Взаимозаменяемость поршневых колец: насколько это реально?
10.11.2014 / 25.04.2018 • 11107 / 4027 При ремонте двигателей автомобилей различных марок и моделей иногда возникают ситуации, когда нужной детали найти быстро не удается. Как правило, это означает, что нужно делать заказ, — и тогда требуемую деталь можно получить только через 5-12 дней, а то и больше, из-за границы. В некоторых случаях подобный срок может оказаться нежелательным или даже неприемлемым. А есть ли способ найти альтернативные решения?
Оказывается, да, есть. По некоторым моторным деталям прослеживается явная аналогия их основных размеров у двигателей, выпускаемых или выпускавшихся различными фирмами. Например, поршневые кольца различных моделей двигателей в ряде случаев частично или полностью взаимозаменяемы. А это значит, что круг поисков существенно расширяется и вероятность найти нужные кольца значительно увеличивается. Тем более что номенклатура поршневых колец, выпускаемых различными фирмами, если не безгранична, то, по меньшей мере, огромна.
— Радиальная ширина выбранных колец должна соответствовать канавкам поршня, то есть нужно, чтобы глубина канавок не оказалась слишком малой. В подавляющем большинстве случаев компрессионные кольца у различных двигателей имеют очень близкую радиальную ширину и практически всегда подходят, чего нельзя сказать о маслосъемных кольцах.
/a131.gif)
— Определенное значение имеют материалы и покрытие колец. Так, желательно, чтобы у найденных колец покрытие соответствовало оригиналу. Нарушение этого правила может привести к снижению их ресурса, а в некоторых случаях (например, при установке нехромированных колец в алюминиевые цилиндры, не имеющие твердого покрытия) — вообще к неработоспособности колец. Эти вопросы также можно уточнить по каталогам.
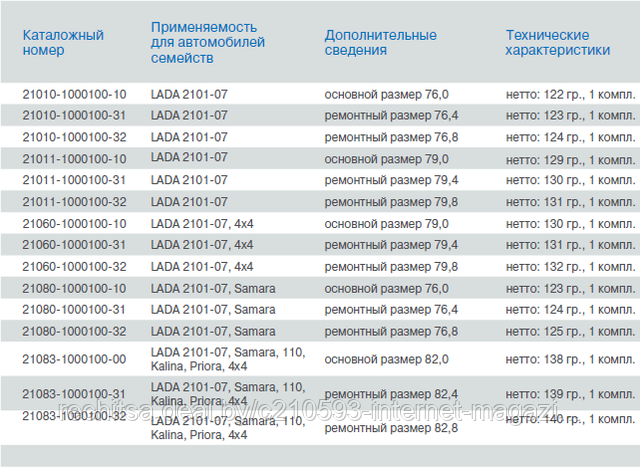
Эта информация может быть уточнена в каталогах фирм-производителей колец. Нецелесообразно также устанавливать на дизель кольца от бензиновых моторов, хотя обратная замена допустима. Во всех случаях очень желательно, чтобы двигатель, кольца от которого использовались, имел примерно те же основные параметры, что и двигатель, на который эти кольца установлены. Речь идет в первую очередь об удельной (так называемой литровой) мощности и максимальной частоте вращения, определяющих степень форсирования двигателя. Очевидно, кольца от «тихоходного» мотора выпуска 20-30 летней давности вряд ли подойдут к современному многоклапанному двигателю с наддувом — не те окажутся материалы покрытия, да и требования к геометрии колец могут быть разными. Так что эти факторы следует учитывать при подборе колец, когда нет точных каталожных данных по их материалу и покрытию. Но, в любом случае, кольца от более новых моделей при соответствии размеров подойдут к более старым. Если найденные кольца удовлетворяют всем перечисленным выше условиям, ходить они будут ничуть не меньше штатных.

цилиндра, мм | колец, мм | ||||
73.![]() | 1.5-1.5-4.0 2.0-2.0-4.0 | Nissan/E10 Mazda/TC | Toyota/2E Nissan/A10, A12 | Toyota/1A, 2A | |
74.0 | 1.5-1.5-4.0 | Honda/EV, EW | Mitsubishi/4G12 | ||
75.0 75.5 | 1.5-1.5-4.0 1.5-1.5-4.0 | Honda/D13, D15, D16 Mitsubishi/4G15 | Opel/1,3I +0.5 Honda/D13, D15 | Toyota/1G, 4K 0.5 Opel/13I | 0.5 Toyota/1G, 4K |
76.0 | 1.5-1.5-4.0 1.5-1.5-2.8 | NIssan/E13, E15, E16 Diahatsu/CB | Nissan/GA16 | 0.![]() | |
77.0 78.0 | 1.5-1.5-4.0 1.5-1.5-4.0 | Honda/EP, EK Mazda/NA, VB | Mazda/UC Nissan/CA16 | ||
80.0 80.5 | 1.75-2.0-3.0 1.5-1.5-4.0 2.0-2.0-4.0 | Nissan/CD17 Mitsubishi/4G37, 4G62 Mitsubishi/4D56 | 0.5 VW/1X, 1Y Toyota/1S Toyota/12R | ||
81.0 82.0 | 1.5-1.5-4.0 1.5-1.5-4.0 | Honda/B18, B20 Ford(US)/114 | Mazda/F6 General Motors/97, 98 | +0.5 Mitsubishi/4G37, 4G62 | +0.![]() |
83.0 | 1.5-1.5-4.0 2.0-2.0-4.0 | Nissan/CA18 Nissan/L16,Z16, L24 | Peugeot/XU5 Toyota/5M до 1982 г. | Toyota/5M, 7M | |
84.0 | 1.5-1.5-4.0 1.5-2.0-4.0 2.0-2.0-4.0 | Toyota/4A, 21R BMW/M20 Isuzu/G180,4ZB1 | Toyota/21R-U Mitsubishi/4G52 | Toyota/1C | |
84.5 85.0 | 2.0-2.0-4.0 1.5-1.5-4.0 2.0-2.0-4.0 | Nissan/CA20,
LD28 Mitsubishi/4G63 Mitsubishi/4G63 до 1985 г. | +0.5 Isuzu/G180, 4ZB1 Nissan/Z20 Nissan/L18, LD20 | +0.![]() Toyota 3T, 3T | +0.5 Toyota 1C |
86.0 86.05 | 1.5-1.5-4.0 2.0-2.0-4.0 2.0-2.0-.4.0 | Mazda/F8, FE, F2 Mazda/RF, R2 Opel/20D | Nissan/SR20 Nissan/2C, L28 +0.5 Mazda/RF, R2 | Toyota/1Y, 2Y, 3Y, 3S +0.5 Nissan/2C, L28 | |
87.5 88.0 | 1.5-1.5-4.0 1.5-1.5-4.0 | Crysler/135, 153 General Motors/258V8 | Toyota/3VZ Isuzu/4ZC1 | +0.5 Toyota/5S | |
89.0 92.0 | 1.5-1.5-4.0 1.5-1.5-4.0 2.0-2.0-4.0 | Ford(US)/183V6 General Motors/273V8 Opel/23D | General Motors/173V6 Subaru/EA71 Subaru/EA71 до 1982 г. ![]() | Isuzu/4ZD1 Volvo/B21 |
Поршневые кольца — как правильно выбрать и заменить
Поршневые кольца — одна из основных деталей цилиндро-поршневой группы двигателя автомобиля. Представляют собой кольца разъемного типа, устанавливаемые на поршни. Обеспечивают герметизацию камеры сгорания, сокращают объем отработанных газов, поступающих в картер, расход масла.
Для чего нужны поршневые кольца
Чтобы обеспечить оптимальные условия для воспламенения топлива, для двигателей внутреннего сгорания крайне важно создать избыточное давление в камере внутреннего сгорания на этапе завершения такта сжатия. Этот показатель называется компрессией.
Для нормальной работы бензиновых двигателей этот величина компрессии должна составлять 9–12 атмосфер, в дизельных силовых установках значение еще выше и достигает 22-32 атмосферы. Чтобы получить такие показатели, важно качественно загерметизировать камеру сгорания на этом этапе работы ДВС. Данную задачу и выполняют поршневые кольца.
1 — поршень; 2 — верхнее компрессионное кольцо; 3 — второе компрессионное кольцо; 4 — маслосъемное кольцо; 5 — поршневой палец; 6 — стопорные кольца
Основные функции поршневых колец
Помимо обеспечения герметизации эти детали двигателя выполняют следующие функции:
- За счет сокращения площади соприкосновения со стенками цилиндра уменьшают силу трения, что способствует сокращению потерь энергии и предотвращению преждевременного износа основных деталей поршнево-цилиндровой группы.
- Предотвращение влияние температурного расширения деталей, сделанных из различных материалов. Для производства поршней и цилиндров применяют сплавы с отличающимся коэффициентом расширения. Установка колец позволяет избежать заклинивание поршней при чрезмерном нагреве. Дополнительно это решение позволяет поддерживать стабильный уровень компрессии при значительных изменениях температуры.
- Маслосъемные поршневые кольца удаляют излишки масла со стенок цилиндра, что позволяет обеспечить оптимальную смазку деталей без чрезмерного расхода смазывающей жидкости.
Отметим, что установка колец позволяет обеспечить частичное охлаждение поршня, отводя тепловую энергию в стенки цилиндра. Такое решение увеличивает срок службы основных деталей.
Причины и последствия износа поршневых колец
При работе ДВС поршневые кольца подвергаются значительной тепловой и механической нагрузке. Нагрев и трение приводят к постепенному износу этих деталей. В результате уменьшается степень герметизации, часть рабочих газов попадает в картер, а не выполняет эффективную работу. Износ колец приводит и к проникновению в камеру сгорания масла, которое изменяет состав топливовоздушной смеси, ухудшая ее воспламеняемость. Значительной проблемой считают и образование нагара на поверхности колец и поршней, что приводит к закоксовке и заклиниванию.
В результате воздействия этих факторов происходит существенное снижение мощности ДВС, увеличивается расход топлива, возрастает опасность выхода из строя деталей поршнево-цилиндровой группы. Устранение последствий заклинивания может потребовать проведение дорогого капитального ремонта.
При обнаружении признаков износа поршневых колец необходимо провести диагностику и замену деталей, отработавших свой ресурс.
Правила выбора и замены поршневых колец
Для замены выбирают только кольца, соответствующие двигателю по каталожному номеру и типу. Если проводилась расточка цилиндровых гильз, необходима установка ремонтных колец с увеличенным размером.
Общая схема работ по замене:
- Все операции выполняют только в соответствии с рекомендациями и инструкциями производителя.
- Для установки используют специальную оправку, прижимающую кольца к поверхности поршня.
- После демонтажа старых деталей тщательно очищают канавки от нагара.
- При установке новых колец важно соблюдать расположение верхних и нижних меток.
- Замки новых поршневых колец должны быть смещены относительно друг друга, не допускается расположение на линии крепежного поршневого пальца. Это необходимо для повышения степени герметизации.
- После монтажа проверяются все нормативные зазоры, величина которых должна соответствовать установленным значениям.
В обязательном порядке проводят обкатку двигателя после замены поршневых колец. Первая тысяча километров пробега осуществляется при работе ДВС в щадящем режиме при нагрузке не более 50% от нормативной. При правильной замене удается полностью восстановить мощность и другие характеристики двигателя.
Вернуться к списку статей
Performance Piston Rings — журнал Engine Builder Magazine
Какие поршневые кольца следует использовать при сборке высокопроизводительного двигателя? Кольца варьируются от чугуна до ковкого чугуна и стали, с различными размерами, профилями кромок и износостойкими покрытиями. Есть много доступных вариантов и много вопросов, на которые нужно ответить. Некоторые комплекты поршней поставляются с кольцами, а другие нет, поэтому выбор остается за вами.
Тип колец, которые являются «лучшими» для любого конкретного двигателя, будет зависеть от ожидаемой мощности двигателя, типа топлива, которое он будет использовать, а также от условий гонок или производительности, в которых он будет работать.
Двигатель, созданный для использования в уличных условиях, не будет подвергаться таким же нагрузкам и условиям, как двигатель, предназначенный для работы на грунтовой дороге, полосе для дрэга или в лодке. Какой бы тип колец вы ни выбрали, они должны обеспечивать наилучшее сочетание контроля герметичности, долговечности, термостойкости и маслоотделения.
Материалы колец
Вообще говоря, стальные поршневые кольца более долговечны, чем кольца из ковкого чугуна, а кольца из ковкого чугуна более долговечны, чем кольца из чугуна. В течение последнего десятилетия большинство серийных двигателей оснащались на заводе стальными верхними компрессионными кольцами, чтобы выдерживать более высокие рабочие температуры и нагрузки современных двигателей с более высокой мощностью.
Тем не менее, многие двигатели драгстеров Top Fuel по-прежнему используют кольца из ковкого чугуна с плазменно-молибденовым покрытием. Почему? Потому что кольца из молибдена обеспечивают уплотнение и смазку, необходимые в этой чрезвычайно сложной области применения. Конечно, кольца меняются после каждого запуска, что нецелесообразно для большинства других типов двигателей.
Кольца с молибденовым покрытием из ковкого чугуна по-прежнему являются лучшим выбором для многих традиционных типов дорожных и полосовых двигателей. Они являются наиболее экономичным выбором для типичных безнаддувных двигателей SB/BB Chevy или Ford и могут безопасно выдерживать компрессионные нагрузки до двух лошадиных сил на кубический дюйм.
Добавки мощности, такие как закись азота, турбокомпрессор или нагнетатель, значительно увеличивают тепловую нагрузку в камере сгорания, что также увеличивает риск детонации, повреждающей кольца. Для двигателей с более высокими выходными характеристиками настоятельно рекомендуется переход на более прочное стальное кольцо.
Серый чугун — хрупкий материал с очень низкой прочностью на растяжение по сравнению с ковким чугуном или сталью. Кольца из чугуна дешевле, чем кольца из ковкого чугуна или стали, и идеально подходят для двигателей с умеренными характеристиками. Но по мере увеличения выходной мощности двигателя чугунные кольца вскоре достигают своего предела.
Ковкий чугун — это прочный материал для колец, который уже много лет используется как в высокопроизводительных двигателях, так и в дизельных двигателях. Таким образом, кольца из ковкого чугуна являются хорошей модернизацией по сравнению с кольцами из серого чугуна в двигателях с более высокой мощностью. Однако стальные кольца могут обеспечить повышение прочности на растяжение и усталостной прочности на 20 и более процентов по сравнению с ковким чугуном.
Одной из причин, по которой все больше и больше колец в настоящее время изготавливают из стали, является более узкая лицевая сторона, которая сейчас используется во многих комплектах колец (как для оригинального оборудования, так и для вторичного рынка). Более тонкие кольца с низким натяжением уменьшают трение и лучше прилегают к стенке цилиндра. Следовательно, они обеспечивают лучшую герметизацию и меньшее количество газов.
Традиционный 5/16? компрессионное кольцо может создавать натяжение от 7 до 8 фунтов по сравнению с натяжением в полфунта в компрессионном кольце диаметром 0,7 мм в двигателе NASCAR. Это значительное снижение трения и сопротивления. Но для этого также требуется более прочный и долговечный материал кольца.
По словам одного поставщика колец, с которым мы беседовали, существует два основных типа стальных колец, которые производятся для вторичного рынка. Одним из них является углеродистая сталь, которая используется в комплектах колец как для высокопроизводительных двигателей, так и для комплектов замены OEM последних моделей. Он на 35 процентов прочнее серого чугуна, может быть покрыт молибденом, хромирован или работать без покрытия в канале ствола.
Другой тип стали — нержавеющая сталь, которая является предпочтительным материалом для беговых колец NASCAR, NHRA Pro Stock и других высокотехнологичных приложений толщиной всего 0,7 мм. Кольца из нержавеющей стали не могут работать в отверстии из чугуна без какой-либо обработки поверхности, такой как газовое азотирование или PVD (физическое осаждение из паровой фазы) со сплавом титана или хрома.
Кольцевые покрытия
Доступны кольца без покрытия (гладкие), с молибденовым покрытием или с некоторым типом обработки поверхности методом PVD (титан, хром или керамика). Нитрид титана является очень популярной обработкой поверхности высокопроизводительных стальных колец в гоночных двигателях высокого класса, поскольку он снижает трение и повышает износостойкость. Обработка колец нитридом хрома предлагает многие из тех же преимуществ и, как правило, более популярна для двигателей с дорожными характеристиками и даже для многих серийных двигателей.
Нитрид хрома также является популярным покрытием для колец, которые устанавливаются в двигатели для внедорожных гонок, поскольку грязь не прилипает к хрому и не царапает цилиндры. Но, как указал другой поставщик колец, молибденовые кольца так же хорошо работают в двигателях для бездорожья, при условии, что двигатель имеет хорошую фильтрацию воздуха, предотвращающую попадание грязи.
Хромированные азотированные кольца с PVD-покрытием отличаются от традиционных хромированных колец. Обработка поверхности азотированных хромированных колец методом PVD очень хорошо прилипает к кольцу и не трескается и не отслаивается, как хромированные кольца с гальваническим покрытием, в неблагоприятных условиях эксплуатации. Хромированные кольца существуют со времен Второй мировой войны и изготавливаются путем гальванопокрытия хрома на поверхности кольца.
Хромированные кольца стали популярным выбором для внедорожных и внедорожных двигателей из-за их способности противостоять истиранию, вызванному переносимыми по воздуху загрязняющими веществами. Однако хромированные кольца имеют примерно на 1000 градусов по Фаренгейту меньшую устойчивость к истиранию, чем кольца с молибденовым покрытием. Поскольку нагрев является основным фактором почти для любого применения, молибден является предпочтительным покрытием поверхности кольца в течение многих лет.
Молибденовые кольца обычно прирабатываются быстрее, чем хромированные, быстрее достигают полной герметизирующей способности и обеспечивают значительно более высокую стойкость к истиранию. Некоторые поставщики колец улучшают стойкость молибденового покрытия к истиранию, комбинируя его с никель-хромовым сплавом (что увеличивает срок службы поверхности на 65 процентов по сравнению с обычными кольцами с молибденовым покрытием).
Единственным недостатком молибдена является то, что материал облицовки может быть поврежден сильной детонацией двигателя, и он может быть несовместим с некоторыми покрытиями канала ствола, такими как сплавы на основе никеля/карбида или алюминия. Для таких применений правильным выбором будет стальное кольцо с PVD-покрытием. Некоторые поставщики колец также не рекомендуют использовать молибденовые кольца в двигателях, в которых топливо на спиртовой основе используется в течение длительного периода времени.
Профили колец
Поршневые кольца доступны со всеми видами профилей кромок, включая квадратную поверхность, коническую поверхность, центральный цилиндр, смещенный цилиндр и ленточный профиль. Верхнее компрессионное кольцо обычно имеет бочкообразную поверхность, а второе кольцо часто представляет собой кольцо с конусной или тонкой поверхностью. Причина использования различных профилей заключается в том, чтобы оптимизировать производительность кольца для работы, которую оно должно выполнять.
Верхнее кольцо в первую очередь является компрессионным уплотнительным кольцом. Его единственная задача — герметизировать камеру сгорания и предотвратить прорыв газов. Верхнее кольцо принимает на себя основную нагрузку тепла и сжатия, поэтому оно должно быть прочным и долговечным.
Верхнее компрессионное кольцо с цилиндрической поверхностью обычно обеспечивает наилучшее сочетание уплотняющей способности и износостойкости. Кольцо с квадратной поверхностью хорошо уплотняется, но в конечном итоге из-за изгиба кольца при движении поршня вверх и вниз приобретает бочкообразный профиль. Придание кольцу бочкообразного профиля снижает износ кольца и продлевает срок его службы.
Работа второго кольца обычно заключается в контроле масла на 80–90 % и герметизации на 10–20 %. Второе компрессионное кольцо дублирует верхнее компрессионное кольцо с точки зрения уплотнения, но в основном действует как маслосъемное. На поверхность второго кольца нанесен небольшой конус (от 2 до 4 градусов), чтобы оно соскребало масло со стенки цилиндра при движении поршня вниз.
Подрезание нижней кромки поверхности 2-го кольца для создания канавки (канавка крюка или профиль скребка) еще больше улучшает маслосъемную способность кольца, особенно в двигателях без наддува. Канавка также обеспечивает разгрузку под поверхностью кольца для отвода картерных газов. Из-за этого второе кольцо типа Napier обычно является лучшим выбором для контроля масла.
Важно отметить, что второе кольцо, очевидно, является направляющим кольцом и должно быть установлено правильной стороной вверх, иначе оно будет перекачивать масло в неправильном направлении и увеличит расход масла.
Для двигателей, работающих на летучем топливе, таком как нитрометан, и двигателей, работающих на большом наддуве, таких как выдыхаемый спирт и дизельные тягачи для грузовиков и тракторов, вторые кольца типа Napier НЕ являются лучшим выбором. Двигатели этого типа работают с таким высоким давлением в цилиндре, что второе кольцо вынуждено справляться с прорывом газов под гораздо большим давлением.
Следовательно, многие двигатели, работающие на выдувном спирте, используют второе кольцо из ковкого чугуна в стиле обратной закрутки или используют верхнее кольцо во второй канавке поршня. Некоторые также используют кольцо в стиле Дайкса с кольцом из ковкого чугуна с плазменной молибденовой поверхностью во второй канавке.
Третье кольцо представляет собой маслосъемное кольцо, обычно состоящее из трех частей и состоящее из пары тонких маслонаправляющих трубок из хромированной или азотированной стали, поддерживаемых расширителем. Преимущества конструкции из трех частей: низкая стоимость, хорошая совместимость с отверстием цилиндра, простота установки и возможность производителя колец изменять натяжение маслосъемных колец по мере необходимости.
Трехкомпонентная конструкция широко используется как в оригинальных, так и в высокопроизводительных кольцах. По общему мнению, традиционная конструкция маслосъемного кольца из трех частей отлично работает, так зачем с ней возиться? Маслосъемное кольцо, состоящее из трех частей, обеспечивает хороший обратный слив масла, хорошее боковое уплотнение масляной канавки и позволяет двум направляющим плотно прилегать к отверстию цилиндра независимо друг от друга, чего не может сделать цельное маслосъемное кольцо. Маслосъемное кольцо, состоящее из трех частей, также имеет меньшую массу, что снижает силы инерции и повышает стабильность кольца, особенно при более высоких оборотах двигателя.
Цельные маслосъемные кольца используются во многих дизельных двигателях с низкой частотой вращения и в некоторых европейских бензиновых двигателях, но они относительно редко используются здесь для повышения производительности. Однако они существуют и успешно используются в различных двигателях F-1, NASCAR и NHRA Pro Stock.
Цельные маслосъемные кольца доступны по специальному заказу, они очень дороги и сильно отличаются от традиционных маслосъемных колец из трех частей. Но у них есть свои преимущества. По словам одного поставщика этих колец, их цельное маслосъемное кольцо диаметром 4,180? отверстие цилиндра с 1,5-миллиметровой канавкой для масляного кольца в поршне оказывает нагрузку всего около 10 ньютонов на отверстие цилиндра.
Конечно, обычные маслосъемные кольца из трех частей также стали тоньше, чтобы уменьшить натяжение и трение. Традиционная тройка, 3/16? толстое масляное кольцо, которое раньше создавало 20 фунтов. натяжения теперь заменено меньшими и более тонкими маслосъемными кольцами из трех частей, которые создают натяжение всего от 3 до 4 фунтов. Меньшее натяжение означает меньшее трение и большую мощность.
Зазоры колец
Независимо от того, какой тип колец вы выберете для двигателя, зазоры концов колец должны соответствовать применению. Чем больше мощность двигателя, тем больше тепла он выделяет в камере сгорания и тем больше расширяется верхнее кольцо в ответ на все это тепло.
По мере расширения кольца расстояние между концами кольца в кольцевом зазоре сужается. Надеюсь, зазора достаточно, чтобы концы кольца не вытягивались слишком сильно и не упирались друг в друга, вызывая истирание кольца.
Двигатели с добавками мощности, такими как закись азота, турбонагнетатель или нагнетатель, очевидно, нагревают камеру сгорания больше, чем большинство безнаддувных двигателей, поэтому при установке колец требуется больший зазор в концевом зазоре.
Эмпирическое правило для верхнего компрессионного кольца: 0,0045? концевого зазора на дюйм диаметра отверстия для двигателя без наддува и 0,006? для приложения сумматора мощности. Более того, многие поставщики колец рекомендуют открывать второе кольцо .005? до 0,010? больше, чем зазор верхнего кольца в двигателях без наддува, чтобы предотвратить скопление газа между верхним и вторым кольцами.
Это может привести к тому, что верхнее кольцо будет трепетать или подпрыгивать, что приведет к потере герметичности. Но в форсированном двигателе второе кольцо подвергается большему воздействию газов и должно иметь такой же зазор, как и верхнее кольцо.
Производители поршневых колец публикуют рекомендации по концевым зазорам в своих каталогах и на своих веб-сайтах. Всегда обращайтесь к этим рекомендациям, так как они будут варьироваться от одного производителя к другому в зависимости от типа используемых колец, из чего они сделаны (чугун имеет более высокую степень теплового расширения, чем сталь) и области применения.
Заключительные мысли о выборе кольца
Хотя на эту тему написаны книги, мы можем свести ее к следующим пунктам:
1) Каков общий бюджет вашего двигателя и какой процент вы тратите на кольца? Например, если вы покупаете набор экзотических цельных маслосъемных колец, которые стоят почти 600 долларов для V8, одни только кольца могут стоить больше, чем поршни! Такие дорогие затраты на комплект колец не имели бы особого смысла для типичного уличного двигателя, но могут быть оправданы для двигателя Pro Stock с высокой стоимостью.
2) Вы строите безнаддувный двигатель или тот, который будет максимально разогнан закисью азота, турбонагнетателем или вентилятором? Чем выше выходная мощность, тем прочнее материал кольца, который потребуется, чтобы выдерживать тепло и давление.
3) Как будет использоваться двигатель? Драг-рейсинг, буксировка грузовиков, кольцевая трасса, морской транспорт, движение по улицам и т. д. Если приложение представляет собой двигатель с уличными характеристиками, сколько времени он реально проведет на полном газу? Выберите кольцевую облицовку, обеспечивающую такую долговечность, которая соответствует области применения.
4) Как часто будет обновляться двигатель? Должны ли кольца прослужить десятки тысяч километров (как на улице) или их будут менять каждый сезон?
5) Какие типы колец используются в аналогичных целях? Если определенный тип кольца или облицовочного материала отлично подходит для всех остальных, попытка быть первопроходцем может оказаться дорогостоящей!
6) Какие типы колец доступны для диаметра цилиндра двигателя и конфигурации поршня? Для некоторых применений (например, двигателей с необычно большим диаметром цилиндра или чрезвычайно короткими легкими поршнями) это может немного ограничить ваши возможности.
Мы благодарим следующих поставщиков колец за их вклад в эту статью: Federal Mogul/Sealed Power, Hastings, MAHLE, NPR и Total Seal.
Распечатать
Вам может понравиться
Кольца круглого сечения? О да! Как выбрать, спроектировать и установить уплотнительные кольца — Tarkka
Кольцевые уплотнения являются воплощением элегантной инженерной мысли: Кольцо стоит всего несколько центов, а канавка, в которую он входит, проста и легка в использовании. производство. Но несмотря на эту простоту, полученное уплотнение способно надежно выдерживают давление в несколько тысяч фунтов на квадратный дюйм. Уплотнительные кольца определенно являются конструкцией машины компонент, с которым вы захотите познакомиться, и в этом видео мы собираемся рассказать вам все о том, как проектировать уплотнения с ними.
Уплотнительное кольцо образует уплотнение, когда его сжимают между двумя
прилегающие поверхности. Когда кольцо сжимается, контактное напряжение между уплотнительным кольцом
и появляются поверхности. Если давление жидкости ниже контактного
напряжение, тогда уплотнение предотвращает утечку жидкости. В общем, как
давление жидкости увеличивается, уплотнительное кольцо еще сильнее сжимается в
канавка, еще больше увеличивая контактное давление и, следовательно, помогая уплотнительному кольцу
герметизировать еще лучше. Эта петля положительной обратной связи по увеличению давления приводит к
повышенная герметизация называется «самоподпиткой».
Уплотнения обычно можно классифицировать как статические или динамичный. Этот гидравлический цилиндр имеет примеры обоих. Уплотнения между цилиндр и торцевая крышка, сальник и торцевая крышка, поршень и шток являются статическими уплотнениями, так как эти компоненты не перемещаются друг относительно друга после сборки цилиндра. Уплотнение между поршнем и цилиндром, а шток и торцевая крышка являются динамическими уплотнениями, так как эти компоненты скользят при срабатывании цилиндра.
Наиболее распространенным типом уплотнения является радиальное уплотнение, которое может
оформлен одним из двух способов. Если канавка находится на внутреннем диаметре корпуса, это
называется штоковым уплотнением. Если канавка находится на наружном диаметре вала, то это
уплотнение поршня. Если у вас есть выбор между уплотнением штока и поршня, лучше
используйте поршневое уплотнение, потому что канавки намного легче обрабатывать и
осмотреть.
Самая большая слабость радиальных кольцевых уплотнений заключается в том, что зазор между компонентами создает путь для выдавливания уплотнительного кольца из-за давление, действующее на него. Компоненты, называемые резервными кольцами, могут помочь этот. Опорные кольца сконструированы таким образом, чтобы выпрыгивать из сальника и блокировать экструзионный зазор. Там, где одно уплотнительное кольцо могло выдержать, возможно, только 2000 фунтов на квадратный дюйм, резервное кольцо может помочь вместить 5000 и более.
Опорные кольца очень дешевы и эффективны. Они сделаны из
пластик, такой как PEEK или тефлон, и у них обычно есть косой вырез, чтобы помочь вам
установить их в сальник. С технической точки зрения, если бы у вас было только давление в
в одном направлении, можно было обойтись только одним резервным кольцом. Однако это очень
легко вставить кольцо не с той стороны, так как дизайн для сборки
меры предосторожности, при проектировании с опорными кольцами всегда следует проектировать для двух.
Другая конфигурация — это лицевое уплотнение, которое вы можете использовать при попытке герметизировать корпус. Это действительно тип прокладки, и они требуется зажимное усилие, обычно обеспечиваемое крепежными деталями, для сжатия уплотнительного кольца. Лицевые уплотнения на самом деле очень сложно сделать правильно, потому что сжатие Уплотнительное кольцо требует большого давления. Этот первый дизайн крышки слишком тонкая, а посередине практически не продавливается уплотнительное кольцо, а значит без герметизации. Мы можем исправить эту конструкцию, добавив губу по периметру.
Третий тип конструкции — уплотнение бобышки. Вы в значительной степени только
видеть их на гидравлической арматуре, но у них есть масса преимуществ для других
Приложения. В этой конфигурации уплотнительное кольцо находится в треугольном пространстве, которое
обычно изготавливается с помощью специального инструмента формы. Уплотнения бобышки очень просты в изготовлении,
так как подрезов нет, и при повреждении железы их можно
переработано, просто обработав профиль немного глубже.
Независимо от конструкции сальника, которую вы выберете, вы, скорее всего, необходимо выбрать готовое уплотнительное кольцо из каталога. Уплотнительные кольца доступны в стандартизированные размеры. Наиболее распространенным стандартом является AS568, и каждый размер присвоили номер «тире».
Уплотнительные кольца, соответствующие этим размерам, доступны во многих разные материалы. Основным критерием выбора материала является рабочей жидкости и температуры. Дизайнерские столы, как этот в Parker Справочник по уплотнительным кольцам — это самый простой способ выбрать подходящий материал. для вашего приложения.
Один и тот же материал часто доступен в различных вариантах
твердость. Твердость обычно выражается твердостью по дюрометру. 70
является довольно типичной твердостью и хороша для большинства применений. 55 дюрометр это много
мягче и является хорошим выбором для давлений ниже, может быть, 1000 фунтов на квадратный дюйм, потому что это
проще в установке и менее чувствителен к чистоте поверхности.
90 Дюрометр чрезвычайно твердый и, следовательно, более устойчивы к экструзии. Для более высоких давлений, превышающих, возможно, 6000 фунтов на квадратный дюйм, вам определенно хочу рассмотреть возможность использования дюрометра 90.
Однако лучшие характеристики при высоком давлении цена. Уплотнительные кольца твердостью 90 могут быть очень сложными в установке, особенно в маленькие размеры. Хороший совет — опустить их в горячую воду на несколько минут, чтобы они их размягчить. Их установка будет несколько проще.
Еще один важный совет по установке – нанесите
качественная смазка уплотнительных колец перед сборкой деталей. В дополнение к
смазывая резину и помогая ей легче скользить, большинство смазок для уплотнительных колец
предназначен для того, чтобы уплотнительное кольцо слегка набухало, помогая увеличить сжатие после
монтаж.
При сборке компонентов необходимо сжать Уплотнительное кольцо совсем немного для создания уплотнения. Это помогает иметь малый угол входа около 15 градусов. Эта поверхность должна быть абсолютно гладкой и без заусенцев. чтобы кольцо случайно не порезалось.
Чистота поверхности компонентов чрезвычайно важна. Как по общему правилу сторона сальника и отверстие или шток должны иметь 32 среднеквадратичных значения. отделка поверхности статических уплотнений. Стенки железы могут быть слегка грубее, на 64. Вот где действительно сияет уплотнение поршня, так как оно как правило, труднее проверить размеры и отделку уплотнения штока железа.
В динамическом приложении уплотнительные кольца могут работать, но
лучше рассмотреть варианты. Это называется Т-образным уплотнением, и они специально
предназначен для динамических приложений. Они упакованы с двумя резервными кольцами в качестве
блок, и их основное преимущество заключается в том, что они имеют широкое плоское дно, чтобы держать
чтобы они не катались в канавке. Они не намного дороже уплотнительных колец,
и, по нашему опыту, очень надежны в динамических приложениях.
До сих пор мы не упоминали, где размеры для компонентов. Есть три параметра уплотнения, которые будут определять размеры: сжатие, растяжение и процент заполнения железы.
Сжатие — это насколько сильно вы радиально сжимаете уплотнительное кольцо, когда он установлен в железе. В общем, подходит 18-25-процентное сжатие. для большинства статических уплотнений, но иногда используется до 30 процентов, особенно для применения в холодных условиях.
Растяжение соответствует тому, насколько уплотнительное кольцо сдвинуто по касательной
растягивается ПОСЛЕ установки в канавку. Это не обязательно делать напрямую
с тем, насколько вы растянете уплотнительное кольцо при установке, правда с небольшим
размеров колец, монтажная натяжка создает другие проблемы. Растяжка должна
быть ниже 5 процентов, потому что высокие значения растяжения приводят к тому, что поперечное сечение
становятся меньше, уменьшая сжатие.
Объемное заполнение сальника является последним параметром. уплотнительное кольцо и резервные кольца несжимаемы, и если у вас недостаточно места, вы не быть в состоянии собрать компоненты, потому что не будет места для уплотнительного кольца идти. Вы также должны следить за тепловым расширением, потому что уплотнительное кольцо будет становиться больше с температурой, и это может фактически раздавить металл компоненты и уступайте их, если у вас недостаточно места. Хорошим ориентиром является поддерживать заполнение сальника ниже 85%.
Хотя вы можете использовать эти уравнения для самостоятельного расчета размеров сальника, существует источник предварительно рассчитанных значений, который называется Справочник по уплотнительным кольцам Parker.
Если у вас не очень необычное или требовательное приложение, рекомендации, которые мы вам дали, и таблицы, опубликованные Parker, должны позволить вам с уверенностью проектировать надежные соединения с уплотнительными кольцами.