Длинноходные и короткоходные моторы – в чем разница, и какие лучше?
- Главная
- Статьи
- Длинноходные и короткоходные моторы – в чем разница, и какие лучше?
Автор: Борис Игнашин
Признайтесь, что вы часто видели в тест-драйвах фразы про «типично короткоходный характер мотора» и не вполне понимали, о чем идет речь. Сегодня мы наконец расскажем, что такое коротко- и длинноходные моторы, в чем разница подходов к проектированию двигателей, и почему сейчас можно уверенно сказать, что «длинноходники» все-таки победили.
Средняя скорость, и какой она бывает
Для понимания вопроса придется вспомнить немного о конструкции ДВС и принципах его работы. Вы наверняка знаете, что в основе любой конструкции двигателя внутреннего сгорания лежит воздействие расширяющихся газов на поршень. Поршни могут быть любой формы и размеров, но у любого поршня есть такой параметр, как средняя скорость, и от нее зависит очень и очень многое.
Средняя скорость поршня – это величина, которую можно определить по формуле Vp = Sn/30, где S – ход поршня, м; n – частота вращения, мин-1. И именно она определяет степень возможного форсирования двигателя по оборотам, ускорения элементов шатунно-поршневой группы во время работы, а также его механический КПД.
От средней скорости поршня зависят нагрузки на стенку поршня, на поршневой палец, шатун и коленвал. Причем зависимость эта квадратичная: с увеличением скорости (Vp) в два раза нагрузки увеличиваются в четыре раза, а если в три – то в девять раз.
Эксперименты инженеров-мотористов уже очень давно доказали, что классическая конструкция шатунно-поршневой группы выдерживает максимальную скорость порядка 17-23 м/с. И чем выше эта величина, тем скорее изнашивается мотор. Увеличить скорость поршня практически невозможно – самые облегченные гоночные двигатели Формулы-1 имели скорость порядка 23-25 м/с, и это безумно много.
От теории – к практике. Как известно, мощность мотора – это производная от крутящего момента, помноженного на обороты (об этом я писал большую статью с таблицами и графиками). То есть, если мы хотим получить больше мощности, то надо увеличивать обороты. А так как скорость поршня ограничена, то у нас не остается другого выбора, кроме как уменьшить его ход. Чем меньше расстояние нужно пройти поршню за один оборот, тем меньше может быть его скорость.
Короткоходные, длинноходные и «квадратные» моторы
Казалось бы, выше мы только что озвучили два прекрасных аргумента для максимального уменьшения хода поршня. К тому же, чем меньше ход поршня, тем больше диаметр цилиндра при том же объеме, и тем более крупные клапаны можно поставить. Улучшается газообмен, а значит, и работа мотора в целом… Но, как оказалось, безмерно уменьшать ход тоже нельзя.
Чем меньше ход, тем больше должен быть диаметр цилиндра, если мы хотим сохранить объем. А вот форма камеры сгорания с ростом диаметра цилиндра ухудшается, соотношение объема камеры и площади неизбежно растет, увеличивается коэффициент остаточных газов, возрастают тепловые потери, ухудшается сгорание топлива… КПД падает, склонность к детонации повышается, ухудшаются экономичность и экологичность.
При уменьшении хода поршня снижается, к тому же, и диаметр кривошипа коленчатого вала, а значит, уменьшается крутящий момент мотора. Ухудшаются и массогабаритные параметры двигателей – они становятся куда крупнее в горизонтальном сечении. К тому же для сохранения рабочего объема приходится увеличивать число цилиндров, а это уже ведет к резкому повышению сложности конструкции. В общем, нужен был компромисс.
Основные задачи проектирования моторов решили к 60-м годам прошлого века, тогда же нащупали пределы прочности конструкции по средней скорости поршня. Стало ясно, что оптимальные параметры мощности, общего КПД и габаритов у атмосферного мотора получаются в том случае, если диаметр цилиндра равен ходу поршня или чуть меньше.
Если они совпадают, то такие моторы еще называют «квадратными». Моторы, у которых диаметр цилиндра все-таки больше хода поршня, называют короткоходными, а те, у которых он меньше, – длинноходными.
Внимательный читатель скажет: стоп, а откуда вообще взялись короткоходные моторы, если эксперименты доказали, что эффективнее всего «квадратные» или чуть-чуть длинноходные?! Все просто: короткоходники получили распространение в автоспорте. Там расход топлива и приемистость на низких оборотах не сильно «делали погоду», и можно было пожертвовать КПД ради достижения большей мощности на высоких оборотах при сохранении малого рабочего объема.
Для получения лучшей топливной экономичности, тяги и чистоты выхлопа, наоборот, ход поршня увеличивали, жертвуя оборотами и максимальной мощностью. Длинноходные моторы применяли там, где были нужны тяга и экономичность.
Тем временем, к 80-м годам среднюю скорость поршня в серийных моторах довели до предела в 18 м/с, дальше ее увеличивать не получалось. Такая ситуация сохранилась до 90-х, когда требования к массогабаритным и экономическим характеристикам моторов резко возросли.
Длинноходный прогресс
90-е годы – это в первую очередь массовое внедрение новых экологических норм, резкое повышение массы кузова автомобилей из-за новых требований по пассивной безопасности, а заодно и возросшие требования к габаритам и экономичности силовых агрегатов. Машины становились просторнее изнутри и безопаснее во всех смыслах.
А двигателям приходилось поспевать за прогрессом. Массовый переход на многоклапанные головки блоков цилиндров повысил мощность и сделал моторы чище. Средний рабочий объем мотора постарались уменьшить и тем самым выиграть в расходе топлива и габаритах. Прогресс в области конструирования поршневой группы позволил уменьшить высоту поршня и увеличить длину шатуна, сделав больше механический КПД мотора.
Следовательно, стало возможно перейти к более длинноходным конструкциям, которые при том же рабочем объеме были компактнее, имели больший крутящий момент и к тому же стали экономичнее. Облегчение поршневой группы позволило снизить нагрузки на нее при высоких оборотах, а массовое внедрение турбонаддува и регулируемого впуска – еще и выиграть в максимальной мощности и тяге. Умеренно длинноходные моторы от этого только выиграли.
В 2000-е в стане двигателей объемом от 2 литров наметился перелом в переходе от «квадратов» к длинноходным конструкциям. И вот вам несколько примеров. При рабочем объеме 2 литра моторы VW серии ЕА888 (стоят на множестве моделей концерна от Skoda Octavia до Audi A5) имеют ход поршня 92,8 мм при диаметре цилиндра 82,5, а 2-литровые моторы Renault серии F4R (более всего известный по Duster) – 93 мм и 82,7 соответственно. Моторы Toyota объемом 1,8 л серии 1ZZ (Corolla, Avensis и др.) – еще более длинноходные, их размерность 91,5х79.
На фото: двигатель Volkswagen Golf GTIРабочие обороты таких двигателей заметно уменьшились, особенно у турбонаддувных, снизились и обороты максимальной мощности. А значит и снижение механического КПД уже не столь важно, зато преимущества налицо. По габаритам моторы лишь немного больше «классических» 1,6 из недавнего прошлого, а по тяге и расходу топлива намного превосходят однообъемных предшественников.
В современных моторах пытаются сочетать высокую эффективность работы длинноходных моторов и повышенный механический КПД короткоходных. Так, в ультрасовременном (но тем не менее уже снимаемом с производства) моторе BMW серии N20В20 (стоят на 1-й, 3-й, 5-й сериях, X1 и X3) применяется несимметричная поршневая группа, в которой ось коленчатого вала и ось поршневых пальцев смещены относительно оси цилиндров. Тут используются регулируемый маслонасос, плазменное напыление цилиндров, бездроссельный впуск и прочие технические «фокусы» для снижения механических потерь и сопротивления впуска. Размерность этого длинноходного мотора 90,1х84, и никто не скажет, что у него плохие характеристики хоть в чем-то, кроме надежности.
Дизели
Дизельные моторы, которые в силу особенностей рабочего цикла обычно являются длинноходными и низкооборотными, выиграли вдвойне. Внедрение турбонаддува резко подняло крутящий момент и позволило снизить степень сжатия, а прогресс топливной аппаратуры и поршневой группы – еще и увеличить рабочие обороты.
В итоге дизели превзошли по литровой мощности атмосферные бензиновые моторы, а по крутящему моменту – бензиновые моторы с наддувом. Так, двигатели серии N57 (3-я, 5-я, 7-я серии, X3, X5 и др.) от BMW при диаметре цилиндра 84 мм и ходе поршня 90 мм имеют рабочий объем 2,993 литра, мощность до 381 л. с. и 740 Нм крутящего момента. Средняя скорость поршня при этом – 13,2 метра в секунду.
Оборотная сторона
Конечно же, беспроигрышных лотерей не бывает, и чудесной высокой отдачи добились ценой надежности – тут нет никакого секрета. Старый принцип актуален и поныне: у «сильно длинноходных» моторов высокая средняя скорость поршня увеличивает нагрузку на стенки цилиндра.
Конечно же, материалы становятся лучше, но при сравнении двигателей одной серии с разными параметрами хода поршня и диаметра цилиндра заметно, что длинноходные модели более склонны к износу поршневых колец и задирам цилиндров. И ресурс поршневой у них оказывается существенно ниже, чем у более «квадратных» собратьев.
А вот при сравнении разных моторов все далеко не так однозначно. На моторах с алюминиевым блоком и алюсиловым покрытием стараются снизить нагрузку на стенку цилиндра в том числе и снижением хода поршня, но, как правило, все равно ресурс получается меньше, чем у моторов с чугунными гильзами или блоком.
Мотор Renault-Nissan серии M4R (Qashqai, Fluence и др.), который пришел на смену уже упомянутому чугунному F4R, имеет ход поршня 90,1 мм при диаметре цилиндра 84 – он все еще длинноходный, но ход поршня значительно сократился. Габариты при этом не увеличиваются за счет более тонкостенной конструкции блока цилиндров.
На фото: двигатель Renault LatitudeСовременные двигатели не нуждаются в высоких оборотах для достижения высокой мощности, а экономичность и экологичность становятся все важнее. Пусть даже в реальной эксплуатации заявленные характеристики и не подтверждаются… К тому же, можно путем усложнения конструкции обойти множество ограничений, которые десятки лет заставляли делать выбор между мощностью и экономичностью моторов.
Короткоходные «крутильные» моторы просто вымирают, им нет места в новом мире. Даже в Формуле-1 отказались от экстремальных конструкций с рабочими оборотами за 19 тысяч и соотношением диаметра цилиндра и хода поршня больше 2,4 к 1. Конечно, для фанатов и гоночных серий выпуск подобной техники сохранится, но в практическом плане смысла в ней уже нет. Победа длинноходных конструкций, за редким исключением, фактически состоялась.
Одним из немногих «оплотов короткоходности» до недавнего времени оставались атмосферные V6 и V8 от Mercedes-Benz. Так, моторы серии М272 (E-Klasse W211, M-Class W164 и др.) – откровенно короткоходные во всех вариантах исполнения. Например, у 3-литровой версии соотношение хода к диаметру будет 82,1 к 88. Как и их предки в лице М104, так и их наследники вплоть до М276, они были олицетворением успешных короткоходных моторов. Компания не стремилась к излишней компактности моторов, места было достаточно, а момента у двигателей объемом 3-3,5 литра и так хватало с запасом. Городить длинноходную конструкцию не было смысла.
Но новое поколение двигателей AMG серий М133/М176 с наддувом стали длинноходными – 83х92 мм, как и перспективная рядная шестерка 3,0 с наддувом серии М256 – 83х92,4 мм.
На фото: двигатель Mercedes-AMG CLA 45 4MATICИз «могикан» остаются разве что моторы GM, их блок V8 6,2 Vortec/L86/LT1 все еще не стремится к компактности, имея размерность 103,25х92 мм, и даже компрессорная версия LT4 сохраняет ту же размерность блока. Но это, скорее всего, тоже ненадолго.
Конец спорам
Даунсайз, наддув, непосредственный впрыск, гладкая моментная характеристика, высокий крутящий момент, регулируемый ГРМ и продвинутые трансмиссии сотворили маленькое чудо. Споры «длинноходный или короткоходный» уже более не актуальны.
Моторы вдруг прибавили в литровой мощности до границ, ранее считавшихся возможными только для специально подготовленных гоночных моторов. Увидев цифры в 120-150 л. с. с литра объема, мы уже не удивляемся, и даже 200 л. с. на литр кажутся вполне реальными, а «смешной» паспортный расход топлива для мощной и тяжелой машины кажется вполне реальным. Дизельные двигатели из «гадких утят» превратились в прекрасных лебедей с литровой мощностью даже большей, чем у бензиновых двигателей.
Во многом все это, плюс уменьшение габаритов и веса моторов, стало возможным благодаря длинноходной конструкции. Окончательно оформившийся тренд вряд ли переломится, особенно с учетом прогнозируемого вытеснения ДВС электромоторами и разнообразными «удлинителями дистанции».
практика
Новые статьи
Статьи / Практика
Снижаем октан: действительно ли можно ли ездить на 95-м бензине вместо 98-го
В Сети можно найти немало случаев, когда «серьёзный технический эксперт» утверждает, что нет ничего страшного в том, чтобы в целях экономии ездить на бензине, октановое число которого чуть н…
2328
0
1
23.
Статьи / Популярные вопросы Как оформить ДТП по европротоколу через Госуслуги Мы уже рассказывали о том, как оформить ДТП по европротоколу, а также о том, что с 2019 года стало возможным оформить европротокол даже при наличии разногласий о причинах и виновнике у уча… 250 0 1 21.09.2022
Статьи / Интересно
Премия «Автомобиль года» как зеркало состояния автомобильного рынка
Буквально только что, на прошлой неделе, были объявлены итоги очередного конкурса «Автомобиль года». Казалось бы, какой «автомобиль года», если весь автомобильный рынок поражен тяжелейшим кр…
907
0
1
19. 09.2022
Популярные тест-драйвы
Тест-драйвы / Тест-драйв Полный привод, самый мощный мотор и силы в запасе: первый тест Chery Tiggo 8 PRO MAX Появление в российской линейке Chery модели Tiggo 8 PRO MAX можно назвать знаковым для бренда. Почему? Да хотя бы потому, что это первый с 2014 года полноприводный кроссовер Chery, приехавши… 18347 13 44 29.04.2022
Тест-драйвы / Тест-драйв
Haval Dargo против Mitsubishi Outlander: собака лает, чужестранец идет
В дилерском центре Haval на юге Москвы жизнь кипит: покупатели разглядывают машины, общаются с менеджерами и подписывают какие-то бумаги. Пока я ждал выдачи тестового Dargo, такой же кроссов…
10929
6
82
13.
Тест-драйвы / Тест-драйв Мотор от Mercedes, эмблема от Renault, сборка от Dacia: тест-драйв европейского Logan 1,0 Казалось бы, что нового можно рассказать про Renault Logan второго поколения, известный каждому российскому таксисту, что называется, вдоль и поперёк? Однако конкретно в этом автомобиле есть… 10190 10 41 13.08.2022
какие существуют двигатели внутреннего сгорания
Двигатель внутреннего сгорания: устройство и принципы работы
04.04.2017
Двигателем внутреннего сгорания называется разновидность тепловой машины, которая преобразует энергию, содержащуюся в топливе, в механическую работу. В большинстве случае используется газообразное или жидкое топливо, полученное путем переработки углеводородов.
Двигатели внутреннего сгорания имеют ряд недостатков. К ним относятся следующие:
- сравнительно большие массогабаритные показатели затрудняют их перемещение и сужают сферу использования;
- высокий уровень шума и токсичные выбросы приводят к тому, что устройства, работающие от двигателей внутреннего сгорания, могут лишь со значительными ограничениями использоваться в закрытых, плохо вентилируемых помещениях;
- сравнительно небольшой эксплуатационный ресурс вынуждает довольно часто ремонтировать двигатели внутреннего сгорания, что связано с дополнительными затратами;
- выделение в процессе работы значительного количества тепловой энергии обуславливает необходимость создания эффективной системы охлаждения;
- из-за многокомпонентной конструкции двигатели внутреннего сгорания сложны в производстве и недостаточно надежны;
- данный вид тепловой машины отличается высоким потреблением горючего.
Несмотря на все перечисленные недостатки двигатели внутреннего сгорания пользуются огромной популярностью, в первую очередь – благодаря своей автономности (она достигается за счет того, что топливо содержит в себе значительно большее количество энергии по сравнению с любой аккумуляторной батареей). Одной из основных областей их применения является личный и общественный транспорт.
Типы двигателей внутреннего сгорания
Когда речь идет о двигателях внутреннего сгорания, следует иметь в виду, что на сегодняшний день существует несколько их разновидностей, которые отличаются друг от друга конструктивными особенностями.
1. Поршневые двигатели внутреннего сгорания характеризуются тем, что сгорание топлива происходит в цилиндре. Именно он отвечает за преобразование той химической энергии, которая содержится в горючем, в полезную механическую работу. Чтобы добиться этого, поршневые двигатели внутреннего сгорания оснащаются кривошипно-ползунным механизмом, с помощью которого и происходит преобразование.
Поршневые двигатели внутреннего сгорания принято делить на несколько разновидностей (основанием для классификации служит используемое ими топливо).
В бензиновых карбюраторных двигателях образование топливовоздушной смеси происходит в карбюраторе (первый этап). Далее в дело вступают распыляющие форсунки (электрические или механические), местом расположения которых служит впускной коллектор. Готовая смесь бензина и воздуха поступает в цилиндр.
Там происходит ее сжатие и поджиг с помощью искры, которая возникает при прохождении электричества между электродами специальной свечи. В случае с карбюраторными двигателями топливовоздушной смеси присуща гомогенность (однородность).
Бензиновые инжекторные двигатели используют в своей работе иной принцип смесеобразования. Он основан на непосредственном впрыске горючего, которое напрямую поступает в цилиндр (для этого используются распыляющие форсунки, называемые также инжектором). Таким образом, образование топливовоздушной смеси, как и ее сгорание, осуществляется непосредственно в самом цилиндре.
Дизельные двигатели отличаются тем, что используют для своей работы особую разновидность топлива, называемую «дизельное» или просто «дизель». Для его подачи в цилиндр используется высокое давление. По мере того, как в камеру сгорания подаются все новые порции горючего, прямо в ней происходит процесс образования топливовоздушной смеси и ее моментальной сгорание. Поджиг топливовоздушной смеси происходит не с помощью искры, а под действием нагретого воздуха, который подвергается в цилиндре сильному сжатию.
Топливом для газовых двигателей служат различные углеводороды, которые при нормальных условиях пребывают в газообразном состоянии. Из этого следует, что для их хранения и использования требуется соблюдать особые условия:
- Сжиженные газы поставляются в баллонах различного объема, внутри которых с помощью насыщенных паров создается достаточное давление, но не превышающее 16 атмосфер. Благодаря этому горючее находится в жидком состоянии. Для его перехода в пригодную для сжигания жидкую фазу используется специальное устройство, называемое испарителем.
Понижение давления до уровня, который примерно соответствует нормальному атмосферному давлению, осуществляется в соответствии со ступенчатым принципом. В его основе лежит использование так называемого газового редуктора. После этого топливовоздушная смесь поступает во впускной коллектор (перед этим она должна пройти через специальный смеситель). В конце этого достаточно сложного цикла горючее подается в цилиндр для последующего поджига, осуществляемого с помощью искры, которая возникает при прохождении электричества между электродами специальной свечи.
- Хранение сжатого природного газа осуществляется при гораздо более высоком давлении, которое находится в диапазоне от 150 до 200 атмосфер. Единственное конструктивное отличие данной системы от той, что описана выше, заключается в отсутствии испарителя. В целом принцип остается тем же.
Генераторный газ получают путем переработки твердого топлива (угля, горючих сланцев, торфа и т.п.). По своим основным техническим характеристикам он практически ничем не отличается от других видов газообразного топлива.
Газодизельные двигатели
Данная разновидность двигателей внутреннего сгорания отличается тем, что приготовление основной порции топливовоздушной смеси осуществляется аналогично газовым двигателям. Однако для ее поджига используется не искра, получаемая при помощи электрической свечи, а запальная порция топлива (ее впрыск в цилиндр осуществляется тем же способом, как и в случае с дизельными двигателями).
Роторно-поршневые двигатели внутреннего сгорания
К данному классу относится комбинированная разновидность данных устройств. Ее гибридный характер находит свое отражение в том, что конструкция двигателя включает в себя сразу два важных конструктивных элемента: роторно-поршневую машину и одновременно — лопаточную машину (она может быть представлена компрессором, турбиной и т.д.). Обе упомянутых машины на равных принимают участие в рабочем процессе. В качестве характерного примера таких комбинированных устройств можно привести поршневой двигатель, оснащенный системой турбонаддува.
Особую категорию составляют двигатели внутреннего сгорания, для обозначения которых используется английская аббревиатура RCV. От других разновидностей они отличаются тем, что газораспределение в данном случае основывается на вращении цилиндра. При совершении вращательного движения топливо по очереди проходит выпускной и впускной патрубок. Поршень отвечает за движение в возвратно-поступательном направлении.
Поршневые двигатели внутреннего сгорания: циклы работы
Для классификации поршневых двигателей внутреннего сгорания также используется принцип их работы. По данному показателю двигатели внутреннего сгорания делятся на две большие группы: двух- и четырехтактные.
Четырехтактные двигатели внутреннего сгорания используют в своей работе так называемый цикл Отто, который включает в себя следующие фазы: впуск, сжатие, рабочий ход и выпуск. Следует добавить, что рабочий ход состоит не из одного, как остальные фазы, а сразу из двух процессов: сгорание и расширение.
Наиболее широко применяемая схема, по которой осуществляется рабочий цикл в двигателях внутреннего сгорания, состоит из следующих этапов:
1. Пока происходит впуск топливовоздушной смеси, поршень перемещается между верхней мертвой точкой (ВМТ) и нижней мертвой точкой (НМТ). В результате этого внутри цилиндра освобождается значительное пространство, в которое и поступает топливовоздушная смесь, заполняя его.
Всасывание топливовоздушной смеси осуществляется за счет разности давления, существующего внутри цилиндра и во впускном коллекторе. Толчком к поступлению топливовоздушной смеси в камеру сгорания служит открытие впускного клапана. Этот момент принято обозначать термином «угол открытия впускного клапана» (φа).
При этом следует иметь в виду, что в цилиндре на этот момент уже содержаться продукты, оставшиеся после сгорания предыдущей порции горючего (для их обозначения используется понятие остаточных газов). В результате их смешения с топливовоздушной смесью, называемой на профессиональном языке свежим зарядом, образуется рабочая смесь. Чем успешнее протекает процесс ее приготовления, тем более полно сгорает топливо, выделяя при этом максимум энергии.
В результате растет кпд двигателя. В связи с этим еще на этапе конструирования двигателя особое внимание уделяется правильному смесеобразованию. Ведущую роль играют различные параметры свежего заряда, включая его абсолютную величину, а также удельную долю в общем объеме рабочей смеси.
2. При переходе к фазе сжатия оба клапана закрываются, а поршень совершает движение в обратном направлении (от НМТ к ВМТ). В результате надпоршневая полость заметно уменьшается в объеме. Это приводит к тому, что содержащаяся в ней рабочая смесь (рабочее тело) сжимается. За счет этого удается добиться того, что процесс сгорания топливовоздушной смеси протекает более интенсивно. От сжатия также зависит такой важнейший показатель, как полнота использования тепловой энергии, которая выделяется при сжигании горючего, а следовательно – и эффективность работы самого двигателя внутреннего сгорания.
Для увеличения этого важнейшего показателя конструкторы стараются проектировать устройства, обладающие максимально возможной степенью сжатия рабочей смеси. Если мы имеем дело с ее принудительным зажиганием, то степень сжатия не превышает 12. Если же двигатель внутреннего сгорания работает на принципе самовоспламенения, то упомянутый выше параметр обычно находится в диапазоне от 14 до 22.
3. Воспламенение рабочей смеси дает старт реакции окисления, которая происходит благодаря кислороду воздуха, входящему в ее состав. Этот процесс сопровождается резким ростом давления по всему объему надпоршневой полости. Поджиг рабочей смеси осуществляется при помощи электрической искры, которая имеет высокое напряжение (до 15 кВ).
Ее источник располагается в непосредственной близости от ВМТ. В этой роли выступает электрическая свеча зажигания, которую вворачивают в головку цилиндра. Однако в том случае, если поджиг топливовоздушной смеси осуществляется посредством горячего воздуха, предварительно подвергнутого сжатию, наличие данного конструктивного элемента является излишним.
Вместо него двигатель внутреннего сгорания оснащается особой форсункой. Она отвечает за поступление топливовоздушной смеси, которая в определенный момент подается под высоким давлением (оно может превышать 30 Мн/м²).
4. При сгорании топлива образуются газы, которые имеют очень высокую температуру, а потому неуклонно стремятся к расширению. В результате поршень вновь перемещается от ВМТ к НМТ. Это движение называется рабочим ходом поршня. Именно на этом этапе происходит передача давления на коленчатый вал (если быть точнее, то на его шатунную шейку), который в результате проворачивается. Этот процесс происходит при участии шатуна.
5. Суть завершающей фазы, которая называется впуском, сводится к тому, что поршень совершает обратное движение (от НМТ к ВМТ). К этому моменту открывается второй клапан, благодаря чему отработавшие газы покидают внутреннее пространство цилиндра. Как уже говорилось выше, части продуктов сгорания это не касается. Они остаются в той части цилиндра, откуда поршень их не может вытеснить. За счет того, что описанный цикл последовательно повторяется, достигается непрерывный характер работы двигателя.
Если мы имеем дело с одноцилиндровым двигателем, то все фазы (от подготовки рабочей смеси до вытеснения из цилиндра продуктов сгорания) осуществляется за счет поршня. При этом используется энергия маховика, накапливаемая им в течение рабочего хода. Во всех остальных случаях (имеются в виду двигатели внутреннего сгорания с двумя и более цилиндрами) соседние цилиндры дополняют друг друга, помогая выполнять вспомогательные ходы. В связи с этим из их конструкции без малейшего ущерба может быть исключен маховик.
Чтобы было удобнее изучать различные двигатели внутреннего сгорания, в их рабочем цикле вычленяют различные процессы. Однако существует и противоположный подход, когда сходные процессы объединяют в группы. Основой для подобной классификации служит положение поршня, которое он занимает в отношении обеих мертвых точек. Таким образом, перемещения поршня образуют тот отправной пункт, отталкиваясь от которого, удобно рассматривать работу двигателя в целом.
Важнейшим понятием является «такт». Им обозначают ту часть рабочего цикла, которая укладывается во временной промежуток, когда поршень перемещается от одной смежной мертвой точки к другой. Такт (а вслед за ним и весь соответствующий ему ход поршня) называется процессом. Он играет роль основного при перемещении поршня, которое происходит между двумя его положениями.
Если переходить к тем конкретным процессам, о которых мы говорили выше (впуск, сжатие, рабочий ход и выпуск), то каждый из них четко приурочен к определенному такту. В связи с этим в двигателях внутреннего сгорания принято различать одноименные такты, а вместе с ними – и ходы поршня.
Выше мы уже говорили о том, что наряду с четырехтактными существуют и двухтактные двигатели. Однако независимо от количества тактов рабочий цикл любого поршневого двигателя состоит из пяти упомянутых выше процессов, а в его основе лежит одна и та же схема. Конструктивные особенности в данном случае не играют принципиальной роли.
Дополнительные агрегаты для двигателей внутреннего сгорания
Важный недостаток двигателя внутреннего сгорания заключается в достаточно узком диапазоне оборотов, в котором он способен развивать значительную мощность. Чтобы компенсировать этот недостаток, двигатель внутреннего сгорания нуждается в дополнительных агрегатах. Самые важные из них – стартер и трансмиссия.
Наличие последнего устройства не является обязательным условием лишь в редких случаях (когда, к примеру, речь идет о самолетах). В последнее время все привлекательнее становится перспектива создать гибридный автомобиль, чей двигатель мог бы постоянно сохранять оптимальный режим работы.
К дополнительным агрегатам, обслуживающим двигатель внутреннего сгорания, относится топливная система, которая осуществляет подачу горючего, а также выхлопная система, необходимая для того, чтобы отводить отработавшие газы.
Каждому, водителю интересно и необходимо знать, как устроен автомобиль, что такое ДВС в машине, из чего состоит двигатель автомобиля и каков у ДВС ресурс.
Отличие двигателей внутреннего сгорания от двигателей внешнего сгорания
ДВС называется так именно потому, что топливо сжигается внутри рабочего органа (цилиндра), промежуточный теплоноситель, например пар, здесь не нужен, как это организовано в паровозах. Если рассматривать паровой двигатель и двигатель, но уже внутреннего сгорания автомобиля, устройство их сходно, это очевидно (на рисунке справа паровой двигатель, слева – ДВС).
Принцип работы одинаков: на поршень, действует какая-то сила. От этого поршень вынужден двигаться вперед или назад (возвратно-поступательно). Эти движения при помощи специального механизма (кривошипного) преобразуются во вращение (колеса у паровоза и коленчатого вала «коленвала» у автомобиля). В двигателях внешнего сгорания нагревается вода, превращаясь в пар, и уже этот пар совершает полезную работу толкая поршень, а в ДВС мы нагреваем воздух внутри (непосредственно в цилиндре)и он (воздух) двигает поршень. От этого коэффициент полезного действия, у ДВС, конечно, выше.
История создания ДВС
История гласит, что первый работающий двигатель внутреннего сгорания коммерческого использования, то есть выпускаемый для продажи, был разработан французским изобретателем Ленуаром. Его двигатель работал на светильном газе в смеси с воздухом. Причем именно он догадался поджигать эту смесь путем электрической искры. Только в 1864 году документально зафиксирована продажа более 310 таких двигателей. На этом он разбогател. Жан Этьен Ленуар потерял интерес к изобретательству и вскоре(в 1877 году) его моторы были вытеснены более совершенными, на тот момент, двигателями Отто, изобретателя из Германии. Донат Банки (венгерский инженер) в 1893 году произвел настоящую революцию в двигателестроении. Он изобрел карбюратор. С этого момента история не знает бензиновых двигателей без этого устройства. И так продолжалось около 100 лет. На смену ему пришла система непосредственного впрыска, но это уже новейшая история.
Все первые двигатели внутреннего сгорания были только одноцилиндровыми. Увеличение мощности велось путем увеличения диаметра рабочего цилиндра. Только к концу 19-го века появились ДВС с двумя цилиндрами, а в начале 20-го века – четырехцилиндровые. Теперь, повышение мощности производилось уже путем увеличения числа цилиндров. На сегодняшний день можно встретить автомобильный двигатель в 2-мя, 4-мя, 6-ю цилиндрами. Реже 8 и 12. Некоторые спортивные автомобили имеют 24 цилиндра. Расположение цилиндров может быть как рядным, так и V-образным.
Вопреки расхожему мнению ни Готлиб Даймлер, ни Карл Бенц, ни Генри Форд устройство двигателя автомобиля не изменяли кардинально (разве что мелкие доработки), но оказали огромное влияние в автомобилестроение как таковое. Что такое ДВС в авто мы сейчас и рассмотрим.
Общее устройство двигателя внутреннего сгорания
Итак, ДВС состоит из корпуса, в котором все остальные детали монтируются. Чаще всего это блок цилиндров.
На данном рисунке показан один цилиндр без блока. Устройство ДВС направлено на максимально комфортные условия для цилиндров, ведь именно в них производится работа. Цилиндр, это металлическая (чаще всего стальная) труба, в которой двигается поршень. Он обозначен на рисунке цифрой 7. Над цилиндром устанавливается головка цилиндра 1, в которую вмонтированы клапана (5 – впускной и 4 — выпускной), а также свеча зажигания 3 и коромысла 2.
Над клапанами 4 и 5 есть пружины, которые удерживают их в закрытом состоянии. Коромысла при помощи толкателей 14 и распределительного вала 13 открывают клапана в определенный момент (тогда, когда это необходимо). Распределительный вал с кулачками вращается от коленвала 11 через приводные шестерни 12.
Движения поршня 7 преобразуются во вращение коленвала 11 при помощи шатуна 8 и кривошипа. Этим кривошипом служит «колено» на валу (смотри рисунок), именно поэтому вал и называется коленчатым. В связи с тем, что воздействие на поршень происходит не постоянно, а только когда в цилиндре горит топливо. У ДВС есть маховик 9, довольно массивный. Маховик как бы запасает энергию вращения и отдает ее при необходимости.
В любом двигателе много трущихся деталей, для их смазывания используют автомобильное масло. Масло это хранится в картере 10 и специальным насосом подается к трущимся деталям.
Синим цветом, показаны детали кривошипно-шатунного механизма (КШМ). Голубым – смесь топлива и воздуха. Серым – свеча зажигания. Красным – выхлопные газы.
Принцип работы ДВС
Разобрав двигатель внутреннего сгорания, его устройство, необходимо уяснить, как взаимодействуют его детали, как он работает. Знать строение еще не все, а вот как взаимодействуют механизмы, в чем преимущество дизельных автомобилей и в чем их недостатки для начинающих (для чайников) очень важно.
Ничего сложного в этом нет. Пошаговым рассмотрением процессов мы постараемся рассказать, как взаимодействуют между собой основные части двигателя при работе. Из какого материала выполнены механические составляющие ДВС.
Все автомобильные двигатели работают на одном принципе: сжигание бензина или дизельного топлива. Для чего? Для получения необходимой нам энергии, конечно. Двигатели автомобилей, иногда говорят – моторы, могут быть двухтактными и четырехтактными. Тактом считается движение поршня либо вверх, либо вниз. Говорят еще от верхней мертвой точки (ВМТ), до нижней (НМТ). Мертвой эта точка называется потому, что поршень как бы замирает на мгновение и начинает движение в обратную сторону.
Итак, в двухтактном двигателе весь процесс (или цикл) происходит за 2 хода поршня, в четырехтактном – за 4. И совершенно не важно, бензиновый это двигатель, дизельный или работающий на газу.
Как ни странно, рассказывать принцип работы лучше на 4-х тактном бензиновом карбюраторном двигателе.
Первый такт — всасывание.
Поршень идет вниз и затягивает за собой смесь из воздуха и топлива. Эта смесь готовится в отдельном устройстве – в карбюраторе. При этом впускной, его еще называют «всасывающий» клапан, конечно, открыт. На рисунке он показан синим.
Следующий, второй такт – сжатие смеси.
Поршень поднимается вверх от НМТ до ВМТ. При этом растет давление и, естественно, температура над поршнем. Но этой температуры недостаточно, для того, чтобы смесь самовоспламенилась. Для этого служит свеча. Она выдает искру в нужный момент. Обычно это 6…8 угловых градусов не доходя до ВМТ. Для начала понимания процесса можно предположить, что искра зажигает смесь точно в верхней точке.
Третий такт – расширение продуктов сгорания.
При сгорании столь энергоемкого топлива, продуктов сгорания в цилиндре очень мало, а вот усилие появляется только потому, что воздух нагрелся при повышении температуры, а значит, расширился, в нашем случае увеличил давление. Именно это давление и совершает нужную работу. Нужно знать, что нагревая воздух на 273 0С, получаем увеличение давления практически в 2 раза. Температура зависит от того сколько топлива сжечь. Максимальная температура внутри рабочего цилиндра может достигать 2500 0С при работе ДВС на полной мощности.
Четвертый такт последний.
После него опять будет первый. Поршень направляется от НМТ к ВМТ. При этом выпускной клапан открыт. Цилиндр очищается, выбрасывая все что сгорело, и что не сгорело, в атмосферу.
Что касается дизельного двигателя, то все основные детали с карбюраторным практически одинаковы. Ведь и тот и другой, это двигатель внутреннего сгорания. Исключение составляет смесеобразование. В карбюраторном смесь готовится отдельно, в том самом карбюраторе. А вот в дизельном – смесь готовиться непосредственно в цилиндре, перед сжиганием. Топливо (солярка) подается специальным насосом в определенный момент времени. Зажигание смеси происходит от самовоспламенения. Температура внутри цилиндра в дизеле гораздо выше, чем в карбюраторном ДВС. По этой причине детали там детали мощнее и система охлаждения лучше. Необходимо отметить, что, несмотря на высокую температуру внутри цилиндра, рабочая температура двигателя никогда не повышается выше 90…95 0С. Иногда, детали дизельных двигателей делают из более твердого металла, что позволяет снизить массу, но увеличивает цену ДВС. Однако, коэффициент полезного действия (КПД) в дизельном двигателе выше. То есть он более экономичен и дороговизна деталей себя окупает.
У дизельного ДВС ресурс выше, если соблюдать правила эксплуатации. Особенно часто механизмы дизелей выходят из строя из-за плохого топлива.
Схема работы дизельного двигателя представлена на рисунке слева. В третьем такте подача топлива показана в момент ВМТ, хотя это и не совсем так.
Системы ДВС обеспечивающие их работоспособность практически одинаковы: система смазки, топливная система, система охлаждения и система газообмена. Есть еще несколько, но они не относятся к главным.
Глядя на устройство любого двигателя внутреннего сгорания можно подумать, что все детали выполнены из стали. Это далеко не так. Корпуса бывают и чугунные и выполненные из алюминиевого сплава, а вот поршни из чугуна не делают, они либо стальные, либо из высокопрочного алюминиевого сплава. Зная общее устройство данного двигателя внутреннего сгорания и условия работы его деталей, очевидно, что и клапана и головку цилиндра нужно делать прочными, поскольку они должны выдерживать давление внутри цилиндра более 100 атмосфер. А вот поддон, где собирается масло не несет на себе особой механической нагрузки и выполняется из тонкой листовой стали или алюминия.
Характеристики ДВС
Когда говорят об автомобиле, то обычно, в первую очередь отмечают двигатель внутреннего сгорания, не его устройство, а его мощность. Она (мощность) измеряется как обычно (по-старинке) в лошадиных силах или (по-современному) киловаттах. Безусловно, чем больше мощность, тем быстрее автомобиль набирает скорость. И в принципе экономичность тем выше, тем двигатель машины более мощный. Однако, это только тогда, когда двигатель постоянно работает на номинальных (экономически оправданных) оборотах. Но на малых скоростях (при неиспользовании полной мощности) КПД сильно падает и если на номинальных режимах дизельный двигатель имеет 40…42% КПД, то на малых только 7%. Бензиновый двигатель не может похвастаться даже этим. Использование полной мощности позволяет экономить топливо. По этой причине расход топлива на 100 километров в малолитражных автомобилях ниже. Этот показатель может составлять и 5 и даже 4 л/100 км. Расход у мощных внедорожников может составлять и 10 и даже 15 л/100 км.
Еще одним показателем для автомобилей является разгон от 0 км/час до 100 км/час. Конечно, чем мощнее двигатель, тем быстрее разгон автомобиля, но про экономичность при этом говорить вообще не приходится.
Итак, двигатель внутреннего сгорания устройство которого Вы теперь знаете, совсем не кажется сложным. И на вопрос «ДВС – что это такое?» Вы можете ответить «Это то, что я знаю».
На чтение 10 мин. Просмотров 1k. Опубликовано 17 ноября 2018
Практически все современные автомобили оснащены двигателем внутреннего сгорания , имеющим аббревиатуру ДВС. Несмотря на постоянный прогресс и сегодняшнее стремление автомобильных концернов отказаться от моторов, работающих на нефтепродуктах в пользу более экологичной электроэнергии, львиная доля машин ездит на бензине или дизельном топливе.
Основными принципом ДВС является то, что топливная смесь воспламеняется непосредственно внутри агрегата, а не вне его (как, к примеру, в тепловозах или устаревших паровозах). Такой способ имеет относительно большой коэффициент полезного действия. К тому же, если говорить об альтернативных моторах на электрической тяге, то двигатели внутреннего сгорания обладает рядом неоспоримых преимуществ.
- большой запас хода на одном баке;
- быстрая заправка;
- согласно прогнозам, уже через несколько лет энергосистемы развитых стран не будут в силах погасить потребность в электроэнергии из-за большого количества электрокаров, что может привести к коллапсу.
Классификация двигателей внутреннего сгорания
Непосредственно ДВС отличаются по своему устройству. Все моторы можно разделить на несколько самых популярных категорий в зависимости от принципа работы:
Бензиновые
Наиболее распространенная категория. Работает на главных продуктах нефтепереработки. Основным элементом в таком моторе является цилиндро-поршневая группа или ЦПГ, куда входит: коленвал, шатун, поршень, поршневые кольца и сложный газораспределительный механизм, который обеспечивает своевременное наполнение и продувку цилиндра.
Бензиновые двигатели внутреннего сгорания подразделяются на два типа в зависимости от системы питания:
- карбюраторные . Устаревшая в условиях современной реальности модель. Здесь формирование топливно-воздушной смеси осуществляется в карбюраторе, а пропорцию воздуха и бензина определяет набор жиклеров. После этого карбюратор подает ТВС в камеру сгорания. Недостатками такого принципа питания является повышенное потребление топлива и прихотливость всей системы. К тому же она сильно зависит от погоды, температуры и прочих условий.
- инжекторные или впрысковые . Принципы работы двигателя с инжектором кардинально противоположны. Здесь смесь впрыскивается непосредственно во впускной коллектор через форсунки, а затем разбавляется нужным количеством воздуха. За исправную работу отвечает электронный блок управления, который самостоятельно высчитывает нужные пропорции.
Дизельные
Устройство двигателя, работающего на дизеле, кардинально отличается от бензинового агрегата. Поджог смеси здесь происходит не благодаря свечам зажигания, дающим искру в определенный момент, а из-за высокой степени сжатия в камере сгорания. Данная технология имеет свои плюсы (больший КПД, меньшие потери мощности из-за большой высоты над уровнем моря, высокий крутящий момент) и минусы (прихотливость ТНВД к качеству топлива, большие выбросы СО2 и сажи).
Роторно-поршневые двигатели Ванкеля
Данный агрегат имеет поршень в виде ротора и три камеры сгорания, к каждой из которых подведена свеча зажигания. Теоретически ротор, движущийся по планетарной траектории, каждый такт совершает рабочий ход. Это позволяет существенно повысить КПД и увеличить мощность двигателя внутреннего сгорания. На практике это сказывается гораздо меньшим ресурсом. На сегодняшний день только автомобильная компания Mazda делает такие агрегаты.
Газотурбинные
Принцип работы ДВС такого типа заключается в том, что тепловая энергия переходит в механическую, а сам процесс обеспечивает вращение ротора, приводящего в движения вал турбины. Подобные технологии используются в авиационном строительстве.
Любой поршневой ДВС (самые распространенные в современных реалиях) имеет обязательный набор деталей. К таким частям относится:
- Блок цилиндров , внутри которого двигаются поршни и происходит сам процесс;
- ЦПГ : цилиндр, поршни, поршневые кольца;
- Кривошипно-шатунный механизм . К нему относится коленвал, шатун, «пальцы» и стопорные кольца;
- ГРМ . Механизм с клапанами, распределительными валами или «лепестками» (для 2-х тактных двигателей), который обеспечивает корректную подачу топлива в нужный момент;
- Cистемы впуска . О них говорилось выше – к ней относятся карбюраторы, воздушные фильтры, инжекторы, топливный насос, форсунки;
- Системы выпуска . Удаляет отработанные газы из камеры сгорания, а также снижает шумность выхлопа;
Принцип работы ДВС
В зависимости от своего устройства, двигатели можно разделить на четырехтактные и двухтактные. Такт – есть движение поршня от своего нижнего положения (мертвая точка НМТ) до верхнего положения (мертвая точка ВМТ). За один цикл двигатель успевает наполнить камеры сгорания топливом, сжать и поджечь его, а также очистить их. Современные ДВС делают это за два или четыре такта.
Принцип работы двухтактного ДВС
Особенностью такого мотора стало то, что весь рабочий цикл происходит всего за два движения поршня. При движении вверх создается разреженное давление, которое засасывает топливную смесь в камеру сгорания. Вблизи ВМТ поршень перекрывает впускной канал, а свеча зажигания поджигает топливо. Вторым тактом следует рабочий ход и продувка. Выпускной канал открывается после прохождения части пути вниз и обеспечивает выход отработанных газов. После этого процесс возобновляется по новой.
Теоретически, преимуществом такого мотора более высокая удельная мощность. Это логично, ведь сгорание топлива и рабочий такт происходит в два раза чаще. Соответственно, мощность такого двигателя может быть в два раза больше. Но эта конструкция имеет массу проблем. Из-за больших потерь при продувке, большого расхода топлива, а также сложностей в расчетах и «норовистой» работе двигателя, эта технология сегодня используется только на малокубатурной технике.
Интересно, что полвека назад активно велись разработки дизельного двухтактного ДВС. Процесс работы практически не отличался от бензинового аналога. Однако, несмотря на преимущества такого мотора, от него отказались из-за ряда недостатков.
Основным минусом стал огромный перерасход масла. Из-за комбинированной системы смазки топливо попадало в камеру сгорания вместе с маслом, которое потом попросту выгорало или удалялось через выпускную систему. Большие тепловые нагрузки также требовали более громоздкой системы охлаждения, что увеличивало габариты мотора. Третьим минусом стал большой расход воздуха, который вел к преждевременному износу воздушных фильтров.
Четырёхтактный ДВС
Мотор, где рабочий цикл занимает четыре хода поршня, называется четырехтактным двигателем.
- Первый такт – впуск . Поршень двигается из верхней мертвой точки. В этот момент ГРМ открывает впускной клапан, через который топливно-воздушная смесь поступает в камеру сгорания. В случае с карбюраторными агрегатами поступление может осуществляться за счет разрежения, а инжекторные двигателя впрыскивают топливо под давлением.
- Второй такт – сжатие . Далее поршень движется из нижней мертвой точки вверх. К этому моменту впускной клапан закрыт, а смесь постепенно сжимается в полости камеры сгорания. Рабочая температура поднимается до отметки 400 градусов.
- Третий такт – рабочий ход поршня . В ВМТ свеча зажигания (или большая степень сжатия, если речь идет о дизеле) поджигает топливо и толкает поршень с коленчатым валом вниз. Это основной такт во всем цикле работы двигателя.
- Четвертый такт – выпуск . Поршень снова движется вверх, выпускной клапан открывается, а из камеры сгорания удаляются отработанные газы.
Дополнительные системы ДВС
Независимо от того, из чего состоит двигатель, у него должны быть вспомогательные системы, которые способны обеспечить его исправную работу. К примеру, клапаны должны открываться в нужное время, в камеры поступать нужное количество топлива в определенной пропорции, вовремя подаваться искра и т.д. Ниже рассмотрены основные части, способствующие корректной работе.
Система зажигания
Эта система отвечает за электрическую часть в вопросе воспламенения топлива. К основным элементам относится:
- Элемент питания . Основным источником питания является аккумулятор. Он обеспечивает вращение стартера на выключенном двигателе. После этого в работу включается генератор, который питает двигатель, а также подзаряжает саму аккумуляторную батарею через реле зарядки.
- Катушка зажигания . Устройство, которое передает одномоментный заряд непосредственно на свечу зажигания. В современных автомобилях количество катушек равносильно количеству цилиндров, которые работают в двигателе.
- Коммутатор или распределитель зажигания . Специальной «умное» электронное устройство, которое определяет момент подачи искры.
- Свеча зажигания . Важный элемент в бензиновом ДВС, который обеспечивает своевременное воспламенение топливно-воздушной смеси. Продвинутые двигатели имеют по две свечи на цилиндр.
Впускная система
Смесь должна вовремя поступать в камеры сгорания. За этот процесс отвечает впускная система. К ней относится:
- Воздухозаборник . Патрубок, специально выведенный в место, недоступное для воды, пыли или грязи. Через него осуществляется забор воздуха, который потом попадает в двигатель;
- Воздушный фильтр . Сменная деталь, которая обеспечивает очистку воздуха от грязи и исключает попадание посторонних материалов в камеру сгорания. Как правило, современные автомобили обладают сменными фильтрами из плотной бумаги или промасленного поролона. На более архаичных моторах встречаются масляные воздушные фильтры.
- Дроссель . Специальная заслонка, которая регулирует количество воздуха, попадающего в впускной коллектор. На современной технике действует посредством электроники. Сначала водитель нажимает на педаль газа, а потом электронная система обрабатывает сигнал и следует команде.
- Впускной коллектор . Патрубок, который распределяет топливно-воздушную смесь по различным цилиндрам. Вспомогательными элементами в этой системе являются впускные заслонки и усилители.
Топливная систем
Принцип работы любого ДВС подразумевает своевременное поступление топлива и ее бесперебойную подачу. В комплекс также входит несколько основных элементов:
- Топливный бак . Резервуар, где хранится топливо. Как правило, располагается в максимально безопасном месте, вдали от мотора и сделан из негорючего материала (ударопрочный пластик). В нижней его части установлен бензонасос, который осуществляет забор топлива.
- Топливопровод . Система шлангов, ведущая от топливного бака непосредственно к двигателю внутреннего сгорания.
- Прибор образования смеси . Устройство, где смешиваются топливо и воздух. Об этом пункте уже упоминалось выше – за эту функцию может отвечать карбюратор или инжектор. Основным требованием является синхронная и своевременная подача.
- Головное устройство в инжекторных двигателях, которое определяет качество, количество и пропорции образования смеси.
Выхлопная система
В ходе того, как работает двигатель внутреннего сгорания, образуются выхлопные газы, которые необходимо выводить из мотора. Для правильной работы эта система обязана иметь следующие элементы:
- Выпускной коллектор . Устройство из тугоплавкого металла с высокой устойчивостью к температурам. Именно в него первоначально поступают выхлопные газы из двигателя.
- Приемная труба или штаны . Деталь, обеспечивающая транспортировку выхлопных газов далее по тракту.
- Резонатор . Устройство, снижающее скорость движения выхлопных газов и погашение их температуры.
- Катализатор . Предмет для очистки газов от СО2 или сажевых частиц. Здесь же располагается лямда-зонд.
- Глушитель . «Банка», имеющая ряд внутренних элементов, предназначенных для многократного изменения направления выхлопных газов. Это приводит к снижению их шумности.
Система смазки
Работа двигателя внутреннего сгорания будет совсем недолгой, если детали не будут обеспечиваться смазкой. Во всей технике используется специальное высокотемпературное масло, обладающее собственными характеристиками вязкости в зависимости от режимов эксплуатации мотора. Ко всему, масло предотвращает перегрев, обеспечивает удаление нагара и появление коррозии.
Для поддержания исправности системы предназначены следующие элементы:
- Поддон картера . Именно сюда заливается масло. Это основной резервуар для хранения. Контролировать уровень можно при помощи специального щупа.
- Масляный насос . Находится вблизи нижней точки поддона.
Обеспечивает циркуляцию жидкости по всему мотору через специальные каналы и его возвращение обратно в картер.
- Масляный фильтр . Гарантирует очистку жидкости от пыли, металлической стружки и прочих абразивных веществ, попадающих в масло.
- Радиатор . Обеспечивает эффективное охлаждение до положенных температур.
Система охлаждения
Еще один элемент, который необходим для мощных двигателей внутреннего сгорания. Он обеспечивает охлаждение деталей и исключает возможность перегрева. Состоит из следующих деталей:
- Радиатор . Специальный элемент, имеющий «сотовую» структуру. Является отличным теплообменником и эффективно отдает тепло, гарантируя охлаждение антифриза.
- Вентилятор . Дополнительный элемент, дующий на радиатор. Включается тогда, когда естественный поток набегающего воздуха уже не может обеспечить эффективное отведение тепла.
- Помпа . Насос, который помогает жидкости циркулировать по большому или малому кругу системы (в зависимости от ситуации).
- Термостат . Клапан, который открывает заслонку, пуская жидкость по нужному кругу. Работает совместно с датчиком температуры движка и охлаждающей жидкости.
Заключение
Первый двигатель внутреннего сгорания появился еще очень давно – почти полтора столетия назад. С тех пор было сделано огромное количество разных нововведений или интересных технических решений, которые порой меняли вид мотора до неузнаваемости. Но общий принцип работы двигателя внутреннего сгорания оставался прежним. И даже сейчас, в эпоху борьбы за экологию и постоянно ужесточающийся норм по выбросу СО2, электромобили все еще не в силах составить серьезную конкуренцию машинам с ДВС. Бензиновые автомобили и сейчас живее всех живых, а мы живем в золотую эпоху автомобилестроения.
Ну а для тех, кто готов погрузиться в тему еще глубже, у нас есть отличное видео:
Все двигатели преобразуют какую-нибудь энергию в работу. Двигатели бывают разные – электрические, гидравлические, тепловые и т. д., в зависимости от того, какой вид энергии они преобразуют в работу. ДВС — двигатель внутреннего сгорания, это тепловой двигатель, в котором в полезную работу преобразуется теплота сгорающего в рабочей камере топлива, внутри двигателя. Также существуют двигателя с внешним сгоранием — это реактивные двигатели самолётов, ракет и т.д. в этих двигателях сгорание внешнее, поэтому они называются двигателями с внешним сгоранием.
Но простой обыватель чаще сталкивается с двигателем автомобиля и понимают под двигателем именно поршневой двигатель внутреннего сгорания. В поршневом ДВС, сила давления газов, возникающая при сгорании топлива в рабочей камере, воздействует на поршень, который совершает возвратно-поступательное движение в цилиндре двигателя и передаёт усилие на кривошипно-шатунный механизм, который преобразует возвратно-поступательное движение поршня во вращательное движение коленчатого вала. Но это очень упрощенный взгляд на ДВС. На самом деле, в ДВС сосредоточены сложнейшие физические явления, пониманию которых посвятили себя многие выдающиеся ученые. Чтобы ДВС работал, в его цилиндрах, сменяя друг друга, происходят такие процессы, как подача воздуха, впрыск и распыление топлива, его смешивание с воздухом, воспламенение образовавшейся смеси, распространение пламени, удаление отработавших газов. На каждый процесс отводится несколько тысячных долей секунды. Добавьте к этому процессы, которые протекают в системах ДВС: теплообмен, течение газов и жидкостей, трение и износ, химические процессы нейтрализации отработавших газов, механические и тепловые нагрузки. Это далеко не полный перечень. И каждый из процессов должен быть организован наилучшим образом. Ведь из качества протекающих в ДВС процессов складывается качество двигателя в целом – его мощность, экономичность, шумность, токсичность, надежность, стоимость, вес и размеры.
Читайте также
Двигателя внутреннего сгорания бывают разные: , бензиновые, со смешенным питанием, и т.д. и это далеко не полный список! Как видите, вариантов двигателей внутреннего сгорания очень много, но если стоит затронуть классификацию ДВС, то для подробного рассмотрения всего объёма материала понадобится минимум 20-30 страниц — большой объём, не так ли? И это только классификация. ..
Принципиальный ДВС автомобиля НИВА
1 — Щуп для замера уровня масла в картере | 22 — Звездочка распределительного вала |
---|
Ни одна область деятельности несравнима с поршневыми ДВС по масштабам, количеству людей занятых в разработке, производстве и эксплуатации. В развитых странах деятельность четверти самодеятельного населения прямо или косвенно связана с поршневым двигателестроением. Двигателестроение, как исключительно наукоемкая область, определяет и стимулирует развитие науки и образования. Общая мощность поршневых двигателей внутреннего сгорания составляет 80 – 85% мощности всех энергоустановок мировой энергетики. На автомобильном, железнодорожном, водном транспорте, в сельском хозяйстве, строительстве, средствах малой механизации, ряде других областей, поршневой ДВС как источник энергии пока не имеет должной альтернативы. Мировое производство только автомобильных двигателей непрерывно увеличивается, превысив 60 миллионов единиц в год. Количество производимых в мире малоразмерных двигателей также превышает десятки миллионов в год. Даже в авиации поршневые двигатели доминируют по суммарной мощности, количеству моделей и модификаций и количеству установленных на самолеты двигателей. В мире эксплуатируется несколько сотен тысяч самолетов с поршневыми ДВС (бизнес-класса, спортивных, беспилотных и т.
д.). В США на долю поршневых двигателей приходится около 70% мощности всех двигателей, установленных на гражданских летательных аппаратах.
Но со временем всё меняется и скоро мы увидим и будем эксплуатировать принципиально другие типы двигателей, которые будет иметь высокие эксплуатационные показатели, высокий КПД, простота конструкции и главное — экологичность. Да, всё верно, главным минусом двигателя внутреннего сгорания является его экологическая характеристика. Как бы не оттачивали работу ДВС, какие бы системы не внедряли, он всё равно оказывается существенное влияние на наше здоровье. Да, теперь можно с уверенностью сказать, что существующая технология моторостроения чувствует «потолок» — это такое состояние, когда та, или иная технология полностью исчерпала свои возможность, полностью выжато, всё что можно было сделать — уже сделано и с точки зрения экологии принципиально НИЧЕГО уже не изменить в существующих типах ДВС. Стоит вопрос: нужно полностью менять принцип работы двигателя, его энергоноситель (нефтяные продукты) на что-то новое, принципиально иное (). Но, к сожалению, это дело не одного дня или даже года, нужны десятилетия…
Пока ещё не одно поколение ученых и конструкторов будут исследовать и совершенствовать старую технологию постепенно подходя всё ближе и ближе к стенке, через которую уже будет невозможно перескочить (физически это не возможно). Еще очень долго ДВС будет давать работу тем, кто его производит, эксплуатирует, обслуживает и продает. Почему? Всё очень просто, но в то же время эту простую истину далеко не все понимают и принимают. Главная причина замедления внедрения принципиально иных технологий — капитализм. Да, как бы это странно не звучало, но именно капитализм, та система, которая как кажется должна быть заинтересована в новых технологиях, тормозит развитие человечества! Всё очень просто — нужно зарабатывать. Как же быть с теми нефтяными вышками, нефтезаводами и доходами?
ДВС «хоронили» неоднократно. В разное время на смену ему приходили электродвигатели на аккумуляторах, топливные элементы на водороде и многое другое. ДВС неизменно побеждал в конкурентной борьбе. И даже проблема исчерпания запасов нефти и газа — это не проблема ДВС. Существует неограниченный источник топлива для ДВС.
По последним данным, нефть может восстанавливаться, а что это значит для нас?
Характеристики ДВС
При одних и тех же конструктивных параметрах у разных двигателей такие показатели, как мощность, крутящий момент и удельный расход топлива, могут отличаться. Это связано с такими особенностями, как количество клапанов на цилиндр, фазы газораспределения и т. п. Поэтому для оценки работы двигателя на разных оборотах используют характеристики — зависимость его показателей от режимов работы. Характеристики определяются опытным путем на специальных стендах, так как теоретически они рассчитываются лишь приблизительно.
Как правило, в технической документации к автомобилю приводятся внешние скоростные характеристики двигателя (рисунок слева), определяющие зависимость мощности, крутящего момента и удельного расхода топлива от числа оборотов коленвала при полной подаче топлива. Они дают представление о максимальных показателях двигателя.
Показатели двигателя (упрощенно) изменяются по следующим причинам. С увеличением числа оборотов коленвала растет крутящий момент благодаря тому, что в цилиндры поступает больше топлива. Примерно на средних оборотах он достигает своего максимума, а затем начинает снижаться. Это происходит из-за того, что с увеличением скорости вращения коленвала начинают играть существенную роль инерционные силы, силы трения, аэродинамическое сопротивление впускных трубопроводов, ухудшающее наполнение цилиндров свежим зарядом топливо-воздушной смеси, и т. п.
Быстрый рост крутящего момента двигателя указывает на хорошую динамику разгона автомобиля благодаря интенсивному увеличению силы тяги на колесах. Чем дольше величина момента находится в районе своего максимума и не снижается, тем лучше. Такой двигатель более приспособлен к изменению дорожных условий и реже придется переключать передачи.
Мощность растет вместе с крутящим моментом и даже, когда он начинает снижаться, продолжает увеличиваться благодаря повышению оборотов. После достижения максимума мощность начинает снижаться по той же причине, по которой уменьшается крутящий момент. Обороты несколько выше максимальной мощности ограничивают регулирующими устройствами, так как в этом режиме значительная часть топлива расходуется не на совершение полезной работы, а на преодоление сил инерции и трения в двигателе. Максимальная мощность определяет максимальную скорость автомобиля. В этом режиме автомобиль не разгоняется и двигатель работает только на преодоление сил сопротивления движению — сопротивления воздуха, сопротивления качению и т. п.
Величина удельного расхода топлива также меняется в зависимости от оборотов коленвала, что видно на характеристике. Удельный расход топлива должен находиться как можно дольше вблизи минимума; это указывает на хорошую экономичность двигателя. Минимальный удельный расход, как правило, достигается чуть ниже средних оборотов, на которых в основном и эксплуатируется автомобиль при движении в городе.
Пунктирной линией на графике выше показаны более оптимальные характеристики двигателя.
Двигатель внутреннего сгорания (ДВС) – это самый распространенный тип двигателя из всех, которые устанавливаются в настоящее время на автомобили. Несмотря на то, что современный двигатель внутреннего сгорания состоит из тысячи частей, принцип его работы весьма прост. В рамках данной статьи мы рассмотрим устройство и принцип работы ДВС.
Внизу страницы смотрите видео, на котором наглядно показано устройство и принцип работы бензинового ДВС.
В каждом двигателе внутреннего сгорания есть цилиндр и поршень. Именно внутри цилиндра ДВС происходит преобразование тепловой энергии, выделяемой при сжигании топлива, в энергию механическую, способную заставить наш автомобиль двигаться. Этот процесс повторяется с частотой несколько сотен раз в минуту, что обеспечивает непрерывное вращение выходящего из двигателя коленчатого вала.
Принцип работы четырёхтактного двигателя внутреннего сгорания
В подавляющем большинстве легковых автомобилей устанавливают четырехтактные двигатели внутреннего сгорания, поэтому мы и берём его за основу. Чтобы лучше понять принцип устройства бензинового ДВС, предлагаем вам взглянуть на рисунок:
Топливно-воздушная смесь, попадая через впускной клапан в камеру сгорания (такт первый – впуск), сжимается (такт второй – сжатие) и воспламеняется от искры свечи зажигания. При сжигании топлива, под воздействием высокой температуры в цилиндре двигателя образуется избыточное давление, заставляющее поршень двигаться вниз к так называемой нижней мертвой точке (НМТ), совершая при этом такт третий – рабочий ход. Перемещаясь во время рабочего хода вниз, с помощью шатуна, поршень приводит во вращение коленчатый вал. Затем, перемещаясь от НМТ к верхней мертвой точке (ВМТ) поршень выталкивает отработанные газы через выпускной клапан в выхлопную систему автомобиля – это четвертый такт (выпуск) работы двигателя внутреннего сгорания.
Такт – это процесс, происходящий в цилиндре двигателя за один ход поршня. Совокупность тактов, повторяющихся в строгой последовательности и с определенной периодичностью, обычно называют рабочим циклом
, в данном случае, двигателя внутреннего сгорания.
- Такт первый — ВПУСК . Поршень перемещается от ВМТ к НМТ, при этом возникает разряжение и полость цилиндра ДВС заполняется горючей смесью через открытый впускной клапан. Смесь, попадая в камеру сгорания, смешивается с остатками отработавших газов. В конце впуска давление в цилиндре составляет 0,07–0,095 МПа, а температура 80-120 ºС.
- Такт второй – СЖАТИЕ . Поршень движется к ВМТ, оба клапана закрыты, рабочая смесь в цилиндре сжимается, а сжатие сопровождается повышением давления (1,2–1,7 МПа) и температуры (300-400 ºС).
- Такт третий – РАСШИРЕНИЕ . При воспламенении рабочей смеси в цилиндре ДВС выделяется значительное количество теплоты, резко увеличивается температура (до 2500 градусов по Цельсию). Под давлением поршень перемещается к НМТ. Давление равно 4–6 МПа.
- Такт четвертый – ВЫПУСК . Поршень стремится к ВМТ через открытый выпускной клапан, отработавшие газы выталкиваются в выпускной трубопровод, а затем в окружающую среду.
Давление в конце цикла: 0,1–0,12 МПа, температура 600-900 ºС.
И так, вы смогли убедиться, что двигатель внутреннего сгорания устроен не очень сложно. Как говорится, все гениальное – просто. А для большей наглядности рекомендуем посмотреть видео, на котором также очень хорошо показан принцип работы ДВС.
Поршни современных двигателей / Ремонт двигателей
Не будет преувеличением сказать, что поршень — наиболее ответственная и специфичная деталь в современном двигателе. Он должен быть легким и прочным, способным выдерживать значительные механические нагрузки и тепловые удары, а кроме того, обладать высокой износостойкостью рабочих поверхностей, низким трением при минимально возможном зазоре в цилиндре.
Последнее требование особенно важно для хорошей герметичности, возможности избежать прорыва газов из камеры сгорания в картер и поступления масла в обратном направлении. Иными словами — для минимального расхода масла с одновременным отсутствием шума (стука) поршня о стенки.
И это только часть проблем, которые приходится решать при конструировании и производстве поршней для конкретных двигателей. В целом получается, что поршень как бы концентрирует технические новшества, заложенные в конструкцию мотора. Тут можно перефразировать известное выражение древних: «Покажи мне только поршень, и я скажу, что это за двигатель».
Словом, разработка и изготовление современных поршней — задача особая. На Западе их производством давно занимаются не изготовители автомобилей, а специализированные фирмы. У них накоплен необходимый опыт и создана соответствующая техническая база, без чего невозможно получить надежный результат. В мире существует несколько фирм такого рода, но наибольшую известность по праву получила немецкая марка «Мале» (Mahle).
Фирма Mahle существует с 1920 года. Название она получила по фамилии своих основателей — братьев Мале. Затем последовали десятилетия непрерывного совершенствования, развития и роста. Сегодня Mahle — это целая группа специализированных компаний, которая так и именуется — Mahle Group. Так, производством поршней, цилиндров и блоков цилиндров занимается концерн Mahle GmbH, привлекший дочерние и долевые фирмы США, Мексики, Бразилии, Испании, Франции и Южной Кореи. Туда же входят известные фирмы Mondial Piston (Испания) и Konig KG GmbH (Австрия). Помимо этого, в группу Mahle входят компании, производящие детали двигателей, включая поршневые пальцы, клапаны и др., а также фильтры (в том числе известная фирма Knecht).
Фирма Mahle приобрела свою мировую известность в основном успехами в разработке и производстве поршней для двигателей всех типов — от маленьких мотоциклетных до мощных, в десятки тысяч киловатт, судовых дизелей. Особенности конструкции и технологии изготовления поршней, выпускавшихся фирмой Mahle, — это этапы развития не только самой фирмы, но и всего мирового моторостроения. Они интересны для всех любителей техники, но особенно для тех, кто так или иначе связан с ремонтом автомобильных двигателей.
Известно, что поршни автомобильных двигателей изготавливаются из легких алюминиевых сплавов. Однако не все знают, что именно Mahle первой в Европе освоила серийное производство поршней из сплава алюминия с кремнием (1926 г.). При этом специальные поршневые сплавы «Mahle 124» с 11-13% кремния (1933 г.) и «Mahle 138» с 17-19% кремния (1937 г.) стали классическими для производителей поршней и сегодня применяются не менее широко.
В 1935 году Mahle впервые начала выпуск поршней со специальным профилем наружной поверхности: вместо цилиндрической формы поршень приобрел овальную и бочкообразную. Такая конфигурация оптимальна, поскольку в реальных условиях овальный и бочкообразный поршень, нагреваясь неравномерно (температура днища, омываемого горячими газами, существенно больше температуры юбки, охлаждаемой при контакте со стенками цилиндра), принимает форму, близкую к цилиндрической. В то же время небольшое заужение нижней части юбки создает гидродинамический эффект (своего рода подъемную силу) при движении поршня вниз — он как бы всплывает на масляной пленке. Найденные формы позволили уменьшить зазор в цилиндре без опасности заклинивания, снизить шум двигателя и повысить долговечность цилиндропоршневой группы. Они сохранились и у поршней самых современных двигателей. Правда, у них вдобавок появился еще и микрорельеф (микроканавки на наружной поверхности глубиной порядка 5 мкм), создающий дополнительную подъемную силу при движении в цилиндре.
С 1926 года Mahle для компенсации теплового расширения поршней использует биметаллический эффект: стальные терморегулирующие вставки внутри поршня при нагревании препятствуют температурному расширению, позволяя держать малый зазор между поршнем и цилиндром. Эту же задачу решают и пазы в верхней части юбки поршня (в канавке маслосъемного кольца или под ней), которые препятствуют распространению тепла от верхней части поршня, нагретой горячими газами, в юбку. Из-за этого температура стенок юбки уменьшается, что также препятствует тепловому расширению поршня. Описанная комбинированная конструкция — со вставками и пазами — получила название Autothermik и успешно применялась фирмой Mahle с 1930 года для поршней многих автомобильных двигателей.
Схема только с пазами (без стальных вставок) хотя и позволяет несколько уменьшить массу поршня, но заметно уступает схеме Autothermik по тепловому расширению. В настоящее время она применяется редко, в основном на двигателях малого рабочего объема.
С ростом мощности и соответственно нагрузок на поршень от пазов на юбке вообще пришлось отказаться, поскольку они ощутимо ослабляют деталь. Поэтому с 1955 года как на бензиновых, так и на дизельных двигателях широко используется конструкция со стальными вставками без пазов, получившая название Autothermatik. Кстати, поршни такого типа имеют все вазовские двигатели.
Дальнейшее развитие порш-ней — конструкция Duotherm, применяемая в основном на бензиновых двигателях с 1970 года. Здесь «управление» тепловым расширением юбки осуществляется как с помощью биметаллического эффекта, так и расширением верхней части поршня. Вследствие этого схема Duotherm по тепловому расширению лучше предыдущих схем, но несколько уступает по прочности схеме Autothermatik.
В последние годы поршни без стальных вставок и пазов (с «жесткой» юбкой) снова оказались в центре внимания. Автомобильные двигатели последнего поколения, многие из которых имеют алюминиевый блок цилиндров, потребовали облегчения поршней без ухудшения их тепловых, прочностных и других эксплуатационных характеристик. Это оказалось возможным, если перейти на материалы с повышенным содержанием кремния (включая сплав «Mahle 244» с 23-26% кремния). Одновременно были разработаны более эффективные методы получения заготовок поршней, в частности вместо литья под давлением — штамповкой (ковкой) и «жидкой» штамповкой. В результате поршни двигателей последних моделей имеют достаточно простую форму, низкую массу, высокую прочность и износостойкость, обеспечивая при этом минимальный шум двигателя.
Особо следует остановиться на конструкции поршней для дизельных двигателей. Как известно, дизель характеризуется очень высокой степенью сжатия (до 22-24 против 9-10 у бензинового двигателя) и соответственно большими силовыми и тепловыми нагрузками на детали, включая поршень. Его совершенствование опять-таки хорошо иллюстрируется цепочкой разработок фирмы Mahle.
Еще в 1931 году Mahle впервые применила чугунную вставку канавки для верхнего кольца, что позволило заметно увеличить ресурс дизельного двигателя. Эта конструкция с успехом применяется и по сей день, хотя с 1974 года (а особенно в последнее время) для упрочнения верхней канавки все чаще применяют износостойкие покрытия.
Обычно такое покрытие имеет толщину 40 — 120 мкм и делается по всему днищу поршня с «заходом» в канавку верхнего кольца, одновременно защищая края днища поршня от перегрева. Покрытие представляет собой так называемое твердое анодирование, то есть термохимическое преобразование верхнего слоя алюминиевого сплава в твердую керамику (окись алюминия Al2O3). Кстати, подобное покрытие, но меньшей толщины (обычно 10 — 15 мкм), используют и на поршнях высокофорсированных бензиновых двигателей с наддувом. Здесь помимо уменьшения износа верхней канавки ставится цель защиты днища поршня от разрушения детонацией.
В поршнях современных дизелей с наддувом нередко применяют так называемое внутреннее охлаждение, которое уменьшает температуру днища на 30-80°С. Оно состоит в подаче масла из системы смазки через форсунку во внутреннюю кольцевую полость поршня, расположенную около пояса поршневых колец. Очевидно, что изготовление поршня с подобным кольцевым отверстием требует специальной технологии.
Кроме этих особенностей, в последних конструкциях автомобильных дизелей с непосредственным впрыском топлива в цилиндр, отличающихся очень высокой нагрузкой на поршень, появилась и другая особенность. В бобышках поршня здесь устанавливают бронзовые втулки в отверстия для поршневого пальца, а сам палец делают волнистым с плавным уменьшением диаметра на 10-40 мкм вблизи краев отверстий поршня и шатуна. Такие решения обеспечивают долговечность соединения поршня с пальцем там, где традиционные конструкции и материалы уже не работают.
Среди достижений фирмы, касающихся дизелей, нельзя не отметить поршни с армированием керамическими волокнами типа Liquostatik, а также поршни типа Ferrotherm, состоящие из двух частей — уплотняющей и направляющей. На подходе и другие новинки.
Большинство поршней традиционно покрывается тонким (порядка 5 мкм) слоем свинца, олова или цинка. Покрытие препятствует задиру юбки на нерасчетных режимах, например при запуске и прогреве, когда условия смазки ухудшены. В последние годы на юбку поршней стали наносить покрытие типа Grafal, которое представляет собой графит со специальным наполнителем, обеспечивающим прочное сцепление со стенкой юбки. Покрытие имеет толщину 15-30 мкм и существенно влияет на износостойкость поршня.
Для V-образных двигателей с алюминиевыми блоками цилиндров и их поршней фирма разработала специальные технологии и материалы. Так, поршни имеют покрытие типа Ferrostan (1975 г.), представляющее собой слой железа толщиной 12-20 мкм, покрытый сверху тонким (1-2 мкм) слоем олова. Блок цилиндров отливают по специальной технологии Silumal из алюминиевого сплава «Mahle 147» (17% кремния, 4% меди) с осаждением повышенного количества кремния вблизи цилиндров. После обработки поверхность цилиндров травят соляной кислотой, при этом алюминий «уходит» с поверхности и там остается чистый кремний. Таким образом, пара материалов в двигателях с такими блоками цилиндров как бы обратна привычной: «железный» поршень работает в «алюминиевом» цилиндре. Этим достигается исключительная износостойкость пары (в комплекте с хромированными поршневыми кольцами), а также низкий уровень шума из-за очень малого зазора в цилиндре (порядка 0,01 мм). Такие блоки теперь применяют самые именитые фирмы (V8 — «Мерседес», «Ауди», «Порше»; V12 — «Мерседес» и БМВ).
Следует упомянуть также успехи Mahle в создании специальных износостойких покрытий цилиндров, в частности Chromal (1951) и Nikasil (1967). Chromal — это хромовое покрытие толщиной 0,06-0,08 мм, осаждаемое электрохимическим способом на алюминиевый цилиндр. Nikasil состоит из никеля с включением мелких (размером около 3 мкм) частиц карбида кремния; такое покрытие имеет наивысшую износостойкость. Это определило использование алюминиевых гильз цилиндров с покрытием Nikasil для двигателей гоночных автомобилей.
Здесь уместно заметить, что Mahle — основной производитель поршней и гильз цилиндров для автомобилей «Формулы 1» (F1). Подавляющее большинство команд, включая Феррари, Вильямс — Рено, Бенеттон-Рено, МакЛарен — Мерседес и другие, использует именно эти комплектующие. Поршень двигателя F1 должен оставаться работоспособным при частоте вращения до 17000 мин-1, поэтому он отличается предельно низкой массой и малой высотой, изготавливается «жидкой» штамповкой и имеет, как правило, внутреннее охлаждение, причем на последних модификациях используют только два поршневых кольца.
Сегодня фирма Mahle выпускает поршневые группы (комплекты «поршень — поршневые кольца — поршневой палец») для подавляющего большинства моделей и модификаций автомобилей европейского производства. Перечень марок впечатляет: «Мерседес», БМВ, «Фольксваген», «Ауди», «Опель», «Рено», «Пежо», «Ситроен», «Фиат» и многие другие. Эта продукция Mahle идет как для конвейерной сборки, так и в запасные части. Достаточно велика номенклатура поршней и для двигателей японских машин. Не забыты российские потребители: фирмой Mahle освоены и уже продаются на нашем рынке поршневые группы и кольца для двигателей ВАЗ и ГАЗ.
Несмотря на огромную массу выпускаемых деталей (в последние годы к ним прибавились поршневые кольца и подшипники коленчатых валов), фирма выполняет и индивидуальные заказы. Например, здесь могут изготовить поршни для новых двигателей в единичных количествах. Имея серьезную исследовательскую, конструкторскую и производственную базу, Mahle может спроектировать и сделать поршень для любого двигателя, удовлетворяющий всем необходимым требованиям, будь то низкий расход топлива и масла, малый выброс токсичных веществ с выхлопными газами, невысокий шум, максимально возможные мощность и долговечность двигателя. При этом будут выбраны оптимальные сочетания материала, конструкции, геометрии и покрытий поршня, необходимые для выполнения поставленных условий.
Интересно, что у фирмы можно заказать и любые поршни, которые когда-либо изготавливались фирмой Mahle: со времени ее основания сохраняются все формы для отливки.
Самый большой двигатель внутреннего сгорания
Начнем с того, что ДВС большого размера с огромной мощностью используются в качестве основной силовой установки на судах. Речь идет о судовых дизельных двигателях. На различных судах можно встретить множество вариантов таких дизелей, однако особого внимания заслуживает двигатель компании Wartsila-Sulzer, а точнее модель RTA96-C.
Сразу отметим, указанный агрегат сегодня по праву можно считать самым большим и самым мощным двигателем в мире, также установка имеет самый большой рабочий объем и размеры двигателя по сравнению со схожими аналогами. Итак, обо всем по порядку.
Содержание статьи
- Дизель-гигант: характеристики
- Особенности конструкции
- Что в итоге
Дизель-гигант: характеристики
Финский производитель Wartsila занимает лидирующие позиции среди компаний, которые специализируются на разработке и выпуске судовых дизелей. Агрегаты обладают высокой единичной мощностью.
Первый двигатель Wartsila — Sulzer с индексом RTA96-C получил 11 цилиндров и появился еще в 90-х годах. ДВС представляет собой двухтактный судовой дизель и был собран на мощностях японской компании Diesel United.
Затем в 2002 году было заявлено о доступности версии с 14 цилиндрами. Добавим, что сегодня компания изготавливает несколько вариантов подобных ДВС. Главным отличием является количество цилиндров, которых может быть от 6 до 14, тогда как общая конструкция практически одинаковая. Примечательно то, что диаметр цилиндра в таком ДВС составляет 960 мм, а ход поршня целых 2.5 метра.
Что касается рабочего объема, то показатель зафиксирован на отметке 1820 л. Как правило, указанный дизель с разным количеством цилиндров ставится на большие суда с вместительностью около 8 000 или 10 000 тонн, которые перевозят контейнеры (контейнеровоз). Указанный судовой дизель-генератор является основной силовой установкой, позволяя судну развить скорость в 25 узлов, что составляет чуть более 45 км/ч.
Общая мощность RTA96-C находится на отметке 108920 л.с. при рабочем объёме 25480 литров. Если же рассматривать мощность такого дизеля при пересчете на 1 литр топлива, получается чуть более 4 л.с. на литр горючего. На первый взгляд, это совсем немного. Более того, ни для кого не секрет, что производители автомобильных двигателей уже давно снимают с 1 литра не менее сотни «лошадок».
Однако важно понимать, что сниженная мощность при таком рабочем объеме является намеренным шагом. Дело в том, что судовой дизель «тихоходный» и очень надежный, обороты коленвала при выходе на максимальную мощность имеют частоту всего 102 об/мин, тогда как автомобильные дизельные ДВС вращаются с частотой около 3-4 тыс. об/мин.
Такая медленная и спокойная работа агрегата на судне позволяет добиться улучшенного наполнения и вентиляции огромных цилиндров, скорость движения поршня также невелика, однако мотор при этом отличается неплохим КПД. На практике это значит, что расход топлива в этом двигателе во всех режимах составляет 118-126 граммов дизтоплива на 1 л.с. в час. Этот показатель фактически в полтора или даже два раза ниже сравнительно с дизелями на авто.
Кстати, максимальный крутящий момент составляет 7 907 720 Нм при 102 об/мин. Расход горючего зафиксирован на отметке больше 6 283 литров в час. Однако когда такой дизель не нагружен или нагружен только частично, показатель КПД составляет около 50%, а также не сильно снижается и при полной нагрузке.
Еще важно учитывать, что судовой дизель получает менее «энергоемкое» топливо, чем автомобильные ДВС. Простыми словами, после сжигания 1 литра очищенной солярки, которую мы привыкли заливать в автомобиль на АЗС, полезной энергии выделится намного больше сравнительно с тяжелым дизтопливом для морских судов.
Также добавим, что модель Wartsila — Sulzer 14RTA96-C (14-цилиндровая версия) имеет вес в 2 тысячи 300 тонн, причем это «чистый» вес, то есть без учета моторного масла и других техжидкостей, которые дополнительно заливаются в агрегат. Только один коленчатый вал этого гиганта весит 300 тонн. В длину установка имеет 26.7 м, а по высоте показатель составляет 13.2 метра.
Особенности конструкции
Если говорить о конструктивных особенностях, примечательно то, что в каждом отдельном цилиндре такого судового дизельного двигателя имеется один большой клапан. Указанный клапан располагается прямо в центре камеры сгорания. Параллельно установлены еще три небольших клапана, которые выполняют функцию форсунок.
Получается, большой клапан выпускной и служит для выпуска отработавших газов из цилиндра, а через меньшие по размеру клапаны поступает солярка. Через выпускные клапаны отработавшие газы из всех цилиндров попадают в выпускной коллектор, затем поступают в 4 турбокомпрессора.
Компрессоры нагнетают воздух, пропуская его через охладители, к специальным «окнам», которые выполнены внизу цилиндра. Эти окна открываются в тот момент, когда поршень доходит до НМТ (нижняя мертвая точка) и пропускают воздух. Еще для передачи усилия от поршня на коленвал используется специальный (крейцкопфный) механизм. Данное решение позволяет продлить срок службы подобного ДВС и увеличить его ресурс, а также снизить вес агрегата.
Такой подход полностью оправдан с учетом особенности воспламенения топлива в дизеле, высоких нагрузок на дизельный двигатель, вибронагруженности установки и необходимости обеспечить максимальную долговечность. Все детали, из которых изготовлен самый большой двигатель, выполнены с использованием проверенных и прочных металлов. Традиционными решениями выступают чугун и сталь.
Что в итоге
Напоследок добавим, несмотря на большой успех в области производства сверхмощных судовых дизелей, инженеры компании Wartsila и далее не намерены останавливаться на достигнутом результате.
Доказательством служит информация о том, что ведутся работы над созданием еще более мощных судовых двигателей внутреннего сгорания. Например, уже обнародованы заявления о разработке судового дизеля с 18 цилиндрами.
Это значит, что в скором времени на фоне уже имеющихся в линейке дизель-генераторов появится еще более мощный ДВС с впечатляющими габаритами и характеристиками. Другими словами, скоро очередной самый большой двигатель в мире будет сдан в эксплуатацию.
Поршень двигателя и его конструктивные особенности
Search — Remove Shortcode
Поиск материалов
plg_search_jcomments
Войти
Регистрация
- Главная
- Техничка
- Поршень двигателя и его конструктивные особенности
Среда, 27 апреля 2016
Если говорить о поршнях, то принцип их работы помогут понять несколько бытовых примеров применения.
Поршень воздушного насоса помогает накачивать камеры автомобильных и велосипедных покрышек. Поршень внутри медицинского шприца помогает набирать и вводить лекарство при уколах. А поршень шприца кулинарного – пальчики оближешь.
Вот такие простые примеры помогают четко понять, что, во-первых, обязательным элементом при работе поршня будет цилиндр – такая труба или полость, внутри которой происходит прямолинейное и поступательное перемещение поршня. Во-вторых, это рабочая среда, которая контактирует с поршнем по его торцевой плоскости. Энергия при работе поршня преобразуется из внутренней энергии рабочей среды в кинематическую энергию движения поршня или из кинематической энергии движения поршня во внутреннюю энергию или работу.
Следует также отметить, что форма поперечного сечения поршня, как правило, круглая, хотя это совсем не обязательно – она может быть и прямоугольной, и квадратной, и любой другой формы. Просто круглая форма является наиболее технологичной, т.е. ее легко изготовить как для самого поршня, так и для рабочего цилиндра.
Особое место занимают поршни, работающие в двигателях внутреннего сгорания. Ведь, по сути, двигатель – это сердце автомобиля, а поршень можно уверенно назвать самой ответственной деталью этого сердца. Условия, в которых функционирует поршень автомобиля, не назовешь легкими. В первую очередь, это высокая температура сгоревших газов в пространстве камеры сгорания над поршнем, которая может достигать 2000°. Она передается как корпусу двигателя — через камеру сгорания цилиндра, так и самому поршню.
И если корпус цилиндра имеет возможности к охлаждению снаружи, то для поршня это требует специальных решений задачи по разбрызгиванию охлаждающей среды (например, масла в виде тумана). В целом, влияние высокой температуры в рабочей зоне поршня определяет выбор материала, подходящего для изготовления, и этот материал должен иметь высокую теплостойкость, иначе поршень может даже расплавиться.
Не менее важно влияние температуры на конструкцию, так как вместе с нагреванием будет происходить расширение самого поршня, что может привести к его заклиниванию, а при частоте возвратно-поступательного движения не менее 200 раз в секунду – к поломке.
В этом случае требуется материал с низким коэффициентом линейного теплового расширения.
Ранее распространенным материалом с достаточными свойствами был чугун, сегодня это сплавы на основе алюминия. Эти материалы также хороши с точки зрения технологичности конструкции, т.е. позволяют изготовлять поршень достаточно простыми средствами. Кроме этого, алюминиевые сплавы и чугун обеспечивают нужный коэффициент трения-скольжения поршня об стенку гильзы цилиндра, это позволяет снизить потери мощности от трения, что, соответственно, повышает КПД цилиндра, а, значит, и двигателя в целом.
Однако относительно большой удельный вес чугунных поршней из-за возникающих в процессе работы сил инерции определяет применение преимущественно в тихоходных двигателях. Для автомобильных двигателей поршни изготавливают из более легких алюминиевых сплавов.
Все эти особенности работы поршня и определяют его конструкцию, которая включает в себя днище, уплотняющую и направляющую части (направляющую еще называют «юбкой»), а головка поршня состоит из днища и уплотняющей части.
Днище непосредственно взаимодействует с горячими газами камеры сгорания, может быть вогнутым или выпуклым, а также иметь дополнительные полости, учитывающие расположение различных выступающих элементов (например, форсунок или свечей зажигания).
На уплотняющей части расположены канавки для установки компрессионных и маслосъемных колец. Часть головки поршня на расстоянии между плоскостью днища и канавкой для первого поршневого (компрессионного) кольца называют «огненным поясом» поршня. И это не случайно, так как назначение компрессионного кольца состоит в том, чтобы не пропускать газы из камеры сгорания в обход поршня (первым компрессионным кольцом отводится 45% тепла).
В тронке (юбке или направляющей части) поршня предусмотрены 2 бобышки для установки пальца-шатуна. Для компенсации температурных напряжений, возникающих у бобышек, на поверхности «юбки» делают углубления для предотвращения задиров, связанных с температурными деформациями, – так называемые «холодильники».
При проектировании поршней конструкторы работают над максимальным их облегчением, что улучшает показатель работы двигателя, стремятся избегать повышенного износа поршня, а также его прогара.
Для решения последней задачи учитывают распределение тепловых потоков от камеры сгорания к различным деталям двигателя, в том числе и потоки, проходящие через поршень.
После анализа распределения тепловых потоков намечают способы охлаждения поршня. Очевидно, что на конструкцию поршня также будет оказывать влияние и то, как он взаимодействует с сопрягаемыми деталями – поршневыми кольцами, гильзами и кривошипно-шатунным механизмом.
Зная и понимая условия и принцип работы поршня в двигателе внутреннего сгорания, невозможно оставаться равнодушным к его конструкции, когда вы смотрите на его изображение, а тем более когда чувствуете его металл в своих руках.
Видео о том как делают автомобильные поршни:
Автор
Super UserКомментируют
Топ блоги
Новости компании Haima 2016.
Новый плагиат от китайцев.
Поездка в Абхазию на авто 2017-18
Как отремонтировать блок управления двигателем автомобиля?
Ford EcoSport рестайлинг — первые фото
Двигатель с переменной степенью сжатия: особенности конструкции — Auto-Self.ru
Как может показаться на первый взгляд, современный двигатель внутреннего сгорания достиг высшей ступени своей эволюции. На данный момент серийно выпускаются различные бензиновые и дизельные моторы, появились гибридные установки, дополнительно реализована возможность перевести двигатель на газ.
В списке наиболее значимых наработок за последние годы можно выделить: внедрение систем высокоточного впрыска под управлением сложной электроники, получение большой мощности без увеличения рабочего объема благодаря системам турбонаддува, увеличение количества клапанов на цилиндр, использование систем изменения фаз газораспределения и т.д.
Результатом стало заметное улучшение характеристик ДВС, а также снижение уровня токсичности отработавших газов. Однако это еще не все. Конструкторы и инженеры по всему миру продолжают не только активно работать над усовершенствованием уже имеющихся решений, но и пытаются создать абсолютно новую конструкцию.
Достаточно вспомнить попытки построить двигатель без коленвала и шатунов, избавиться от распредвала в устройстве ГРМ или динамично изменять степень сжатия двигателя. Сразу отметим, хотя одни проекты еще находятся в стадии разработки, другие уже стали реальностью. Например, двигатели с изменяемой степенью сжатия. Давайте рассмотрим особенности, преимущества и недостатки таких ДВС.
Изменение степени сжатия: зачем это нужноМногие опытные водители знакомы с такими понятиями, как степень сжатия двигателя и октановое число для бензиновых моторов, а также цетановое число для дизельных. Для менее осведомленных читателей напомним, что степень сжатия представляет собой отношение объема над поршнем, который опущен в НМТ (нижняя мертвая точка) к тому объему, когда поршень поднялся в ВМТ (верхняя мертвая точка).
Бензиновые агрегаты имеют, в среднем, показатель 8-14, дизели 18 -23. Степень сжатия является фиксированной величиной и конструктивно закладывается во время разработки того или иного двигателя. Также от степени сжатия будут зависеть и требования к использованию октанового числа бензина в том или ином моторе. Параллельно учитывается и то, атмосферный двигатель или с наддувом.
Если говорить о самой степени сжатия, фактически это показатель, который определяет, насколько сильно будет сжиматься топливно-воздушная смесь в цилиндрах двигателя. Если просто, хорошо сжатая смесь лучше воспламеняется и полноценнее сгорает. Получается, увеличение степени сжатия позволяет добиться роста КПД двигателя, получить улучшенную отдачу от мотора, снизить расход топлива и т.д.
Однако есть и нюансы. Прежде всего, это детонация двигателя. Опять же, если не вдаваться в подробности, в норме заряд топлива и воздуха в цилиндрах должен именно гореть, а не взрываться. Более того, воспламенение смеси должно начинаться и оканчиваться в строго заданные моменты.
При этом топливо имеет так называемую «детонационную стойкость», то есть способность противостоять детонации. Если же сильно увеличить степень сжатия, тогда горючее может начать детонировать в двигателе при определенных режимах работы ДВС.
Результат — неконтролируемый взрывной процесс сгорания в цилиндрах, быстрое разрушение деталей мотора ударной волной, значительный рост температуры в камере сгорания и т.д. Как видно, сделать постоянной высокую степень сжатия нельзя именно по этим причинам. При этом единственным выходом в данной ситуации является возможность гибко изменять данный показатель применительно к разным режимам работы двигателя.
Такой «рабочий» мотор недавно предложили инженеры премиального бренда Infiniti (элитное подразделение Nissan). Также в аналогичные разработки были и остаются вовлечены другие автопроизводители (SAAB, Peugeot ,Volkswagen и т.д). Итак, давайте рассмотрим двигатель с изменяемой степенью сжатия.
Переменная степень сжатия двигателя: как это работает
Прежде всего, доступная возможность изменять степень сжатия позволяет в значительной мере увеличить производительность турбомоторов с одновременным уменьшением расхода топлива. В двух словах, в зависимости от режима работы и нагрузок на ДВС топливный заряд сжимается и сгорает в самых оптимальных условиях.
Когда нагрузки на силовой агрегат минимальны, в цилиндры подается экономичная «бедная» смесь (много воздуха и мало топлива). Для такой смеси хорошо подходит высокая степень сжатия. Если же нагрузки на мотор растут (подается «богатая» смесь, в которой больше бензина), тогда закономерно возрастает риск возникновения детонации. Соответственно, чтобы этого не произошло, степень сжатия динамично уменьшается.
В двигателях, где степень сжатия постоянна, своеобразной защитой от детонации является изменение УОЗ (угол опережения зажигания). Данный угол сдвигается «назад». Естественно, такой сдвиг угла приводит к тому, что хотя детонации нет, но при этом теряется и мощность. Что касается мотора с изменяемой степенью сжатия, сдвигать УОЗ нет необходимости, то есть не происходит мощностных потерь.
Что касается самой реализации схемы, фактически задача сводится к тому, что происходит физическое уменьшение рабочего объема двигателя, однако сохраняются все характеристики (мощность, момент и т. д.)
Сразу отметим, над таким решением трудились разные компании. В результате появились разные способы управления степенью сжатия, например, изменяемый объем камеры сгорания, шатуны с возможностью подъема поршней и т.д.
- Одной из самых ранних разработок стало внедрение дополнительного поршня в камеру сгорания. Указанный поршень имел возможность перемещаться, одновременно изменяя объем. Минусом всей конструкции стала необходимость устанавливать дополнительные детали в БЦ. Также сразу проявились изменения формы камеры сгорания, горючее сгорало неравномерно и неполноценно.
По указанным причинам данный проект так и не был завершен. Такая же участь постигла и разработку, которая имела поршни с возможностью изменения их высоты. Указанные поршни разрезного типа оказались тяжелыми, еще добавились трудности касательно реализации управления высотой подъема крышки поршня и т.д.
- Дальнейшие разработки уже не затрагивали поршни и камеру сгорания, максимум внимания был уделен вопросу подъема коленчатого вала.
Другими словами, стояла задача реализовать управление высотой подъема коленвала.
Схема устройства такова, что опорные шейки вала расположены в специальных муфтах эксцентрикового типа. Указанные муфты приводятся в движение посредством шестерен, которые связаны с электрическим двигателем.
Проворот эксцентриков позволяет поднять или опустить коленчатый вал, что и приводит к изменению высоты подъема поршней по отношению к ГБЦ. В результате объем камеры сгорания увеличивается или уменьшается, одновременно меняется и степень сжатия.
Отметим, что было построено несколько прототипов на базе 1.8-литрового турбированного агрегата от Volkswagen, степень сжатия менялась от 8 до 16. Двигатель долго испытывали, но серийным агрегат так и не стал.
- Еще одной попыткой найти решение стал двигатель, в котором степень сжатия менялась посредством подъема всего блока цилиндров. Разработка принадлежит бренду Saab, а сам агрегат чуть даже не попал в серию. Двигатель известен как SVC, объем 1.
6 литра, агрегат с 5 цилиндрами, оснащен турбонаддувом.
Мощность составила около 220 л. с., крутящий момент чуть более 300 Нм. Примечательно то, что расход горючего в режиме средних нагрузок снизился почти на треть. Что касается самого топлива, появилась возможность заливать как АИ-76, так и 98-й.
Инженеры Saab разделили блок цилиндров, выделив две условные части. В верхней находились головки и гильзы цилиндров, тогда как в нижней части коленчатый вал. Своеобразным соединением этих частей блока с одной стороны был подвижный шарнир, а с другой особый механизм, оснащенный электроприводом.
Так была реализована возможность немного поднять верхнюю часть под определенным углом. Такой угол подъема составил всего несколько градусов, при этом степень сжатия менялась от 8 до 14. При этом герметизировать «стык» должен был кожух из резины.
На практике сами детали для подъема верхней части блока, а также и сам защитный кожух оказались весьма слабыми элементами. Возможно, именно это помешало мотору попасть в серию и проект дальше закрыли.
- Очередную разработку далее предложили инженеры из Франции. Турбомотор с рабочим объемом 1.5 литра получил возможность менять степень сжатия от 7 до 18 и выдавал мощность около 225 л.с. Моментная характеристика зафиксирована на отметке 420 Нм.
Конструктивно агрегат сложный, с разделенным шатуном. В той области, где шатун крепится к коленвалу, деталь оснастили особым зубчатым коромыслом. В месте соединения шатуна с поршнем также была внедрена планка-рейка зубчатого типа.
С другой стороной к коромыслу была прикреплена рейка поршня, который реализовывал управление. Система приводилась от системы смазки, рабочая жидкость проходила через сложную систему каналов, клапанов, а также имелся дополнительный электропривод.
Рекомендуем также прочитать статью о том, как форсировать двигатель. Из этой статьи вы узнаете о существующих доступных способах форсирования двигателя внутреннего сгорания для получения большей мощности, лучшего отклика на педаль газа, увеличения крутящего момента и т. д.
В двух словах, перемещение управляющего поршня оказывало воздействие на коромысло. В результате менялась и высота подъема основного поршня в цилиндре. Отметим, что двигатель также не стал серийным, а проект был заморожен.
- Следующей попыткой создать двигатель с изменяемой степенью сжатия стало решение инженеров Infiniti, а именно двигатель VCT (от англ. Variable Compression Turbocharged). В этом моторе стало возможным менять степень сжатия от 8 до 14. Особенностью конструкции является уникальный траверсный механизм.
В основе лежит соединение шатуна с нижней шейкой, которое является подвижным. Также использована система рычагов, которые приводятся в действие от электродвигателя.
Управляет процессом контроллер, посылая сигналы на электродвигатель. Электромотор после получения команды от блока управления смещает тягу, а система рычагов реализует смену положения, что и позволяет менять высоту подъема поршня.
В результате агрегат Infiniti VCT с рабочим объемом 2. 0 литра с мощностью около 265 л.с. позволил экономить почти 30% горючего сравнительно с аналогичными ДВС, которые при этом имеют постоянную степень сжатия.
Если производителю удастся эффективно решить имеющиеся на данный момент проблемы (сложность конструкции, повышенные вибрации, надежность, высокая конечная стоимость производства агрегата и т.д.), тогда оптимистичные заявления представителей компании вполне могут воплотиться в реальность, а сам двигатель имеет все шансы стать серийным уже в 2018-2019 году.
Поделитесь с друзьями в соц.сетях:
Как работают автомобильные двигатели внутреннего сгорания и их конструктивные особенности
ХАРАКТЕРИСТИКИ АВТОМОБИЛЬНОГО ДВИГАТЕЛЯ
Большинство автомобилей приводится в движение поршневым двигателем, известным как двигатель внутреннего сгорания (ВС), который сжигает смесь бензина и воздуха. Смесь сгорает в камере сгорания внутри цилиндра над поршнем.
При сгорании смесь быстро расширяется, и давление, оказываемое на верхнюю часть поршня, толкает ее вниз по цилиндру. Нижняя сторона поршня соединена стержнем, известным как соединение с коленчатым валом, и их расположение позволяет преобразовывать нисходящий путь поршня во вращательное движение вала от возвратно-поступательного движения к вращательному движению. В зависимости от конфигурации двигателя внутреннего сгорания мощность коленчатого вала передается на колеса, приводящие автомобиль в движение, через сцепление или преобразователь крутящего момента, коробку передач и главную передачу.
Впускной и выпускной клапаны в верхней части цилиндра контролируют поступление бензино-воздушной смеси и выход продуктов сгорания в выхлопную систему. Клапаны приводятся в действие эксцентриковыми кулачками распределительного вала, который приводится в движение коленчатым валом. Смесь воспламеняется в камере сгорания свечой зажигания. Ток высокого напряжения или высокого напряжения, необходимый для образования искры, генерируется в отдельной системе зажигания и обычно подается на каждый цилиндр по мере необходимости через распределитель, обычно приводимый в движение распределительным валом.
КАК ДВИГАТЕЛИ ВНУТРЕННЕГО СГОРАНИЯ НАЧАЮТ СГОРАНИЕ ТОПЛИВА
Чтобы запустить двигатель, его необходимо провернуть. Это делается электрически с помощью стартера, который вращает коленчатый вал, обычно путем зацепления небольшой шестерни с зубьями шестерни вокруг внешнего края маховика, прикрепленного болтами к концу коленчатого вала. Помимо обеспечения средства запуска двигателя, маховик сглаживает импульсы мощности от поршней и позволяет коленчатому валу вращаться относительно плавно.
Всякий раз, когда коленчатый вал вращается стартером, движение поршней вверх и вниз многократно всасывает смесь воздуха и топлива в цилиндры (камеру сгорания) до тех пор, пока камера сгорания не заполнится достаточным объемом воздушно-топливной смеси, чтобы при выключенном зажигании искры от свечей воспламеняют смесь в камере сгорания, в этом случае сразу же начинается сгорание, приводящее к запуску двигателя.
КОМПОНЕНТЫ, ОБЕСПЕЧИВАЮЩИЕ ДЛИТЕЛЬНУЮ РАБОТУ ДВИГАТЕЛЕЙ ВНУТРЕННЕГО ХОДА И БЕЗОПАСНУЮ РАБОТУ
Для обеспечения стабильной работы и продления срока службы двигатели внутреннего сгорания оснащены системой охлаждения и системой смазки.
Система охлаждения двигателей внутреннего сгорания может быть воздушной или водяной. В методе воздушного охлаждения не используется вода внутри двигателя, а внешнее окружение камер сгорания выполнено с ребрами из равномерно разнесенного металла, что позволяет легко рассеивать тепло, выделяемое при сгорании, в окружающую среду, а температура окружающей среды будет снижаться. помогают поддерживать умеренную температуру в камере сгорания.
Метод водяного охлаждения был наиболее широко использован для автомобильных двигателей и, по-видимому, является наиболее эффективным для автомобильных двигателей, при таком методе внутри корпуса двигателя создаются отверстия водяного канала, особенно в камере сгорания, так что два выходных отверстия водяных каналов будут прикреплены к впускному и выпускному отверстиям радиатора, так что, когда двигатель работает, вода будет непрерывно рециркулировать из радиатора в двигатель, а внешний вентилятор поможет в охлаждении. горячая вода, поступающая из двигателя, прежде чем она сможет вернуться обратно из впускного отверстия.
Система смазки работает почти так же, как система охлаждения, но ее основная функция ограничивается только внутренней частью двигателя. В то время как вода и воздух охлаждают двигатель, система смазки обеспечивает плавную работу двигателя с меньшим износом. Хотя система смазки обеспечивает некоторый уровень охлаждения двигателя, ее основная функция заключается в уменьшении износа движущихся частей двигателя.
КОМПОНЕНТЫ, ПЕРЕДАЮЩИЕ МОЩНОСТЬ ОТ ДВИГАТЕЛЕЙ ВНУТРЕННЕГО СЦЕПЛЕНИЯ
Компонентами, передающими мощность, являются поршни, шатуны и коленчатый вал, они спрятаны внутри блока цилиндров, а снаружи блока и головки цилиндров находится ряд жизненно важных вспомогательных компонентов.
Компоненты включают; впускной и выпускной коллекторы, которые подают топливо и воздух в цилиндры и выводят выхлопные газы, карбюратор, распределитель, стартер, генератор и обычно бензонасос. Положения этих компонентов немного различаются в зависимости от компоновки двигателя. Некоторые из внешних компонентов трудно найти. Карбюратор обычно находится под большим воздушным фильтром, а выпускной коллектор может быть наполовину спрятан в тепловой камере, которая направляет теплый воздух к карбюратору.
Также будет несколько шлангов малого диаметра. Помимо подачи воды к обогревателю салона и от него, шланги часто подают воду из блока цилиндров в рубашку вокруг впускного коллектора, где тепло помогает испарять смесь. Они также направляют картерные газы во впускной коллектор.
Однако на внешних частях двигателя концы коленчатого вала обычно соединены с маховиком, шкивом или любым приводным механизмом, где мощность может быть использована для любой цели, для которой она предназначена. В случае автомобильного двигателя мощность будет направлена на приводной механизм колес автомобиля.
ТЯЖЕЛЫЕ МЕТАЛЛИЧЕСКИЕ ЧАСТИ ДВИГАТЕЛЕЙ ВНУТРЕННЕГО СЦЕПЛЕНИЯ
Из-за значительных температур и сил, возникающих в двигателе внутреннего сгорания, компоненты, непосредственно контактирующие с нагрузками, должны быть чрезвычайно жесткими и очень прочными, чтобы выдерживать суровые условия в двигателе. Что касается деталей и узлов двигателя внутреннего сгорания, то для указанной цели можно найти три основных узла:
ГОЛОВКА ЦИЛИНДРОВ
Головка цилиндров содержит камеры сгорания, клапаны (обычно по два в каждом цилиндре ), свечи зажигания, пружины, закрывающие клапаны, и клапанный механизм, открывающий их, а также впускные и выпускные каналы.
БЛОК ЦИЛИНДРОВ
Блок цилиндров содержит цилиндры и содержит коленчатый вал, поршни и шатуны. Он также может нести распределительный вал, но на некоторых двигателях он может быть установлен над головкой цилиндров и там, где это делается. , двигатель известен как двигатель с верхним распределительным валом (OHC). в двигателях с водяным охлаждением как блок цилиндров, так и головка блока цилиндров имеют каналы, по которым циркулирует охлаждающая вода.
КОЛЕНВАЛ В СБОРЕ
Коленчатый вал в сборе включает поршень, шатуны и коленчатый вал. Вал установлен в коренных подшипниках, установленных между цилиндрами в нижней части блока цилиндров. На одном конце коленчатого вала находится маховик. В основании двигателя поддон из штампованной стали или литого алюминия представляет собой резервуар для смазочного масла. Вверху крышка удерживает масло, которое смазывает шестерню клапанов и на современных двигателях обеспечивает изоляцию от атмосферного воздуха.
Филип Н. @ EngineeringAll.com
Филип является выпускником факультета машиностроения Мор и инспектором по неразрушающему контролю с обширными практическими знаниями в других областях техники и программного обеспечения.
Он любит писать и делиться информацией, касающейся инженерных и технологических областей, науки и окружающей среды, а также технических должностей. Его сообщения основаны на личных идеях, изученных знаниях и открытиях из инженерных, научных и инвестиционных областей и т. д.
Пожалуйста, подпишитесь на нашу рассылку и следите за нашими страницами в социальных сетях, чтобы получать регулярные и своевременные обновления.
Вы можете подписаться на страницы EngineeringAll в социальных сетях, набрав «@ EngineeringAlls» в любой форме поиска в социальных сетях (Facebook More, Twitter, Linkedin, Pinterest More, Tumblr More и т. д.).
Вы можете отправить свою статью для бесплатного просмотра и публикации, используя страницу «ПУБЛИКАЦИЯ ВАШЕЙ СТАТЬИ» в кнопках МЕНЮ.
Если вам понравился этот пост, поделитесь им с друзьями, используя кнопки социальных сетей.
НАЖМИТЕ ЗДЕСЬ, ЧТОБЫ ПОДПИСАТЬСЯ НА НАШИ ОБНОВЛЕНИЯ ПО ЭЛЕКТРОННОЙ ПОЧТЕ
Будущее конструкции двигателя внутреннего сгорания: тенденции 2022 года
Изобретение двигателя внутреннего сгорания (ДВС) было благом для транспорта, эффективности и всего, что связано с Америкой. Но по мере того, как технологии интегральных схем устаревают, а заботы об окружающей среде возрастают, на смену им приходят альтернативы.
Автопроизводители и потребители размышляют о будущем производства легковых и грузовых автомобилей с двигателями внутреннего сгорания и смотрят на , что заменит существующих дизайнов. Обзор того, что привело нас к этому, а также новые проблемы эффективности и защиты окружающей среды, которые может помочь решить порошковый металл, — это уроки, которые не должен упустить ни один инженер OEM:
Будущее проектирования двигателей внутреннего сгорания
Ищите эти внешние факторы, чтобы повлиять на подход инженеров конструкция двигателя внутреннего сгорания в течение следующего десятилетия:
- ограничения выбросов CO₂
- Эффективность двигателя для снижения этих выбросов
- Дизель по сравнению с традиционным газом
- Электромобили по сравнению с автомобилями с ДВС
- Порошковая металлургия поддерживает переход к экологичности
Откройте изображение в новой вкладке, чтобы увидеть полноразмерную версию этой инфографики:
1.
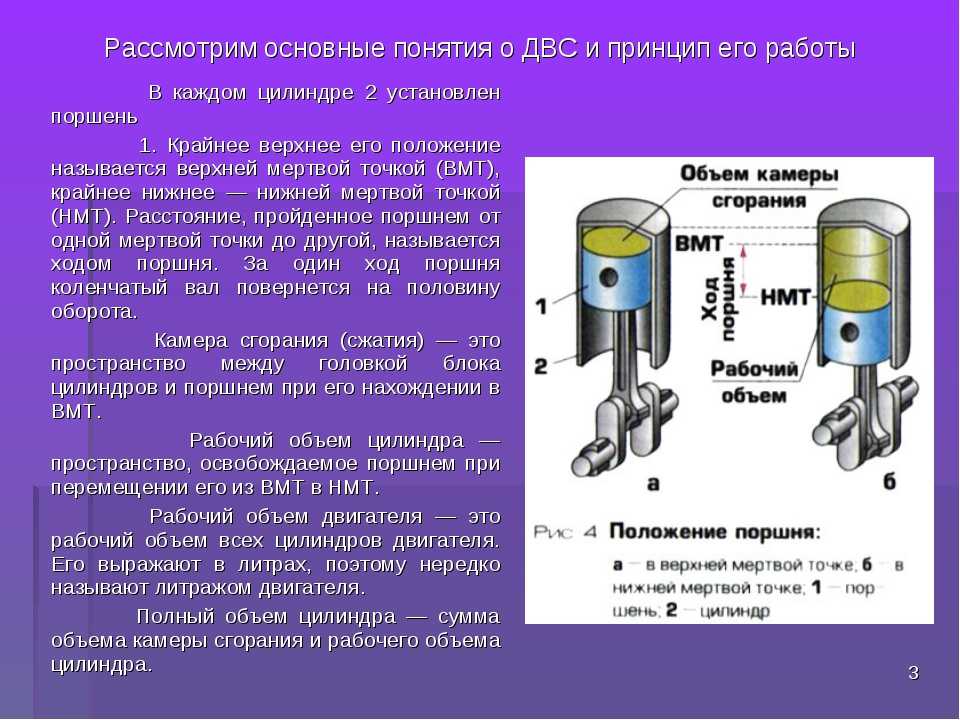
В августе 2021 года Агентство по охране окружающей среды США (EPA) предложило пересмотренные рекомендации по выбросам парниковых газов для легковых и грузовых автомобилей 2023–2026 годов выпуска. Предлагаемые стандарты включают увеличение выбросов на 10% по сравнению с текущими стандартами для автомобилей 2023 модельного года и повышение уровня выбросов на 5% в каждый из следующих 3 лет. Существующие стандарты ежегодно ужесточаются всего на 1,5%.
В то же время EPA объявило о планах по сокращению выбросов загрязняющих веществ большегрузными грузовиками посредством более строгих правил. Агентство ожидает, что новые правила будут применяться к большегрузным автомобилям, начиная с 2027 модельного года.
Независимо от планов Агентства по охране окружающей среды, политическая и экологическая атмосфера по-прежнему подталкивают к повышению эффективности двигателя внутреннего сгорания больше, чем потребительский спрос. Независимо от того, согласны ли лично инженеры и руководители с изменениями в воздухе, отрасль неуклонно движется в этом направлении.
2. Как повысить эффективность выбросов двигателей внутреннего сгорания?
Управление по энергоэффективности и возобновляемым источникам энергии сообщает, что производители сократили выбросы загрязняющих веществ более чем на 99% за 30-летний период. Творческие умы добились этого, сохранив или увеличив экономию топлива.
Помимо бензина и дизельного топлива производители изучают другие способы повышения экономии топлива:
- Использование биодизеля
- Использование других альтернативных или возобновляемых видов топлива
- Комбинация двигателей внутреннего сгорания с гибридными электрическими силовыми установками
3. Дизельные двигатели по сравнению с традиционными бензиновыми двигателями
Когда европейцы перешли с дизельных автомобилей на бензиновые, произошло соответствующее увеличение выбросов углекислого газа. По неожиданному повороту некоторые из сегодняшних автомобильных стратегий основаны на дизельных двигателях.
Согласно отчетам, многие большие дизельные грузовики производят меньше выбросов CO2, чем некоторые автомобили меньшего размера, работающие на газе. Совершенствование технологий привело к созданию дизельных двигателей, которые может заправлять небольшие транспортные средства и обеспечивает:
- меньший расход топлива
- Снижение уровня выбросов углерода
- Больший крутящий момент
- Двигатель с увеличенным сроком службы
Исследование Мичиганского университета, проведенное в 2021 году (вместе с General Motors), показало, что в потребительских автомобилях 100% возобновляемое дизельное топливо может снизить выбросы углерода. Участвующие инженеры заявили, что биотопливо из возобновляемых углеводородов сократило углеродный след на 80% по сравнению с традиционным нефтяным топливом в дизельных двигателях Chevy Cruze и GMC Sierra, которые они тестировали.
Возможно, дизельное топливо является подходящей заменой, в то время как некоторые части мира (например, США) начинают покупать электромобили?
4. Электромобили с аккумуляторными батареями и автомобили с двигателем внутреннего сгорания
Вы знали, что это произойдет. Хотя бензиновые двигатели, похоже, не исчезают полностью, они сталкиваются с жесткой конкуренцией со стороны своих электрических конкурентов.
Даже BMW, чей член совета директоров, отвечающий за разработку, в 2019 году назвал автомобильную электрификацию «переоцененной»., сигнализирует о начале конца. В октябре 2021 года BMW объявила, что к 2024 году прекратит производство двигателей внутреннего сгорания на одном из своих заводов (в Мюнхене). Над головами проэлектрической толпы всегда могла висеть батарея. А именно:
- Размер
- Стоимость
- Долговечность
- Возможности зарядки или их отсутствие
Тем не менее, по прогнозам, электромобили достигнут ценового паритета с традиционными автомобилями к середине 2022-х годов, поскольку стоимость аккумуляторов для электромобилей резко упадет. В 2021 году агентство BloombergNEF прогнозировало, что к 2023 году стоимость литий-ионного аккумулятора для электромобиля упадет ниже 100 долларов за кВтч, т. е. примерно на 20%. Эти сокращения, безусловно, происходят быстрее, чем ожидал рынок.
Беспокойство по поводу запаса хода станет меньшей проблемой для электромобилей в будущем. Технологии развиваются, и появляется все больше зарядных станций. «Беспокойство по поводу запаса хода» (страх потребителей, что им негде будет зарядить аккумулятор) по-прежнему остается серьезной проблемой, которую OEM-производителям еще предстоит решить.
5. Порошковая металлургия поддерживает переход к экологичности
Усовершенствованная порошковая металлургия, сильно отличающаяся от порошковой металлургии вашего отца, становится все более важным фактором при проектировании компонентов двигателей.
«Зеленая» технология порошковой металлургии идет рука об руку с будущим экологичных автомобилей. Спеченные магнитомягкие материалы с более высокой плотностью обеспечивают беспрецедентное повышение производительности. Возможно, вы уже слышали историю о порошковом металле, но эти новые материалы отличаются от материалов стандарта 35, на которые производители полагались десятилетиями.
Стандарт MPIF 35 является отличной базой для производителей порошковой металлургии, но для ваших будущих конструкций статора и ротора могут потребоваться материалы и процессы, превосходящие «стандартные» уровни производительности. В некоторых случаях вы даже можете исключить компонент из сборки, используя порошковый металл.
Современная передовая технология уплотнения может быть немного дороже на начальном этапе, но в долгосрочной перспективе она может значительно сэкономить производителям (и водителям).
Многие компоненты могут быть переведены на порошковый металл. Порошковая металлургия добилась больших успехов в создании мелких деталей для электродвигателей и других автозапчастей по многим причинам:
- Уменьшает вес
- Повышает эффективность электродвигателя, в том числе улучшает магнитные свойства
- Создает детали в форме сетки
- Позволяет использовать передовые материалы и процессы
- Более высокая прочность и твердость
В частности, магнитомягкие композитные материалы прокладывают путь к сверхэффективному электродвигателю.
Порошковая металлургия – это уже не просто стержни и торцевые крышки!
Куда вы пойдете дальше?
Современные услуги порошковой металлургии позволяют плавно перейти от традиционной конструкции двигателя внутреннего сгорания к более эффективным и экологически безопасным двигателям будущего. Достижения в области материалов для ПМ (как вы найдете ниже) и процессов (таких как спекание) сделали это возможным.
Конечно, двигатели внутреннего сгорания еще какое-то время будут существовать. Порошковая металлургия также может способствовать созданию новых или альтернативных конструкций двигателей внутреннего сгорания.
Чтобы узнать, как можно использовать новые материалы и процессы порошковой металлургии для улучшения конструкции и производительности двигателя, посетите наш Центр ресурсов:
Связанные ресурсы
- Прошлое и будущее дизайна автомобильных силовых агрегатов: электромобили, гибриды, ДВС, дизель
- Дизайн автомобильной трансмиссии: крутящий момент + 3 других соображения и тенденции
- 3 Тенденции в производстве автозапчастей: есть ли место порошковому металлу?
(Примечание редактора: эта статья была первоначально опубликована в сентябре 2019 г. и недавно обновлена.)
Обзор проектных соображений для систем внутреннего сгорания дизельных двигателей малой грузоподъемности. (Конференция)
Обзор конструктивных соображений для систем внутреннего сгорания дизельных двигателей малой грузоподъемности. (Конференция) | ОСТИ.GOVперейти к основному содержанию
- Полная запись
- Другие родственные исследования
Аннотация не предоставлена.
- Авторов:
- Майлз, Пол С.
- Дата публикации:
- Исследовательская организация:
- Национальная лаборатория Сандия. (SNL-CA), Ливермор, Калифорния (США)
- Организация-спонсор:
- Управление по энергоэффективности и возобновляемым источникам энергии (EERE) Министерства энергетики США, Транспортное управление. Офис автомобильных технологий
- Идентификатор ОСТИ:
- 1240837
- Номер(а) отчета:
- ПЕСОК2015-1437К
567282
- Номер контракта Министерства энергетики США:
- АК04-94АЛ85000
- Тип ресурса:
- Конференция
- Отношение ресурсов:
- Conference: Предложено для презентации на 12-й Международной конференции по процессам сгорания в двигателе.
12-13 марта 2015 года в Людвигсбурге, Германия.
- Страна публикации:
- США
- Язык:
- Английский
Форматы цитирования
- ГНД
- АПА
- Чикаго
- БибТекс
Майлз, Пол С. Обзор соображений по проектированию систем сгорания дизельных двигателей малой грузоподъемности. . США: Н. П., 2015.
Веб.
Копировать в буфер обмена
Майлз, Пол С. Обзор соображений по проектированию систем сгорания дизельных двигателей малой грузоподъемности. . Соединенные Штаты.
Копировать в буфер обмена
Майлз, Пол С.
2015.
«Обзор соображений по проектированию систем сгорания дизельных двигателей малой грузоподъемности». Соединенные Штаты. https://www.osti.gov/servlets/purl/1240837.
Копировать в буфер обмена
@статья{osti_1240837,
title = {Обзор соображений по проектированию систем сгорания дизельных двигателей малой грузоподъемности.},
автор = {Майлз, Пол С.},
abstractNote = {Аннотация не предоставлена.},
дои = {},
URL-адрес = {https://www.osti.gov/biblio/1240837},
журнал = {},
номер =,
объем = ,
место = {США},
год = {2015},
месяц = {3}
}
Копировать в буфер обмена
Просмотр конференции (0,54 МБ)
Дополнительную информацию о получении полнотекстового документа см. в разделе «Доступность документа». Постоянные посетители библиотек могут искать в WorldCat библиотеки, в которых проводится эта конференция.
Экспорт метаданных
Сохранить в моей библиотеке
Вы должны войти в систему или создать учетную запись, чтобы сохранять документы в своей библиотеке.
Аналогичных записей в сборниках OSTI.GOV:
- Аналогичные записи
Поршневые кольца для двигателей внутреннего сгорания
Обзор курса
Двигатель внутреннего сгорания представляет собой машину, состоящую из тысяч частей, которые сложным образом взаимодействуют друг с другом для получения мощности. Одна часть, поршневые кольца, жизненно важны для разделения камеры сгорания и картера, возможно, выполняя самую важную работу из всех. По окончании курса слушатели будут:
- Знать терминологию поршневых колец и компоновку в двигателях внутреннего сгорания.
- Уметь описать функцию, конструктивные особенности, материалы и покрытия применительно к компрессионным и маслосъемным кольцам в двух- и четырехтактных двигателях.
- Уметь описать осевую динамику колец в двух компрессионных кольцах при работе двигателя, вопросы уплотнения колец.
- Уметь определять механизмы прорыва газов и расхода масла, а также способы смягчения последствий для каждого из них.
- Будет понимать проблемы и подходы к проверке, измерению и моделированию износа колец и стенок цилиндров в двух- и четырехтактных двигателях внутреннего сгорания.
В конечном счете, этот курс вооружит слушателей важными знаниями о конструкции поршневых колец внутреннего сгорания и методах измерения/уменьшения износа
Кто должен посещать?
Лица, которым нужны дополнительные знания о поршневых кольцах двигателей, включая терминологию, компоновку и применение отдельных колец, а также то, как каждое из них влияет на конструкцию двигателя. Те, кто хочет расширить свои знания о конструкции поршневых колец, чтобы лучше общаться с инженерами-конструкторами поршневых колец. Учащиеся, желающие ознакомиться с передовыми технологиями измерения и анализа износа поршневых колец. Содержание этого курса одинаково понравится студентам инженерных специальностей, энтузиастам ДВС, исследователям ДВС, инженерам по надежности и экспертам RCA.
Краткое содержание курса
Модуль 1: Вводный взгляд
Модуль 2: Детали конструкции кольца
Модуль 3: Контроль температуры и динамика кольца
Модуль 4: Движение кольца и стенка цилиндра
Модуль 5: Перекачка масла
2 Модуль 6: Механизмы износа кольца и стенки цилиндра
Модуль 7: Проверка степени износа
Модуль 8: Измерение и анализ
Преподаватель
Кевин Хоаг
Г-н Хоаг имеет более чем 40-летний опыт разработки дизельных и бензиновых двигателей как в промышленных, так и в учебных заведениях, а также является членом Общества автомобильных инженеров. Он занимает должность инженера института в SwRI и в настоящее время возглавляет Консультативный комитет SwRI по исследованиям (ACR). Его опыт обширен и включает в себя как дизельное топливо, так и искровое зажигание, разработку характеристик двигателя, контроль выбросов, компоновку и балансировку двигателя, литье, ковку и материалы, анализ структурной усталости, системы обработки воздуха, охлаждения и смазки. Он также имеет большой опыт взаимодействия с клиентами, применения и обслуживания двигателей, а также инженерное образование. Особые моменты технического вклада г-на Хоага включают разработку четкой формулировки для анализа второго закона двигателей внутреннего сгорания, создание и управление группой Heat & Fluids в Cummins, Inc., а также директора-основателя и ведущего разработчика магистра инженерии в области систем двигателей ( MEES) Программа Университета Висконсина. Он имеет патенты и является автором многочисленных публикаций, а также имеет несколько наград и наград. Г-н Хоаг в настоящее время является членом Общества автомобильных инженеров (SAE) и братства Tau Beta Pi Engineering.
Кредиты
- СЕУ : .4
- ПДГ : 4
Расписание
Даты/время проведения мероприятий:
- 01.07.2022 12:01–23:59
- 30.06.2023 12:01–23:59
Преподаватель
Кевин Хоаг
Местоположение
Это онлайн-курс.
Политика отмены
После того, как вы получили доступ к материалам онлайн-курса, отмена или возврат средств не разрешены.
Если вы планируете пройти курс междисциплинарных профессиональных программ, во время регистрации необходимо внести оплату. Ниже приведены варианты оплаты:
Оплата кредитной картой
Зарегистрируйтесь онлайн и оплатите кредитной картой.
- Найдите курс на веб-сайте, а затем нажмите кнопку «Зарегистрироваться сейчас» на веб-странице курса.
- Введите всю необходимую информацию о участнике курса и информацию об оплате на странице регистрации на курс.
- Вы получите электронное письмо с подтверждением успешной регистрации и оплаты.
Зарегистрируйтесь по телефону и оплатите кредитной картой.
- Позвоните в отдел регистрации конференц-центра UW по телефону 608-262-2451.
- Предоставить представителю по регистрации конференц-центра:
- название курса, даты и/или номер курса.
- необходимую информацию об участниках курса и информацию об оплате.
- Вы получите отправленный по почте документ или электронное письмо для подтверждения успешной оплаты зачисления.
Оплата чеком
Отправьте по почте заполненную регистрационную форму и чек, подлежащий оплате UW Madison.
- Заполните регистрационную форму (находится либо в конце брошюры курса, которую вы получили по почте, либо здесь).
- Подготовьте чек, подлежащий оплате UW Madison.
- Отправьте регистрационную форму и чек по почте: Отдел регистрации по адресу: Engineering Specialist 702 Langdon Street Madison, WI 53706
- Вы получите отправленный по почте документ или электронное письмо для подтверждения успешной регистрации и оплаты.
Военный
Если вы используете форму SF-182, позвоните по нашему регистрационному номеру 608-262-2451 или напишите по адресу Registrations@pyle.wisc.edu для получения подробной информации и инструкций.
Отмена мероприятия
Мы оставляем за собой право отменить курс из-за недостаточного количества участников или непредвиденных обстоятельств. Если мы отменяем курс, участники будут уведомлены по электронной почте или по телефону, и им будет предоставлена возможность полного возмещения средств или переноса их регистрации и любых уплаченных сборов на другой курс. Мы не несем ответственности за невозвратные авиабилеты, бронирование отелей и другие расходы, связанные с поездкой. Для отмены курса для зачисленных см. примечания на странице курса.
Поршневые кольца для двигателей внутреннего сгорания
Дата: Чт. 01 июля 2021 г. – Чт. 30 июня 2022 г.
ID: RA01771-C194
Плата:
Кредиты:
- CEU :.
Кевин Хоаг
Адрес:
Это был онлайн-курс.
Программный директор
Андреа Стшелец
Свяжитесь с нами
Связанные курсы
3D-печать двигателя внутреннего сгорания — быстрее выйти на рынок
Разработка двигателя внутреннего сгорания может занять много времени, от трех до пяти лет. Что, если бы вы могли сократить это время вдвое? Для Lumenium LLC, стартапа из Вирджинии, разрабатывающего инновационное семейство двигателей внутреннего сгорания, 3D-печать с помощью системы Desktop Metal позволила им достичь этой цели.
Асимметрично-вращательный двигатель с обратным рабочим объемом (IDAR) компании представляет собой новую конструкцию для обеспечения мощного и эффективного внутреннего сгорания. Его уникальная геометрия двигателя обеспечивает впечатляющую, но эффективную производительность небольшого и легкого двигателя, который потребляет меньше топлива и производит меньше выбросов.
Ключом к разработке этого движка была возможность быстро повторять функции и конструкции деталей во время прототипирования.
Детали Lumenium должны выдерживать экстремальные температуры и нагрузки, присущие работе двигателя внутреннего сгорания. Каждый компонент двигателя должен соответствовать определенным требованиям, включая высокую точность размеров, прочность при динамических нагрузках и низкое тепловое расширение, а вес каждой детали является важным фактором, влияющим на общую удельную мощность и эффективность.
Седло и маятник в сборе рядом с установленным маятником для двигателя внутреннего сгорания IDAR.Аддитивное производство помогло команде разработчиков выполнить эти требования и заняться деталями сложной геометрии, такими как внутренние каналы охлаждения, для повышения производительности двигателя. С Studio System от Desktop Metal команда внедрила эту технологию в существующее рабочее пространство для более быстрой итерации дизайна и функционального прототипирования.
Рынок стоимостью 350 миллиардов долларов
Двигатели внутреннего сгорания представляют собой рынок стоимостью 350 миллиардов долларов с тремя категориями двигателей: традиционные поршневые двигатели, новые двигатели с оппозитными поршнями и роторные двигатели. Технология двигателя IDAR от Lumenium добавляет четвертую категорию, стоящую в середине традиционной технологии двигателей, что представляет собой сдвиг парадигмы в производстве энергии. Компоненты двигателя должны выдерживать условия динамической нагрузки, силу сгорания 1500 фунтов на квадратный дюйм и температуру сгорания 1500 °C.
Возможность выполнять частые итерации проекта может улучшить конечную производительность двигателя. Полный цикл разработки двигателя для каждого поколения двигателя IDAR занимает от трех до пяти лет. Критически важно было найти более быстрый и экономичный подход к прототипированию.
Почему 3D-печать лучше, чем обработка на станках с ЧПУ
Lumenium производит около 20 прототипов в месяц.
Большинство (около 95%) изготавливаются на собственном производстве с использованием 5-осевой обработки с ЧПУ и электроэрозионной обработки. Обработка сложной геометрии с ЧПУ включает в себя сложные траектории движения инструмента и иногда более 80 операций обработки. Каждая операция требует перепрограммирования, что часто включает в себя индивидуальную фиксацию и оператор для повторного выравнивания детали. Даже если на печатной детали требуется последующая обработка, общее количество операций обработки значительно меньше. Для программирования станка с ЧПУ требуется обученный, преданный своему делу оператор, а на одну сложную работу могут уйти недели. Некоторые детали требуют постобработки сторонними поставщиками, что увеличивает срок изготовления до трех недель.
Оставшиеся 5 % деталей-прототипов — обычно обычные круглые детали — отправляются во внешний механический цех, где время выполнения заказа составляет в среднем около трех недель.
В дополнение к длительному времени выполнения заказа и высоким затратам механическая обработка предлагает ограниченные возможности для изготовления легких деталей.
Вес имеет решающее значение для производительности двигателя, поскольку снижение веса двигателя на 50% потенциально может удвоить номинальную скорость двигателя (об/мин) и выходную мощность. Чтобы уменьшить вес с помощью методов механической обработки, инженеры мало что могут сделать, кроме выбора легкого материала. Без замены материала уменьшение веса за счет механической обработки обычно требует изменения геометрии детали, что увеличивает время и сложность, что может привести к появлению слабых мест в структуре детали.
Студийная система печатает детали с заполнением с закрытыми ячейками — внутренней решетчатой структурой, напечатанной по всей детали. Пользователи могут регулировать расстояние между наполнителями в соответствии с требованиями по прочности и весу. Детали, напечатанные с заполнением, будут иметь значительно более низкую теплопередачу. Это снижает вес детали при сохранении прочности, что позволило команде разработчиков использовать сталь как часть своего решения.
В большинстве методов 3D-печати, основанных на экструзии, включая осаждение связанного металла, горизонтальные отверстия требуют внутренних поддерживающих структур для сохранения формы. Однако адаптация формы отверстия может устранить необходимость в опорах. Команда разработчиков изменила конструкцию, изменив круглые отверстия на более угловатую форму (например, каплевидную), которая не требует опорных конструкций во время изготовления.
Конструкция седла состоит из зубцов по верхнему и нижнему краям, которые сопрягаются с поворотными рычагами. Зубцы помогают компоненту выдерживать усилия двигателя, а обработка этих критически важных элементов позволяет получить гладкую и точную поверхность сопряжения, чего нельзя достичь с помощью одной только печати.
В Fabricate пользователи могут выборочно регулировать толщину оболочки. Важно отметить, что при этом размеры детали не изменяются. Вместо этого он утолщает твердую оболочку вокруг детали, чтобы предотвратить обнажение заполнения детали во время обработки.
Команда разработчиков увеличила толщину оболочки только верхней и нижней частей до 5,2 мм, чтобы учесть материал, который будет удален во время обработки зубцов.
После изготовления детали прошли постобработку. Это включало обработку с ЧПУ и проволочную электроэрозионную обработку. Критические поверхности седла были обработаны, сверху и снизу были добавлены зубцы, а также просверлены отверстия и нарезана резьба. После завершения команда дизайнеров соединила седло и поворотный рычаг.
Для Lumenium быстрое прототипирование имеет решающее значение для разработки и усовершенствования продукта, поскольку движок IDAR приближается к коммерциализации. Конструкция и функция каждой детали в сборке имеют решающее значение, поэтому возможность быстрой доработки и итерации напрямую влияет на общую производительность двигателя. Печатное седло, поворотный рычаг и шатун демонстрируют экономию времени и средств, которую обеспечивает Studio System.
Настольный металл
Desktopmetal.com
Двигатели внутреннего сгорания | Конструкция машины
Наиболее транспортабельными и надежными источниками энергии являются двигатели внутреннего сгорания.
Большинство промышленных двигателей внутреннего сгорания (ДВС) малой мощности, около 30 л.с. или меньше, работают на бензине, поскольку дизельные двигатели слишком тяжелые и дорогие. Например, в небольшом водяном насосе с приводом от двигателя бензиновый двигатель будет составлять примерно 60% стоимости всего комплекта. С дизельным двигателем стоимость была бы ближе к 90%.
Таким образом, в диапазоне малой мощности выбор двигателя в основном основывается на таких факторах, как выбор между четырех- и двухтактным режимом работы и между чугунной или алюминиевой конструкцией.Четырехтактный двигатель обычно является предпочтительной бензиновой силовой установкой. Он имеет репутацию долго безотказной работы, ровно работает на холостом ходу и хорошо работает на малых оборотах, не требует смазки в топливе и вообще не имеет выхлопа с видимым дымом.
Небольшие двигатели обычно имеют воздушное охлаждение для простоты и снижения веса. Однако вода наиболее эффективно охлаждает большие стационарные двигатели.
Четырехтактные двигатели мощностью до 40 л.с. обычно имеют простые клапаны с Г-образной головкой, которые дешевле, чем верхний распредвал. Верхний распредвал обеспечивает большую мощность и экономию топлива и обычно используется в более крупных двигателях.
В малых двигателях используется тот же простой дыхательный механизм и карбюратор, что и в автомобильных двигателях. Более сложный впрыск топлива и наддув предназначен для более крупных и дорогих двигателей и дизелей.
Четырехтактные двигатели мощностью более 10 л.с. обычно изготавливаются из чугуна. С двигателями меньшего размера у покупателя есть выбор между чугуном и литым под давлением алюминием. Алюминиевый двигатель дешевле, если он производится в больших количествах.
Говорят, что железо лучше изнашивается, но сторонники алюминиевого двигателя утверждают, что при правильном уходе он прослужит так же долго.
Железо более устойчиво к грязи, в то время как попадание грязи в двигатель довольно вредно для алюминиевого двигателя.
Автомобильные, морские и авиационные двигатели значительно более сложны, чем небольшие промышленные двигатели, и алюминий успешно используется в больших двигателях для этих целей.
Двухтактный двигатель развивает значительно большую мощность, чем четырехтактный двигатель того же размера. Преимущество двухтактного двигателя в удельной мощности составляет от 50% до 300% и более. Например, четырехтактный двигатель мощностью 40 л.с. может весить 250 фунтов, а двухтактный двигатель такой же мощности весит всего 65 фунтов. Один двухтактный двигатель развивает мощность 80 л.с. при рабочем объеме всего 440 см³.
Благодаря такому высокому соотношению мощности и веса двухтактный двигатель обычно предпочтительнее для спортивных автомобилей или там, где двигатель необходимо поднимать, удерживать или переносить вручную. Электропилы и большинство подвесных судовых двигателей двухтактные, как и большинство снегоходов.
Новые разработки в этой области заставили автопроизводителей переосмыслить прежние концепции двухтактных двигателей. Одна исследовательская фирма обнаружила, что при тонком распылении топлива сгорание происходит более полно, выхлоп достаточно чистый, чтобы обойтись без каталитического нейтрализатора, а холостой ход контролируется более тщательно.
В других областях применения двухтактный двигатель имеет неблагоприятную репутацию из-за неровного холостого хода, плохой работы на низких скоростях, резкого поведения и быстрого загрязнения. Поскольку они, как правило, лучше всего работают на высоких скоростях, срок их службы может быть коротким. Также в топливо необходимо добавлять смазку.
К их преимуществу, первоначальная стоимость составляет примерно 70% от стоимости эквивалентного четырехтактного двигателя, произведенного в том же объеме производства. Двухтактные двигатели обычно изготавливаются из алюминия в целях снижения веса.
Дизели , как правило, становятся конкурентоспособными с бензиновыми двигателями мощностью более 30 л.
с., и они становятся более логичной альтернативой по мере увеличения потребности в мощности. Их обычно выбирают из-за их эксплуатационной экономичности и большей долговечности. В целом дизель стоит примерно в 2 1/2 раза дороже бензинового двигателя, но в среднем дизель служит примерно в 2 1/2 раза дольше. Помимо того, что дизельные двигатели дороже бензиновых, они также производят больше шума и вибрации. Дизели также работают в узком диапазоне оборотов и обычно требуют значительного переключения передач при использовании в автомобилях без гидротрансформаторов. Они требуют впрыска топлива, что способствует их более высокой стоимости.
Дизели приобрели свою репутацию прочных тяжелых двигателей в первую очередь потому, что они сконструированы так, чтобы выдерживать высокие усилия зажигания и высокое давление в цилиндрах, которые являются следствием высокой степени сжатия, необходимой для самовоспламенения.
Иногда выбор двигателя основывается не только на экономических соображениях.
Тенденция к стандартизации топлива, например, часто диктует использование небольших дизелей на установках, уже использующих большие дизели. Тенденция к использованию больших дизельных сельскохозяйственных тракторов, например, поощряет использование дизельных двигателей меньшего размера, поэтому хранится только один вид топлива.
Дизельное топливо менее летучее, чем бензин, и поэтому более безопасно в обращении. А дизельное топливо в меньшей степени подвергается хищениям, чем бензин, что заставляет многих строительных подрядчиков рассматривать дизельное топливо для небольших двигателей. Многие компании стандартизировали дизельную мощность для всех двигателей; большинство двигателей, используемых на буровых установках, являются дизельными.
Географическое положение также может повлиять на выбор дизельного топлива по сравнению с бензиновым. Европейские страны, например, сильно склоняются к дизельным двигателям даже для двигателей мощностью менее 30 л.с.
Как и в случае с бензиновыми двигателями, есть выбор между двух- и четырехтактными дизелями.
Однако дизели были усовершенствованы и усовершенствованы до такой степени, что внешние функциональные различия между двух- и четырехтактным режимом работы с точки зрения мощности, экономичности или долговечности незначительны.
Для работы двухтактного дизельного двигателя требуется механический нагнетатель воздуха для принудительной подачи воздуха, чтобы двигатель был достаточно аспирационным. Это в дополнение к турбонагнетателям (с приводом от выхлопных газов), которые часто используются как на четырехтактных, так и на двухтактных дизелях.
Двигатель Ванкеля по функциональным характеристикам, включая вес, выходную мощность, КПД и скорость, напоминает двухтактный бензиновый двигатель. Короче говоря, Ванкель имеет тенденцию экономить немного больше веса и места по сравнению с обычным четырехтактным двигателем. Эта экономия варьируется от незначительной суммы в небольших двигателях до значительной суммы по сравнению с большим автомобильным двигателем V8. Здесь Ванкель весит примерно вдвое меньше и имеет примерно одну треть размера четырехтактного поршневого двигателя.
Некоторые исследователи полагают, что в долгосрочной перспективе Ванкель с его четырехтактным принципом действия может оказаться лучше двухтактного. Изначально у Ванкеля была плохая герметизация камеры сгорания и высокий расход топлива. Но постоянные разработки привели к значительным улучшениям в герметизации и снижению расхода топлива.
Wankel получил признание в некоторых сегментах автомобильного рынка, но в настоящее время он не подходит для промышленного применения. Однако некоторые крупные промышленные роторные двигатели были разработаны специально для комплексных приложений, включающих приводы компрессоров, генераторов и насосов. В основном эти роторные двигатели представляют собой высокомощные тихоходные агрегаты.
Газовая турбина исключительно хорошо подходит для приложений, где требуется значительная выходная мощность при постоянной скорости. Например, одно из наиболее важных применений в промышленности — это приведение в действие огромных электрогенераторов для увеличения выработки пара в условиях пикового спроса в энергетических компаниях.
Однако газотурбинные двигатели дороги как в покупке, так и в эксплуатации. Электроэнергия, вырабатываемая на уровне коммунальных предприятий газовой турбиной, стоит в три-четыре раза больше, чем вырабатываемая паровой турбиной.
Стоимость газовой турбины находится в диапазоне от 15 до 35 долларов за л.с., тогда как поршневые двигатели обычно стоят от 1 до 10 долларов за л.с. Высокая стоимость турбины связана с необходимостью использования дорогих материалов, способных выдерживать высокие температуры.
Турбины плохо экономят топливо при малой нагрузке, и им требуется значительное время для набора скорости при ускорении. Таким образом, они, как правило, делают плохие автомобильные двигатели. Они лучше подходят для тяжелых грузовиков и автобусов, а также для мощных стационарных устройств, где они работают с одинаковой высокой скоростью. Несмотря на свои недостатки, газотурбинный двигатель мощностью 1500 л.с. приводит в движение армейский боевой танк M1. Двигатель может развивать 40-тонную машину со скоростью более 40 миль в час.