движется назад. К шнеку прилагается противодавление, поэтому материал перед шнеком не имеет воздушных карманов. Материал течет по контрольному кольцу и перед кончиком винта.Когда винт начинает двигаться вперед, чтобы начать заливку этапа, стопорное кольцо предотвращает материал, из протекающих спин и держит это происходит в пресс-форму.
Наконечник сопла и лента нагревателя сопла — это то, что торчит из конца ствола. Поддержание температуры в этой области имеет решающее значение для предотвращения проблем с течением или косметических проблем. Если материал замерзнет в сопле, этот твердый материал вызовет скачки давления впрыска, и вы увидите твердый материал в детали.
Воздушный выстрел всегда делается при запуске и выключении машины.Это просто выброс материала из конца ствола в скважину узла впрыска за неподвижной плитой. Воздушные выстрелы всегда производятся при низком давлении, чтобы не причинить травм.
Следующее видео будет посвящено плитам, которые являются частью машины для литья под давлением, которые удерживают форму закрытой, пока в нее попадает материал.
Двухступенчатый блок открывает новую эру в технологии впрыска.
Двухступенчатый блок управления впрыском (ICU) обеспечивает уровень точности и надежности, недоступный до сих пор для литьевых машин, использующих технологию поршневого винта.Запущенный специалистом по системам пластификации Xaloy на выставке NPE 2003 в июне, он обновляет хорошо известную концепцию непрерывно работающего экструдера, питающего емкость для литья под давлением, который сегодня обычно используется для производства преформ для бутылок из ПЭТ (Husky — самый известный представитель). но мало места за пределами специализированных приложений. Battenfeld использует этот принцип, например, в своей машине для формования микроформовок, а также в высокоточных машинах Sodick Plustech.
Xaloy говорит, что ICU «открывает новую эру в технологии литья под давлением» в широком диапазоне приложений. В наборах для переоборудования процессоров используются существующие приводы блока впрыска, добавляется экструдер, который приводится в действие двигателем, который изначально использовался для вращения шнека впрыска, и добавляется коллектор в передней части блока впрыска. Компания также надеется заинтересовать производителей станков предложением варианта в качестве оригинального оборудования, хотя и признает, что перспективы приобретения в нынешнем экономическом климате невелики.
Отделение интенсивной терапии является продуктом сотрудничества между Xaloy (штаб-квартира в США в Пуласки, штат Вирджиния) и R. Dray Mfg. (Даллас, Техас). Технический дизайн в значительной степени исходит от Dray, а Xaloy заботится о технологии управления. Боб Дрей, ведущий представитель конструкции экструзионных шнеков, говорит, что технологические процессы в литье под давлением практически не продвинулись вперед за 40 лет. «Если у нас есть технология, доступная для экструзии, почему бы нам не использовать ее для инъекций?» он говорит.
Дрей отмечает, что экструдер ICU с высоким (30: 1) соотношением L / D доставляет расплав с постоянной вязкостью, что невозможно с установками с возвратно-поступательным движением шнеков, поскольку эффективное соотношение L / D составляет винт, в лучшем случае менее 25: 1, падает при отступлении винта.Кроме того, конструкция ICU не требует обратного клапана, что является потенциальной причиной изменения дозы от выстрела к выстрелу.
Вместо этого порт подачи от экструдера к вытяжной ванне заблокирован соплом узла впрыска, которое выходит в коллектор. Когда узел впрыска находится в переднем положении, порт открыт, и расплав может вытекать из экструдера перед плунжером, который при отступлении создает противодавление обычным образом. Торпеда в передней части сопла предотвращает попадание расплава в форму.Затем, когда узел впрыска втягивается непосредственно перед тем, как плунжер движется вперед, поток из экструдера прерывается, и поток открывается в форму.
Затем движущийся вперед узел впрыска прикладывает давление уплотнения. Это может быть сделано очень точно из-за узкого поперечного сечения канала перед торпедой, поэтому узел впрыска должен пройти долгий путь, чтобы упаковать небольшое количество материала. Заявленная точность выстрела составляет ± 0,1%.
Xaloy, вероятно, предложит четыре размера с диаметром экструдера от 25 до 60 мм.«Система имеет гораздо лучшую пропускную способность, чем обычный узел впрыска, поэтому нам не нужно согласовывать все диаметры шнеков на сегодняшний день», — говорит технический директор Xaloy Хартмут Янке. Он утверждает, что 100-миллиметровый шнек может сравниться с блоком с экструдером всего лишь с половиной диаметра.
Дрей отмечает, что систему можно легко сконфигурировать для различных вариантов основного процесса литья под давлением, таких как поточное компаундирование, в то время как «совместное впрыскивание — это не проблема».
Янке говорит, что презентации, сделанные компанией для процессоров, были хорошо приняты.