Конструкции клапанов — CrewTraffic
Клапаны без корпуса устанавливают непосредственно в крышку цилиндра, что дает возможность увеличить проходные сечения для воздуха и газов, но при этом необходим демонтаж крышки для осмотра и притирки клапанов. В четырехтактных дизелях выпуск газов всегда обеспечивается выталкивающим ходом поршня. Поэтому для улучшения наполнения цилиндра воздухом диаметр впускного клапана иногда увеличивают (приблизительно на 20%) за счет уменьшения диаметра выпускного.
В четырехтактных дизелях обычно применяют два или четыре газораспределительных клапана, а в двухтактных МОД – один клапан. Увеличение числа клапанов усложняет конструкцию цилиндровой крышки, но снижает их механическую и тепловую напряженность за счет уменьшения диаметра и массы.Клапан без корпуса (см. рис. 11.2) состоит из штока 8 и тарелки 11, имеющей коническую рабочую фаску. Чаще всего применяют клапаны с углом фаски 45 °, обеспечивающим большую жесткость клапана и плотную его посадку на седло, лучшую самоцентровку во время работы и при притирке, лучший отвод теплоты от тарелки, а также наиболее выгодную форму газового потока при полном открытии клапана.
Фаска тарелки прижимается к седлу, протачиваемому в крышке цилиндра (см. рис. 11.2, а) или к съемному седлу 12 (см. рис. 11.2,6), зафиксированному в крышке пружинящим кольцом или другими способами (запрессовка, развальцовка, зачеканка). Фаску и седло тщательно притирают. Шток 8 клапана перемещается в направляющей втулке 9. Клапан прижимается к седлу пружинами 10, упирающимися в нижнюю и верхнюю 7 тарелки. Верхняя тарелка крепится коническими полукольцами («сухарями») на конической шейке штока клапана (применяют и другие способы крепления верхней тарелки). Для предотвращения разбивания торца штока в него вставляют закаленный сухарь или устанавливают на него колпачок.
В современных двигателях стали применять седла, рабочей поверхности которых придана W- образная форма с карманом 1, в котором аккумулируется воздух, препятствующий протечке горячих газов зону контакта с тарелкой клапана (рис11.3).
Клапаны с корпусом (см. рис.11.4) конструктивно сложнее, имеют меньшее проходное сечение, но удобнее в эксплуатации, так как можно производить их осмотр, притирку и замену без демонтажа цилиндровой крышки.
Из-за наличия теплового зазора в приводе клапана его движение начинается и заканчивается ударом, вызывающим дополнительные напряжения в седле и тарелке, пружине и на поверхностях
контакта клапанного механизма.
Для обеспечения безударной ра боты и сиижения шума в М.0Д с прям0 точно-клапанной продувкой применяют гидравлический привод клапанов. Гидравлический привод способствует также уменьшению массы движущихся частей и сил инерции клапанного привода, повышению надежности работы.
В рассматриваемой конструкции (рис 11.4) механический привод клапана заменен на гидравлический. С этой целью на шток клапана надет поршень 6, на который давит масло, поступающее по каналу 7 от гидравлического поршневого усилителя, привод которого осуществляется от установленного на распределительном валу кулачка. Клапанные пружины в новой конструкции устранены и их функцию выполняет “воздушная пружина” с поршнем 5. При снижении давления масла в приводе клапана его возврат на седло осуществляется воздушной пружиной, в которой сжатый воздух снизу давит на поршень 5 и клапан поднимается и мягко садится на седло, что существенно уменьшает наклеп посадочных поверхностей.
Снижение тепловой напряженности клапанов достигают интенсивным охлаждением цилиндровой крышки в районе седла и непосредственно седла.
В современных мощных МОД и СОД часто предусматривают автоматический поворот клапанов относительно оси во время работы дизеля. Вращение клапанов обеспечивает более равномерное распределение температур в тарелке и меньшую ее деформацию, равномерный износ тарелки и седла и их некоторую самопритирку.
Наиболее просто это достигается установкой специальных лопаток на нижней части штока 3, которые под действием газового потока поворачиваются совместно с клапаном.
Справочная и техническая информация о деталях двигателей
Справочная и техническая информация о деталях двигателейразвернутьсвернуть
Мощность двигателя, при прочих равных условиях, прямо пропорциональна количеству горючей смеси или воздуха и топлива, поступающего в его цилиндры через впускные клапаны и качества очищения цилиндра от отработанных газов через выпускные клапаны.
Для улучшения наполнения двигателя диаметр впускного клапана выполняется обычно большим, чем выпускного. Так как при выпуске скорость потока отработанной смеси выше, чем свежей впускной, за счет выталкивания отработанных газов поршнем на такте выпуска. При много клапанной системе, например у двигателя AUDI ADR, диаметр выпускной тарелки клапана больше чем у впускных, но устанавливается 3 впускных клапана и 2 выпускных, таким образом, общая площадь впускных клапанов все равно больше. Уменьшение диаметра выпускных клапанов позволяет снизить их температуру и уменьшить величину движущихся масс, приходящихся на один клапан.
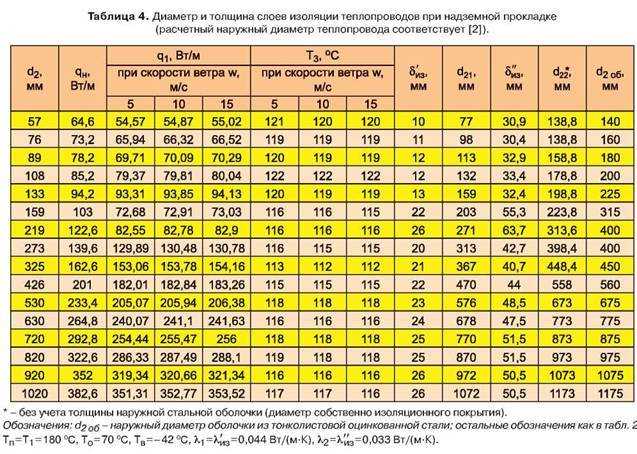
Основными элементами клапана являются головка (тарелка) и стержень (шток). С целью уменьшения гидравлических потерь на впуске и выпуске переход от головки клапана к стержню делается, возможно, более плавным.
Клапаны, особенно выпускные, работают высокой тепловой напряженности, температура тарелки впускного клапана достигает при полной нагрузке двигателя 350-500ºС, а выпускного 700-900ºС. Столь высокая тепловая напряженность выпускных клапанов обусловливается главным образом их очень сильным нагревом во время процесса выпуска. Клапаны подвергаются так же коррозирующему действию газов. Материал клапанов вследствие этого должен обладать стойкостью против коррозии и хорошо сопротивляться износу, поскольку условия смазки клапана не удовлетворительны.
Для повышения износостойкости и продления срока службы клапаны проходят дополнительную обработку, путем наваривания специального сплава (стеллита) на рабочую фаску клапана.
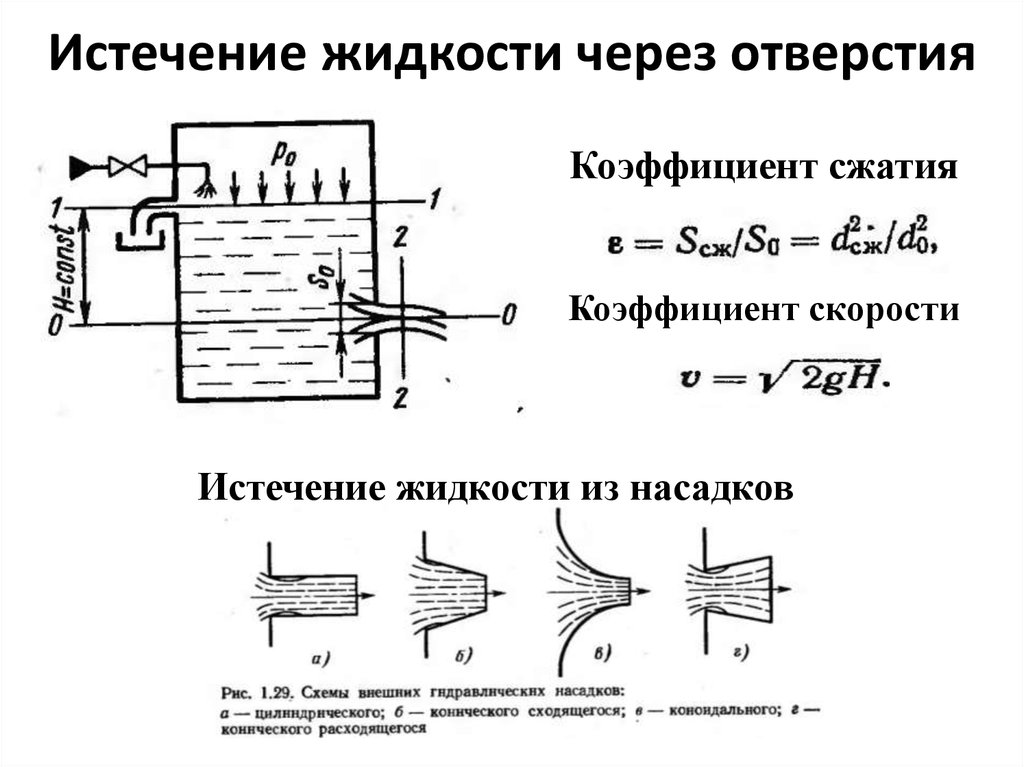
Выпускные клапаны форсированных двигателей иногда выполняют полыми. Заполняющее на 50-60% полость клапана легкоплавкое вещество (натрий или специальные соли) во время работы двигателя плавится и энергично взбалтывается, что обеспечивает лучший отвод тепла от головки к стержню клапана и тем самым устраняет его перегрев. Таким образом можно понизить температуру тарелки клапана на 80 –150 °C. Для уменьшения массы, в современном моторостроении находят применение полые, незаполненные впускные клапаны. Полые выпускные клапаны применяются преимущественно с целью понижения температуры в особо опасной области галтели (закруглённого перехода).
Впускные и выпускные клапаны разделяются на :
- Цельнометаллический (монометаллический) клапан. Эти клапаны производятся только из одного материала. При этом выбирается такой материал, который подходит к предъявляемым требованиям, это высокая теплостойкость и антифрикционные свойства.
- Биметаллический клапан.
Биметаллические клапаны это соединение двух металлов: материала тарелки клапана с высокой теплостойкостью и материала штока клапана, который закалён со стороны конца стержня клапана, и при этом обладающего высокими антифрикционными свойствами для скольжения внутри направляющей втулки клапана. Соединение этих двух материалов выполняется при помощи сварки трением.
Клапан с наполнителем |
Биметаллический клапан |
Порошковые клапаны для экстремальных температур | Gemco Valve
Gemco Valve и ATEC Valve объединили свой опыт и технологии для создания уникального решения для обработки экстремально температурных абразивных порошков для GTI. Институт газовых технологий — передовое энергетическое предприятие, расположенное в Дес-Плейнс, штат Иллинойс. GTI решает важные энергетические проблемы, превращая необработанные технологии в практические решения.
Один из текущих исследовательских проектов GTI предназначен для Министерства энергетики; специально для ARPA-E (Агентство перспективных исследовательских проектов-Энергетика). ARPA-E — это правительственное агентство США, созданное по образцу Агентства перспективных исследовательских проектов Министерства обороны США, которому поручено продвигать и финансировать исследования и разработки передовых энергетических технологий. Текущий проект GTI включает в себя передовые методы передачи и хранения энергии с использованием термальной жидкости и термальных резервуаров. GTI описывает исследование следующим образом: «… технология термальных жидкостей на основе частиц имеет потенциал для захвата, транспортировки, хранения и повторного использования энергии при температурах 650 ° C …. Технология включает смешивание частиц размером от 10 до 100 микрон (например, углерода, песка, минералов, керамики, огнеупоров, металлов, композитов, стекла) с подходящими свойствами, такими как рабочая температура, точка плавления, теплопроводность и удельная теплоемкость, с соответствующей нереактивностью. газ (воздух, N2, CO2 и т. д.) для создания двухфазного теплоносителя».* 1
Немногие подходящие клапаны рассчитаны на работу в этом диапазоне температур, а GTI требуется для переноса их абразивных частиц с помощью транспортировки плотной фазы при 20 фунтов на квадратный дюйм. Типичный высокотемпературный диапазон для высокотемпературных клапанов составляет 400-450ºC. Следует отметить, что более высокие температуры относятся к категории «экстремальных» температур* 2 .
Порошковый клапан Gemco Valve и ATEC Valve в действии.
Компания Gemco Valve предоставила сегментный клапан ATEC, рассчитанный на давление 2 бар (30 фунтов/кв. дюйм) при 650°C (1200°F) в размерах 3 дюйма/80 мм, 2 дюйма/50 мм и 1,5 дюйма/40 мм. Материалы конструкции как 309использовались нержавеющая сталь со сплавами 625 и 276 и графитовые уплотнения. Седла из закаленного металла были подпружинены, чтобы учесть тепловое расширение и обеспечить газонепроницаемое уплотнение в широком диапазоне требуемых рабочих температур.
Одна из проблем, связанных с нагревом, с которой столкнулась команда, заключалась в том, что блок автоматизации/привода необходимо было защитить от высоких рабочих температур клапанов. Есть два типичных метода решения этой проблемы, каждый из которых обычно подходит. Обычная изоляция вокруг трубопровода и клапана или теплозащита, в которой используется барьер между клапаном и блоком привода. Однако компании GTI требовался легкий доступ к пакету автоматизации, поэтому команда разработчиков предложила уникальное решение. Во-первых, они увеличили длину карданного вала, чтобы увеличить расстояние между клапаном и приводом, а затем добавили ребра радиатора для увеличения отвода тепла. Эта комбинация оказалась рентабельной, практичной и эффективной.
Компания GTI успешно провела испытания на паллетах в Калифорнийском университете в Мерседе. Ни заказчик, ни испытательный центр не ожидают каких-либо эксплуатационных или проектных проблем, и на момент написания этой статьи клапаны успешно работали на месте в течение нескольких месяцев.
Если вас интересует более подробная информация о высокотемпературных клапанах, ознакомьтесь с этой статьей о высокотемпературных вариантах исполнения.
* 1 Одновременное производство электроэнергии и тепла.
* 2 Информатор обрабатывающей промышленности
Изучение причин, обнаружение и предотвращение
Загрязнение – это образование нежелательных отложений материала на поверхностях теплопередачи во время технологического нагрева и охлаждения.
Это происходит во всех отраслях промышленности и в большинстве конструкций теплообменников, с последствиями, варьирующимися от ухудшения теплопередачи до сопротивления потоку и перепадов давления. Образуя своего рода изоляцию на теплообменных поверхностях и уменьшая теплопередачу, загрязнение снижает эффективность теплообмена .
В этой статье мы расскажем:
- Стоимость, виды и причины загрязнения
- Как обнаружить загрязнение
- Как очистить теплообменник
- Как предотвратить загрязнение 90 047
Расходы, связанные с загрязнением
Предотвращение загрязнения теплообменников обычно сосредоточено на самих теплообменниках, однако на загрязнение и производительность теплообменника могут влиять характеристики системы, которые присутствуют как до, так и после теплообменника.Эти характеристики могут включать различные свойства продукта, обращение с продуктом перед теплообменником и эксплуатационные характеристики другого оборудования, такого как насосы, клапаны и противодавление.
~ Мелисса Фрайер, менеджер по развитию бизнеса систем теплообмена в санитарных целях, Альфа Лаваль
Короче говоря, затраты на загрязнение многочисленны и разнообразны.
- Неэффективность производства из-за перепадов давления и плохой теплопередачи
- Время обслуживания и оборудование для удаления тяжелых отложений
- Чистящее оборудование и химикаты
- Утилизация опасных чистящих растворов
- Сокращение срока службы и дополнительные затраты на энергию
- Потери производства из-за остановов
- Замена засоренного оборудования
- Снижение эффективности регенерации
Типы загрязнения
Наиболее часто встречающиеся типы загрязнения и старения при гигиенической обработке делятся на четыре основных типа: поверхность деталей теплообменника. Загрязнению способствуют несколько переменных, , включая рН воды, вязкость продукта и шероховатость поверхностей компонентов, среди многих других. Вместе переменные могут быть выражены как коэффициент загрязнения, который численно представляет сопротивление теплопередаче — или тепловое сопротивление — в вашей системе. Молочные продукты включают жиры, сахара и белки, которые способствуют загрязнению. При производстве продуктов питания и напитков твердые частицы могут слипаться и забиваться, а в фармацевтических целях частицы косметических средств и фармацевтических препаратов, образующиеся в процессе обработки, могут прилипать и накапливаться. В большинстве случаев загрязнение уменьшается при более высоких скоростях жидкости, потому что увеличение скорости потока увеличивает напряжение сдвига жидкости , что приводит к большему удалению отложений. Для более значительных отложений увеличение скорости потока за пределами определенной точки может не уменьшить засорение значительно. В случае очень сильных отложений увеличение скорости потока может не иметь никакого эффекта. Вода может образовывать накипь из-за таких минералов, как карбонат кальция (CaCO3). Отложение солей на поверхности теплообменника увеличивается с повышением температуры. Аналогичным образом, биологический рост может происходить при повышении температуры во время обработки пищевых продуктов. Наконец, белки и жиры в пищевых продуктах могут сгореть, если разница температур между выходом горячего продукта и входом горячей среды слишком значительна. Во время обработки молока фосфат кальция и сывороточный белок могут скапливаться на поверхностях теплообменника. Загрязнение вызывает увеличение перепада давления за счет уменьшения площади, через которую может течь продукт. Как правило, в молочных продуктах белки, жиры, сахара и минералы могут выделяться из раствора и осаждаться на поверхностях теплообменников и каналах загрязнения. Если в жидкости происходят химические изменения, это различие может привести к образованию слоя отложений на поверхности труб или пластин. Например, взвешенные соли могут затвердевать при повышении температуры. Для предотвращения коррозионного обрастания слоев термостойкого материала выбирайте блоки, изготовленные из коррозионностойких нержавеющих сталей и сплавов. Для более агрессивных продуктов с высоким содержанием солей детали агрегатов могут быть изготовлены из титана, сплавов нержавеющей стали или Super Alloys™ AL-6XN® и Hastelloy® C-22®. Обнаружение загрязнения обычно происходит путем физического осмотра или путем мониторинга производительности системы. Физический осмотр включает измерение толщины отложений на пластинах, трубах или трубах. Мониторинг температуры и давления — лучший способ устранения неполадок и обнаружения загрязнения теплообменников. Приборы измеряют и сообщают о критических переменных, которые могут указывать на загрязнение теплообменника. Мониторинг температуры жидкостей, проходящих через теплообменники. Падение температуры может указывать на потерю теплопередачи из-за загрязнения. Определяют перепады давления между входом и выходом теплообменника. Показывают снижение, которое может быть вызвано накоплением загрязняющего материала в трубах и пластинах. Очистка необходима для поддержания эффективности теплообменника. Оборудование для очистки на месте (CIP) обеспечивает циркуляцию чистящих химикатов и ополаскивателей для промывки внутренних поверхностей теплообменников без их разборки. Правильный расход обеспечивает эффективное механическое действие жидкостей при очистке. Некоторые производители рекомендуют минимальную скорость 1 фут/сек на пластинах теплообменника, но требования зависят от производителя. В некоторых случаях может потребоваться повышенный расход — например, при стерилизации молока и обработке вязких жидкостей или жидкостей, содержащих частицы. Очистка накипи или накипи представляет собой процесс удаления карбоната кальция, сульфата кальция или силикатов с поверхностей пластин. Чистящие средства должны быть совместимы как с листовым металлом, так и с составом прокладок. Для пластин из титана и нержавеющей стали никогда не используйте соляную кислоту. Осадок чаще всего состоит из оксидов металлов, ила, глинозема, двухатомных организмов и их экскрементов. Отложения накапливаются, потому что тепло высвобождает минералы и другие частицы из жидкостей во время циклов обработки, и они оседают и откладываются на теплопередающих поверхностях. Никогда не используйте соляную кислоту с пластинами из нержавеющей стали или титана, поскольку кислота вызывает общую коррозию, точечную коррозию и коррозионное растрескивание под напряжением . При использовании теплообменников для повышения температуры обработанных пищевых продуктов может произойти биологический рост, такой как бактерии, нематоды и простейшие. Производители могут предоставить более подробную информацию об очистке и стерилизации конкретного оборудования. Операторы CIP обычно выполняют четыре этапа процесса химической очистки: Базовый процесс безразборной мойки — это работа одного человека, которая включает Кожухотрубчатые теплообменники работают при сравнительно низких внутренних скоростях жидкости, поэтому они более подвержены загрязнению, чем пластинчатые теплообменники. Чистящие химикаты зависят от тех же переменных, что и для пластинчато-рамного теплообменника, и чистящие составы должны быть совместимы с металлургией теплообменника. Во время всех процессов очистки операторы должны использовать надлежащее защитное снаряжение, такое как защитная обувь, защитные перчатки и средства защиты глаз, чтобы избежать травм. ~ Мелисса Фрайер, менеджер по развитию бизнеса систем теплообмена в санитарных целях, Альфа Лаваль Хотя загрязнение нельзя предотвратить на 100%, несколько шагов могут увеличить интервалы между техническим обслуживанием. Более шероховатые поверхности увеличивают загрязнение из-за сбора частиц, поэтому выбирайте теплообменники, изготовленные из 304, 316 или коррозионностойких пластин, труб и трубок. Установите рекомендуемые производителем режимы очистки для предотвращения чрезмерного накопления частиц. Поддержание равномерного и постоянного потока технологических жидкостей через поверхности теплопередачи обычно приводит к меньшему загрязнению за счет предотвращения прилипания и накопления частиц. Частицы, взвешенные в технологических жидкостях, склонны осаждаться в областях с низкой скоростью, особенно там, где скорость быстро меняется. Обратная промывка использует клапан, который меняет направление потока жидкости через теплообменник для вытеснения твердых частиц на входе теплообменника. Портовой фильтр предотвращает даже попадание частиц в устройство, что снижает степень загрязнения. Это руководство предназначено для переработчиков, руководителей производства и инженеров-механиков, чтобы помочь им в процессе выбора теплообменника. Руководство по выбору правильного теплообменника Прочесть руководство Как вы уже знаете, загрязнение теплообменников может привести к ухудшению теплопередачи, сопротивлению потоку и падению давления, что может сделать правильный выбор для вашего процесса жизненно важным. Мы здесь, чтобы помочь! Чтобы получить запасные части для поддержания работы ваших текущих установок, прямую замену изношенного или неэффективного теплообменника или новую установку для нового процесса, свяжитесь с CSI сегодня по телефону 417-831-1411 . Наша команда обслуживания клиентов, инженеры, дизайнеры и специалисты по продуктам предлагают решения с использованием широкого спектра брендов, технологий и возможностей. Причины загрязнения теплообменников
Ключевые факторы загрязнения
Чтобы помочь контролировать загрязнение, операторы обращают внимание на четыре ключевых фактора обработки:
Скорость жидкости
Температура жидкости
Химия жидкостей
Материалы изготовления
Пластины, трубы и теплообменники целиком могут быть изготовлены из нержавеющей стали AISI 304 или AISI 316L.
Как обнаружить загрязнение теплообменников
Преобразователи температуры
Датчики давления
Расходомеры
Очистка теплообменника
Важность расхода при очистке
Во время очистки стороны продукта скорость потока всегда должна быть как минимум такой же, как скорость потока продукции.
Используемые чистящие средства по назначению
Накипь, образование накипи
Кроме того, никогда не используйте воду с содержанием хлора более 300 частей на миллион при приготовлении чистящих растворов. В каждом случае, когда нельзя избежать хлорирования нетитанового оборудования, проконсультируйтесь с поставщиком оборудования.
Удаление осадка
Удаление биологического обрастания
Удаление нароста требует такого же внимания к составу пластины и прокладки, как и удаление накипи.
Основы химической очистки
9004 5 Рекомендуемые ограничения для чистящих растворов
Процесс безразборной мойки для пластинчатых и рамных теплообменников
Очистка кожухотрубных теплообменников
Для поддержания эффективной работы и более высоких коэффициентов передачи поддерживайте чистоту поверхностей теплообмена кожуха и трубы.
Как предотвратить засорение теплообменников
Наилучший способ уменьшить засорение состоит в том, чтобы не допустить его, в первую очередь, путем использования теплообменника, размер которого соответствует применению, обеспечивая адекватные скорости, площадь поверхности и разность температур.
Для достижения устойчивости к обрастанию необходимо обратить внимание на:
Материал поверхностей
Постоянный поток
Обратная промывка
Портовая фильтрация
Руководство по выбору правильного теплообменника
Следующие шаги
Соавтор
Мелисса Фрайер (Melissa Fryer) — менеджер по развитию бизнеса в области санитарного теплообмена в группе Альфа Лаваль, занимающейся теплообменом пищевых продуктов. Мелисса получила степень бакалавра. имеет степень в области химического машиностроения Государственного университета Нью-Йорка в Буффало и обладает более чем 25-летним опытом определения, расчета и устранения неполадок теплообменников на рынке продуктов питания, напитков и молочных продуктов. Мелисса фокусируется на инженерных решениях для удовлетворения потребностей клиентов и обладает обширными знаниями и страстью к этой отрасли.
О CSI
Компания Central States Industrial Equipment (CSI) является лидером в области дистрибьюции гигиенических труб, клапанов, фитингов, насосов, теплообменников и расходных материалов для техобслуживания для гигиеничных промышленных процессоров с четырьмя распределительными предприятиями в США.