Ремонтные размеры коленвалов для продления их службы + видео » АвтоНоватор
Коленчатый вал изготавливается либо из чугуна, либо из легированной стали, оба материала довольно прочные, но дефекты все же со временем возникают, и как раз для их устранения нужны ремонтные размеры коленвалов. Это своеобразные допуски, до которых можно уменьшить толщину шеек без сильного ущерба для прочности детали. И, поскольку шейки обычно взаимодействуют с подшипниками, для последних предусмотрены вкладыши с ремонтным уменьшением.
Когда могут потребоваться ремонтные размеры коленвалов?
Прежде всего, давайте рассмотрим различные виды возникающих дефектов, а также причины их появления. Если нарушена геометрия посадочных мест под опорные подшипники блока, следует ожидать быстрого износа шеек. Иными словами, если наблюдается данный процесс, причина, скорее всего, именно та, что указана выше, либо в некачественном материале самого вала. Из-за некачественного масла или нерегулярной его замены на шейках могут появиться задиры, также источником данной неприятности может стать засорившийся масляный фильтр, либо, что совсем уже плохо – слабое давление в системе.
Но наиболее частый вид повреждений – царапины на шейках (не путайте их с трещинами из-за усталости металла, при появлении которых приходится менять деталь). Возникают такие дефекты из-за продолжительной эксплуатации вала, кроме того, причина может крыться в засорении масла инородными частицами. При этом обращайте внимание на глубину царапин, мелкие, до 5 микрон, могут быть заполированы, а вот более значительные требуют шлифовки, в результате чего приходится переходить на следующие ремонтные размеры коленвалов. Иногда, при сильном износе поверхности, деталь уменьшается сразу на 2 размера.
Что следует учитывать, изменяя размеры шеек коленвалов?
Шейки у коленчатого вала бывают двух типов – опорные и шатунные. Последние, как ясно из названия, предназначены для того, чтобы на колена передавались поступательные движения шатуна, преображаясь, таким образом, в крутящий момент. По сути, получается принцип колодезного ворота, точнее, его изогнутой ручки, по отношению к которой человеческое предплечье может считаться шатуном. В стандартном двигателе размеры шеек коленвалов соответствуют 47.8 миллиметрам. Логично, что и подшипники, и кольца шатунов также подогнаны под этот размер. Однако спортивный тип коленвалов является исключением, у него шейки имеют диаметр всего 43 миллиметра, а значит, он требует специальных вкладышей для подшипников и установку соответствующих шатунов.
Но вернемся к шейкам и их дефектам. При наличии таковых ремонт может осуществляться до 4 раз путем шлифовки, как уже было сказано выше. Соответственно, прежде чем изменять ремонтные размеры шеек коленчатых валов, внимательно замерьте деталь и выясните, до какой степени могут произойти ее изменения, после чего заранее приобретите вкладыши с новыми размерами. Определить степень износа можно по зазору между шейкой и подшипником, который, достигая 0.07-0.09 миллиметров, грозит снижением давления масла и шумами во время работы ДВС, а будучи менее 0. 03 миллиметра может стать причиной описанных выше задиров.
Какие бывают ремонтные размеры шеек коленчатого вала?
Собравшись отшлифовать шейки вала, позаботьтесь заранее о вкладках, при первом ремонте их можно использовать с уменьшением на 0.25 миллиметров. При необходимости последующие ремонтные размеры шеек коленчатого вала могут быть изменены на 0.5, 0.75 и 1 миллиметр, соответствующие должны быть приобретены и вкладыши. Последующие шлифовки связаны с прямым риском разрушения вала прямо в процессе работы, по этой причине размеры вкладышей 1.25 и 1.5 найти крайне сложно.
В процессе ремонтных работ первыми следует шлифовать шейки основания, а уже во вторую очередь – шатунные.
- Автор: Михаил
- Распечатать
Оцените статью:
(10 голосов, среднее: 4. 6 из 5)
Поделитесь с друзьями!
Adblock
detector
Размеры шеек коленвала
Статья обновлена 28.03.2022
Коленчатый вал (коленвал) — важный узел в составе кривошипно-шатунного механизма автомобиля. Его функция заключается в том, чтобы воспринимать возвратно-поступательное движение поршней и преобразовывать его в крутящий момент, обеспечивая таким образом плавную работу двигателя. Конструктивно состоит из нескольких коренных и шатунных шеек, соединенных между собой щеками. По мере износа вал перешлифовывают на ремонтные размеры, что соответственно меняет и размеры шеек коленвала. Обычно предусматривается до 6 ремонтных размеров, советские стандарты допускали 8 для ряда моделей.
Когда требуются ремонтные размеры коленвалов
Место перехода от коренной или шатунной шейки к щеке испытывает наибольшие нагрузки в конструкции коленвала, а потому износ в этом месте наиболее велик.
Таким образом, ремонтные размеры требуются при каждой шлифовке коленвала. Определяются они в зависимости от метода обработки вала. В ходе производства каждый вал проходит несколько этапов закалки, повышающих прочность и износостойкость его поверхности. Чаще всего используется термическая обработка, но в ряде случаев для усиления прочности воздействие высоких и низких температур сочетают с химическим (закалка ТВЧ, азотирование, закалка поверхностного слоя). В результате достигается достаточная глубина закалённого слоя, чтобы шейки вала можно было шлифовать 4–6 раз без потери рабочих качеств вала.
Важно знать, что валы, закаленные методом азотирования, не подлежат шлифовке.
Образец коленвала
Конструкция коленвала:
- Коренная шейка — опорная часть вала. Находится в картере двигателя и опирается на коренной подшипник.
- Шатунная шейка соединяет вал с шатунами и одновременно обеспечивает поступление к ним смазки через специальные каналы.
- Щёки — детали, соединяющие коренные и шатунные шейки.
- Передняя выходная часть вала или носок — место крепления зубчатого колеса или шкива отбора мощности для привода ГРМ.
- Задняя выходная часть вала или хвостовик — место крепления маховика или шестернёй отбора мощности.
- Противовесы — конструктивно являются продолжением щек и снимают часть нагрузки с коренных подшипников.
Как узнать размеры коленвалов
Существуют специальные таблицы, где можно узнать размеры коленвалов для конкретной модели автомобиля или техники. Такие таблицы есть для всех видов транспортных и технических средств, на которых установлен двигатель внутреннего сгорания. Размеры вкладышей, имеющихся в продаже, соответствуют этим размерам.
Например, для Opel Kadett 1,3S стандартные размеры коренных шеек составляют 54,972–54,985 мм, при шлифовке на глубину 0,25 мм – 54,722 – 54,735 мм, при шлифовке на 0,5 мм – 54,472 — 54,485. Размеры шатунных шеек, соответственно, составляют 42,971 — 42,987 в стандартном (нулевом) варианте, 42,721 — 42,737 при шлифовке на 0,25 мм и 42,471 — 42,787 при глубине обработки 0,5 мм. Для автомобиля ВАЗ-2108 стандартный диаметр составит уже 50,779–50,819 мм, а ремонтных размеров предусмотрено четыре: 50,549–50,569, 50,229–50,319, 50,049–50,069 и 49,799–49,819.
Как правило, при первом ремонте шейку шлифуют на глубину около 0,25 мм. Следующие размеры располагаются друг от друга на таком же расстоянии: 0,5, 0,75 и 1 мм. Для ряда моделей также возможны шаги в 0,125 мм. Таблицы допускают шлифовку ещё на два размера, 1,25 и 1,5 мм, однако такая обработка чревата разрушения вала в процессе работы. По этой причине в магазинах размеры вкладышей 1,25 и 1,5 представлены редко. При значительном износе иногда перешлифовывают «через размер», т. е. уменьшают диаметр сразу на два размера.
Размеры шеек на ВАЗ
Ремонт коленчатых валов
Шлифовка коленвала выполняется на вращающемся наждачным круге. В процессе работы вал поворачивают вокруг осей базирования то коренных, то шатунных шеек. Также необходимо следить за соблюдением межцентрового состояния и крайне бережно отнестись к сохранению форме галтелей, иначе ремонт может только ускорить разрушение коленчатого вала.
После шлифовки вал необходимо динамически отбалансировать в сборе с маховиком, чтобы избежать вибрации в отремонтированном двигателе. Однако на практике это условие редко выполняется, особенно при индивидуальном ремонте.
В некоторых случаях устранить повреждения шеек шлифованием невозможно. Тогда можно рассмотреть вариант наплавке или напыления (в том числе — плазменного) с последующим шлифованием под нулевой (номинальный) размер. В зависимости от наплавляемого материала прочность шейки может даже повыситься по сравнению с заводскими значениями. На финальной стадии обработки шейки полируют и подвергают финишированию до получения оптимальной степени шероховатости.
Важно учитывать, что размеры шеек одного типа обязательно должны совпадать. Разные типы же могут иметь разные диаметры. Например, коренные могут быть второго ремонтного размера, а шатунные – третьего. Исключение – ситуации полевого ремонта, при котором шейки могут вообще не иметь стандартного ремонтного размера.
Также необходимо отметить, что специфика нагрузок, приходящихся на коленвал, часто вызывает его поломку. Чаще всего это случается из-за увеличения зазоров с вкладышем, что влечет за собой ухудшение смазки. Сломанный коленвал не ремонтопригоден и подлежит замене.
Заключение
Шейка коленвала испытывает основные нагрузки при работе двигателя, поэтому состояние этой детали должно регулярно проверяться. Ее повышенный износ приводит к появлению дополнительных вибраций в двигателе и может, в конечном счете, вызвать поломку коленвала. При должном опыте и наличии оборудования можно выполнить шлифовку самостоятельно, однако большинство владельцев легковых машин предпочитает поручить эту работу профессионалам.
Читайте еще:
Полировка коленчатого вала: убедитесь, что шейки коленчатого вала правильно отполированы
Современные высокопроизводительные двигатели с жесткими допусками
больше, чем когда-либо, зависят от качественных процедур восстановления,
долговечных деталей и точной механической обработки. Один из лучших способов обеспечить долгий срок службы подшипников
в современных двигателях — правильно отполировать шейки
на коленчатом валу.
Масляная пленка между шейками коленчатого вала
и нагруженной частью коренных и шатунных подшипников составляет всего около
толщиной 0,00005 дюйма при работающем двигателе. Если шейки
слишком шероховатые или имеют заусенцы, частицы или другой мусор, который торчит
над поверхностью, это может привести к истиранию подшипников и увеличению износа подшипников
и риску их заедания.
Чугунные кривошипы обычно содержат около 4% углерода
. Углерод образует небольшие узелки графита, окруженные
относительно мягкой формой железа, называемой «ферритом».0005 вокруг графитовых узелков образует маленькие заусенцы или зазубренные лоскуты
, выступающие над поверхностью. Высота этих заусенцев может достигать
0,00035 дюйма, что более чем достаточно для разрезания
масляной пленки и врезания в подшипники.
Ферритовые заусенцы создают пилообразную поверхность, , обычно обращенные в сторону от направления
, шейка была отшлифована или отполирована.0005 считается «благоприятной» ориентацией, потому что борфрезы
с меньшей вероятностью впиваются в подшипники. С другой стороны,
если острые кромки направлены в одном и том же направлении вращения,
это «неблагоприятная» ориентация и с гораздо большей вероятностью вызовет проблемы.
Хитрость, конечно же, заключается в том, чтобы выяснить, какой
способ какой, то есть, каким способом шлифовать кривошип и каким
способом его полировать, чтобы добиться правильной ориентации ферритовых
заусенцев.
Конечной целью при полировке шеек коленчатого вала
является получение относительно плоской и гладкой поверхности
(средняя шероховатость 10 микродюймов или менее) с большим количеством опорной поверхности
для поддержки масляной пленки. Но также важно
ориентировать оставшиеся ферритовые заусенцы в благоприятном направлении
, чтобы они оказывали меньшее абразивное воздействие на подшипники.
В шатунах из кованой стали нет графита
или феррита, о которых можно беспокоиться, поэтому нет необходимости шлифовать
кривошип в одном направлении, затем отполируйте его в противоположном направлении.
Несмотря на это, для достижения наилучших результатов рекомендуется полировать стальной кривошип
в том же направлении, в котором он вращается.
Техника полировки
Одним из способов достижения оптимальной чистоты поверхности
шеек чугунного кривошипа является шлифовка шеек коленчатого вала
в направлении, противоположном его обычному вращению в двигателе
, а затем полировка в том же направление вращения в 9двигатель 0005. Это оставит благоприятную поверхность с острыми краями
ферритовых заусенцев, обращенными назад. Полировка кривошипа в направлении
, противоположном направлению, в котором он был отшлифован, также сломает больше ферритовых заусенцев
, оставив более чистую и гладкую поверхность.
По словам Стива Блегги, менеджера по продажам компании
Abrasive Accessories, Inc., Фриско, Техас, обычно используется полировальная лента с абразивом
#320 или #400 в зависимости от требований к чистоте поверхности
. самые популярные 9Размеры 0005 — это размер ремня 1 x 64 дюйма и 1 x 72 дюйма.
Ян Багнолл, менеджер по продажам RMC Rogers Machine
Co. , Бэй-Сити, Мичиган, говорит, что большинство автомобильных коленчатых валов обычно вращаются в двигателе на
по часовой стрелке. Некоторые морские и промышленные двигатели вращаются
против часовой стрелки, поэтому первое, что вам нужно определить, это
, в какую сторону обычно вращается кривошип, прежде чем вставить его в
шлифовальный станок или полировальный стенд.
«Большинство станков для шлифовки коленчатых валов и полировальные стенды
поворачивают коленчатый вал в сторону оператора (по часовой стрелке, если
если смотреть с левого конца машины, против часовой стрелки
если смотреть с правого конца)» говорит Багнолл.
машина – которая противоположна своему нормальному направлению вращения
в двигателе. Если коленчатый вал установить в шлифовальный или полировальный стенд
носиком влево, то, с другой стороны,
он будет вращаться в том же направлении, что и в двигателе».0003
Как следует установить кривошип, чтобы добиться
неблагоприятной ориентации при шлифовании и благоприятной
ориентации при полировке? Бэгнолл говорит, что шлифовальный круг на большинстве кривошипно-шлифовальных станков
также вращается против часовой стрелки, поэтому искры и мусор
отбрасываются вниз во время полировки шейки.
Это оставит ферритовые заусенцы, ориентированные
в неблагоприятном направлении на шейках, если кривошип, который обычно
вращается по часовой стрелке в двигателе, установлен носовой частью к
верно. Если кривошип установлен носом влево, операция шлифования
оставит ферритовые заусенцы с благоприятной ориентацией
и снизит эффективность этапа полировки.
Для получения наилучшей отделки коленчатый вал
необходимо перевернуть после того, как он был отшлифован, так, чтобы передняя часть
находилась слева для полировки. Это необходимо, поскольку абразивная
поверхность полировальной ленты, которая движется по шейке кривошипа
, отходит от оператора и отбрасывает пыль и мусор назад
и в путь.
Однако, если коленчатый вал установлен носовой частью
вправо и вращается против часовой стрелки в оборудовании,
ремень будет шлифоваться в том же направлении, что и
кривошип. Это снизит эффективность этапа полировки
и оставит неблагоприятную ориентацию оставшихся ферритовых заусенцев
. Поворот кривошипа так, чтобы передняя часть была влево для полировки
, удалит больше заусенцев и оставит благоприятную ориентацию
, которая является лучшей обработкой поверхности для подшипников.
Не все согласны с этой рекомендацией.
Некоторые говорят, что они достигли хороших результатов независимо от того, каким образом
кривошип установлен, отшлифован и отполирован. Некоторые восстановители говорят, что
они шлифовали и полировали коленчатые валы в обоих направлениях с
без плохих результатов. Если поверхность вала достаточно гладкая, вращение
, при котором он шлифуется, не должно иметь значения. Тем не менее, микроскопическое
исследование отделки поверхности обычно показывает, что наилучшая отделка
чугунного коленчатого вала достигается при неблагоприятной шлифовке
и благоприятная полировка.
Почему бы просто не установить кривошип в шлифовальный станок
носиком влево для шлифовки и полировки? Этот подход
экономит время, поскольку вам не нужно перемещать кривошип
после шлифовки, но при этом сохраняется благоприятная ориентация ферритовых заусенцев
, что снижает эффективность операции полировки
.
Альтернативным методом является использование двухэтапной процедуры полировки
. Хотя не все производители подшипников
согласен с процедурами полировки, Рон Томпсон, инженер по подшипникам
в Federal-Mogul Corp., Детройт, Мичиган, говорит, что неправильная обработка коленчатого вала
может быть особенно вредной для подшипников. При использовании оборудования для ленточной полировки
он рекомендует полировать шейки в неблагоприятном направлении
(противоположном направлению вращения) лентой #280 с зернистостью
, а затем обрабатывать шейки в благоприятном направлении (то же направление
, что и при вращении) с помощью Ремень с зернистостью 320.
Полировка лентой
Еще один способ полировки шатунных шеек после шлифовки
— с помощью оборудования, в котором используется лента для микрообработки, а не абразивная лента
. Этот тип оборудования работает иначе, чем ленточный полировальный станок. Вместо трения вращающейся абразивной ленты
о вращающуюся шейку, абразивная лента остается неподвижной
и прижимается к шейке при вращении кривошипа.
Лента соприкасается в четырех точках, что, по словам поставщиков этого типа оборудования,
обеспечивает более равномерный контакт
и равномерная полировка поверхности — хотя внешний вид может быть несколько
более тусклым, чем то, к чему привыкли многие люди. Затем лента продвигается примерно на дюйм для следующей
цапфы, и так далее, пока все
цапфы не будут отшлифованы. С лентой
также используется смазка, помогающая смыть мусор.
По сравнению с полировкой ленты, которая может удалить от
0,0002 дюйма до 0,0005 дюйма или более дюймов металла с цапфы
в зависимости от зернистости ленты, длины полировки и приложенного давления
оператором, ленточная полировка почти не удаляет металл. Абразив
на ленте очень мелкий. Абразивная лента размером 15 микрон аналогична зернистости
и ленточному абразиву #600. Полировка чугунного кривошипа со шлифованным покрытием
12 RA в течение 15 секунд 15-микронной лентой, например,
, может улучшить покрытие до 7 RA или выше.
Одним из заявленных преимуществ полировочной ленты
является снижение риска ошибки оператора. Давление, оказываемое
лентой на кривошип, фиксировано и не зависит от того, насколько сильно
оператор нажимает на ручку.
Другое предполагаемое преимущество — более стабильные результаты
. Режущее действие полировальной ленты меняется по мере ее износа. Новый ремень режет агрессивнее, чем бывший в употреблении. Лента
каждый раз полируется одинаково. Лента
также стоит меньше при длительных перевозках, чем ремни
. Рулон ленты стоит около 33 долларов и обычно делает около
200 оборотов, если лента продвигается примерно на полдюйма на шейку.
Но первоначальные инвестиции в оборудование для полировки лент значительно
выше, чем у традиционного оборудования для полировки лент.
Ручные ленточные полировальные машины обычно стоят от 500 до
700 долларов США в зависимости от того, работает ли полировальная машина с пневматическим или электрическим приводом. Полировальные стенды Belt
обычно продаются по цене от 2000 до 2600 долларов США в зависимости от размера кривошипов, которые может вместить стенд.
Оборудование для полировки ленты, для сравнения,
может стоить от 13 000 долларов США для полировального станка вторичного рынка до 50 000 долларов США или на
больше для устройства типа OEM. Таким образом, большой объем рукояток обычно составляет
необходимо, чтобы оправдать инвестиции в полировальную машину.
Кен Бартон из QPAC Corp., Лансинг, штат Мичиган, говорит
, что его компания поставляет производителям оригинального оборудования
ленточные полировальные машины для кривошипов. «Сегодня OEM-производители используют ленту для полировки почти
всех коленчатых валов, — сказал Бартон. «Обычно они
шлифуют новый кривошип до 25–30 RA, а затем полируют его до спецификации
, которая может составлять от 8 до 12 RA для автомобильного коленчатого вала или от 5 до 7
RA для дизельного коленчатого вала».
Бартон говорит, что наилучшие результаты при полировке лентой
достигаются, когда кривошип шлифуется так же, как он вращается в
двигателе, а затем полируется таким же образом. Он говорит, что это продлевает срок службы ленты
, а также улучшает внешний вид.
Марк Джелтема, специалист по продуктам и поставщик
технической поддержки в K-Line Industries, Голландия, Мичиган (K-line имеет
эксклюзивное соглашение с QPAC на поставку технологии полировки ленты
на рынок послепродажного обслуживания), также говорит лучшее результаты
достигается при вращении кривошипа в том же направлении, в котором он обычно
вращается в двигателе, когда он полируется лентой.
«Наша машина реверсивная, и носовая часть
обычно устанавливается слева», — объяснила Джелтема. «Этот
оставит благоприятную поверхность с полировкой вала в диапазоне от 3 до
6 микрон с 30-секундной полировкой с использованием 15-микронной ленты».
Опыт полировки
Том Бэгли из Grooms Engines, Parts, Machining,
Inc. , Нэшвилл, Теннесси, говорит, что его компания недавно приобрела подержанный
OEM машина для полировки ленты. «Это машина
колебательного типа, в которой используется 30-микронная лента», — пояснил он. «Мы
запускаем ленту в течение 10 секунд на каждой шейке, при этом кривошип поворачивается
сначала в одну сторону, затем в другую, причем последний раз в благоприятном направлении
. Это дает нам очень стабильные результаты в диапазоне от 6 до 9
RA. .»
Бэгли говорит, что использует оборудование для полировки ленты
как на чугунных, так и на стальных кривошипах. «По сравнению с ленточным полировальным станком,
требуется немного больше времени, чтобы очистить шейки лентой
, но мы очень довольны результатами, — сказал он. по-прежнему кладут другую отделку поверхности на цапфы
, которые идут против сальников», — сказал он. «Мы используем ленту
толщиной 40 микрон, которая оставляет отделку от 14 до 18 RA. Мы считаем, что это помогает лучше удерживать
масло для хорошего уплотнения, чем хорошо отполированная поверхность».
Стив Шмидт из Jasper Engine and Transmission
Exchange, Джаспер, штат Индиана, говорит, что его отдел коленчатых валов недавно
перешел с полировки ремня на полировку ленты. «Лента не может
обработать 80 коленчатых валов в день и медленнее, чем ремни, но мы стабильно достигаем
обработки шейки в диапазоне от 7 до 8 RA с лентой 3M 30
микрон», — сказал Шмидт. Подводные камни при полировке
Одной из ошибок, которую иногда допускают при полировке ремня
коленчатого вала, является чрезмерная полировка шеек
Независимо от того, пытается ли оператор добиться яркого хромированного внешнего вида
или пытается убрать чрезмерную шероховатость, оставшуюся после операции шлифовки
, чрезмерная полировка может создать «эффект ореола»
вокруг смазочных отверстий. Образовавшиеся впадины уменьшат площадь подшипника
и прочность масляной пленки, что может привести к преждевременному выходу из строя подшипника
.
Величина давления, оказываемого полировальной
шейкой на шейку, также влияет на режущее
действие ленты и количество материала, удаляемого с шейки.
Все, что нужно, это очень легкое нажатие и не более
нескольких секунд. Чрезмерное давление может изменить геометрию шейки
, что приведет к проблемам с зазором и увеличению утечки масла.
Если азотированный коленчатый вал был отшлифован до размера
меньшего, чем на 0,010 дюйма, после шлифовки коленчатый вал необходимо повторно азотировать
, а затем выправить перед полировкой.
Не забудьте отполировать радиусы галтелей и
уплотнение поверхностей, а также поверхностей подшипников скольжения.Штриховка 0005 на штоке и коренных шейках желательна, но уплотнения и упорные поверхности
должны иметь прямолинейную полировку.
Save the Crank — Коленчатый вал из Огайо
Гоночный коленчатый вал не обязательно является одноразовым компонентом — как показано в журнале Drag Racing Scene .
Гоночные шатуны соответствуют самым жестким допускам. Как правило, обработанные поверхности современных гоночных коленчатых валов имеют допуск 0,0003 дюйма (или лучше) прямо из коробки производителя. Эти точные допуски на шлифование обеспечивают отличные несущие поверхности, что увеличивает срок службы кривошипа и подшипниковых поверхностей при массивной скручивающей нагрузке, которую они испытывают в гонках.
В мире дрэг-рейсинга напряжение, воздействующее на коленчатый вал, невероятно велико при преобразовании радиальных сил от поршня и штока во вращательное движение коленчатого вала. Лучшие материалы и допуски на обработку в компонентах вашего двигателя ведут войну со злоупотреблениями, связанными с высокими оборотами, сцеплениями, гидротрансформаторами и пусковыми механизмами. Список сценариев ненависти к коленчатому валу можно продолжать и продолжать.
Станция правки многократно используется в процессе ремонта, чтобы убедиться, что сварка и механическая обработка не изменяют коленчатый вал. Благодаря опыту персонала все должно быть в точности по размеру без чрезмерной корректировки во время операции гидравлической правки. Выход из строя шатунного или опорного подшипника является наиболее распространенной проблемой в тяжелом низу гоночного двигателя. Другие распространенные неисправности включают область упорного подшипника, обычно расположенную на задней шейке блока. Сам коленчатый вал может быть поврежден без выхода подшипника из строя. Общий износ поверхностей коленчатого вала может выйти за пределы допустимых размеров, могут иметь место трещины или изгибы.
Прежде чем вы отправитесь и выбросите этот поврежденный коленчатый вал за высокую цену в кучу металлолома, есть очень жизнеспособные методы ремонта для этих описанных сценариев. Конечно, самый простой ремонт — перешлифовать типичный шток и коренную шейку на меньший диаметр, устранив таким образом повреждение.
Хотя подшипники легко доступны для компенсации уменьшенного диаметра шейки коленчатого вала после «переточки», многие спорят о прочности коленчатого вала после типичной очистки 0,010/010. Мы сохраним этот спор для другой технической статьи.
Процессы предварительного и последующего нагрева различаются в зависимости от марки и материала кривошипа в нескольких печах Ohio Crank. Каждая рукоятка обрабатывается по-разному для достижения наилучшего результата.
В процессе дуговой сварки под флюсом используется гранулированный флюс, который обтекает активный шов. Это пример очень популярного варианта ремонта коленчатого вала, когда упорный фланец изнашивается из-за проблем с трансмиссией или сцеплением/гидротрансформатором. Затем этот фланец можно приварить и повторно обработать до нужных размеров. Есть авторитетные специалисты по коленчатым валам, такие как Ohio Crankshaft, у которых есть навыки и оборудование для ремонта ваших дорогих коленчатых валов, поэтому они живут, чтобы сражаться в другой день.
«Гоночные коленчатые валы достаточно просты, когда речь идет о материалах и используемых процессах закалки», — объясняет владелец компании Ohio Crankshaft Стэн Рэй. «Мы также ремонтируем коленчатые валы, начиная от огромных воздушных компрессоров и заканчивая кривошипами авиационных двигателей Allison длиной 7 1/2 футов и самолетами WWII. Некоторые из этих ремонтов усложняются уникальными материалами и процессами закалки. За прошедшие годы мы освоили множество процессов сварки и термообработки для множества различных материалов кривошипа».
Гранулированный флюс не только создает защитный газ для защиты сварочной дуги от примесей из воздуха, но и образует шлак расплавленного флюса, окружающий сварной шов по мере его охлаждения.
Рэй рекомендует первым шагом при ремонте коленчатого вала провести анализ поврежденного узла.
«Мы всегда рекомендуем покупателю позвонить нам, чтобы подробно описать, какой у него коленчатый вал и какие общие повреждения он имеет, прежде чем тратить доллары на доставку», — продолжает Рэй. «Хотя мы можем успешно устранить некоторые довольно серьезные повреждения, мы просто ненавидим, когда кто-то тратит деньги, чтобы отправить нам кривошип, который не подлежит ремонту. Что еще более важно, мы обычно можем узнать, какой у них коленчатый вал, вместе с описанием повреждений и определить, можем ли мы его отремонтировать. Современные цифровые фотографии и электронная почта также могут помочь нам в диагностике ремонта».
По прибытии кривошип подвергается тщательной проверке с помощью магнитопорошкового тестирования, широко известного как процесс «Magnaflux». Кольцо электрического тока создает вокруг коленчатого вала магнитное поле. Жидкий раствор, содержащий мелкий порошок железа, течет по коленчатому валу. Трещина в металле нарушит магнитное поле, таким образом, смесь жидкости и металла сконцентрируется в трещине. Ультрафиолетовый черный свет четко освещает любые трещины, обычно невидимые невооруженным глазом.
Мы следили за Рэем Дарнером в процессе ремонта. Дарнер имеет более чем 30-летний опыт шлифовки и ремонта коленчатых валов в штате Огайо.
«Весь процесс ремонта основан на знании того, какой процесс лучше всего подходит для каждого кривошипа, который мы ремонтируем», — говорит нам Дарнер. «При каждом ремонте учитываются разные сварочные проволоки, тепло и скорость сварки».
Завершенный сварной шов показывает тщательную сварку как опорной поверхности, так и закругленных углов. Обратите внимание на тепловое окрашивание кривошипа вокруг сварного шва. Перед процессом сварки свариваемые поверхности коленчатого вала слегка шлифуют, чтобы удалить любые посторонние материалы, такие как материал подшипников, застрявшие в кривошипе. Шатунные шейки также могут быть некруглыми на поврежденных поверхностях, так что это также обеспечивает ровную шейку для сварки.
На сварочной станции Ohio Crankshaft используется оборудование для сварки под флюсом, которое считается наиболее эффективным способом обеспечения надлежащего проникновения наростов материала для повторной обработки. Этот процесс сварки позволяет флюсу, подаваемому самотеком, полностью покрывать точку дуги сварочного аппарата MIG с высокой силой тока. Как и в любом процессе сварки, флюс создает газ, который защищает сварочную дугу от примесей в обычном воздухе, которым мы дышим.
Сварочный аппарат устроен аналогично шлифовальному станку. Если шатунная шейка, которая вращается за пределами осевой линии коленчатого вала, требует сварки, сварочный аппарат запрограммирован на перемещение с ходом штока, чтобы сохранить точное расстояние между наконечником сварочного аппарата и движением шейки.
Ярким примером рентабельного ремонта кривошипа является этот узел, у которого были повреждены коренная и шатунная шейки.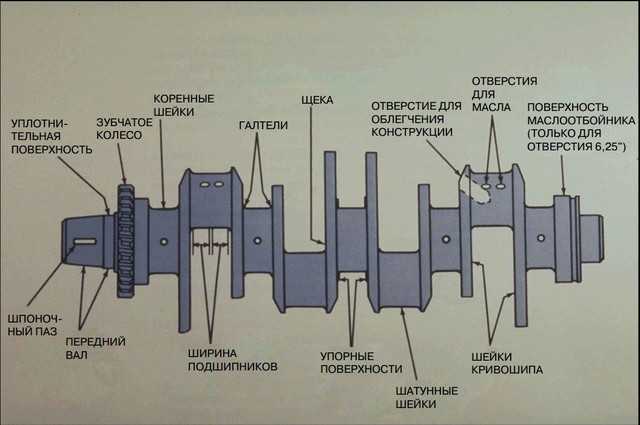
Металлический жидкий раствор пропитывает коленчатый вал, а проверяемые участки освещаются черным ультрафиолетовым светом. Электрическое поле разрушается вокруг любых трещин, что концентрирует мелкие частицы металла, делая видимыми любые трещины, невидимые невооруженным глазом (стрелка).
«Мы уделяем пристальное внимание прямолинейности кривошипа на протяжении всего процесса ремонта», — описывает Дарнер. «С самого начала и на всех этапах сварки и переточки мы следим за тем, чтобы кривошип оставался прямолинейным. Мы также уделяем очень пристальное внимание ремонту радиуса на каждой стороне шейки в соответствии со спецификациями. В этой части процесса ремонта опыт окупается. Провар между поверхностью цапфы и закругленными концами может быть разным. Знание различных марок и материала каждого кривошипа окупается».
Эта рукоятка тщательно приспособлена для сварки.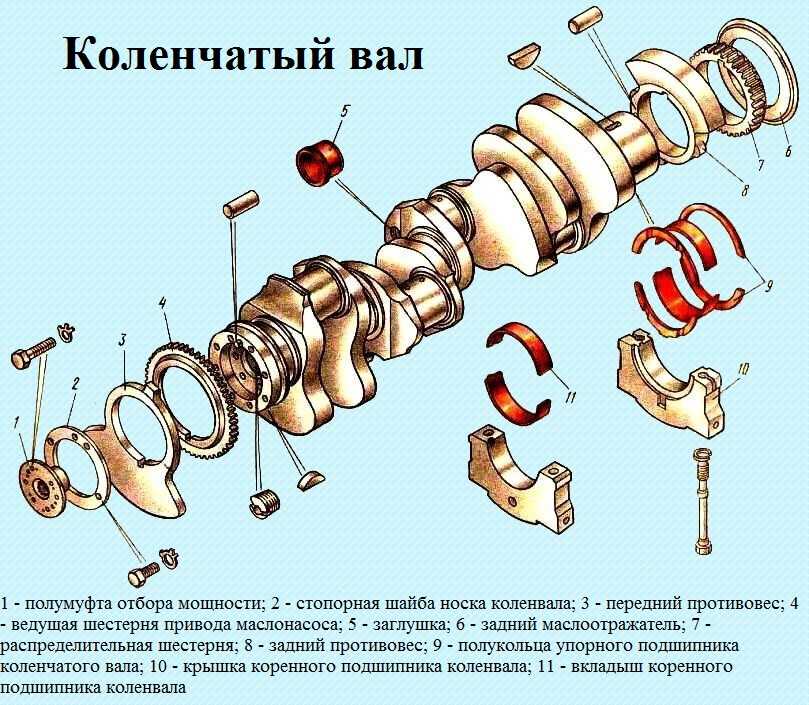
Процесс выпрямления не совсем высокотехнологичен, но грамотный процесс выпрямления больше похож на искусство, чем на науку. Станция гидравлического кривошипного пресса стратегически расположена между сварочной и шлифовальной станциями внутри предприятия по производству коленчатых валов в Огайо. Эта станция заполнена приспособлениями и несколькими циферблатными индикаторами, которые контролируют множество точек по длине кривошипа. Гидравлическое давление подается, чтобы «согнуть» кривошип до надлежащих допусков.
«Здесь опыт окупается», — улыбается Дарнер. «Мы знаем, сколько встречного изгиба необходимо для любого данного кривошипа, и ожидаем, что он вернет надлежащий допуск. Это похоже на выпечку печенья; вы просто получаете опыт в том, что нужно между 5140, 4340 или заводной рукояткой, чтобы вернуть ее в прямое положение одним выстрелом, не заходя слишком далеко.